戴姆勒在印度采用了以人为中心的方法改进制造厂
操作与制造工程副总裁Felix Homburg指出,我们在戴姆勒金奈卡车制造厂参观的起点是一个大型公告栏,上面有很多员工的激励方案。月度员工和“精益追逐”竞赛很普遍,但是这种活动的重要性可不容小觑,因为印度的以人为中心的汽车业非常依赖劳动力的付出,才能获得稳定的质量与产量标准。
装配车间非常巨大,可以看到两个主要生产线(一个是重型卡车,一个是中型卡车),在生产线牵头的会议区展示了工厂在操作交流机构上的透明度。在这里与团队和部门领导人开例会,这样所有人都可以讨论操作进度,可以与Homburg和其他高级经理讨论问题。这种开放式平台提供了更好的管理途径,并且能够促进员工之间更多的合作精神,Homburg强调这种精神对团队责任心的培养非常有益,也有利于团队建立信心和更高的参与度。
创建质量文化这里从车间到车辆,所有东西的规模都是巨大的,但是操作进度却是冷静的,有效率的。主要装配区域和小点的部件装配区域都是一尘不染的。公司非常重视创建一个快乐、健康的工厂工作环境。Homburg解释说,这对员工的参与度,效率的提高,以及创建质量文化都是有利的。
看到卡车装配之后走下生产线似乎挺简单。梯状底盘上有车轴、悬架、动力系统和驾驶室,这些都是沿着生产线,在不同的站点安装的。这种开放而简单的汽车构造是装配步骤直接。但是,这里还有很多因素,以及各种复杂性都在平衡两条装配线的过程中出现困难。
首先,根据不同的车型,在不同的工作站上回出现各种工作量,这是因为面对不同的市场,制造不同的汽车,零部件成分级别也大相径庭(比如新款3143 CM卡车,被誉为“霹雳火”)。我认为,加长平均制造时间会有利于平衡不同车型的制造,但是有趣的是,Homburg说,缩短平均时间才有利于提高质量以及产量。此外,有些零部件的物理尺寸和重量都非常巨大,这为去爱苏高效安装这些零部件提出了挑战。
“…我们的生产操作非常诱惑力,因此我们又能为为国内市场和出口市场制造车型” – Felix Homburg, 戴姆勒
把基础打好随着工厂上下人工操作水平的提高,工厂也努力在生产厂建设牢固的基础工艺和程序。这似乎非常依赖自我开发的开衫策略,才能优化效率、质量和生产力。在线侧轮胎安装区域里,我看到在操作流程总的一些细微变化,还有一些明智的方法,比如在货架、工具使用和送递中的人体工学,这些对整个流程的效率都起到了巨大的促进作用。轮胎和轮圈都很笨重巨大,但是他们使用简单而高效的推车,将轮胎送地道转配线工作站,使安装操作变得更加顺利。这个方法已经在戴姆勒的全球网络中共享。

零部件的配套组件可以极大提高错误改正和装配流程,这里的零部件箱子和货架都是由工人专门开发设计的,在车辆周围放置,并随着生产线向下移动。套件中的零部件摆放被称为“外科手术”,所有东西的位置都特定,可以随时拿到。这些装配已经开发很多,但是这些货架订制的速度却是令人瞠目结舌。这些特殊的团队得到预成型管子、连接器、支架和扣件,并且能够被呼叫到线侧,与任何这种型号的零部件现场进行测量和比对。这样就可以迅速进行改变和调整。正如Homburg强调的那样,这进一步鼓励工人思考自己的特殊工作,并想办法改进工艺。
专家项目除了持续实行各种小的改善措施之外,还有一些长期项目在进行之中。这些措施被称为“专家项目”,其中的一个项目就是为了改善驾驶室分布装配线效率的。Humburg解释说,这些项目已经开发执行了3个多月;驾驶室装配线一直在寻找方法,改善线侧零部件和材料的布置,并减少操作的空间。虽然大多数改善都需要低技术方法,但是我很吃惊地看到这里使用一个自动引导车(AGV),将驾驶室送递到主要装配线上。他们告诉我,这是为了研究提高大型驾驶室单元送递效率可行性而进行的试验系统。
生产Bharat Benz(9t-49t)卡车, FUSO(9t-49t)卡车,还有发动机和传动器
