A Daimler adota uma abordagem centrada no pessoal para fazer avançar suas operações de fabricação na Índia
A primeira coisa que Felix Homburg, vice-presidente de Operações e Engenharia de fabricação apontou no início de nossa visita da fábrica de caminhões da Daimler Chennai, foi um grande quadro de avisos com vários sistemas de incentivos para o empregado. Funcionário do Mês e competições 'Lean-O-Mania' não são incomuns, mas a importância destas não deve ser subestimada uma vez que a indústria automotiva da Índia depende muito do engajamento com a força de trabalho para alcançar os níveis necessários de qualidade e produtividade em um base consistente.
A grande sala de montagem permite uma visão muito aberta entre os dois principais pólos de produção (para caminhões pesados e médios) e a montagem da seção aberta nas linhas é uma boa representação da transparência da estrutura de comunicação operacional da fábrica. Aqui reuniões regulares são realizadas com líderes de equipe e seção de modo que todos sejam capazes de discutir os desenvolvimentos operacionais e quaisquer problemas com Homburg e outros gerentes seniores. Este fórum aberto oferece um maior acesso à gestão, que por sua vez promove um ethos muito mais colaborativo entre a força de trabalho, e isso é importante porque, segundo Homburg, devolve a responsabilidade para as equipes e ajuda muito na construção de confiança e um maior engajamento.
Criando uma cultura de qualidade
Tudo aqui é grande desde o tamanho de corredor até os próprios veículos, mas toda a operação prosseguem com calma e bastante eficiência. O conjunto principal e áreas de sub-montagem menores estão impecavelmente limpas, a empresa deu muita importância para a criação de um ambiente de trabalho agradável saudável (dentro e fora) da fábrica. Isto, Homburg explicou, contribui para o engajamento, melhora a eficiência e criou uma cultura de qualidade.
Observando a montagem dos caminhões que vêm para a linha, o processo parece enganosamente simples. O chassi tem eixos, suspensão, motor e transmissão e cabines instaladas em várias estações ao longo da linha e aparentemente esta arquitetura de veículo aberto, simples tornaria o processo de montagem mais simples do que com um carro. No entanto, há uma série de fatores que compõem a complexidade e criam desafios ao equilibrar as duas linhas de montagem.
Em primeiro lugar, há uma carga de trabalho muito variável em algumas estações, dependendo da variante ou modelo (nomeadamente o novo caminhão 3143 CM, internamente apelidado de "Thunderbolt"), devido aos diferentes níveis de conteúdo, dependendo do veículo e para o qual mercado está sendo construído. Eu sugeri que isso tornou maior a média do tempo de ciclo preferíveis para ajudar com equilíbrio, mas curiosamente Homburg explicou que os tempos mais curtos ciclo ajudaram a melhorar a qualidade bem como a produtividade. Além disso, o tamanho físico e o peso de algumas das peças aumenta o desafio de intalá-las rapidamente e eficientemente.
"... nossas operações de produção são muito robustas, assim somos muito capazes de construir modelos para os mercados interno e exportar" – Felix Homburg, Daimler
Obtendo o direito básico
Com o alto nível de operações manuais em toda a fábrica, a empresa tem trabalhado muito duro para estabelecer processos e procedimentos fundamentais sólidos dentro de todas as operações de produção. Ela também tem visto uma forte dependência de Kaizens auto-desenvolvidos para otimizar a eficiência, qualidade e produtividade. A montagem de pneus do lado da linha era uma área que foi mostrada onde mudanças simples para o fluxo da operação e algumas soluções inteligentes para estantes, ferramentas e entrega ergonomia tinham feito uma diferença significativa para a eficiência do processo. Os pneus e jantes são pesados de forma mais simples e muito eficazes pois agora entregam os pneus para a estação de linha de montagem (organizado na orientação correta para os eixos com rodas duplas) tornando a instalação uma operação muito mais suave. Esta é uma solução que foi compartilhada com a rede global da Daimler.

