Com o impulso para a eletrificação de motor e transmissão ganhando força, os produtores de aço de alta resistência estão se preparando para lucrar, relata James Bakewell
Em 2017, as vendas globais de veículos elétricos a bateria (BEVs) e veículos elétricos híbridos plug-in (PHEVs) atingiram 1,3 milhão de unidades, segundo Frédéric Painchault, diretor de Marketing Automotivo Global da siderúrgica ArcelorMittal. “Isso representa uma baixa participação no total de vendas de veículos - menos de 2%. No entanto, o mercado está crescendo rapidamente, em mais de 57% em comparação a 2016. As montadoras globais planejam lançar aproximadamente 340 modelos BEV e PHEV nos próximos três anos. Isso significa que as vendas devem chegar a quase 5 milhões de unidades até 2050."
E isso é só o começo. Basjan Berkhout, gerente de marketing da Automotive na Tata Steel Europe, acrescenta: “A Tata Steel espera que os veículos elétricos representem 90% das vendas de veículos [na União Europeia (UE)] até 2050.”
A legislação ambiental é o principal motivo para a indústria automotiva ter passado para os motores elétricos. A UE, por exemplo, determinou que os carros novos não podem emitir mais de 130g de dióxido de carbono por quilômetro percorrido. Essa meta será reduzida para 95g por quilômetro em 2021, gradualmente a partir de 2020, e provavelmente será ainda mais rigorosa em 2030.
O nível de aceitação de transmissões elétricas varia de região para região. Berkhout diz que a maior influência continua sendo o mercado chinês, onde o governo estabeleceu cotas obrigatórias de produção de veículo elétricos para os OEMs que operam no local para reduzir as emissões de escapamento. Com a China sendo o maior mercado de lucro para a maioria dos OEMs, o risco de ignorar isso é grande demais. Outra pressão está melhorando a qualidade do ar nas cidades-alvo. O aperto das emissões de escape na União Europeia também foi focado com maior intensidade após as consequências do escândalo do diesel e da mudança pendente no final deste ano para o novo teste de emissões WLTP.
Painchault acrescenta: “A incerteza sobre os regulamentos de Economia de Combustível Média Corporativa (CAFÉ) nos EUA pode significar que o crescimento na região do NAFTA não seja tão alto. Na Europa e na China, a ArcelorMittal está prevendo que o número combinado de vendas de BEV e PHEV excederá as vendas de motores de combustão interna (ICE) até por volta de 2025. A maior parte do crescimento virá de PHEVs. Nosso cenário para 2030 é que cada tipo de veículo - PHEV, BEV e ICE - seja responsável por um terço das vendas. Dentro de quinze a vinte anos, veículos não-ICE devem dominar o mercado.”
Ganhando um lugar no futuro elétrico
A indústria siderúrgica é tipicamente otimista quanto ao seu lugar no futuro elétrico. Por exemplo, em um relatório recente, a Tata Steels diz que a crescente demanda por veículos de emissões ultrabaixas (ULEV) impulsionará o crescimento do fornecimento de aço para a indústria automotiva em 4,2 milhões de toneladas somente na Europa.
Nos últimos anos, a inovação, para não mencionar os lucros, na indústria de materiais automotivos tem sido impulsionada principalmente pela necessidade de produtos mais leves e/ou mais fortes que permitam às montadoras reduzir a massa de seus veículos ICE - diminuindo assim o consumo de combustível e as emissões de dióxido de carbono. Nos primeiros veículos elétricos, como o i3 da BMW ou o Model S da Tesla, os materiais leves têm sido fundamentais - plásticos reforçados de fibra de carbono (CFRP) e alumínio, respectivamente.
Com os veículos ICE, os consumidores estão acostumados a dirigir por centenas de quilômetros sem precisar reabastecer. Para alcançar uma faixa comparável de uma única carga de um VEB, uma bateria muito grande, cara e pesada teve que ser usada, significando que os fabricantes de automóveis tiveram que cortar peso em outras partes do veículo. Será sempre este o caso?
O presidente do setor automotivo da NanoSteel, Craig Parsons, afirma: “Sim, é provável que os veículos elétricos tenham mais incentivo ao peso leve do que os veículos ICE. Uma bateria sempre tem uma quantidade finita de armazenamento de energia e, portanto, alcance, e a redução de peso equivale a um aumento direto na faixa total de veículos, que é o maior obstáculo do projeto enfrentado pelos veículos elétricos. As baterias são muito pesadas e cada quilo economizado no veículo criará mais espaço para uma bateria de longa duração e/ou uma bateria menos potente para o veículo viajar por uma determinada distância.”
