La combinación de ingenio, un atrevido plan de exportaciones y una subvención gubernamental han permitido a Geely lanzar un taxi eléctrico LTC completamente nuevo en una planta construida para ello
:¿Cómo se produce un vehículo marginal como el taxi negro londinense en bajos volúmenes y obtener beneficios? A este reto se enfrentaba el holding Zhejiang Geely cuando comenzó a desarrollar un taxi completamente nuevo para su lanzamiento a finales de año y que se produciría en la nueva planta de Coventry, Inglaterra.
La magnitud de la tarea de London Taxi Company, como se conoce ahora la empresa, es incluso superior teniendo en cuenta que la normativa londinense exige que todos los nuevos taxis negros registrados a partir del 1 de enero de 2018 sean capaces de funcionar a cero emisiones. Eso significa sustituir el fiable pero contaminante motor diesel con la que puede ser la segunda combinación más costosa de tren de potencia después de las celdas de combustible: eléctrico con un motor de combustión amplificador de autonomía.
El enfoque de Geely es fascinante, ya que conlleva una combinación del tradicional ingenio británico, el uso creativo de Geely de la red de cadena de suministro existente (concretamente la de Volvo), un plan de exportaciones atrevido y una gran inversión del gobierno británico para construir la planta.
[sam_ad id=17 codes='true']
Geely salvó la empresa London Taxi Company (anteriormente London Taxis International) al comprarla después de la bancarrota de su matriz en 2013. LTI producía entorno a 3,500 taxis anuales en su planta de Holyhead Road en Coventry. Los taxis negros de Londres llevaban produciéndose allí desde 1948 pero Geely, accionista desde 2007, trasladó la producción a China y desde 2010 importaba kits para su ensamblado en la planta de Coventry.
Una planta a medida del nuevo taxi La antigua planta se encontraba cerca del centro de Coventry y no era adecuada para construir el nuevo TX5 limpio y de alta tecnología, por lo que LTC construyó una nueva instalación de 37,000 metros cuadrados con capacidad para 24,000 autos a las afueras de la ciudad en un nuevo parque industrial cerca de la villa de Ansty. En total LTC calcula una inversión de 325 millones de libras (415 millones de dólares) en la planta y en el desarrollo del rango de vehículos, que el año próximo incluirá también un furgón de reparto urbano en la misma plataforma.
Parece una inversión reducida, y en parte se debe a la manera inteligente de construir el nuevo TX5. En lugar de un chasis de carrocería en bastidor, el nuevo taxi está construido entorno a un monocoque de aluminio extruido, similar a como Lotus y Aston Martin fabrican sus coches.
El aluminio es tres veces más caro que el acero, según el proveedor de piezas metálicas Gestamp (que no forma parte de esta operación), pero también pesa la mitad y LTC asegura que es crucial para aumentar la autonomía de la batería y garantizar que el conductor no gaste demasiado en combustible con el motor amplificador de 1.5 litros. “No es un vehículo barato. La clave para nosotros es hacer que resulte rentable para el propietario", comenta Carl-Peter Forster, presidente de LTC y miembro de la junta de Geely.
“Para conseguir que sea un proyecto comercialmente viable necesitamos reducir el umbral de rentabilidad. No daré una cifra, pero es muy bajo", declaró Forster.
Colaboración con Volvo para el suministroEl aluminio de la carrocería procede del Reino Unido, y Philip Bracken, director de adquisiciones de LTC, asegura que supone gran parte del 32% de origen británico por valor. El proveedor es el especialista en aluminio Sapa Group, que también anodiza el metal en el Reino Unido. La siguiente pieza más grande en adquirir localmente son los paneles de carrocería de plásticos compuestos SMC que LTC pinta en su antigua planta de Holyhead Road.
De las demás piezas del TX5, el 32% procede de Europa y el 32% de China, el 4% restante procede de EUA.
Sorprende cuántas piezas comparte con los Volvo actuales, ya que se trata de una marca de gama alta. ‘Compartir’ es la palabra clave. “Nada proviene de Volvo pero nos han asesorado sobre los proveedores que utilizan para sus piezas", comenta Bracken. La ventaja son precios más competitivos que si LTC hubiera contactado por separado con los proveedores, comenta Bracken.
La batería de 33 kwh procede del proveedor de Volvo, LG Chem, y el motor eléctrico es de Siemens. Ambos se utilizan también en los híbridos enchufables de Volvo. El motor es el mismo que el nuevo motor de gasolina turbo de Volvo y proviene de la fábrica de Geely en China. El taxi también utiliza la electrónica de Volvo, la caja de cambios, el panel de mandos y probablemente todo el eje trasero de su ballesta transversal de materiales compuestos (aunque todavía no está confirmado).
