La planta de Renault en Valladolid está ensayando las últimas tecnologías digitales de producción
La planta española se ha convertido en la estrella de la red de producción de Renault ya que produce uno de los lanzamientos más exitosos en la nueva línea de productos: el SUV compacto Captur. Desde que comenzara la producción en 2013, el vehículo ha superado la cifra de 1 millón de unidades y, aunque la mayoría se destinan a Europa, muchos se exportan también a mercados lejanos como Corea del Sur y China.
La planta de Valladolid comenzó a producir en 1972, pero a pesar de su diseño fraccionado y edificios clásicos, se ha reinventado hasta el punto de que ha sido elegida como una de las tres plantas de la red de Renault líderes en tecnologías digitales de ‘Producción 4.0’. La planta ha sido pionera en avances como la maquinaría con Wi-Fi, tabletas inteligentes para supervisores, etiquetado digital de piezas. La empresa aspira a aumentar la productividad, reducir las pérdidas de tiempo y mejorar la seguridad. El objetivo de los cambios es ayudar a clientes y trabajadores. “Los humanos estamos en el centro de la planta del futuro", afirma José-Vicente de los Mozos, director de cadena de suministro y producción de Renault (y antiguo director de planta en Valladolid).
La planta también produce un número limitado del Twizy, una scooter eléctrica de cuatro ruedas, pero la gran aportación de Valladolid a la red de Renault es el Captur, que sigue siendo el más vendido en su segmento en Europa a pesar de los varios lanzamientos de la competencia desde que debutara hace cuatro años. El año pasado produjeron 245,696 automóviles, de los cuales tan solo 2,855 fueron modelos Twizy. Este año espera producir 250,000 unidades, muy por encima de las 212,133 de 2014 (el primer año completo de producción del Captur).
Valladolid se encuentra a 200 km de Madrid en el centro de España y es también fundamental en la producción de motores de Renault. La planta de motores se encuentra en el mismo terreno de 100 hectáreas a las afueras de esta modesta ciudad y produce un sorprendente 42% de los motores de la marca Renault en tres turnos de producción. También produce motores, tanto de gasolina y diesel, para la marca Dacia, su socio Nissan y Daimler, que utiliza los motores diesel de 1.5 litros para sus vehículos compactos de segmento A. Incluso suministra motores para la india Mahindra. En total los motores de la planta se utilizan en 36 modelos individuales. Con 1.56 millones de motores producidos el año pasado, se trata de la mayor planta de motores de Renault, superando incluso a la de Cleon en Francia, que solo supera a su rival español en producción total cuando se cuenta la producción de cajas de cambios.
La localización aislada de la planta en el centro de España tiene más sentido cuando tenemos en cuenta que la planta de Renault en Palencia se encuentra a tan solo 50 km al norte. Allí es donde Renault construye el modelo Megane de segmento C y el SUV compacto Kadjar de la misma estructura. El año pasado produjo una cantidad récord de 332,247 vehículos, respecto a los tan solo 133,701 en 2014; una producción que ha ayudado sin lugar a dudas a Valladolid en el sur, que no solo suministra los motores diesel y gasolina, sino también los parachoques para ambos autos de Palencia además de piezas estampadas y piezas de plástico para el Megane.
Mejoras digitales Muchos constructores están investigando maneras para mejorar la producción con las últimas tecnologías digitales, Renault es una de ellas. El centro de desarrollo tecnológico de la empresa se encuentra en Boulogne, al norte de Francia, donde emplea a 300 trabajadores. Valladolid, Cleon en Francia y Curitiba en Brasil son las plantas que funcionan como cobayas, pero el primer paso en esta revolución conectada es garantizar que las máquinas, la gente e incluso las piezas que hay que conectar digitalmente puedan hacerlo realmente, lo que significa implementar Wi-Fi en toda la planta. Este proyecto ya se ha completado al 80% en todas las plantas de Renault, afirma Eric Marchiol, director de transformación digital en producción y cadena de suministro.