A montagem de kits de peças é amplamente utilizada para ajudar o processo de montagem, com peças e estantes especialmente projetadas e desenvolvidas pelos trabalhadores da linha localizadas e em torno do veículo enquanto este se move na linha. O layout das peças dentro dos kits é descrita como "cirúrgica", com tudo em uma posição particular, prontamente a mão. É evidente que uma grande quantidade de desenvolvimento tem ido para estes kits mas a velocidade à qual estas estantes por encomenda podem ser construídas e implantadas é surpreendente. Equipes especiais fornecidas com pré-formados de tubos, conectores, suportes e parafusos podem ser chamado para a borda da linha para medir e construir qualquer coisa deste tipo no local. Ela também permite que quaisquer alterações ou adaptações sejam feitas muito rapidamente. Como Homburg observou isso incentiva ainda mais os trabalhadores a pensar sobre seu trabalho específico e encontrar soluções para melhorar o processo.
Projetos de especialistas
Bem como os pequenos Kaizens inumeráveis que têm sido e continuam a ser implementados há também maiores, projetos a longo prazo em andamento. Estes são chamados "projetos de perito" e um tal projeto é para melhorar a eficiência da linha de sub-montagem. Homburg explicou que esses projetos seriam concebidos e executados ao longo de um período de três meses; a linha de táxi está estudando formas de melhorar o layout das peças e materiais na borda da linha e reduzir o espaço necessário para esta parte da operação. Embora a maioria destes desenvolvimentos exijam uma solução pouco tecnológica, fiquei surpreso ao ver um veículo guiado automatizado (AGV) usado para entregar os táxis para a linha principal. Foi dito que este era um sistema experimental que estava sendo usado como parte de um estudo de viabilidade para melhorar a entrega das unidades de táxi.
Produção de caminhões Bharat Benz (9T-49T) e FUSO (9T-49T) além de motores e transmissões
Capacidade de até 70.000 unidades por ano, dependendo do modelo
Local cobre 400 acres e emprega mais de 3.000 funcionários. É o lar da empresa e de uma abordagem integrada de P&D, bem como uma fábrica de barramento dedicado
Veículos apresentam mais de 85% de conteúdo local de mais de 300 fornecedores

Soluções simples para o complexo constrói
A linha de transmissão também revelou um processo complexo necessário para construir cada caixa de velocidades, mas também um sistema muito simples que utiliza bolas de golfe codificadas por cores para indicar quando certos conjuntos de componentes precisam de recarga. Cada trabalhador tem de se concentrar totalmente em seguir um processo de montagem exata que inclui pré-aquecimento de determinados componentes a uma temperatura pré-definida de modo a permitir a montagem de seções que requerem um ajuste de interferência. No momento da minha visita a seção de motor e transmissão estava se preparando para adicionar uma nova linha de transmissão com a capacidade adicional construída para exportação. Em preparação para esta equipe as operações tinham construído uma réplica exata da linha planejada de papelão, com estações de montagem, ferramentas, equipamentos, transportadores. O processo é então trabalhado, cronometrado e filmado, com tudo, desde tempos de ciclo até a ergonomia trabalhada em detalhes, tanto quanto possível identificando as áreas problemáticas e para otimizar o layout para todas as seções da nova linha.
Com esta fábrica de caminhão impressionante no Oragadam e uma nova unidade de produção de ônibus localizado ao lado, a Daimler tem demonstrado a sua clara intenção de lutar por participação de mercado no setor dos veículos comerciais muito competitivo da Índia. A fábrica continua a expandir com novos edifícios em construção, embora Homburg e sua equipe não poderia revelar que as operações de produção além disso. O que também ficou claro desde a minha visita é que a empresa tem entendido como jogar com os pontos fortes da força de trabalho da Índia, conquistando o desenvolvimento de habilidades para resolver problemas, e criar um maior sentido de compromisso. Curiosamente em uma fábrica onde tudo é em grande escala as inovações menores e mais simples estão fazendo uma grande diferença.
