BYD has surged onto the global stage, challenging industry giants like Tesla with its aggressive expansion and pioneering battery technology. BYD’s production soared from half a million to over 4 million vehicles. As the company celebrates its 30th anniversary, its blend of vertical integration, cutting-edge automation, and global supply chain mastery has redefined the EV landscape.
Chinese electric vehicles have been making waves overseas in the last few years, especially in places like Mexico, Malaysia, and Thailand. A big part of their appeal is the price tag – these cars usually cost a lot less than their Japanese, South Korean, or European rivals. But if you ask Chinese EV makers, they’ll tell you it’s not just about saving money, they say their cars bring a whole new level of innovation to the table.
In recent years, Chinese carmaker BYD has experienced remarkable growth and success. The numbers tell a compelling story: BYD’s production has surged from approximately 500,000 units to over 4 million in almost seven years. This represents an over 700% increase, a clear indicator of the company’s aggressive expansion strategy. BYD nearly caught up to Tesla in 2024 pure EV deliveries (1.76 million vs. 1.79 million) but stole the show with plug-in hybrids, firmly securing its spot as the world’s top new energy vehicle maker.
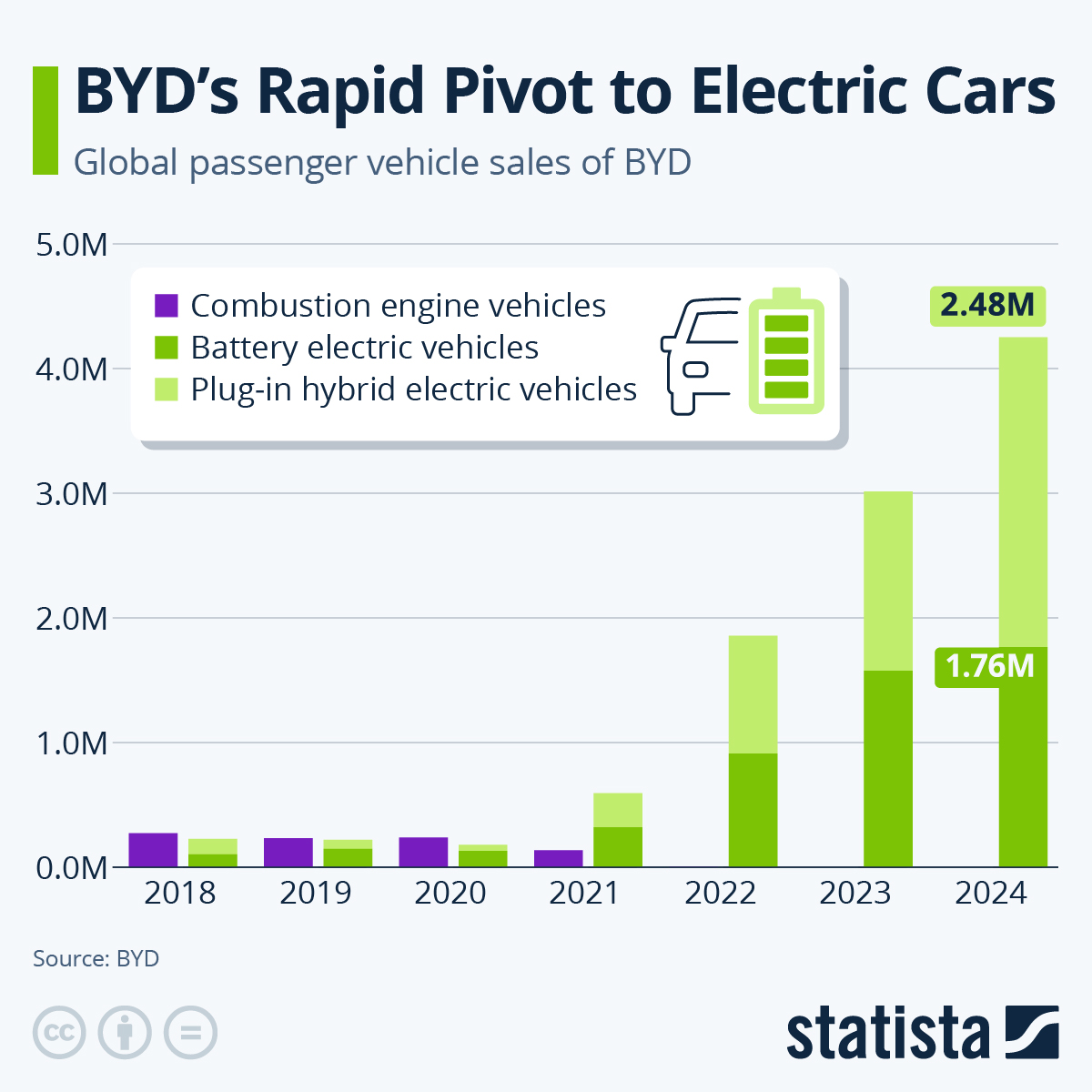
It didn’t stop there; BYD surged past Tesla in Q3 revenue, bringing in $28.2 billion to Tesla’s $25.18 billion. December marked yet another milestone with BYD’s 10 millionth plug-in vehicle rolling off the line. And all of this comes just in time for the company’s 30th anniversary. This growth, driven by their focus on New Energy Vehicles (NEVs), has propelled them to the forefront of the global automotive industry.
