Los fabricantes de aceros de alta resistencia se posicionan ante el inminente dominio de los vehículos eléctricos. Informe de James Bakewell
En 2017 las ventas de vehículos eléctricos de baterías (VEB) y de híbridos enchufables (HE) alcanzaron los 1.3m de unidades, según Frédéric Painchault, director de marketing automotriz en la siderúrgica ArcelorMittal. "Se trata de una cuota muy reducida del total de vehículos, menos del 2%. Sin embargo, el mercado crece rápidamente, un 57% respecto a 2016. Las grandes marcas pretenden lanzar al mercado unos 340 modelos VEB y HE en los próximos tres años. Esto significa que deberían alcanzar los 5m de unidades para 2020”.
Y esto es solo el principio. Basjan Berkhout, director de marketing automotriz en Tata Steel Europa, comenta: “Tata Steel prevé que los vehículos eléctricos representarán el 90% de las ventas en la Unión Europea para 2050”.
El principal motivo para la transición a modelos eléctricos será la legislación medioambiental. La UE por ejemplo ya ha establecido que los nuevos autos deben emitir menos de 130g de dióxido de carbono por kilómetro recorrido. Este objetivo se reducirá a 95g por kilómetro en y probablemente será incluso más estricto para 2030.
El grado de implementación de los motores eléctricos varía de una región a otra. Berkhout afirma que la mayor influencia sigue siendo el mercado chino, donde el gobierno ya estableció cuotas obligatorias de producción de VE a las marcas que operan en el país con el fin de reducir las emisiones. China es el principal mercado para la mayoría de las marcas, por lo que ignorar sus exigencias podría ser desastroso. Otro punto de presión son los objetivos de calidad del aire en las grandes ciudades. La limitación de las emisiones en la UE también ha vivido una mayor presión después de la crisis del diésel y el inminente cambio de estándares con la aplicación del nuevo test WLTP de emisiones.
Painchault añade: “La incertidumbre de la normativa Corporate Average Fuel Economy [CAFE] en Estados Unidos podría significar que se modere el crecimiento en la región del TLCAN. En Europa y China, ArcelorMittal prevé que las ventas de vehículos VEB y HE superarán las ventas de motores de combustión interna (MCI) en torno a 2025. El principal crecimiento se producirá en los híbridos enchufables. Prevemos que para 2030 cada tipo de vehículo – VEB, HE y MCI – representará un tercio de las ventas. Dentro de 15 a 20 años los vehículos eléctricos dominarán el mercado”.
Obteniendo un lugar en el futuro eléctrico
La industria del acero se suele mostrar optimista sobre el futuro eléctrico. Por ejemplo, en un reciente informe de Tata Steels afirman que el aumento de la demanda de vehículos de emisiones mínimas aumentará el consumo de acero de la industria automotriz en 4.2m de toneladas solo en Europa.
En los últimos años, la innovación y los beneficios han llegado al sector de materiales automotrices de la mano de la necesidad de productos más ligeros y resistentes que permitan a los fabricantes reducir el peso de los vehículos MCI para reducir el consumo de combustible y las emisiones de dióxido de carbono. Sucede lo mismo en los primeros modelos eléctricos, como el BMW i3 o Tesla Model S, los materiales ligeros también han sido la clave (plásticos reforzados con fibra de carbono (CFRP) y aluminio, respectivamente).
Con los vehículos MCI los consumidores están acostumbrados a poder conducir varios cientos de kilómetros sin necesidad de repostar. Para alcanzar el mismo nivel de autonomía los vehículos eléctricos necesitan una batería muy grande, pesada y costosa, lo que significa que las marcas deben reducir el peso por otros lados. ¿Esto será siempre así?
El presidente de automotriz de NanoSteel, Craig Parsons, comenta: "Sí, es probable que los vehículos eléctricos tengan más incentivos para reducir el peso que los MCI. Una batería tiene una capacidad limitada para almacenar energía, y por lo tanto una autonomía limitada, reducir el peso representa un aumento directo en la autonomía, la principal preocupación con los vehículos eléctricos. Las baterías son muy pesadas y cada gramo ahorrado en el vehículo ofrece más espacio para una mayor batería y/o una batería menos potente pero con mayor autonomía".
