Stellantis turns to AI tools and fast deployment to cut production costs and launch times
Stellantis chief manufacturing officer Arnaud Deboeuf reveals technologies across automation, factory planning and lineside logistics that reduce transition costs and time to market.

At a roundtable event at the Stellantis ‘Factory Booster Day’ on September 18, an annual innovation forum bringing together the carmaker’s plant leadership and key suppliers, senior manufacturing leaders presented a range of artificial intelligence-based tools and systems that were aimed at solving real-world problems across the company’s plants. The solutions showcased included technology to improve how existing robots track parts, a system to retrofit carts and dollies into autonomous mobile robots (AMRs,), as well as large scale, cloud-based digital platforms that support factory planning across design, construction and production operations all combined.
Arnaud Deboeuf, Stellantis chief manufacturing officer, and Jean-Christophe Marchal, senior vice-president of vehicle process engineering, put a strong emphasis on solutions that could be implemented quickly, and without major factory rework, rather than those that might require considerable redesign and implementation costs.
Opening the roundtable discussion, Deboeuf noted that each of Stellantis’ 80 production plants is invited to raise a challenge on certain problems they are facing. This list of challenges is shared with partners, ranging from big suppliers to small startups and universities, inviting them to develop solutions.
“What we are sharing today is that we are doing step-by-step improvements, super-pragmatic, based on the problems we at Stellantis have,” Deboeuf told journalists including AMS. “Our clients [and plant managers] are raising problems, and our partners are bringing solutions. We implement them quickly and with a global view.”
This is clearly an important exercise in the current manufacturing climate where costs are increasing and the need for flexibility and efficiency are high priorities. “We have a big ambition for manufacturing to reduce our transformation costs globally by 40%…” said Deboeuf, referring to the carmaker’s Dare Forward 2030 strategic plan, which includes an objective to reduce manufacturing costs by 30%, as well as to achieve carbon neutrality by 2038.
“What we are sharing today is that we are doing step-by-step improvements, super-pragmatic, based on the problems we at Stellantis have. Our [plant managers] are raising problems, and our partners are bringing solutions. We implement them quickly and with a global view.”
Arnaud Deboeuf, Stellantis
Small steps, big gains?
Cost certainly seems to be at the forefront of these solutions, and while Stellantis is still making large capital investments in its manufacturing operations (including recent investments in Michigan for EV and energy storage), it is also focused on cost effective upgrades to brown field sites that can deliver considerable benefits to ongoing production.
A good example of doing a lot with seemingly little is a solution from Norwegian robotics start up wheel.me. This involves replacing the standard casters on the carts and dollies used to transport parts and materials around the factory floor, with autonomous wheels, effectively converting these basic transport units into AMRs. This system is currently in use at the OEM’s Sterling Heights Assembly plant in Michigan, supporting RAM pickup truck production. (Read more on logistics automation technology for Stellantis at AMS sister title, Automotive Logistics.)
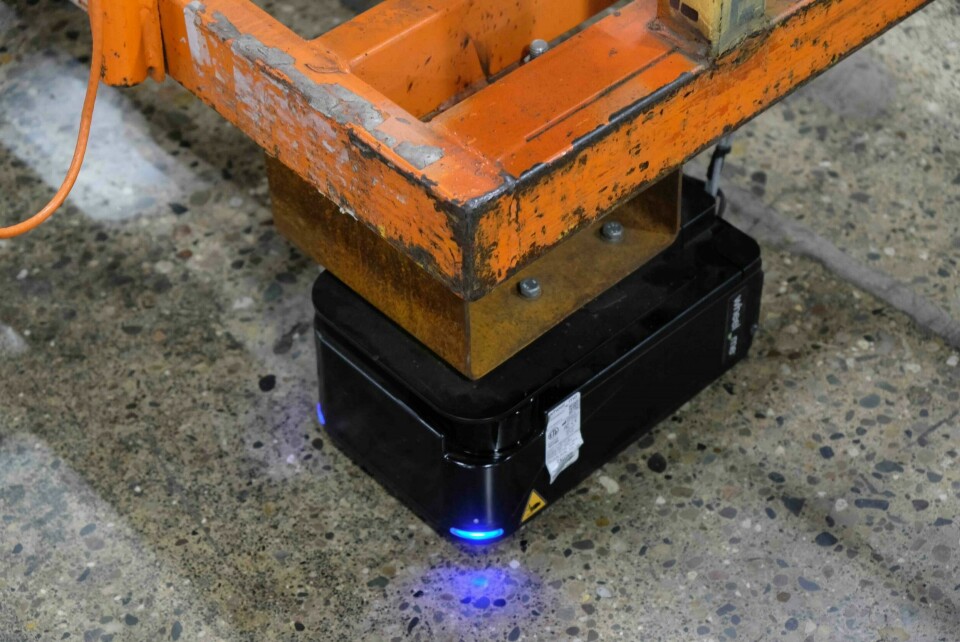
Stellantis is working with Norway’s wheel.me on a solution that retrofits dollies and turns them into AMRs
“We want to have this transportation done in an efficient manner and to be able to design, implement, and manage different sizes of containers, not just a single standard,” said Jean-Christophe Marchal, who also pointed out that plant logistics automation has generall lagged other plant functions in digitalisation and robotics, partly as a result of container, plant layout and design costs.