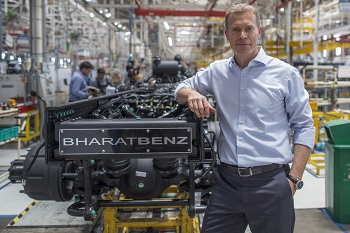
Felix Homburg foi vice-presidente de Operações e Engenharia de Manufatura da Daimler India Commercial Vehicles desde abril de 2015. Anteriormente, ele tinha sido diretor da subsidiária Atlantis da Daimler, localizada perto de Cape Town desde 2011. Graduado em Engenharia Elétrica, ele começou sua carreira na Daimler em 2003 no Programa Internacional de Gestão Associada, completando posteriormente várias tarefas com um foco em fabricação nas fábricas Daimler Trucks em Woerth (Alemanha), Portland / Oregon (EUA) e Saltillo (México).
AMS: Durante a visita à fábrica, vimos um muitos ciclos de trabalho pequenos, mas muito eficazes sendo usados na linhas de produção.Você poderia explicar a abordagem para o desenvolvimento dessas soluções?
Felix Homburg (FH): A manifestação de ciclos na Indian é uma solução brilhante, inteligente, que custam pouco ou nenhum dinheiro. Quando olhamos para ciclos que normalmente não envolvem grandes orçamentos; alguém [na linha de produção] surge com uma idéia e nós a construimos. Você viu as equipes móveis durante a turnê que traz todas as ferramentas e tubos pré-forma, etc. [para a borda da linha] para construir novos carros. A resolução de problemas é muito importante para nós, é uma grande parte da nossa gestão de chão da fábrica. Atuamos de uma maneira que nos permite parar a linha se houver algum problema. Assim, mesmo uma parada de linha é realmente parte da rotina de resolução de problemas.
Esses blocos permitem-nos ter a força de trabalho em uma metodologia na qual ela segue as instruções de trabalho padrão. Isso, então, faz com que pensem no que realmente importa - onde as melhorias podem ser feitas em sua área de trabalho. Nós dirigimos estas melhorias, quer através dos ciclos ou projetos maiores - nós chamamos esses de "projetos perito" - e estes podem levar até três meses para serem concluídos. Para facilitar estas melhorias que têm uma "equipe enxuta", que é altamente treinada nesta área, no entanto, esses projetos são de responsabilidade e executados pelo chefe de departamento que pode chamar os membros da equipe para o apoio e ajuda com metodologia e estruturação do trabalho.
Temos também comissões onde a cada trimestre, revisamos nossas metas anuais, olhando para os passos necessários e os recursos disponíveis para decidir qual grande projeto deve ser executado. Atualmente estamos trabalhando em um projeto com nosso fornecedor eixo, e o projeto da linha de táxi onde queremos dar passos maiores de aproveitar esta operação para o próximo nível de valor X-sem-valor acrescentado, para remover uma grande quantidade de resíduos - fora do processo de montagem. Este é um sistema que alimenta a si mesmo, com a construção de eficiência de custos, boa formação e, sobretudo, um ótimo lugar para trabalhar, onde as pessoas sentem que podem contribuir.
AMS: O que identificou a linha de táxi como o próximo grande projeto para melhorias?
FH: Foi mais que a linha de chassis tinham progredido muito em termos de design de linhas e eficiência e a linha de táxi - em relação a isso - foi ficando para trás, de modo que desafiou a equipe de linha de táxi para tomar algumas grandes passos.
AMS: A construção de variantes adicionais para exportação aumentou a complexidade da operação de produção?
FH: Você viu que as nossas operações de produção são muito robustas e somos muito capazes de construir modelos para ambos os mercados interno e de exportação. Nós estabelecemos fundamentos muito sólidos na nossa produção. É por isso que olhamos para um veículo de exportação, basicamente, como apenas uma outra variante para construir.
AMS: Você mencionou o treinamento. Como que é feito, você envia alguma equipe para a Alemanha?
FH: Não. Temos um centro de treinamento totalmente integrado aqui. Bem como o treinamento de indução para todos - que é bastante sofisticado - temos mais formação especializada para funções específicas, que envolve ambos elementos teóricos como práticos. Isso nos permite desenvolver habilidades para o próximo nível. Um exemplo disso seriam eletricistas automotivos, porque com o aumento da regulação das emissões [na Índia], caminhões estão agora com níveis mais altos de eletrônica, de modo que o potencial de problemas com esses sistemas aumenta a complexidade e precisamos de trabalhadores qualificados no local para lidar com quaisquer problemas .