Production network and strategy
BYD’s manufacturing footprint spans multiple continents, with a significant concentration in China. Key facilities include the Xi’an plant in Shaanxi, with an annual production capacity of 900,000 vehicles, and the Changsha plant in Hunan, capable of producing 600,000 vehicles annually. The Hefei facility in Anhui, operational since June 2022, is set to reach a capacity of 1.32 million vehicles upon completion of its three-phase development. Collectively, BYD’s domestic production capacity in China has reached 5.82 million vehicles annually as of 2024.
Internationally, BYD has expanded its presence with manufacturing plants in several countries. In July 2024, the company inaugurated a facility in Rayong, Thailand, with an annual capacity of 150,000 vehicles. This plant is BYD’s first wholly-owned operation outside of China and is expected to employ 10,000 workers. Additionally, BYD has announced investments in Szegad Hungary along with Camaçari, Brazil, and Manisa, Turkey, each projected to produce 150,000 vehicles annually upon commencement in 2025 and 2026, respectively.
Battery production and innovation
BYD’s top-notch battery manufacturing lies at the heart of its success in the electric vehicle market. The company’s subsidiary, FinDreams Battery Co., focuses on lithium iron phosphate (LFP) technology, featuring the groundbreaking “Blade Battery,” celebrated for remarkable safety and efficiency. As of December 2023, FinDreams Battery held its place as the world’s second-largest EV battery manufacturer, behind CATL.
Also read: How BYD’s partnership with Apple shaped the future of EV battery technology
To secure a steady supply of critical raw materials, BYD has moved into mining operations. In 2023, the company secured mining rights in Brazil’s “Lithium Valley,” marking its first mining investment beyond China. Looking forward, the company expects to unveil solid-state EV batteries by 2027, aiming to boost energy density and safety.
Gallery: BYD in production
So how did BYD grow its production volume so rapidly?
BYD’s success in rapidly scaling up to become a leading global EV manufacturer can be largely attributed to a strategic approach that weaves together production innovation, supply chain optimisation, and deep vertical integration. Over the past decade, the company has leveraged its heritage in battery production to build a robust ecosystem stretching from raw material sourcing to final vehicle assembly. This strategic control has minimised external dependencies, reducing exposure to both cost fluctuations and supply constraints. At the same time, BYD’s emphasis on advanced production processes has facilitated consistent model rollouts, even amid growing demand across international markets.
1. Vertical integration
One of BYD’s defining strategies has been the in-house production of key components. Rather than relying on external suppliers for core components, BYD manufactures batteries, power electronics, electric motors, and semiconductors in-house. This vertically integrated model became more prominent after the launch of the Blade Battery in 2020, which introduced a new cell-to-pack format, noted for enhanced safety and improved energy density.
“The battery is up to 40% of an EV’s cost,” says Wang Chuanfu, BYD’s founder and chairman. “Our in-house control over this is our competitive edge.”
BYD’s production line is highly automated, featuring robotic handling systems that not only accelerate assembly but also maintain exacting quality standards. Since its introduction, the Blade Battery has been deployed across multiple BYD models, contributing to lower manufacturing costs by consolidating module assembly and eliminating conventional pack structures. By late 2022, BYD’s total battery production capacity had surpassed 135 GWh, enabling the company to meet soaring NEV demand while controlling costs.
This strategy contributed to the company delivering 1.86 million new energy vehicles in 2022, nearly triple the volume of the previous year. Unlike BYD, Tesla relies on external suppliers like CATL or LG Energy Solution for a significant share of its batteries.