Una fábrica de bajo coste
El taller de carrocería de 30 millones de libras funciona prácticamente a nivel de cuartos asépticos y representa el corazón de Ansty. La estructura monocoque se ensambla en cinco secciones, cada una con su propia área de sub-ensamblado. Las piezas de aluminio se cargan en portapiezas y los robots aplican el adhesivo. El proceso está automatizado al 50%.
Luego las piezas se remachan entre sí para que no se deslicen durante el horneado. Antes de llegar a uno de los cuatro hornos, se ensamblan las secciones en un portapiezas para crear la carrocería terminada. El proceso de horneado requiere unos 20 minutos a 180°C. Este sería el cuello de botella si los planes de exportación de LTC tienen éxito y la demanda supera las 24,000 unidades anuales. La nave de ensamblado tiene una capacidad para 36,000 vehículos.
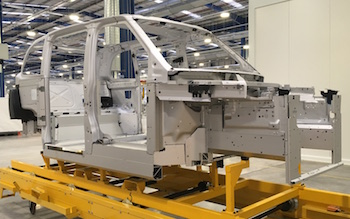
“No utilizamos más robots por los reducidos volúmenes. Se trata de utilizar la automatización de manera inteligente, donde nos ofrezca una mejora en la calidad", nos comenta el director de ingeniería de producción Pete Baynton, quien llegó de Caterpillar el año pasado, pero que adquirió sus conocimientos en aluminio soldado cuando trabajó para Lotus. Cuando esté a plena producción LTC empleará a 1,000 trabajadores, en la actualidad 60-70 de su plantilla de 400 trabajan en la producción del vehículo, según calcula Baynton. Algunos proceden de la antigua planta en Holyhead Road, pero allí estaban trabajando con un mínimo de plantilla.
Para el taller de carrocería, el taxi viaja por una sección de pre-corte suspendido en un sistema de monorraíl eléctrico antes de cargarlo en vehículos autónomos AGV que los llevan a la planta donde se encajan puertas y paneles de mando. Luego vuelve al monorraíl para el matrimonio con el motor, batería y los ejes antes de que el auto se dirija al ensamblado de tapicería a través de una cinta integrada en el suelo. Todas las piezas se transportan con 'trenes de arrastre' eléctricos con hasta seis vagones cargados con las piezas almacenadas bajo el mismo techo. Al margen de los trenes de carga, el área de ensamblado no tiene carretillas elevadoras.
Geely producirá también un vehículo similar en su nueva planta en China que la empresa acaba de empezar a construir, comenta Forster. El propio diseño del taxi es una evolución del modelo anterior, pero ahí acaban los parecidos. “Esto es único", comentó el CEO Chris Gubbey en la inauguración de la planta en marzo. “Nueva planta, nuevo producto, nuevo modelo de negocio, nuevos mercados y nuevo equipo. No existe en ningún otro lugar".
¿Por qué han elegido una estructura de aluminio soldado?
Cuando el presidente de Geely, Li Shufu, compró la empresa a principios de 2013 solo contaba con un ingeniero. Está claro que no era suficiente. Entonces propuse la necesidad de atraer a personal experimentado. Contactamos a una empresa de ingeniería llamada Emerald Automotive (dirigida por el anterior director comercial de Lotus, Andy Tempest) que había desarrollado un prototipo de vehículo comercial ligero, un vehículo eléctrico con extensión de autonomía y querían producirlo a nivel industrial. Por lo que les propuse comprar su empresa y trabajar juntos. Ahora Emerald está asociada a nuestra empresa y básicamente es la división de ingeniería de LTC.
¿Cómo les convencieron en Emerald de la viabilidad de su producto?
Trabajamos 6 meses con los modelos conceptuales. Luego dijimos “en 11 meses, el 31 de noviembre de 2014, tendréis que entregar dos modelos de demostración completos con las piezas disponibles de Geely Group. Esta fue la prueba del algodón. Se abrió el telón y salió el modelo de prueba, tenía un gran aspecto, no se distinguía de los modelos de producción.
¿Cómo compensan los costes del aluminio y el tren de potencia eléctrico?
No es un vehículo barato. La clave para nosotros es que sea competitivo para el conductor y más barato que el TX4 actual. El automóvil permite ahorrar 500 libras mensuales en gasolina.
¿Cuál es la relevancia de la planta?
Tenemos que aumentar el volumen paulatinamente, pero tenemos un umbral de rentabilidad bajo. 325 millones de libras – 50 millones por la fábrica – parece mucho, pero es mucho menos que una planta tradicional. Un taller de pintura y carrocería de acero con utillaje cuesta como mínimo 400 millones de libras. La nuestra costó 50 millones de libras, incluido el prensado de los paneles de plástico.