Luego hay que hacer que las máquinas sean ‘inteligentes’, lo que representa instalar sensores o cámaras en todas las piezas de maquinaria importantes, incluidas las 300 prensas de estampado en todo el mundo, lo que llevará bastante tiempo. Luego hay que conectar los más de 5,000 robots. “Tenemos muchos tipos. Es un trabajo duro”, afirmó Marchiol. Así se generan datos, lo que significa que Renault puede realizar lo que denomina "mantenimiento predictivo", donde los técnicos localizan problemas antes de que afecten a la producción, o por lo menos lo intentan.
La otra mejora es cada vez es más popular en la industria, la creación de 'emparejamientos' de autos y motores con las piezas que necesitan en contenedores que viajan junto al automóvil a lo largo de la cinta de transporte de ensamblado. La flota de 210 vehículos automáticos guiados (AVG) suministra el contenedor con el kit al inicio del área de ensamblado, estos vehículos guiados siguen cintas magnéticas en el suelo para llevar los contenedores junto a la línea. Los trabajadores toman las piezas que necesitan y las colocan en la línea de ensamblado mientras permanecen en la cinta durante 20 a 50 metros, según la estación (hay 260 estaciones en la nave de ensamblado). Según Marchiol de Renault, esto ha transformado la línea de una "jungla de piezas" hace cinco años a un proceso mucho más sencillo.
Marchiol afirma que Renault probó vehículos de suministro de piezas autónomos como AGV, pero resultaron ser demasiado costosos en comparación con los que siguen la cinta magnética. La mayoría de AGV son bajos, tienen forma de patinete y proceden del especialista español Kivnon y funcionan empujando las carretillas por debajo.
Taller de pintura de dos tonos
La planta de estampado, el área de moldeado de parachoques y los talleres de pintura y carrocería se encuentran en áreas separadas, cercanas pero no adjuntas. El taller de carrocería trabaja en 2.5 turnos al igual que los principales procesos del ensamblado de automóviles (un medio turno se refiere a la mitad de la plantilla, no la mitad del tiempo). Si la fábrica trabajara a 3 turnos aumentaría su capacidad en 50,000 unidades hasta 300,000 vehículos, afirmó el director de la planta, Rafael Vázquez. Por otro lado, el taller de chapa está automatizado al 99% y cuenta con 468 robots.
Al igual que el taller de carrocería, el taller de pintura procesa 62 vehículos a la hora con 106 robots que pintan 11 colores. La dificultad aquí está en que el 79% de los Captur deben pintarse en dos colores, con el techo de un color diferente. Esto dobla el tiempo que el automóvil pasa en el taller de carrocería porque después de pintar la carrocería debe cubrirse y luego pasar de nuevo para pintar el techo.
La nave de ensamblado del Twizy está separada de la del Captur y produce tan solo 12 unidades por hora. 30 trabajadores construyen el vehículo y el chasis se suelda manualmente, una tecnología muy básica para un vehículo futurista. La nave de ensamblado del Captur tan solo tiene 10 robots pero al igual que el taller de carrocería y pintura, produce 62 vehículos por hora en dos turnos y medio. Ocupa el mismo edificio antiguo de 1972 de cuando comenzó a operar la empresa, con el tradicional tejado dentado y ventanales en los montantes, desde entonces se ha dividido en dos áreas. Las puertas y los paneles de mando tienen sus propias líneas de subensamblado.
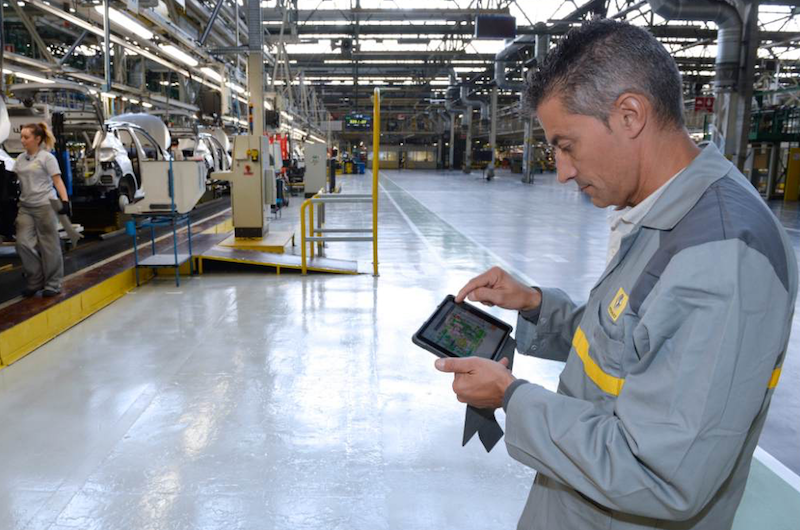
Una de las renovaciones más interesantes se produjo en 2012 cuando Renault instaló 50,000 metros cuadrados de celdas fotovoltaicas para pasar a la tecnología solar. Se encuentran sobre las nuevas áreas de aparcamiento cubiertas que Renault construyó al identificar el granizo como la mayor amenaza financiera medioambiental para la empresa.