Gerente de desenvolvimento de negócios para o setor automotivo SSAB, Jonas Adolfsson, concorda. Ele diz que, independentemente do motor e transmissão empregados, a física envolvida no movimento de um veículo continua a mesma. As forças de resistência ao movimento são aceleração, resistência ao rolamento, gradiente e resistência ao vento. Todos, exceto os últimos, são fortemente influenciados pelo peso do veículo. Ele diz: "As baterias têm uma densidade de energia muito pior [Watt-horas por quilo] quando comparadas às que são a gasolina ou a diesel, assim eu diria que a redução de peso seria ainda mais importante."
"A redução de massa tem um impacto limitado no alcance estendido. Por exemplo, uma redução de 100 kg em massa aumenta apenas a distância entre seis a 11 quilômetros…" – Jean-Luc Thirion, ArcelorMittalJean-Luc Thirion, diretor de Pesquisa e Desenvolvimento Global para o setor automotivo da ArcelorMittal, tem uma opinião diferente: “A redução da massa tem um impacto limitado no aumento do alcance. Por exemplo, uma redução de 100 kg na massa aumenta apenas a distância entre seis a 11 quilômetros. Para aumentar o alcance, é muito mais fácil e menos dispendioso adicionar mais baterias. O impacto da economia de peso em velocidade máxima e aceleração também é insignificante. Uma economia de massa de 100 kg aumenta a velocidade máxima em menos de um quilômetro por hora e reduz o tempo de aceleração em menos de meio segundo. ”
Berkhout concorda: “Todos os veículos devem ser tão leves e econômicos quanto possível, mas com a tecnologia atual, veículos híbridos e totalmente elétricos são 20-30% mais pesados. Um veículo mais leve ampliará a autonomia de um veículo híbrido ou totalmente elétrico, mas a custos mais altos. O fabricante de um veículo pagaria significativamente mais pela redução adicional de peso apenas por um pequeno aumento no alcance?”.
Ele usa o mais recente VW Golf como exemplo. O hatchback está disponível em variantes a gasolina, a diesel, híbridas e totalmente elétricas, com um peso de 1206 kg, com o a diesel apresentando 1301 kg, o híbrido 1615 kg e o elétrico 1615 kg. A variante elétrica tem um alcance de 300 km. Se 10 kg de peso fossem cortados da carroceria em branco (BIW), isso significaria apenas uma redução de peso de 0,62%, o que aumentaria o alcance do veículo em apenas 10 km.
Tecnologias de recuperação de energia já existem em BEVs, que ajudam a ampliar seu alcance. Além disso, futuros desenvolvimentos em infraestrutura também devem ser considerados. Um BEV pode ser recarregado durante a noite na casa do motorista, pode ser recarregado sem fio durante o trajeto e também, recarregado automaticamente quando estacionado no local de trabalho. Neste cenário, uma bateria pesada e cara, capaz de armazenar energia suficiente para uma jornada de 300 km sem a necessidade de recarga, é redundante.
Embalagem de componentes diferentes e estruturas de veículos
Se tudo isso for provado correto, a indústria siderúrgica tem uma oportunidade ideal para reafirmar seu domínio no mercado de materiais automotivos. A eletrificação de unidade de tração poderia criar uma série de aplicações novas para aços fortes e moldáveis na estrutura da carroceria desses veículos
Por exemplo, Berkhout supõe que se o ICE não estiver mais colocado na frente do veículo a estruturas como radiadores, e a posição das rodas dianteiras não for ditada pela posição do motor, o comprimento da extremidade dianteira pode ficar mais curto. Se a extremidade dianteira for mais curta, o comprimento da estrutura de impacto é menor, mas deve absorver a mesma quantidade de energia em um impacto frontal. Isso poderia exigir o uso de um segmento maior do trilho dianteiro, feito com um aço de maior qualidade, e a estrutura BIW envolvente que sustenta o trilho dianteiro também teria que gerenciar cargas mais altas.
Ele continua: “Com as baterias montadas sob o piso, a carga de impacto lateral também precisará ser gerenciada de maneira diferente. Hoje, nos veículos ICE, temos um reforço de balancim suportado pelas peças transversais do banco; estes suportam o pilar B durante o impacto. Se a bateria estiver posicionada no veículo onde geralmente estão os membros cruzados do assento, o compartimento da bateria deverá suportar a carga de impacto lateral. A unidade de bateria Opel Ampere pesa mais de 400 kg e destes, 70 kg constituem o compartimento da bateria. Isso também leva a alterações nos painéis do balancim para suportar o compartimento da bateria e absorver mais carga."
