Thomas Dose discusses leadership, diversity, and challenges at BMW’s Chennai Plant
How do you go from being a consultant to being a plant manager? Thomas Dose, managing director of the BMW plant in Chennai, India, talks in an interview about his path, the challenges and opportunities in India and the importance of diversity and sustainability.
Before your role as plant manager in Chennai, you had already worked in several positions at BMW. How did you end up here in India?

Before I came to India for the second time - I had already been here once - I worked in consulting. I then came to BMW and worked in internal consulting, where I spent years helping people to do things better. At some point you want to get involved yourself and take on management responsibility. For this purpose I deliberately went to the BMW plant in Leipzig and took on the role of group leader in assembly for a year and a half, which I really enjoyed. After I indicated that I would also like to go abroad, I was offered the position of assembly manager in India. There I learned a lot about people, culture, car manufacturing and logistics. After that I was able to take over the reference packing plant in Wackersdorf. What I had learned about leadership in India I was also able to apply in Upper Palatinate, Germany. Because at the end of the day we are all human and want to be valued. In addition, South Indians and Upper Palatinate people share a down-to-earth attitude. After that I went to Berlin to work in logistics, but after two years the position here in India became available again and I came back as plant manager. I have been here for five years now and am very happy to have achieved a lot together with the team and to have successfully managed the turnaround.
What is the most important lesson you learned in all these positions for your current role?
The importance of diversity. Everyone has different strengths and cultural backgrounds that ideally come together in a melting pot. The idea that you have to teach someone how to do it right is a dead end. Instead, it’s about realizing that we can all learn from each other. Different perspectives and approaches add a lot of value. When someone who grew up here in the Indian culture gives their honest opinion on a problem, it often brings new perspectives that improve the end result.
You mentioned the down-to-earth nature that South Indians and Upper Palatinate people have in common. What are the differences between your current team and your previous team?
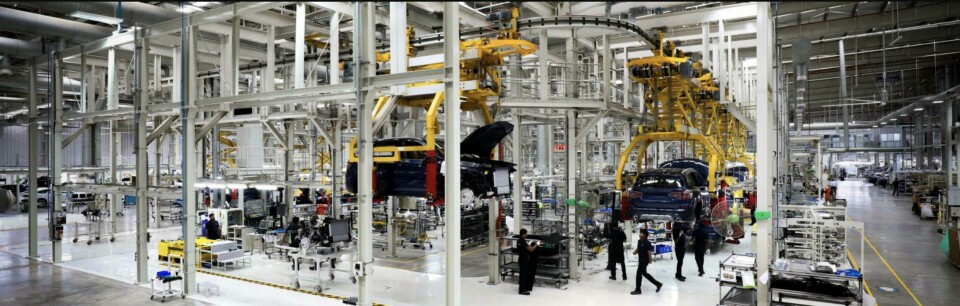
In a large corporation, you often have the opportunity to advance your career by changing jobs. Here in India, career opportunities are often more limited regionally. Many employees at the Chennai location have therefore been doing the same job for years, but are still highly motivated and enjoy their work. India is also very family-oriented. In Germany, the role of the employee is often separated from that of the family. My assembly manager knows the employees’ families and visits them regularly. Family Day, which we hold once a year, is a big event. When you see the employees as part of the BMW family, a completely different energy and joy in work arises. In Germany, the concept of a “big family” sounds nice, but here it is actually lived.
The BMW family is currently embarking on a new cooperation with Tata in the form of the joint venture BMW Techworks India, which is to develop global software solutions for both business and vehicle IT. Here in your assembly halls, the developers from India will come into contact with the end products. What does that mean for you and your team?
For us, this means being able to convey the joy of our products to our new colleagues in the IT department. It definitely does something to a person when they see our products, come into contact with them and work on them. If we can transport this enthusiasm to the IT department, we create a strong connection to our vehicles. That’s why we want to carry out introductory training courses at the factory to strengthen this connection.
And on the other hand, what concrete added value do you hope to gain from the collaboration for your processes here in the factory?
The joint venture will be strongly focused on building, designing and maintaining our IT landscape. It is always better to be close to the product and process in order to develop IT solutions that are tailored to the needs. It is a mutual fertilization: improvements from production flow into IT, and vice versa, we can benefit from new IT technologies. And this collaboration works much better when people meet in person. One tour replaces 1,000 meetings.
Since your arrival in 2019, you have placed a strong focus on the sustainability of the site. What measures have you been able to implement so far?
At our plant, we pursue a variety of sustainability measures that help us significantly reduce our environmental impact. Our central goal is to gradually switch the three main resource lines - water, gas and electricity - to alternatives with a lower footprint. When I came here in 2019, there was a major drought and we had a really severe water shortage. When we were fortunate enough to get rain again, we immediately got to work creating rain retention systems. By collecting and treating rainwater, including using wells and pond systems, we were able to eliminate the need for purchased water and are now independent when it comes to this resource. We use this water not only for everyday thingssuch as flushing toilets, but also for technical processes such as water testing on vehicles. After that, we also reduced gas consumption. We used to use natural gas in the paint shop, the kitchen and other areas. Today, these systems have been converted to run on electricity from the solar panels on our roof. We are currently working on optimizing our overall electricity consumption. We already cover 50 percent of our energy needs with solar energy, and we plan to increase this share further. We are also working on storage options for our solar energy and alternative air conditioning systems to save on compressors.
Finally, what is your vision for the Chennai plant over the next five years?
The Chennai plant and the entire organization in India have achieved a high status in the BMW world: from a relatively unknown, far-away production site to a jewel in the network. We have worked hard on this in the past and now India is seen as an equal partner. I hope that this development will be intensified in the future of the plant. Among other things, we should ask ourselves how we can use our well-trained employees even better in the network. At the same time, we want to invite other production sites to come to India and learn from us. I believe that this mutual fertilization is extremely important. Especially in view of the increasingly difficult geopolitical situation. What is happening on the global work level at BMW is fantastic. It shows how strongly the BMW logo unites us. That is also myVision for the future: to promote further cooperation and exchange.