The recent installation of what is claimed to be the biggest ever servopress machine anywhere in global automotive metalforming sector demonstrates the key advances made in pressing technology
Servo press technology has been making increasing inroads into automotive metalforming applications for some time now. The reasons are not particular to the demands of the automotive sector but reflect the advantages the technology can bring to manufacturing processes. The most crucial of these is simply the element of control flexibility that servo presses can provide; the motion of the slide is driven directly by the motor and can be varied during a single operation – speeded up, slowed down or made to dwell – according to requirements. The consequence is an enhanced ability to form parts accurately and without compromise to material quality irrespective of the intended part geometry.
The technique has two older rival pressing technologies. These are non-servo mechanical presses – in which the energy of the motor is transmitted to the slide via a complex system involving a clutch, gears and flywheel – and hydraulic presses – in which the motor drives a hydraulic pump which in turn actuates a piston-cylinder unit to drive the slide. Both still have their uses but neither can match the intrinsic flexibility of servo presses because in both cases the slide motion is fixed in both amplitude and speed.Moreover, the advance of servo press technology in the automotive manufacturing sector has recently taken a giant step forward – quite literally, with the recent commissioning of what is claimed, plausibly, to be the biggest such machine in use in the sector anywhere. The machine in question is now in operation at the plant in Bielefeld, Germany, of Spanish-owned component maker Gestamp Automoción. Appropriately, the machine itself has Spanish origins since the project to design and install it was carried out by a team drawn from both Bielefeld and the Logroño, Spain, office of Japanese-Spanish equipment supplier Nidec ARISA.
Big in BielefeldThe sheer dimensions of the installation, which was shipped to Germany last December, indicate just how unusual it is. The whole thing is 37 metres in length, 20 metres in width and rises 10 metres above ground level with a further six metres extending vertically in the opposite direction. Its total weight is 1,350 tonnes and it has a power rating of 9MW of torque and 7MW of energy storage effected through a system of compensation engines. All this enables the machine to deliver 45,000KN of force at the die surface.
The overall system is configured as a single press with two carriages and three uprights, which makes it capable of levelling the eccentric loads of the die. The machine is fed by means of a format destacker with multiple loading stations in order to support ergonomic efficiency for machine operators. Meanwhile, a conveyor belt system transports materials through an oil-programmable band lubricator in order to ensure the best oil application level for each operation. The die change system, including change of references in the unstacker, is fully automated.
Off-line programming is effected through Nidec ARISA’s own Optiservo software, which has been specially written to take account of the fact that the company’s servo presses have an open curve capability that enables the operator to create as many different curves as needed. Specifically, the software enables a production engineer to simulate and optimise the curves without stopping production, both reducing set-up times and preventing collisions.
"The specifications and the continuous and quick development of the automotive industry make it necessary to have very accurate and flexible machines that are able to work with different materials and dies at the maximum speed and the minimum energy consumption" - Roberto Gonzalo, Nidec ARISA
The details are confirmed by Roberto Gonzalo, responsible for project management at Nidec ARISA, who also says that the Bielefeld installation represents the biggest servo press application that the company has so far implemented – “and for a tandem double servo press,” he adds. Nevertheless, the record may soon be at least equalled if not exceeded since Gonzalo explains that “we are also doing other machines with similar dimensions”.
A new frontierAccording to Gonzalo, the project to design and build the new servo press installation at Bielefeld involved confronting some fundamental questions about how its performance objectives could be achieved. “During the design process, we had to deal with the fact that the requirements for the printing processes to cope with new materials with high tensile strength, especially the differences of force between the first and subsequent forming stations, cause problems in the deformations of the transfer presses,” he reports.
A number of possible solutions presented themselves, including the use of an individual press prior to the transfer press, though, as Gonzalo states, this approach would be far from straightforward. “The deformation processes, which would normally be deep-drawing, require high forces,” he says, explaining that this might compromise the symmetry of the die loads in the press. However, the major disadvantage of such a system would be an overall reduced performance due to the need to move the parts from one press to another.
