在原始设备制造商的努力下,复合材料的使用变得更加广泛,数量更多,从而减轻汽车重量
今年早些时候,宝马公司宣布,要在新一代7系列豪华轿车的底盘上,广泛利用碳纤维增强塑料(CFRP)。新车型的重量达到130公斤,比原来的车型更轻,同时在乘客舒适度和安全设备上还有提高。除了能够降低能源消耗和二氧化碳排放,还能降低汽车的惯性重心,并提高操作性能。
据SGL集团(宝马CFRP项目主要合作商)首席执行官Jürgen Köhler称,“在BMW7系列上使用碳纤维产品,是碳材料在汽车业里大范围系列应用的里程碑。”
混合材料方案
车辆是在混合材料“碳芯”汽车结构的基础上制造的。在乘用车单位上,比如中立柱的结构因素上使用CFRP,会提高乘用车的总强度和抗扭弯。因此,乘用车钢板因素的配置是可以调整的,可以明显降低车身重量。
CFRP还应用在车辆混合顶棚构架上。碳纤维的应用将由SGL Automotive Carbon Fiber公司开发(SGL-ACF)— 是BMW和SGL集团的合资公司 — 地点是在华盛顿州Moses Lake工厂。工厂在过去几年内的生产力稳步提高。初加工品是这些纤维利用全自动纺织生产工艺制造而成。然后,初加工品将直接送到宝马集团,并及工程CFRP零部件。
SGL集团在德国Wackersdorf工厂也提供碳纤维面料,以及回收材料。集团与BMW集团一同开发,将这些回收碳纤维产品用于C-柱和保护罩分割物上。
宝马公司称,制造i3和i8车型上使用的CFRP密集材料过程的经验 — 以及相关基础设施 — 是结果如此成功的关键。
新款BMW7系列使用了大量的额碳纤维,成为汽车业使用第二多的系列CFRP生产项目,仅次于i系列车型。
设计,生产和装配
CFRP材料的硬度和轻度,使其成为生产汽车结构组件的理想材料。但是广泛使用需要在零部件的设计,生产和装配上进行全新的改变 — 这对汽车制造商来说是个极大的投资。
2010年宣布出售Lamborghini的Sesto Elemento,这是扩大使用CFRP最激动人心的案例。Sesto Elemento的562bhp V10是在Gallardo的基础上,用CFRP结构制造。999公斤的汽车能达到100公里/小时,在2.5秒中内就能达到300公里/小时的速度。为了把这种性能发挥的更高程度,Sesto Elemento的生产使Lamborghini的工程师们有机会测试各种技术,应用于今后CFRP零部件的制造商。
公司在CFRP技术应用于汽车上历史很长。2001年到2010年,在Murciélago的生产中大约使用了31%的碳纤维增强环氧预浸料。这些材料继而应用于所有外部车体板材,以及内部结构零部件上,最后接合到钢材空间构架上。
成本与数量
在制造这个汽车的过程中,Lamborghini公司强调,为这些结构铺上CFRP板层,以及常常的高压热加工所产生的高成本。但是公司认为这个工艺适合Murciélago,每年的生产率大概会达到400辆。
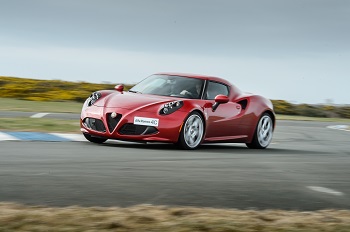
Murciélago的后续产品Aventador于2011年3月在Geneva车展中亮相,全复合材料构架设计上含有50%的碳纤维。这个设计极大提高了扭转刚度,比Murciélago在碰撞方面显示出更佳的性能。
Aventador的CFRP组件每年的产量大约是800个,大部分是利用液体树脂工艺制造,比如真空辅助树脂传递模塑(VaRTM),以及树脂传递模塑(RTM)上。Lamborghini公司认为这些技术在这些数量上是搞笑的,但对更高数量的生产来说,需要开发新的技术。
锻造复合材料
Lamborghini采用的革新技术当时还有所谓了锻造复合材料,在汽车结构和悬挂摆臂上使用。这是与高尔夫俱乐部制造商Callaway一同合作开发,不连续的纤维增强材料适用于高产量CFRP零部件的生产。
锻造复合材料是在碳纤维增强模压塑料板材(CFSMC)的基础上而成,有Quantum Composites公司提供。该材料是由25.4mm长的碳纤维短麻屑(占材料重量的53%)构成,随意分布在两层乙烯基酯树脂中间的衬垫上。这些材料经过滚筒压缩称板材形状,再卷起来,成为标准预浸材料。
这个材料用于配对金属工具热压工艺中的压塑法。它能承受大约132-160摄氏度,6.9-10.3MPa的压力,加工时间在3至5分钟。Lamborghini公司称,这种材料能大幅度降低生产循环时间,以及复杂的三维零部件的需要(这在持续的碳叠层组合材料中不典型)。
