OEMs enfrenta o desafio de assimilar um número crescente de veículos elétricos e montagens em suas operações de produção. Volkswagen e Renault mergulhou com o e-up! e o Zoe
A cinco quilômetros do centro da capital da Eslováquia, na margem norte do Danúbio, está a fábrica da Volkswagen Bratislava - casa do primeiro modelo VW que tem uma unidade completamente elétrica. A fábrica foi inaugurada em 1991 e no ano seguinte começou a produção em massa do Passat Variant. Empregando 9.400 funcionários, é um dos maiores empregadores da República Eslovaca e maior exportador do país. Bem como o elétrico VW e-up! a fábrica faz o VW Touareg, Audi Q7, Skoda Citigo e Assento Mii, além da carroceria do Porsche Cayenne.
Vladimír Viskup é chefe de chassis na fábrica. É em seu departamento que os trabalhadores instalam o motor elétrico e baterias, que chegam a partir da fábrica em Brunswick, Lower Saxony. Viskup, e tem o orgulho de exaltar as virtudes de sua força de trabalho e os processos de fabrico, o qual ele descreve como "a fábrica do futuro". "Para a montagem do e-up! nós treinamos funcionários extras", diz ele. "Na sala você vai ver, não há empilhadeiras. Todas as peças são trazidas para a linha por um sistema de transporte sem condutor. Além disso, você não verá os habituais cartões de informação de carro. Toda a instrução de entrada é tratada por via eletrônica, através de minicomputadores. Isso economiza toneladas de papel."
Nos últimos dois anos, Albrecht Reimold foi presidente da Volkswagen Eslováquia. Antes disso, ele havia dirigido a fábrica da Audi em Neckarsulm, na Alemanha. "Nós valorizamos muito a confiança demonstrada pelo conselho em nossa fábrica pela atribuição do e-up! para Bratislava", diz ele. "Enquanto nós estamos orgulhosos desse fato também reconhecemos que é um desafio para nós. No entanto, não é tudo novo uma vez que somos ajudados pelo fato de que construímos o híbrido Touareg aqui desde 2009 e assim temos experiência de mais de quatro anos com acionamentos elétricos.
"Todos os funcionários estão muito empenhados, curiosos e de mente aberta para a nova tecnologia. Suas habilidades e competências são muito importantes para nós e precisamos desenvolver estas. Por exemplo, nós treinamos mais de 3.200 trabalhadores em tecnologia de alta tensão, como parte do novo programa.
"É claro que a tecnologia de veículos elétricos é diferente das tecnologias tradicionais de fabricação automotiva, por isso tiveram que desenvolver um grande número de cursos de formação. Mas no coração de tudo está a segurança. A segurança de nossos funcionários é a prioridade absoluta: você deve chegar no trabalho saudável e ir para casa saudável novamente.
"Nós pedimos muito da nossa equipe nos interesses dos nossos clientes, mas também reconhecemos o desempenho. Da Cultura, a gestão desempenha um grande papel em [nossa organização]. Por exemplo, em uma pesquisa recente os índices de satisfação de Volkswagen como um empregador na Eslováquia voltou a aumentar em 4%. Isso nos deixa muito orgulhosos, assim como o fato de que nós tivemos participação acima da média na pesquisa. "
Montagem EVs em operações já existentes
Alguns fabricantes de automóveis estão optando por manter o fabrico e montagem de EVs e seus componentes separados, enquanto outros estão integrando-os em fluxos de produção existentes. Caindo firmemente na última categoria está a Renault, que lançou o Clio Novo ao lado da Zoe EV ao mesmo tempo em sua fábrica de Flins, localizada nos arredores de Paris. Os processos de produção das carrocerias Zoe e Novo Clio são tão semelhantes que é preciso um olhar cuidadosamente treinado para detectar as diferenças entre as duas, mas o Zoe é projetado exclusivamente para a propulsão elétrica e é repleto com a tecnologia elétrica mais avançada. Apesar disso, a sua chegada na fábrica não exigiu tantas adaptações à produção como seria de se esperar.