Aumento de la producción de motores de gasolina Los consumidores han abandonado drásticamente el uso de motores diesel a favor de los motores de gasolina en toda Europa debido en gran parte por la crisis de las emisiones diesel, por lo que Renault se ha visto obligada a cambiar su producción en la planta de motores. En la actualidad el 70% de la producción en la planta de Valladolid son motores diesel, pero no por mucho tiempo. “Queremos aumentar la proporción de gasolina hasta el 50/50 lo antes posible. Esperamos conseguirlo para finales de año”, afirma la directora de la planta Anne Catherine Brieux.
Las ventas de vehículos diesel en Europa occidental cayeron el año pasado hasta el 46% durante los primeros ocho meses, un 50% menos que en el mismo periodo del año pasado, según las cifras del analista LMC Automotive. El declive ha reducido en un cuarto de millón las ventas de vehículos diesel hasta su menor nivel desde 2003, lo que ha forzado a los fabricantes como Renault a reorganizar su producción. “El mercado está cambiando muy rápido”, afirma Brieux.
El motor más importante de la planta es actualmente el diesel de 1.5 litros que se utiliza en las marcas de la alianza y en el rango Clase A de Mercedes. Construimos este motor en dos de las tres líneas y la recientemente reformada tercera línea produce los motores de gasolina de 1.2 litros de cuatro cilindros y el 0.9 litros de tres cilindros. El objetivo ahora es que las líneas de diesel sean tan flexibles como la nueva línea de gasolina, se utilizarán las mismas tecnologías, lo que permitirá construir motores diesel y gasolina en la misma línea. “Flexibilidad significa la posibilidad de mecanizar un cigüeñal para diesel, luego otro para gasolina y luego uno de gasolina de tres cilindros", afirmó Brieux.
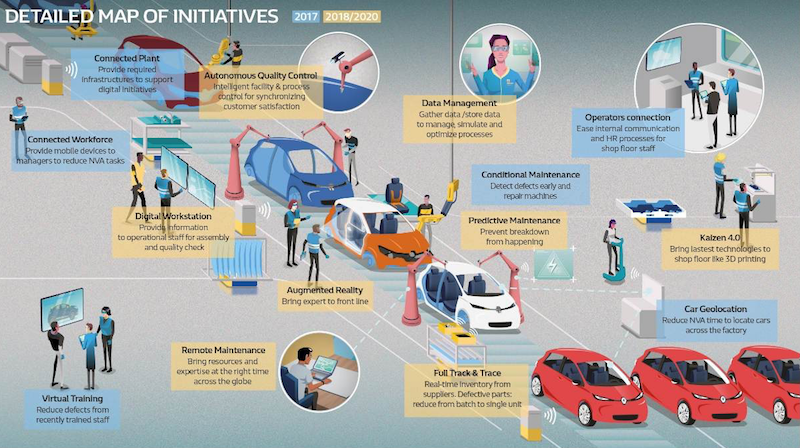
Esta es una estrategia de localización clave para la planta, pero no la única. Brieux quiere que los más de 350 proveedores de la planta de motores estén más cerca, lo que significa en España o en la cercana Portugal. En la actualidad algunos de los proveedores están tan lejos como Estados Unidos y Corea del Sur. “Se trata de reducir el tráfico de camiones y el nivel de existencias", afirma. Renault planea expandir el cercano parque de proveedores para la planta de motores y la planta de ensamblado.