2. Platform standardisation & modular design
Another crucial element of BYD’s strategy is the use of platform standardisation and modular architecture. The e-Platform 3.0, introduced in 2021, consolidated core EV elements – such as the motor, controller, and chassis – into a single framework. This design reduced parts count and simplified assembly, enabling production lines to switch between different vehicle models with relative ease.
In practical terms, a shared platform also streamlines parts sourcing and logistics, as consistent components can be utilised across multiple vehicle lines. This commonality - an example of Design for Manufacture (DFM) - not only saves costs but also allows BYD to pivot quickly in response to shifting market trends. As an example, models such as the BYD Dolphin and Seal, both built around the e-Platform 3.0, were taken from concept to commercial production in well under two years. In addition to cutting manufacturing times, this approach made it easier to share components across multiple product lines, streamlining procurement and helping maintain consistent quality standards.
3. Simultaneous engineering & rapid product development
Another crucial factor in BYD’s rise is its simultaneous engineering methodology. Rather than isolating design, engineering, and manufacturing functions, BYD’s teams operate in parallel from the early concept stage through to production. By integrating R&D, design, and manufacturing decisions, BYD can rapidly incorporate new features or rectify potential production hurdles.
“A BYD car, comparable to the Model 3, costs 15% less than production in Tesla’s Shanghai gigafactory.”
A prime example is how the Song, Qin, and Han model ranges share core components – such as chassis, electrical architectures, and battery systems – significantly reducing customisation complexity and parts duplication. This commonality also speeds up product updates; for instance, when BYD rolled out software enhancements for the Qin and Han in 2022, production lines were able to incorporate changes mid-cycle without lengthy retooling or halts.
4. Automation & gigacasting
High levels of automation have played a key role in BYD’s ability to scale. Automation extends from welding and painting, to pack assembly and final inspection, supported by real-time monitoring systems for quality control. BYD’s Xi’an plant reported 97% automation in 2020, using automated guided vehicles (AGVs), robots, and intelligent warehousing for maximal efficiency.
BYD maintains comprehensive in-house testing labs dedicated to batteries, motors, and electronics, employing high-precision equipment to detect faults at micro-levels. Coupled with real-time data analytics, these testing protocols minimise defects and enable proactive refinement of production parameters. According to the company’s 2022 annual report, iterative feedback loops – where test results feed directly back into design and assembly—helped BYD reduce component failure rates and enhance overall vehicle reliability. BYD is rolling out local datacentres across Europe to support its autonomous and internet-connected vehicles
Notably, while Tesla champions gigacasting, BYD currently utilises traditional stamped steel welding which contributes to reduced labour intensity and shorter cycle times. This shift to casting major components has slashed production steps by more than 30%, directly impacting throughput and unit cost. However, acknowledging potential cost efficiencies, they are reportedly evaluating the adoption of gigacasting technology.
5. Global supply chain coordination
Beyond China, BYD’s strategy of localising elements of production—such as electric bus chassis in Hungary and battery assembly in Brazil—demonstrates a flexible, region-specific approach to supply chain management. The ability to source components locally, align logistics precisely with production schedules, and collaborate with regional suppliers ensures stable inventory levels and cost efficiencies.
This model has been validated by BYD’s global expansion announcements, including facilities in Thailand aiming for 150,000 units of annual capacity by 2024 (as reported by the Thai government in partnership with BYD). Each new site leverages regional advantages, such as local raw material availability or automotive expertise, to extend BYD’s competitive edge.
“Our overseas market will account for a relatively large proportion of our global sales in the future,” Stella Li, CEO, BYD Americas
BYD is aiming for 5-6 million sales by 2025, with Stella Li, CEO of BYD Americas predicting “nearly half” from overseas. Additionally, Li emphasised, “We stand behind our products. As with any groundbreaking technology, there are challenges, but we are committed to ensuring the highest levels of safety and performance,” from a November 2023 statement.
Battery technology remains a key pillar of BYD’s strategy. As a pioneer in blade battery technology, the company is now developing next-generation solid-state batteries, which promise higher energy density, longer lifespan, and improved safety.
In addition to technological advancements, BYD is also focusing on fleet electrification and commercial vehicles, including electric buses and trucks, which are gaining traction globally. The company is further enhancing its models by integrating advanced driver assistance systems (ADAS) as a standard feature, providing cutting-edge safety and automation at no extra cost.
No comments yet