AMS: Quando a fábrica foi inaugurada, foi relatado que os veículos construídos aqui teriam até 85% de conteúdo local. Este valor aumentou?
FH: Sim, tem aumentado, apesar de não publicarmos os números exatos. É um nível elevado, mas tudo o que podemos obter, melhora localmente a nossa posição de custo. Nós sabíamos quando começamos que para sermos competitivos neste mercado [indiano] precisávamos empurrar o conteúdo de veículos localizado para acima de 85%.
AMS: Quais peças vocês ainda importam?
FH: Os componentes mais complexos - Sistema eletrônico, de combustível, etc. - para os quais ainda não encontramos um fornecedor indiano para oferecer.
Temos trabalhado duro para conseguir mais de 300 fornecedores que trabalham conosco. Alguns são alemães, fornecedores tier 1 com sede aqui, mas também temos muitos fornecedores totalmente domésticos que têm ajudado a desenvolver e entregar a qualidade que precisamos.
AMS: Daimler tem um centro de P&D aqui. Como é que ele está ligado a sua operação de produção?
FH: O primeiro objetivo do nosso centro de P&D é desenvolver produtos para o mercado indiano. Nosso mais novo produto, o caminhão CM 3143 para a indústria de mineração e construção, que chamamos internamente o Thunderbolt, foi concebido aqui. De qualquer maneira, nós [da produção] estamos envolvidos em conceitos de design numa fase precoce com as duas novos produtos e atualizações.
AMS: Você concordaria agora há uma relação muito mais próxima de trabalho entre o design ea fabricação?
FH: Sim e hoje é vital. É muito importante projetar um veículo com montagem em mente, desde o início, porque enquanto é fácil de fazer mudanças na fase de concepção é muito mais difícil mudar as coisas em engenharia de produção. Deve ser concebido de uma maneira que reduza o tempo de montagem, gere a complexidade.
AMS: Você abriu recentemente uma unidade de produção de ônibus neste site. Quanta semelhança há entre os camiões e ônibus?
FH: Nós construimos o chassis para os ônibus de tração dianteira e as motorizações. Podemos, então, dirigir o chassi para a fábrica de ônibus onde as carrocerias estão equipadas. Fez sentido localizar a fábrica de ônibus neste site; bem como o compartilhamento de certas peças que evita ter de conduzir o chassis uma longa distância para carrocerias para serem instaladas, que é comum em algumas regiões.
"Nós temos pessoas muito boas aqui com habilidades para resolver problemas fortes e nossa formação e sistemas nos tornam muito fortes neste mercado" – Felix Homburg, Daimler India
AMS: O novo Thunderbolt teve qualquer impacto sobre as operações de produção?
FH: O Thunderbolt desafia nossa produção porque é produzido na linha de trabalhos pesados e em algumas áreas que requerem até quase o dobro da carga de trabalho de um caminhão HDT. O desafio para a nossa equipe de produção é de chegar a soluções muito flexíveis para equilibrar a carga de trabalho em toda a linha. Assim, enquanto não eliminarmos completamente picos nos tempos de ciclo para estes modelos, ainda nos concentramos na normalização das operações, uma vez que esta é a única maneira de conseguir consistência na qualidade.
Nós começamos a produção do 3143 em maio de 2015, de modo o aumentando a demanda está também afetando o equilíbrio da linha. Estamos muito orgulhosos deste veículo, o nosso primeiro modelo concebido na Índia. Nós temos pessoas muito boas aqui com fortes habilidades de resolução de problemas e nosso treinamento e sistemas nos tornam muito fortes neste mercado.
AMS: Tendo configurado e executado esta fábrica, que é o maior desafio - em termos de produção - qual desafio você enfrenta para construir caminhões na Índia?
FH: Eu acho que gerir o elevado número de fornecedores locais que contribuem com mais de 85% do nosso conteúdo é um grande feito. Os níveis consistentes de qualidade que exigimos nem sempre ocorrem facilmente; às vezes eles precisam do apoio da nossa parte. Neste momento, por exemplo, temos um projeto com um importante fornecedor de chassis, trabalhando com eles para entender nossa metodologia enxuta. Assim, quanto mais capazes eles ficam, mais estável nosso sistema de produção fica.