O chefe do departamento de Tecnologia de Aplicação da ThyssenKrupp, Lutz Keßler, concorda que o compartimento da bateria é um local ideal para alvos com aços de alta resistência. Ele diz: “A bateria é o coração de um carro elétrico e o componente mais sensível e caro, respondendo por 30 a 50% dos custos totais do veículo. Por isso, é ainda mais importante desenvolver soluções para proteger a bateria que não aumentem ainda mais os custos dos veículos elétricos”.
Thirion acrescenta: “Alguns produtos para estampagem a quente hoje disponíveis, como o Usibor 2000 [da ArcelorMittal], agora podem atingir uma resistência à tração de 2000MPa. Duas décadas atrás, a força máxima era de apenas 340MPa, assim esse é um aumento espetacular. Os tipos martensíticos para laminação e a linha Fortiform da ArcelorMittal - a terceira geração de aços avançados de alta resistência [AHSS] - também possuem altas resistências. Esses aços permitem que os projetistas de veículos protejem a cabine e a bateria de uma forma ideal."
De fato, a Tata prevê que a demanda europeia de aços avançados para a estrutura desses veículos aumentará em aproximadamente 2,6 milhões de toneladas até 2050, já que os fabricantes procuram economizar peso de maneira econômica.
Aços elétricos para motores
Outra área-chave de crescimento para o aço será nas motorizações usadas nos ULEVs, incluindo os motores elétricos e células de bateria. Esperado pela Tata para responder por um aumento de 1,6 milhão de toneladas na demanda europeia de aço até 2050, esses componentes usarão maiores níveis de aços elétricos e chapeados, respectivamente.
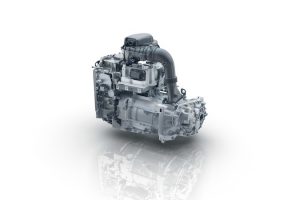
O aço elétrico é um material essencial na construção de motores elétricos, e os graus de aço elétrico utilizados podem alterar o desempenho dessas máquinas. A Tata acredita que isso será extremamente importante para os fabricantes de automóveis, uma vez que eles procuram diferenciar seus grupo motopropulsor dos de seus concorrentes. Aços elétricos com maior desempenho podem melhorar a eficiência dos motores, o que ajudará a ampliar a autonomia ou aumentar o desempenho dinâmico do carro.
Enquanto isso, as baterias de íons de lítio - a solução de armazenamento de energia atualmente favorecida pela maioria das montadoras - são fabricadas em três diferentes formatos de células de bateria: cilíndricas; prismática; e de bolsa. Os formatos prismáticos e de bolsas são geralmente embalados em um invólucro não ferroso, enquanto que as células cilíndricas são colocadas dentro de uma 'lata' revestida de níquel e provavelmente serão as mais comuns, especialmente no futuro imediato, pois oferecem armazenamento barato de energia. confiável, relativamente fácil de fabricar e possui boa estabilidade mecânica. Estes são bons candidatos para fabricação com aços elétricos.
Os produtores de aço prevêem que o alumínio e o CFRP terão um impacto relativamente baixo nesses veículos por várias razões.
Em primeiro lugar, eles permanecerão proibitivamente caros. Em segundo lugar, o aço demonstra melhores propriedades mecânicas - o aço é mais rígido do que o alumínio, tem uma resistência à fadiga muito maior e é mais fácil de formar, unir e pintar sobre outros materiais.
Keßler diz: “Apesar do excelente perfil de propriedade que o aço oferece, a competição entre os materiais continuará sendo um desafio. Assim, os fabricantes de aço também devem buscar continuamente soluções novas e melhores. Na ThyssenKrupp, por exemplo, estamos trabalhando para fechar a lacuna entre a formação a quente e a frio, destacando as oportunidades de formação a frio oferecidas pelos novos aços de dupla fase de altíssima resistência da classe 1200. Também desenvolvemos recentemente uma tecnologia que, para aços de alta resistência em particular, elimina o retorno da mola na fábrica de prensas, reduz o uso de material e garante maior confiabilidade do processo."
Finalmente, pode-se argumentar que o alumínio e o CFRP são menos sustentáveis do que o aço quando todo o ciclo de vida é considerado, o que poderia ser um grande impulsionador futuro no setor automotivo. Thirion diz: “A avaliação do ciclo de vida (ACV) examina as emissões totais geradas durante os três estágios da vida de um veículo: produção; fase de acionamento; e reciclagem. Estudos mostram que o alumínio emite de quatro a cinco vezes mais gases de efeito estufa (GEEs) do que o aço durante todo o ciclo de vida de um veículo.
Sem surpresa, Berkhout revela que a Tata Steel está ativamente fazendo lobby junto às organizações governamentais da UE para introduzir a LCA para medir as emissões veiculares.