"A chegada de um veículo elétrico poderia ter introduzido uma série de mudanças, mas conseguimos mantê-las a um mínimo estrito", explica Didier Lehingue, vice-diretor da fábrica. "Esse foi o objetivo da equipe de 20 pessoas encarregada com o desenvolvimento industrial do Zoe." David Garreau, gerente sênior de qualidade para a industrialização do Zoe, diz que os primeiros 12 meses foram "fundamentais para definir a base e encontrar a organização industrial otimizada". O objetivo era encontrar soluções inteligentes, desde a fase de projeto até os métodos de produção, para adaptar os sistemas existentes e manter o investimento inicial sob controle. Por exemplo, a velha geração Acma ou robôs da ABB foram reutilizados. Depois de horas de reuniões, previsões e cálculos, estimativas de custos e o desenvolvimento do processo de ponta a ponta, as decisões foram finalmente dadas para as tecnologias e layout.
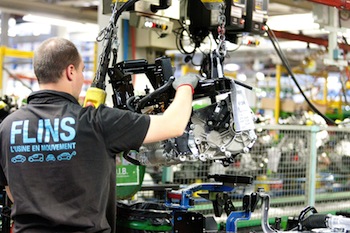
A chegada do EV solicitou alguns ajustes maiores na oficina de estampagem, que fabrica os painéis de abertura (portas e tampas traseiras). A produção tinha de se tornar suficientemente flexível para fazer os painéis de abertura por quatro modelos diferentes - o Zoe, Novo Clio, Clio e Nova Coleção Clio RS - em vez de apenas dois Anteriormente, o Clio RS III e Clio III. As carrocerias em branco das versões RS são então enviadas para Dieppe, onde são pintadas e montadas. Uma etapa extra foi adicionada em linha com a montagem para a instalação da bateria na parte inferior da carroçaria do Zoe. A linha de produção pode alternar entre a coleção de Clio e Novo Clio sem fazer quaisquer alterações, de modo que os três modelos são fabricados na mesma linha de uma forma fluida.
"Estamos desbravando novos caminhos através da montagem das baterias diretamente na fábrica de produção, em uma oficina de 500 metros quadrados criada a partir do zero e mantida em segurança sob sigilo por dezoito meses", diz Garreau. "Outro grande desafio consistiu [da] criação de uma linha de montagem utilizando processos de fabricação próximos aos encontrados em linhas de produção subsistemas mecânicas, com os operadores trabalhando em estações de trabalho fixas, em uma fábrica de automóveis, onde os operadores trabalham nos veículos conforme eles se movem ao longo de uma linnha de conjunto.
"Após longas discussões, a decisão foi finalmente alcançada sobre o processo de montagem da bateria. Os operadores trabalham nas baterias em uma paralisação, a fim de garantir a qualidade de construção, mas por um tempo limitada, a fim de manter o ritmo com o fluxo de produção dos veículos. Se eles não terminaram quando o seu tempo acabou, eles podem pressionar um botão para reter a bateria. Caso contrário, a bateria se desloca para a próxima estação de trabalho".
Permanecendo sãos e salvos
A oficina de montagem da bateria foi projetada para atender critérios rigorosos de qualidade e segurança, organizados mais como um 'quarto branco' do que uma oficina industrial convencional. A equipe do projeto optou por processos altamente automatizados, em especial, todas as operações sobre as baterias carregadas para 400V, a fim de proteger a segurança dos operadores. Mais de um terço das operações são realizadas por robôs, em comparação com apenas 10% de uma oficina de montagem mecânica
Cada funcionário na oficina de montagem da bateria é especialmente qualificado para trabalhar neste ambiente incomum. A oficina é dividida em duas zonas de segurança bastante distintas: a zona de 60V e 400V. Os riscos elétricos são limitados pela realização da maioria das operações manuais na zona 60V. A bateria é ligada na última hora no final da linha por dois operadores especialmente treinados. O escritório de design incluiu uma abertura no alojamento de bateria, que é utilizado para ligar os módulos de um para o outro no fim do processo.
