Combinando criatividade, plano de exportação corajoso e um subsídio do governo, a Geely lançou um táxi elétrico LTC todo-novo em uma fábrica construída para este propósito.
Como você constrói um carro de nicho de baixo volume como o táxi preto de Londres tornando-o rentável? Esse foi o dilema para a Geely Holding Group Zhejiang quando começou a desenvolver o novo táxi que está definido para lançamento no final do ano a ser construído em uma fábrica totalmente nova em Coventry, Inglaterra.
O tamanho da tarefa para a London Taxi Company, como é agora conhecido, foi ainda mais montanhoso dado que os regulamentos de Londres estipulam que todos os novos táxis pretos matriculados após 01 de janeiro de 2018 precisavam ser adaptados para zero de emissões. Isso significava substituir o fiel e pesado, motor diesel com indiscutivelmente a segunda mais cara combinação do mundo de motor e transmissão depois das células de combustível: elétrico, com um motor de combustão que pode se entender para gama.
Como a Geely tem abordado isto é fascinante, e envolve uma combinação de boa engenhosidade britânica, uso liberal da Geely (ou, mais especificamente, da Volvo), rede de cadeia de abastecimento existente, um plano de exportação corajoso e um grande investimento do Governo do Reino Unido para obter a fábrica construída.
A Geely salvou a London Taxi Company (anteriormente London Taxis International) quando comprou a empresa mãe que estava em falência em 2013. LTI vinha aumentando táxis a uma taxa de cerca de 3.500 por ano em sua fábrica em Holyhead Road, em Coventry. Este tinha sido o lar do táxi preto de Londres desde 1948, mas, como um investidor desde 2007, a Geely tinha movido produção para a China e a partir de 2010 e houve a importação de kits para a planta de Coventry para montar.
Uma planta construída para o novo táxi
A antiga fábrica, que fica próxima ao centro de Coventry não seria adequado para construir o TX5 de alta tecnologia, assim a LTC que construiu uma nova instalação de 37.000m² com uma capacidade de 24.000 por ano nos arredores de a cidade em um novo parque industrial não muito longe da aldeia de Ansty. No total, a LTC avalia que gastou £325m ($415M) na planta e desenvolvimento da gama de veículos, que no próximo ano também incluirá uma van de entrega urbana fora da mesma plataforma.
A soma do investimento soa barata - e é, em parte devido à maneira inteligente o novo TX5 tem sido construído. Em vez de um chassis de carroceria-em-quadro, a nova cabine é construída em torno de monocoque de alumínio extrudido leve ligado, o mesmo sistema utilizado tanto pela Lotus como Aston Martin para construir os seus carros.
O alumínio é cerca de três vezes mais caro que o aço leve, de acordo com o fornecedor de peças de metal Gestamp (que não é o vendedor aqui), mas também é metade do peso e a LTC diz que foi crucial para aumentar o alcance da bateria e garantir que o taxista não gaste muito alimentando o motor extensor de alcance de 1.5 litros. “Não é um veículo barato. O truque para nós é ser capaz de torná-lo custo competitivo para o proprietário", diz Carl-Peter Forster, presidente da LTC e membro do conselho para Geely.
A outra coisa útil sobre a estrutura de alumínio ligado é que pode ser montado em uma oficina de fábrica que requer muito menos investimento do que uma oficina padrão - o custo da LTC é de apenas £30m, de acordo com Forster (veja mais na entrevista). O baixo investimento da fábrica, ajudada por £16m do Fundo de Crescimento Regional do Governo, foi a chave para fazer todo o trabalho do projeto.
“A fim de tornar este um empreendimento comercialmente viável tivemos de baixar. Eu não vou dar-lhe um número, mas é muito baixo", afirma Forster.
Ajuda para o fornecimento Volvo
O alumínio para a carroceria é originado no Reino Unido, e Philip Bracken, gerente de compras para LTC, diz que esta é uma grande parte da taxa de localização do Reino Unido, 32% em valor. O fornecedor é especialista em alumínio Sapa Group, que também anodiza o metal no Reino Unido. As peças maiores fornecidas no Reino Unido são o SMC (composto de moldagem de folha), painéis de carroceria compósito de plástico, que LTC pinta na sua planta velha de Holyhead no momento.
Do restante, as peças para a TX5, 32% vêm da Europa e 32% da China, com os quatro por cento restantes dos EUA.
O que é surpreendente é a forma como muitas das peças são compartilhadas com Volvos modernos, uma vez que é uma marca premium. 'Compartilhada' é a palavra chave aqui. “Nada vem da Volvo em si, mas o que eles fizeram foi nos dar conselhos sobre fornecedores que utilizam para suas peças,” disse Bracken. A vantagem é preços mais baratos do que se a LTC fornecesse de forma independente, diz Bracken.
A bateria de 33kwh é proveniente de fornecedor Volvo LG Chem, e o motor elétrico é da Siemens. Ambos são usados em veículos híbridos Plug-in da Volvo. O motor é a unidade turbo a gasolina de Volvo nova de três cilindros, proveniente de uma fábrica Geely na China. O táxi também usa comutadores e provavelmente todo o eixo traseiro com a sua mola de lâmina composta transversal (embora isso não tenha sido confirmado).