Another possible solution would have been to manufacture a standalone asymmetric press, which would allow the deformations caused by the forces generated during use to be compensated for by the asymmetric structure of the press. But, again, this option was not without its accompanying problems. “This solution would be feasible as long as the dimensions required for the die were such that a single carriage press could not be manufactured,” states Gonzalo. “In addition, such a press would cause asymmetric deformations when working with dies with the distribution of cantered loads.”
Therefore, Gonzalo continues, the technical solution chosen was to acquire a single press with two carriages and three uprights, capable of levelling the eccentric loads of the die and with sufficient die dimensions for a wide range of present and future work. It was implicit in this option that “the press should have servo drive” in order to achieve the necessary quality levels, which, along with its transfer process, would also allow for a high production rate. “The high tensile strength material needs a very accurate forming speed in order to achieve the required part quality,” he says. “This is only possible with the precise speed control of servo presses.” Moreover, during construction the challenge was to build and mount components weighing more than 200 tonnes to accuracies of less than 0.1mm.
Keeping the customer satisfiedGonzalo adds that this level of performance requirement, though not unique to the automotive industry, is now typical to it. “The specifications and the continuous and quick development of the automotive industry make it necessary to have very accurate and flexible machines that are able to work with different materials and dies at the maximum speed and the minimum energy consumption,” he states. “Only servo presses can satisfy all these requirements.”
Meanwhile, the user of the press indicates that the new machine is fulfilling expectations. According to Lutz Huxholl, Gestamp Bielefeld plant manager, the press is now successfully making “mainly chassis” parts for several major customers from high-strength steel. The parts include “spring links and lower control arms”.
As for the scale of the installation, Huxholl says that apart from its ability to tackle immediate manufacturing tasks, Gestamp also regards it as providing a degree of future-proofing and even of enhanced credibility in the market. “With this investment, the Gestamp Bielefeld plant is heading towards the future as well as ensuring it is competitive in the present,” he states. “This servo transfer press opens up various new manufacturing options. It is always important for automotive suppliers to be equipped with modern production facilities. Furthermore, such a servo transfer press provides a unique selling point.”
Improving energy managementBut servo press technology is also making a significant impact in the industry on the other side of the Atlantic. A major supplier of the technology there is Komatsu North America. Product manager George Schreck acknowledges that precise control of the slide motion is a key attribute of the technology, while pointing out that it also represents a distinct advance in “energy management” compared with flywheel-based counterparts. The key limitation with the latter, he says, is that they can only deliver energy to the slide when they are spinning at a fast rate, which means that the slide motion has to be quick as well. But the technology is in any case intrinsically more energy efficient.
On that count, Schreck says that testing carried out by Komatsu in cooperation with a third-party agency has shown that “during physical work a servo press is 30-40% more energy efficient than one using a flywheel.” The saving in comparison with a hydraulic press would, he adds, be even greater.
This does not mean that there are no circumstances in which either hydraulic or flywheel-based presses would be more appropriate techniques to use. The former, notes Schreck, has superior “deep drawing” capabilities while the latter makes more sense in the case of a high but single-speed slide motion that does not require advanced control capability. Nevertheless, Schreck confirms, there is an increasing market preference for servo press technology. In the case of Komatsu North America, he adds, that is evident from the fact that “seven out of ten” sales of mechanical presses are now of servo type machines.
A first step for FCA at WarrenOne major vehicle-maker in North America which first explored the use of servo press machines as primary manufacturing systems as recently as last year is FCA US. In January 2016, the company started production on a new, $63m, 180-inch wide servo tandem press line at its Warren Stamping Plant in Michigan, supplied by Komatsu. Within six months, FCA had commissioned two further identical installations at its Sterling Stamping Plant, also in Michigan.