公司利用锻造复合材料,降低了Sesto Elemento悬架控制手臂重量,与铝材质大约轻27%。该材料出现在2010年版Lamborghini Gallardo LP570-4 Superleggera上。此外,这些零部件的生产只需要6分钟。
自开发Sesto Elemento以来,锻造复合材料已经用于生产Aventador J跑车两件式座椅,以及新款Huracán发动机舱的制造商。然而,Huracán的底座与大众Audi R8采用相同的符合材料结构。R8 Audi Space Frame (ASF)采用铝和CFRP结构,重量只有200公斤 — 比之前的还要轻10公斤。
ASF车体模型前端和后端是用大量的铝制造而成,而CFRP应用于后围、中央通道和3段式B-柱。这种大型组件主要用RTM工艺制造,构成ASF的支柱,占整个节后的13%。
在后围的横向构建上,需要在横向方面具有高强度,因此CFRP的纤维层大面积单向对齐。最多有14层叠加在一起,构成5mm后的板材,抗张强度达到3.95GPa。在B-柱加固方面,纤维层要在所有方向都要对齐,来支持纵向和横向的负载。这些零部件的抗张强度达到0.9GPa。
这种材料与BMW 7系列之间的差别惊人。
更多主流应用
事实上,Audi似乎也会在更多主流车辆上采用CFRP零部件。今年6月,Audi在CFRP调查方面的长期合作商,Voith公司宣布,公司将接受德国一家汽车制造商的订单,为未来的车型制造CRFP组件,而且产量很高。
“(Shelby GT250 Mustang)车轮采用碳纤维,要比铝制车辆的重量轻60磅,而强度更高,转向反应更佳” – Adam Wirth, Ford
最近,CFRP用于生产汽车结构组件,比Huracán或R8都要便宜。Alpha Romeo的价格大约是45,000英镑(约合69,500美元),该车中的4C被誉为“买得起的超级跑车”。4C于2013年晚些时候推出,在意大利摩德纳的Maserati工厂生产。该车能够在4.5秒内就能从0加速到100公里/小时,最高时速达到258公里。
想要获得这种性能,需要保证汽车的重量-马力比要达到每马力低于4公斤;4C的设计师选择减少汽车的重量,而不是提高马力。汽车重量只有895公斤,采用大量的铝、低密度SMC和CFRP。
单片式结构
4C夸口说,所采用的CRFP单体结构与LaFerrari(100万英镑)的相似。单片式结构重65公斤,由那不勒斯的Adler Group 制造。制造这个车需要TenCate Advanced Composites公司提供的E700系列碳纤维预浸材料,并且用手工铺开,装到真空袋,并在高压锅里加工。
使用这个工艺之后,Adler就能一步到位生产通常需要多片多次生产步骤的组件。举例来说,一个传统的钢门立柱通常需要6个不同的钢片;可是在4C里,门柱只是单体壳的一部分。制造这种单体壳过程中的复杂性和成本,只能通过少量生产来平衡;每年最多能生产3,500辆4C。
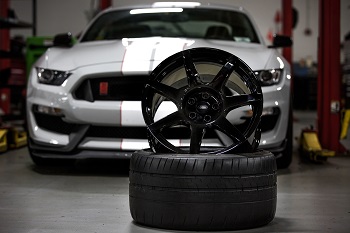
CFRP可以不必限定在白车身和汽车构架上。Ford公司称,要成为第一个量产CFRP车轮的汽车制造商。
这些车轮 — 比铝制车轮的重量几乎轻50% — 是福特Shelby GT350R Mustang的亮点,并设定为标准设备。这些车轮是与澳大利亚Carbon Revolution公司一同合作开发的。
Carbon Revolution公司已经开发了一个真空树脂灌注技术,可以不使用预浸材料。预浸材料需要以低温度环境(接近冰点)运输和储藏,成型之后保质期短,很难适应复杂的集合结构 — 正如我们所见 — 需要在高压下成型和加工。
柔性聚合物
公司采用的方法涉及一种柔性聚合物铸模元素。这种柔性元素可以在倒凹区和腔体内铸模,这是传统僵硬的模具所无法企及的。此外,柔性聚合物模具生产成本要比硬性方法低得多,而且可以在低耐力下制造其他工具构建。相比之下,配对的固体模具必须在高耐力下加工,才能获得与接合模具组件相配。
Ford Performance公司底盘主管Adam Wirth说,“碳纤维车轮与铝制车轮相比,重量要轻60磅(27公斤),而且更加坚固,转向反应更佳。”据福特公司称,通过减少弹簧下重量(那些组件不是悬浮的),轻量车轮对Shelby的搬运和性能产生巨大的影响。车轮重量减轻,就减少了40%的转动惯量,是车辆在启动、停车和转弯上更加方便,提高了反应速度。此外,轻质车轮还降低了悬挂部件 — 弹簧和MagneRide减震器 — 的工作负载,即便是在起伏不平或破损的道路上,也能让轮胎与道路一直保持接触。