Como é uma fábrica de baixo investimento
A oficina de pintura de £30m é operada quase em níveis de sala limpa, e representa o coração da operação Ansty. A estrutura monocoque é montado em cinco seções diferentes, cada um com a sua própria área de sub-montagem. As peças de alumínio são carregadas em gabaritos; robôs, em seguida aplicam a cola. Todo o processo é cerca de 50% automatizado.
As peças são então rebitadas juntamente para que elas não se movam antes do cozimento. Antes de passar em um dos quatro fornos, as seções são montados em um gabarito de enquadramento para criar a carroceria acabada. O processo de cozimento requer cerca de 20 minutos a 180°C. Este será um gargalo futuro se planos da LTC para exportação exceder 24.000 por ano. A sala de montagem pode gerenciar 36.000, fomos informados.
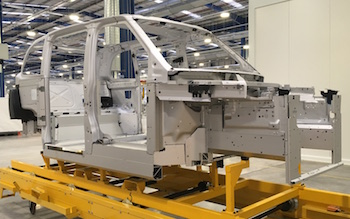
A linha de montagem é mais convencional e muito menos automatizada do que a de carroceria. A AMS viu a ação em um ritmo reduzido conforme os empregados montam protótipos antes do lançamento com muito pouca ajuda de robôs. Há apenas um em montagem, que aplica cola para as janelas antes de serem montadas manualmente no carro.
“Nós não usamos robôs para encaixá-los por causa de nossos volumes. Usamos automação inteligente que nos dá uma melhoria da qualidade", diz o gerente de engenharia de produção Pete Baynton, que veio da Caterpillar no ano passado, mas tinha conhecimento do alumínio ligado em um cargo anterior na Lotus. Em plena produção, a LTC empregará 1.000 funcionários, mas atualmente 60-70 de seus 400 trabalhadores estão em produção de veículos, Baynton estima. Alguns vieram de Holyhead Road, mas a antiga fábrica estava trabalhando com uma equipe esqueleto.
A partir da oficina, os táxis passam pela seção pré-desbaste pendendo de um sistema de monotrilho elétrico antes de serem carregados para o AGVs, que seguem uma linha no chão de fábrica, para equipar com painéis e portas. Depois, de volta para o monotrilho para casar o motor, bateria e eixos antes que o carro dirija-se para montagem de aparo ao longo de um transportador em movimento embutido no chão. Todas as peças são entregues por 'tow-trens' elétricos com até seis caminhões carregados a partir das peças armazenadas sob o mesmo teto. Além destes trens de carga, a área de montagem é livre de empilhadeiras.
A Geely também fará um veículo similar em uma nova fábrica na China, onde a empresa acaba de iniciar construção, diz Forster. O design do próprio táxi é uma evolução sensível do que era antes, mas essa é a extensão da continuação. “Este é único”, disse o diretor executivo Chris Gubbey na abertura da planta em março. “Nova planta, novos produtos, novos processos de negócios, novos mercados, nova equipe. Não existe em nenhum outro lugar.”
Como você acabou escolhendo uma estrutura de alumínio ligado?
Quando o presidente da [Geely], Li Shufu comprou a empresa no início de 2013, ele tinha um engenheiro. Claramente que não era o suficiente. Por isso, eu sugeri que nós tínhamos que trazer know-how. Fui apresentado a uma empresa de engenharia chamada Emerald Automotive [liderada pelo ex-diretor comercial da Lotus, Andy Tempest] e eles tinham desenvolvido um protótipo de um veículo comercial ligeiro, eletrificado de gama-estendida e estavam bastante interessados em industrializa-lo. Eu disse 'nós vamos comprar a sua empresa, bem-vindo a bordo'. Então a Emerald é uma empresa irmã, basicamente, o braço de engenharia da LTC.
Como a Emerald conseguiu convencê-lo que funcionaria?
Tivemos meio ano de trabalho conceitual. Em seguida, nos comprometemos “em 11 meses, em 31 novembro de 2014, entregaríamos dois totalmente projetados, com demonstradores usando todas as partes e peças disponíveis do Grupo Geely. Era um teste de ácido. A cortina se abriu e o demonstrador entrou e tudo estava bem; você não reconheceria a diferença comparando com como é agora.
Como você equaliza o preço do alumínio com motor e transmissão elétrica?
Este não é um veículo barato. O truque para nós foi sermos capazes de torná-lo competitivo para o motorista e mais barato que o TX4 existente. Se você não usa a gasolina você economiza £500 por mês.
Qual papel a fábrica desempenha nisso?
Temos que construir o volume ao longo do tempo, para isto o truque é que temos de ter um baixo ponto de equilíbrio. £325m - £50m para a fábrica - parece muito, mas nunca chegaríamos a lugar nenhum com a configuração tradicional. Obter uma carroceria de aço e de pintura decente com todo o ferramental custa £400m. Fizemos isso por £50m, incluindo painéis de plástico prementes.