The details are confirmed by Al Whitted, global head of press shops and dies for FCA, who says that although the company previously operated “some smaller servos” in other countries, the Warren installation was its first implementation of the technology “in the NAFTA region”. The immediate spur for the investment at Warren was, Whitted adds, simply a requirement for extra capacity. “We were having to offload work, and that imposes a huge price penalty,” he explains.
The decision to take this step into the new world of servo technology was, Whitted says, the result of a number of factors. One was the feedback the former Chrysler part of the company was able to glean from the previous Fiat experience of the technology - “our colleagues in EMEA”, as he describes them, though he notes that “they were also fairly new to it”. However, the main attraction was just the promise the technology held of increased output, enhanced flexibility, energy efficiency and decreased die changeover times. He indicates that all those expectations were fulfilled.
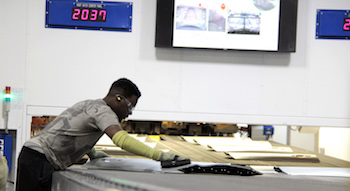
On that latter count, for example, Whitted reports that: “We have some old lines where the die change can take 40 minutes, whereas on these new lines that can take just two to three minutes.” However, the reason for that is less the servo technology itself than the modernity of the equipment. “Our previous newest such systems were 20 years old,” he admits.
So far, the new servo systems at both plants have been used for the production of existing parts but, says Whitted, that is soon about to change. “We have got the JL coming up, which is our new Jeep Wrangler, and our new Ram pick-up truck, and we have designed the dies for them specifically for the servo presses,” he confirms. The launch dates for those vehicles will be, respectively, November of this year and Q1 of next year with part production preceding those dates by appropriate margins.
When that happens, Whitted adds, the new machines will run “at 100% capacity”, though they are already close to that level because the company has pulled as many jobs as possible from older crossbar machines and transferred them to the servos, modifying the dies where necessary. The consequence for the parts involved, he reports, was a “30% increase in speed”. Though he refrains from giving actual production figures, Whitted says that “parts we used to run at nine strokes per minute we now run at 12 strokes per minute and we expect to run them even faster when we start using the dies that have been specially designed for them.”
Given the size of the machines, Whitted says that the company’s intention is to run “all of its really big parts in them”. He gives the examples of “body side apertures, double door inners and outers and hood inners and outers”. Their role in the successful launch of the new vehicles will be “critical”, says Whitted.
On the point of the dies designed for the servo machines, Whitted says that one thing that becomes possible is to make them “with a lower profile” than has been the case previously. In turn, that enables parts to be transferred “from one station to the next” faster than might otherwise be possible. The significance is that each of the new servo installations comprises five immediately co-located presses in sequence – that is the meaning of the word ‘tandem’ in this context – with the lead press rated at 2,400 tons and the other four at 1,200 tons.
"We have some old lines where the die change can take 40 minutes, whereas on these new lines that can take just two to three minutes" - Al Whitted, FCA US
Given that the new machines represented a first foray into a new type of technology, a lot of preparatory work was necessary. Again, though, the US operation was able to draw on experience in parallel operations in the former Fiat business. “We had a lot of read-across from EMEA,” says Whitted, adding that a “big cross-section” of personnel from the US were deployed worldwide to familiarise themselves with the requirements for successful servo operation: “We sent them to Serbia, Italy and Japan.”
In consequence, the commissioning process for the Warren Stamping installation was, Whitted suggests, not overly problematical. It was even less so for the two at Sterling, which benefitted from the experience at Warren.
Whitted says that the company is still “learning every day” about how to get the most from the technology, but he can pinpoint some of the key lessons so far. The first is the necessity for the inclusion of people at all levels and from all relevant technology areas, from as far upstream as die design and as far downstream as maintenance, in the planning as well as practical implementation processes. The second is to effectively integrate of all supporting technologies - “robots, washer units, destackers – if those things are not properly integrated then however sophisticated the press technology, the installation won’t run.”
Nevertheless, the potential of the technology to improve production processes has also become evident. Whitted says that what has impressed him and FCA US most is the capability it provides “to put the tonnage exactly where we need it on the part”.