“Compared to what you see normally in the plant, we can convert existing trailers and equipment into autonomous vehicles without major changes, which was exactly what we needed,” added Deboeuf. “It’s a perfect fit for our compact plants where space is limited.”
Also working on upgrading existing equipment is French startup Inbolt. According to co-founder Albane Dersy, the company’s target is to upgrade the capabilities of standard industrial robots combining AI and vision systems. Dersy said this system enables robots to adjust their trajectory and operations in real-time avoiding conflicts or impacts.
“We make industrial robots smarter with AI-powered software that processes data from a 3D camera mounted on the robot at a very high speed to enable the robot to do real-time decision making, basically as a worker would do,” Dersy said. “What usually makes automation really hard is that robots are blind machines. By having a vision system, we are able to automate a workstation without transforming the working environment.”
Deboeuf noted that this solution met the requirements of several challenges that had been raise by the plants. These include improving the workplace by automating tasks that are ergonomically challenging to perform manually, improving quality and reducing transformation costs.
Cloud to help scale simultaneous engineering
Whilst wheel.me and Inbolt address very specific applications, Stellantis also revealed more about its plans to create digital factory twins and improve design and engineering processes that impact manufacturing, as part of design-for-manufacture optimisation strategies. Stellantis has been using a cloud-based platform from Autodesk called Construction Cloud to facilitate an upstream, simultaneous engineering process to engage with all the stakeholders (including line integrators, paintshop, bodyshop, etc.) in the virtual design, development and validation of new production operations (plants) and vehicle platforms.
This project offers advantages in reducing production costs and potential overspends, as well as shortening the design, development, production project timeline, according to Marchal.
Marchal commented that this platform would create an ecosystem for all stake holders involved in any given part of a project to engage and interact alongside the Stellantis teams. “It’s about making sure we are designing an efficient process, for sure, but also in a short timeframe, avoiding mistakes, and creating an ecosystem in which everybody can interact in an efficient manner,” he said.
Deboeuf wouldn’t comment on any specific targets for reducing vehicle development and implementation cycles except to note that Stellantis has shortened this process in line with current industry benchmarks.
Currently, Stellantis is using the Construction Cloud in the design and engineering phase, including at its Windsor assembly plant, where it was instrumental in reducing setup time and improving overall design quality. However, it is yet used to change operations on the shopfloor. Dr. Alexander Stern, manufacturing strategy lead from Autodesk, said that it will be possible to connect these processes. The system is geared towards both design and validation, as well as build and operating stage. “Once you have a validated 3D model, you can use that to continuously optimise,” he said.