年产量根据倒班情况最高可以达到70,000辆
工厂占地 400 英亩,员工数量超过3,000人。这里是公司的总部,集中了研发中心以及专门的公交车工厂
车辆的85%的成分来自当地300多家供应商

复杂的的结构,建议的方案从变速器生产线也能看出,制造每个变速箱都需要机器复杂的工序,但是有一个非常简单的系统,能够利用彩色标识高尔夫球来指出有些组件什么时候需要更换。每个工人都必须集中精神,准时跟上装配步骤,比如将一些组件与加热到预制温度,才能使装配达到所要求的干涉配合。在我参观的时候,动力系统部门正要增加一个变速器生产线,为了出口生产更多的产品。为了这个目标,操作团队用硬纸板制造了一个复制品,带有完整的装配工作站、工具、设备、传送带。这个过程经过试用,计时和录像,从话费时间到人体工学环境等细节,是被各种问题,优化新生产线上所有部门的布置。
有了Oragadam这个卡车厂和附近新建的公交车生产厂,戴姆勒公司向人们展示了要挑战印度商务车部门市场份额的决心。工厂将继续扩大工厂建设,但是Homburg和他的团队没有透露增加生产什么产品。通过参观我发现,公司非常明白如何加强印度的劳动力水平,解决发展中的技术问题,创造主人翁精神。有趣的是,在这个所有的东西都是超大尺寸的工厂里,小而简单的革新却带来了巨大的变化。
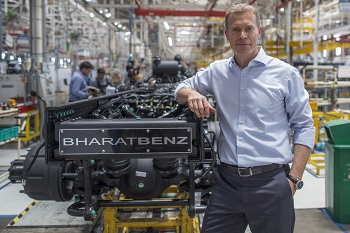
从2015年4月以来,Felix Homburg一直担任戴姆勒印度公司操作与制造工程副总裁。从2011年到2015年,他在戴姆勒南非Atlantis Foundries(在Cape Town附近)分公司担任执行董事。从大学电子工程专业毕业之后,2003年开始他进入戴姆勒国际管理联合项目部门工作,之后在Woerth(德国)、Portland/ Oregon(美国)、Saltillo(墨西哥)的戴姆勒卡车厂的制造部门工作。
AMS:在参观工厂的过程中,我们看到整个成产险上实行了很多小却很有效果的改善措施。您能说说这些方法吗?
Felix Homburg(FH):印度的改善措施非常明智而聪慧,而成本很少。我们发现,这些改善措施并不需要很大的预算;有人想到了一些方法,我们就自己实施。你在参观时看到了机动团队带来了所有的工具和预成型管子等东西,(在线侧)搭建新的推车。解决问题对我们非常重要,使我们场地管理重要的一部分。如果在生产质量并不能“监管”质量是,我们就能停止生产线。因此,即便是生产线停止也是我们解决常规问题的方法。
这些模块构建能让我们将劳动力融入到一种方法论当中,遵循工作指示标准。这让他们考虑问题的关键 — 即工作中需要改进的地方。这些改进通过改善策略和大型项目(我们称为“专家项目”)进行,这些可能需要3个月才能完成。为了促进这些改进措施,我们建立了一个“精益团队”,他们都受到这方面的高水平培训。但是,这些项目都是部门领导的责任,他们可以召唤精益团队成员来支持,构建工作。
我们还有指导委员会,每个季度都审核年度目标,审查所需要的措施和可获得的资源,并决定实施哪个项目。目前,我们与车轴供应商合作,正着手“端对端”项目,车轴和驾驶室生产线项目上实行准时化顺序供应,我们希望通过这个项目,把附加值和无附加值业务推到下一个阶段,从装配流程中消除大量的浪费。这个体系能够自己供应能源,因此成本效益很高,培训精良,更重要的是,这是一个人人都愿意的工作,人们愿意做贡献。
AMS:是什么确定驾驶室生产线是下一个大型改进项目呢?这里是否出现了瓶颈?
FH:实际是底盘生产线经历了更长的设计与效率提高,因此驾驶室生产线 — 相比之下 — 已经落后了,因此我们督促驾驶室生产团队跑步跟上来。
AMS:为出口而多生产的部分是否增加了生产操作的复杂性?
