新的技术可以提高焊接技术并降低能源消耗
一辆中等大小的汽车需要5,000个焊接,原始设备制造商们都在投资研究节能焊接结束,以此减少成本。降低耗能已经成为全球研究所最为关注的课题之一。美国哥伦比亚俄亥俄州立大学的工程师们宣称,已经成功攻破这个难题,开发了一种新的焊接技术,比普通方法减少80%的耗能,但是接合力却高出50%。
新的方法可能对汽车业产生巨大的影响,因为人们倾向把传统的钢质零部件与轻质替代金属相结合,减少汽车重量。然而,尽管最近的金属设计优势很多,但是替代金属仍然为制造商面前摆出了挑战。
蒸汽铝箔焊接术俄亥俄州立大学材料科学与工程专业教授Glenn Daehn说,“很多材料被认为无法用传统方法焊接,一部分原因是高热和再冷却会使材料脆弱。材料发展日新月异,但是焊接术并没有改进。我们能够复杂的微观结构设计金属,但是这种微观结构在焊接的时候就会受到破坏。用我们的方法,材料可以在塑造的同时被粘合在一起,而且变得非常坚硬。”
在电阻点焊方面,制造商在金属片上通过高电流,天然电阻生产热量,形成熔化槽,完成焊接。然而,高电流非常耗能,而且熔化的金属就不在坚硬。近些年来,Daehn和他的团队尝试了各种方法来解决问题,获得了半打以上的专利,整个系统被称作蒸汽铝箔焊接术(VFA)。
VFA利用一个高电容器组合,在一片薄铝箔内部制造非常短的电脉冲。在几百万分之一秒中内,铝箔蒸发了,产生的热气将两篇金属粘合在一起,速度是每小时数千英里。金属片并没有熔化,因此接缝中的金属并没有弱化。相反,冲击力直接将金属里的原子融合在一起。能源消耗被降低了,因为电脉冲很短,铝箔汽化所需要的能量要比熔化金属零部件的要少。
“材料发展日新月异,但是焊接术并没有改进。我们能够复杂的微观结构设计金属,但是这种微观结构在焊接的时候就会受到破坏…” - Glenn Daehn, Ohio State University
到目前为止,这个团队已经在型钢和铝合金之间建立了强大的联系,而且将高强钢和铝进行接合,比金属接缝要强大。大学城,这项技术还能应用于塑造金属零部件,并同时进行焊接。Daehn和他的团队现在想要与制造商合作,进一步开发这项技术。
点焊仍然是节能技术开发的重点。然而,传统的点焊,尤其是对铝组件,能源消耗非常高,而且电极损耗也很高。因此,在更换电极时经常需要停止,电极成本过高。

DeltaSpot点焊系统为了解决这些问题,Fronius公司开发的DeltaSpot点焊系统能够在电极和金属板之间的形成连续的拉丝。这样就保护了电极,在焊接之前保证材料的清洁地抵达接触点,并降低了整个耗能。
Fronius公司称,不管焊接材料是否是铝、或是不同级别的钢、或是镀锌或镀层薄板,灵活并可控制的流程保证了点焊的高质量。公司称,显而易见的高质量、系统的高生产力,加上节能等因素造就更加高效、稳定的生产工艺。Georg Fischer就是与Fronius共同开发DeltaSpot方案的众多供应商之一,他们帮助制造最新款Porsche Panamera汽车上的铝质门框。
最新的DeltaSpot产品还有杠杆式焊枪,提高了适用性和系统的技术,缩短了生产停滞期,并降低了运营成本。变压器和整流器也被移动到离电极更近的地方,以便减少输电损耗。
那么,激光焊接又如何了呢?去年在德国慕尼黑举行的全球激光光子学展览会上,Audi展示了以激光为基础的焊接工艺在生产中的积极效益。比如,Audi A8上的一些轻量零部件最快只要两次焊接就可以完成。
远程激光焊接术来自Audi内卡苏尔姆工厂的Jan-Phillip Weberpals说,远程激光焊接术在铝制悬挂式零部件焊接作业上,利用Lawerline的一个4kw的直接半导体光源,能在12秒钟内完成9个滚焊 — 这是传统激光焊接时间的一半。这不仅提高了焊接速度,而且能够节省25%的能源消耗。
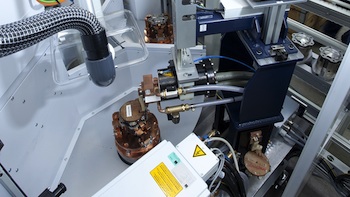
在激光焊接术领域中的一位佼佼者就是Trumpf公司,日前刚刚推出的TruLaser Robot 5020 Basic Edition。他们的紧凑机器人系统拥有6个轴,能够焊接最厚4mm的低碳钢、不锈钢和铝板,为自动化激光焊接铺平了道路。更重的是,系统中的TruDiode直接半导体光源能够提高40%的效率,从而减少使用者的操作成本。