Stern pointed to customers, including Magna, who are already are already leveraging design and engineering data from the cloud directly into manufacturing. “It is obviously a matter of data quality and some differences between brownfield and greenfield plants,” he said. “But once you have a validated 3D model, you can use that to continuously optimise”
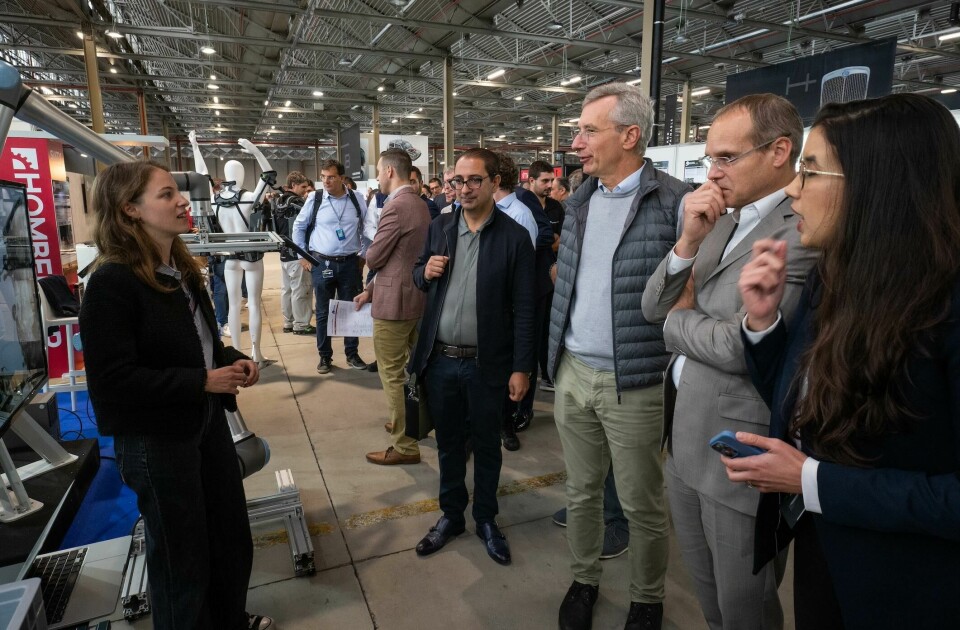
Stellantis is implementing tools that require minimal downtime and transformation costs, including Inbolt’s vision system and a digital twin cloud system with Autodesk
According to Marchal, Stellantis is in the process of digitally scanning all its plants, starting with those that have major vehicle projects planned.
AI is the enabling tool
Artificial intelligence is becoming a key tool in Stellantis’ digital transformation of manufacturing. Although not part of the roundtable presentation, Deboeuf also highlighted a predictive maintenance project that uses generative AI, which has been in progress for the last two years with positive results.
”Every night, we download all the problems that we have had in the plants that day, and the processes for solving the problems,” he said. “All this data is downloaded into the system so, whenever you raise a problem, the system provides specific information on how this has been managed previously in another plant, another country with the same equipment.”
“This is the first step, which is already in place and deployed across 28 locations worldwide, all connecting to this predictive maintenance system. What we now want to develop is how can we have predictive maintenance system that also provides the solution.”
Incremental development Vs Big Capex projects
All carmakers are trying to manage the shift to electric vehicle production and the current market woes that are requiring a rethink on strategy, projects and costs. Stellantis recently announced a significant drop in profits, and CEO Carlos Tavares has emphasised the need for efficiency improvements in producing electric vehicles, and as the carmaker faces strong competition, including from Chinese OEMs. In Germany, Volkswagen is considering closing plants for the first time in its history.
However, the projects at Factory Booster Day demonstrate how the carmaker prefers digitalisation that plant managers can implement directly without large capital expenditure or large teams required for installation. “We are looking for solutions which the plant managers love, want to implement, and can manage by themselves,” Marchal said. “We don’t want process engineering teams to spend time adapting or modifying the path for equipment or containers, and we want to avoid digging or building anything on the shop floor.”
“We are looking for solutions which the plant managers love, want to implement, and can manage by themselves. We don’t want process engineering teams to spend time adapting or modifying the path for equipment or containers, and we want to avoid digging or building anything on the shop floor.”
Jean-Christophe Marchal, Stellantis
Asked about big change programmes such as the gigacasting, that have been pursued by competitors, such as Tesla and Volvo Cars, Deboeuf observed that in that specific case Stellantis had reviewed the process but didn’t see enough benefits across a number of metrics for it to warrant the high level of investment required. He pointed to the innovations from the Factory Booster Days as positive and importantly cost-effective solutions that delivered tangible benefits.
Stellantis is continuing to make large investments in transitioning its production operation to EVs, but it also sees clear benefits to a more incremental approach. According to Deboeuf, implementing innovations such as those from the event, along with continuous improvement and lean processes, has reduced transformation costs by 11%, energy consumption by 23%, and quality issues by 40% since 2021.
“Leveraging the latest technologies, especially AI, is a significant lever to achieve the level of excellence we are aiming for,” he said.