El director de desarrollo de negocio automotriz en SSAB, Jonas Adolfsson, se muestra de acuerdo. Afirma que con indiferencia del motor utilizado, el desplazamiento de vehículo sigue respondiendo a las mismas leyes de la física. Las fuerzas contra el desplazamiento son la aceleración, resistencia al rodamiento, la pendiente y la resistencia al viento. Todas menos la última están muy influenciadas por el peso del vehículo. Comenta: "Las baterías tienen una densidad de energía muy inferior [Vatios por kilogramo] que la gasolina o el diésel, por lo que considero que reducir el peso es incluso más importante".
"La reducción del peso tiene un impacto limitado en la extensión de la autonomía. Por ejemplo, una reducción de 100kg de peso tan solo aumenta la autonomía en 6 a 11 kilómetros…" – Jean-Luc Thirion, ArcelorMittalJean-Luc Thirion, director de investigación y desarrollo automotriz en ArcelorMittal, muestra otra opinión: "La reducción del peso tiene un impacto limitado en la extensión de la autonomía. Por ejemplo, una reducción de 100kg de peso tan solo aumenta la autonomía en 6 a 11 kilómetros. Para aumentar la autonomía es mucho mas fácil y menos costoso añadir más baterías. También es marginal el impacto de la reducción de peso en la velocidad punta y la aceleración. Una reducción de 100kg aumenta la velocidad punta en menos de un kilómetro por hora y el tiempo de aceleración en menos de medio segundo”.
Berkhout concuerda: “Todos los vehículos deberían ser tan ligeros y económicos como sea posible, pero con la tecnología actual los vehículos híbridos y eléctricos son un 20-30% más pesados. Un vehículo más ligero aumentará la autonomía de un vehículo eléctrico o híbrido, pero con un mayor coste. ¿Una marca debería pagar mucho más por aligerar el vehículo y aumentar la autonomía mínimamente?”
Para responder utiliza el ejemplo del último VW Golf. La versión hatchback está disponible en gasolina, diésel, híbrido y eléctrico, la versión de gasolina tiene una tara de 1,206 kg, 1,301kg para el diésel, y las versiones híbrida y eléctrica pesan ambas 1,615 kg. La versión eléctrica tiene una autonomía de 300 km. Si se redujeran 10 kg de peso en la carrocería en bruto sería una reducción del 0.62% y aumentaría la autonomía del vehículo en 10km.
Los vehículos de baterías ya cuentan con tecnologías de recuperación de energía para aumentar su autonomía. Además debe tenerse en cuenta el desarrollo de la infraestructura. Un vehículo de baterías podría cargarse rápidamente durante la noche en el hogar del conductor, podría realizarse una carga lenta inalámbrica durante el desplazamiento o también podría cargarse automáticamente en el puesto de trabajo. En estos casos el uso de una batería capaz de acumular 300 km de viaje sin recarga sería redundante.Diferentes ensamblados de componentes y estructuras de vehículos
En caso de que estos conceptos sean correctos, la industria del acero tiene una gran oportunidad para reafirmar su dominio en el mercado automotriz. Las versiones eléctricas de los trenes de potencia pueden conllevar nuevas aplicaciones para aceros resistentes y maleables en la carrocería de estos vehículos.
Por ejemplo, Berkhout calcula que si el motor de combustión ya no está en el frontal del vehículo junto con el radiador y otros, y si la posición de los neumáticos frontales no está marcada por la posición del motor, entonces el frontal podría ser más corto. Si el frontal es más corto, entonces la longitud de la estructura de choque será más corta, pero tendrá que ser capaz de absorber la misma cantidad de energía en caso de un impacto frontal. Para ello podría ser necesario utilizar una barra de carga más grande con un acero de mayor grado y el soporte de la misma también tendría que soportar cargas mayores.
Continúa: “Si las baterías se ensamblan debajo del suelo, también tendrá que gestionarse de manera diferente la carga de impacto. Los motores actuales de combustión cuentan con refuerzos en los estribos y los travesaños de los asientos, estos apoyan al montante B en un impacto. Si se colocan las baterías donde normalmente se encuentran los travesaños de los asientos, la bandeja de la batería deberá ser capaz de resistir la carga de un impacto lateral. La batería del Opel Ampere pesa más de 400kg, de los cuales 70kg corresponden a la bandeja estructural de la batería. También genera cambios en los estribos que soportan la bandeja de baterías y que reciben una mayor carga”.
El director de tecnologías aplicadas de ThyssenKrupp, Lutz Keßler, se muestra de acuerdo con que la bandeja de baterías es el lugar ideal para utilizar aceros de alta resistencia. Comenta: “La batería es el núcleo de un vehículo eléctrico y el componente más sensible y costoso, representa entre el 30 y 50% del coste total del vehículo. Por ello es más importante desarrollar soluciones que protejan la batería y que no aumenten excesivamente el coste del vehículo eléctrico”.