如果公司已经拥有激光切削机械能与TruDisk固体激光器融合,那么切削成本会更低。这是因为,激光能够用于网络中的很多系统,比如TruLaser Robot 5020 Basic Edition。这能减少最高50%的投资成本,实现光源利用率的最大化。
使用Trumpf TruDisk激光技术的就有GKN Driveline公司在德国茨维考工厂,两年前放弃二氧化碳转而使用TruDisk 5302现为引导激光。
负责中心工艺及茨维考工厂经营规划的Zoran Bubic说,“固体激光器焊接系统能极大减少生产成本,效率提高了近30%,比我们之前的二氧化碳系统更好,更节能。”
固体激光焊接系统的另外一个好处就是可以利用波长,使材料更有效地吸收热量,因此所需激光能源就少得多。在墨西哥、上海的GKN Driveline工厂也即将使用类似系统。
激光复合焊接术另一个颇受汽车业青睐的工艺就是激光复合焊接术,这种工艺同时使用了激光焊接和电弧焊,而且在同一个焊池里使用同一个焊接设备。使用这种工艺的公司就是Mercedes-Benz。
传统的MIG或激光工艺使用冷焊丝,而激光符合焊接利用低能源输入将焊接速度提高两倍,并且减少耗能,同时减少热变形。此外,可以使用电弧焊接材料,自发二氧化碳激光焊能够高度控制焊接质量和性能。
大多数原始设备制造商的工厂都实现了自动化,但是配有传统MIG或MAG焊接系统的机器人必须经常停下,清洁喷嘴里喷出的焊渣。这种工艺在时间、材料和能源损耗上还有很大的改进空间。因此很多汽车制造商,以现代汽车为代表,已经改用CMT工艺了。CMT不仅能减少焊渣,而且还能极大提高金属过度稳定性,明显减少点击的倾斜角。光是这个技术就能减少机器人在焊接时60%的停顿时间,提高了能源效率。
Fronius是特殊CMT技术供应商之一。在CMT工艺上,线圈移动被放到程序控制当中,这样热量就能快速进入。因此,材料转移几乎不会产生电流。

对于那些质疑摩擦搅拌焊接的人来说,FSW焊接工艺区域激光焊接和MIG焊接之间。然而,通用汽车和TWB公司、Alcoa公司,以及Pacific Northwest National Laboratory通过合作,改进了FSW工艺,能够减少生产时间和成本,同时提高轻量零部件的强度。
摩擦搅拌焊接术合作的成果就是,使用铝之后,车门内板比使用现今制造方法轻了62%,便宜25%,同时保持原有的速度、规格、质量和持久性。研究团队决定对FSW进行改进,使公司制造的TWB能够广泛应用于汽车轻量材料。有了这个新的工艺,一个FSW机械就能每年接合250,000个汽车组件。
据TWB公司称,与GM公司合作完成了100个铝板的焊接、加工和分析。此后,TWB公司称他们的研究是世界上能安装运行铝制TWB,并且进行高产量制造的世界第一例。
当然,没有两个焊板是完全一样的。反过来,也没有两个焊缝的耗能是完全一样的。精确评定焊线所需能源就是开始节约的第一步。从此以后,工厂能够决定对焊接设备进行生么样的升级、组织、监控才是最适合工厂的需要,并达到节能的总体目标。
ABB公司的Statcon(静止同步补偿器)和Dynacomp(实时动态无功功率补偿器)技术用于无功补偿的方案,被菲亚特公司用于解决印度焊接质量问题,这主要迫于地方动力质量难题。此外,这个方案还用于改进能源效率,最高改进率达到99.5%。
有人称Statcon和Dynacomp能够产生快速而平滑的无功补偿,解决很多行业网罗动力质量问题,比如低功率因素、电压跌落、闪烁和高谐波水平等。
Statcon技术基于IGBT(是绝缘栅双极型晶体管 — 一种快速交换的高效功率半导体元件)。ABB公司称,该技术能够产生快速而动态的无功补偿,反应时间只有百万分之20至30秒。它能通过产生感应或电容性功率而出现平滑而无极的补偿,适用于提高薄弱网络的电能质量。
ABB印度公司开发的新一代Statcon具有控制、操作、优化、保护、诊断和使用者界面增强能特点,能够满足市场对高端功能的需求。
Dynacomp是一种晶闸管投切电容器组技术,能够产生快速稳定的功率因素补偿,用于低电压网络。一共有23个不同额定功率的Dynacomp电板安装在变电站里,为发电厂、白车身、喷漆和装配车间,以及研发中心和公用系统提供动力。
ABB方案能够为现场的动力网络提供稳定性,极大降低了耗能,避免网络因子在消耗大量无功功率而产生的损失,提高了焊接稳定性和生产率,而且还降低了焊接车间的维护成本。此外,该方案的节能模式能在感知负载时自动重启,从而节约了厂用电量,并消除了手动启动。