A fábrica faz as juntas de montagem de duas partes, a fim de garantir a qualidade de montagem da tampa da bateria. A vedação de cinco metros é instalada por um robô em torno do perímetro da tampa e passa entre os parafusos. Um robô verifica a posição dos parafusos e envia o caminho exato de um segundo robô, que instala o selo, a fim de alcançar a precisão de uma ordem milimétrica. A vedação e as funções elétricas de todas as baterias são então testadas, em particular os ciclos de carga e descarga. Depois que as baterias são armazenadas, prontos para instalação.
Fabricação de motores
Enquanto o veículo é montado nos arredores de Paris, o motor elétrico para o Zoe é fabricado 51 milhas ao noroeste de Flins na fábrica da Renault Cléon na Normandia, que até recentemente produziu o motor de combustão interna Energy dCi.Mas a partir de meados do verão ele compartilhará essa instalação com a fábrica R240 para o Zoe. Foi preciso um investimento de €300 milhões ($344m) para deixar a fábrica pronta para motor elétrico e montagem da bateria. "Nosso objetivo é tornar a fábrica de motor e transmissão líder da Aliança", diz Mendi Ammad, diretor da unidade. "Cléon foi escolhido por duas razões:. Sua base de produção e sua engenharia e equipes operacionais"
Grande parte da maquinaria e muitos dos sistemas de inspeção instalados para o R240 já estavam no local. Este equipamento foi convertido e recondicionados, em parte ou na totalidade, pelo departamento de manutenção Cléon - economizando cerca de 40% do custo do investimento. Bem como a sua capacidade de produção, foi a força de trabalho que conferiu a Cléon o motor, tanto o seu tamanho como nível de habilidades. "Todos os especialistas de função estão presentes no local, para uma melhor comunicação e maior capacidade de resposta", acrescenta Ammad. "Como parte de uma abordagem de design para o custo, as equipes em Cléon ajudaram o centro de engenharia para escolher as peças mais adequadas em termos de facilidade de produção e controle de custos.
"Por mais de dois anos, a fábrica tem aproveitado de sua experiência para produzir a caixa de junção para a Zoe, ligado a um motor elétrico, que até agora é proveniente de um fornecedor. Nós desenvolvemos o domínio completo de montagem do módulo eletrônico e acumulando uma experiência robusta na produção do controle eletrônico de potência (PEC) na R240.

"A linha de montagem altamente manual do PEC exige minúcia considerável, dado o tamanho diminuto dos 180 componentes em questão. Três tipos de teste - estáticos, selagem, e dinâmico - são realizados em 100% dos PEC para verificar cerca de 20 critérios elétricos". Com eletrônica de potência sob controle, as equipes foram capazes de dedicar sua energia para outras áreas, como o rotor e estator. Lá eles foram capazes de chamar a experiência de parceria de aliança Nissan, que produz o seu próprio motor para o Leaf.
"O estator e rotor são as principais inovações essenciais para o motor e transmissão elétrico e exigiram uma melhoria das habilidades em novas tecnologias na Renault", acrescenta Ammad. "Em 2011, Cléon comprava as suas primeiras máquinas de rotor e estator para o departamento Protótipo da fábrica. Isto provou ser um trunfo importante ao selecionar as tecnologias e fornecedores para a máquina de enrolamento, em preparação para a produção de alto volume." A linha de estator possui o maior número de inovações de processo. "As operações de liquidação, laçam e impregnam estudos necessários de engenharia antes de processos de desenvolvimento complexos," Ammad confirma.
Conforme anunciado em agosto deste ano, a Audi desenvolverá a bateria para um SUV puramente eletricamente motorizado usando módulos de células poderosas dos fornecedores sul-coreanos LG Chem e Samsung SDI.
Os dois parceiros Audi planejam investir na tecnologia celular na Europa e abastecerão o produtor alemão de automóveis a partir de suas fábricas europeias. A intenção é que esta nova tecnologia dará aos motoristas do EV SUV uma gama de mais de 500 km.
"Junto com nossos parceiros de desenvolvimento da Coréia do Sul, estamos trazendo a produção da mais recente tecnologia de células de bateria para a União Europeia e reforçando a indústria europeia com esta tecnologia-chave", afirma Bernd Martens, membro do conselho de administração da Audi para a Compra.