Thirion añade: "Algunos productos disponibles hoy en día para el estampado en caliente, como el Usibor 2000 de ArcelorMittal pueden alcanzar una fuerza tensil de 2000 MPa. Hace dos décadas la máxima fuerza tensil era de tan solo 340MPa, por lo que es un aumento espectacular. Los grados martensiticos para la laminación por rodillos y el rango Fortiform de ArcelorMittal – la tercera generación de aceros de alta resistencia de estampado en frío – también ofrecen una gran fuerza tensil. Estos aceros permiten a los diseñadores de vehículos proteger la cabina del piloto y la batería de manera óptima".
De hecho, Tata prevé que la demanda europea de aceros avanzados para la estructura de estos vehículos aumentará en aproximadamente 2.6m de toneladas para 2050 a medida que los fabricantes intentan reducir peso de manera económica.
Aceros eléctricos para motores
Otra área clave de crecimiento para el acero serán los trenes de potencia utilizados en los vehículos de mínimas emisiones, incluyendo los motores eléctricos y baterías. Tata prevé que representarán un aumento de la demanda de acero en Europa de 1.6m de toneladas para 2050, estos componentes utilizarán un mayor nivel de aceros eléctricos y galvanizado respectivamente.
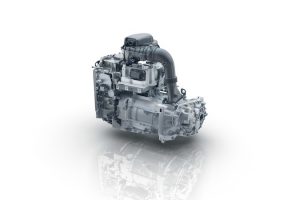
El acero eléctrico es un material esencial en la construcción de motores eléctricos y el grado de los aceros utilizados puede alterar el rendimiento de estas máquinas. Tata considera que será extremadamente importante para los constructores automotrices diferenciar sus trenes de potencia de los de la competencia. Los aceros eléctricos de alto rendimiento pueden mejorar la eficiencia de los motores, lo que permitirá aumentar la autonomía o mejorar el rendimiento dinámico del auto.
Por otro lado, las baterías de iones de litio – el sistema de almacenamiento de energía más común entre las marcas – se producen en tres formatos de batería: cilíndrica; prismática y en petaca. Los formatos cilíndrico y de petaca se suelen empaquetar en carcasas no ferrosas, mientras que las celdas cilíndricas se empaquetan en 'latas' niqueladas y serán probablemente las más comunes, por lo menos en un futuro cercano, ya que ofrecen un almacenamiento económico de la energía, fiable, relativamente fácil de producir y con una buena estabilidad mecánica. Estas últimas podrían producirse con aceros eléctricos.
Las siderúrgicas predicen que el aluminio y los plásticos CFRP tendrán un impacto reducido en estos vehículos por varios motivos.
En primer lugar, seguirán siendo excesivamente costosos. En segundo lugar, el acero demuestra mejores propiedades mecánicas, el acero es más rígido que el aluminio, tiene una mayor resistencia a la fatiga, además es más fácil de moldear, unir y pintar que otros materiales.
Keßler asegura: “A pesar de las ventajas que ofrece el acero, la competencia entre materiales seguirá siendo un reto. Por ello las siderúrgicas deben seguir investigando continuamente nuevas y mejores soluciones. En ThyssenKrupp por ejemplo estamos trabajando para reducir la brecha entre el conformado en frío y caliente, para ello ofrecemos oportuniades de conformado en frío con los nuevos aceros de fase dual y resistencia ultra-elevada de la clase 1200. Recientemente hemos desarrollado también una tecnología que – especialmente en los aceros de resistencia ultra-elevada – elimina el repliegue en la planta de prensado, reduce la cantidad de material usado y garantiza una mayor fiabilidad de proceso”.
Finalmente, se puede argumentar que el aluminio y los plásticos son menos sostenibles que el acero al analizar todo el ciclo vital, lo cual podría ser clave en el futuro de la industria automotriz. Thirion afirma: "La evaluación del ciclo de vida analiza todas las emisiones generadas en las tres fases de un vehículo: producción; uso y reciclado. Los estudios muestran que el aluminio emite de cuatro a cinco más veces de gases de efecto invernadero que el acero durante todo el ciclo vital de un vehículo”.
No sorprende que, según revela Berkhout, Tata Steel esté activamente promocionado que la UE utilice la medición del ciclo vital en las emisiones del vehículo.