FH:你已经看到了,我们的生产设备非常强健,因此我们完全有能力为国内和出口市场生产新车型。我们已经建立了非常稳固的生产基础。这就是我们把出口车型的生产只是当做另一个变体生产的原因。
AMS: 你之前谈到过培训问题。这是怎么进行的呢,你们把员工送到德国去了吗?
FH:我们不需要。我们这里有一个综合性培训中心,除了入门培训之外 — 这非常有经验了 — 还有针对特殊职能的特殊培训,有理论的,也有实践的。我们把技术再推进了一步。比如说汽车电子技工,因为印度卡车排放量标准越来越严苛,就需要更高的电器水平,因此这些负责系统带来的潜在问题就需要技工在现场解决这些问题。
AMS:当初工厂开业时就称,这里生产的汽车本地化成分达到85%。这个比率增加了吗?
FH:是的,增加了,但我们没有公布确切的而数据。这个水平很高了,我们在当地采购九尾提高我们的成本以。我们知道,我们要向在印度追求竞争力,就要把本地化成分率提高到85%以上。
AMS:你们还在进口哪些零部件?
FH:更多的是复杂的组件 — 电子器件、能源系统等 — 这些我们还没有发现印度供应商。
我们已经有300多家供应商与我们合作。有些是德国的一级供应商,在这里设有基地,但是还没有完全的国内供应商能在我们的帮助下提供高质量产品。
AMS:戴姆勒在这里有一个研发中心。这与你们的生产操作有联系吗?
FH:我们研发中心的第一个目标就是为印度市场开发产品。我们的最新产品3143CM卡车,用于矿业和建筑业,我们内部称其为Thunderbolt,这个车就是在这里设计的。顺彬说一下,我们这里的设计概念还处于早期阶段。
AMS:你同意设计和制造之间的关系更加密切的看法吗?
FH:是的,现在尤为如此。在设计之处,就能够在脑中考虑装配问题,这一点非常重要。因为,虽然在设计的时候做出一些改动很简单,但是在制造工程中做出改动就非常困难。设计应该按照减少装配时间、复杂性管理的方法进行。比如说,一个主要线束可以用在不同的变体车型上。我们的研发中心就是要解决卡车、车轴和框架上的每一个零部件。
AMS:你们刚刚开了一个公交车生产厂。卡车和公交车有多少共性呢?
FH:我们生产前轮驱动公交车底座和动力系统。我们能把底座开到公交车厂,然后在那里安装车身。把公交车厂建在那里意义重大;除了共享一些零部件之外,还能避免底座经过很长路程才能安装车身的情况,而这种不便在很多地区都存在。
"我们这里的人都很出色,解决问题的能力很强,我们的培训和使用的系统非常强大,在市场中游刃有余" – Felix Homburg, 戴姆勒印度
AMS:全新Thunderbolt汽车队生产操作有什么影响吗?
FH:Thunderbolt对我们的生产来说是一种挑战,因为这个车型是在重型车生产线上生产的,有些地方需要最多两倍的劳动力和重型卡车。对我们生产团队的挑战就是需要非常灵活的方案,才能平衡所有生产线上的劳动力。因此,虽然我们可能无法完全消除这些车型产距时间中的峰值,但是我们仍然可以重点关注操作的标准化,因为这是保证一贯质量的唯一方法。
我们从2015年5月开始生产3143汽车,因此试产过量和需求增长也会影响生产线的平衡。我们为这个车非常自豪,这是我们在印度设计的第一个车型。我们这里的人都很出色,解决问题的能力很强,我们的培训和使用的系统非常请打,在市场中游刃有余。
AMS:建立并经营这个工厂,在印度制造卡车过程中,尤其是在制造方面,最大的挑战是什么?
FH:我认为管理数量庞大的地方供应商(我们零部件85%以上都是他们供应的)是一个很大的成就。能够达到我们的质量要求并不容易;有时候还需要我们这方面的支持。比如所,目前我们有的一个项目有一个重要的底盘供应商,和该供应商合作,我们理解到我们精益方法论的异议。因此,他们变得越有能力。我们的生产系统就会越稳定。