A fábrica de Valladolid da Renault está liderando algumas das últimas tecnologias de fabricação digital.
A fábrica espanhola tornou-se uma estrela na rede de produção da Renault para fazer um dos lançamentos dos novos segmentos mais bem sucedidos da marca: o SUV pequeno Captur. Desde o início da produção em 2013, o carro passou pelo marco de "1m construídos" e, enquanto a maioria está ligada à Europa, vários também são exportados para mercados distantes como a Coreia do Sul e a China.
A fábrica de Valladolid começou a produção em 1972, mas apesar do layout fraturado e dos edifícios originais, reinventou-se no ponto em que foi escolhida como uma das três usinas na rede Renault, liderando algumas das últimas tecnologias digitais, incluídas na etiqueta de "Fabricação 4.0". Ao lançar avanços como máquinas habilitadas para Wi-Fi, tablets inteligentes para supervisores e marcação de peças digitais, o fabricante de automóveis espera aumentar a produtividade, reduzir o tempo perdido e melhorar a segurança. As mudanças são lançadas para ajudar o cliente e o trabalhador. "O ser humano está no centro da fábrica do futuro", diz Jose-Vicente de los Mozos, chefe de cadeia de suprimentos e fabricação da Renault (e ex-diretor da fábrica em Valladolid).
A fábrica também faz o scooter elétrico Twizy de quatro rodas em pequenos números, mas a visibilidade proeminente de Valladolid na rede Renault é principalmente graças ao Captur, que continua sendo o best-seller em seu segmento em toda a Europa, apesar de vários rivais fazendo lançamentos desde que estreou mais de quatro anos atrás. No ano passado, a fábrica fez 245.696 carros, dos quais apenas 2.855 eram Twizys. Ela espera produzir cerca de 250 mil este ano, acima dos 212.133 de 2014 (o primeiro ano completo de produção do Captur).
Valladolid, a 200 km a noroeste de Madri, no centro da Espanha, também é vital para as necessidades de produção de motores da Renault. A planta do motor compartilha o mesmo site de 100 hectares nos arredores desta cidade modesta e produz 42% dos motores da marca Renault em três turnos. Também faz motores, tanto a gasolina como a diesel, para a marca Dacia, o parceiro da Aliança Nissan e Daimler, que leva o diesel de 1.5 litros para a sua classe de carros pequenos em classe A. Também fornece motores para o Mahindra da Índia. No total, os motores da planta são montados em 36 modelos individuais. Os 1.56m de unidades produzidas no ano passado a qualificam como a maior planta de motores da Renault, superando até Cleon na França, que chega perto de seu rival espanhol na produção total quando as caixas de velocidades são levadas em consideração.
A localização isolada da planta no centro da Espanha faz um pouco mais de sentido quando se leva em conta que a planta Palencia da Renault fica a apenas 50km ao norte. É aí que a Renault constrói os modelos do segmento C do Megane e o SUV compacto Kadjar. No ano passado, fez um recorde de 332.247 veículos, acima de apenas 133.701 em 2014; uma mudança que, sem dúvida, ajudou Valladolid ao sul, que fornece não apenas motores a gasolina e diesel, mas também para-choques para carros Palencia, peças estampadas e peças de plástico para o Megane.
Melhorias digitais
Muitos fabricantes estão investigando maneiras de melhorar a produção usando a tecnologia digital mais recente, e a Renault não é diferente. O centro da empresa para desenvolvimento de tecnologia fica em seu centro Renault Digital em Boulogne, no norte da França, onde a empresa emprega 300 funcionários. Valladolid, Cleon na França e Curitiba no Brasil são as plantas de teste, mas o primeiro passo nesta revolução conectada é garantir que essas máquinas, pessoas ou mesmo peças que precisam ser conectadas digitalmente possam realmente fazê-lo, o que significa que há Wi- Fi em toda a planta. Este projeto já está 80% concluído nas fábricas da Renault, observa Eric Marchiol, chefe de transformação digital para a fabricação e cadeia de suprimentos.
Assim, você precisa tornar as máquinas "inteligentes", o que significa instalar sensores ou câmeras em cada peça de maquinaria significativa, incluindo 300 prensas para estampar em todo o mundo, algumas das quais são bem antigas. Então os mais de 5000 robôs devem ser conectados. "Nós temos muitos tipos. Assim é um trabalho difícil", disse Marchiol.
Este agora cria dados, o que significa que a Renault pode executar o que chama de "manutenção preditiva" - na qual os técnicos podem detectar problemas antes deles afetarem a produção, ou pelo menos tentar.
Em seguida, há rastreabilidade, que significa rastrear o máximo possível de 5.000 peças de um carro, usando tags RFID (identificação por radiofrequência) ou digitando códigos QR. Isso ajuda a identificar onde as peças estão, transmitindo informações para a equipe de montagem (por exemplo, configurações de torque) e identificar peças com "problema" para um grau mais limitado do que apenas por lote. Cada carro também possui uma etiqueta RFID, dando aos gerentes uma visão em tempo real de onde estão os veículos. O plano é abrir esta informação aos clientes, que então conseguem rastrear seu carro através do processo de construção.
O Wi-Fi em toda a planta permitirá aos supervisores registrar problemas e enviar fotos por meio de tablets aos gerentes sem a necessidade de papelada ou passeios demorados para reportar. As respostas chegam mais rápido e a Renault reconhece que isso incrivelmente economiza 90 minutos por dia para os supervisores.
A outra atualização é uma que está se tornando mais popular em todo o setor - carros e motores "kitting" com as peças em um contêiner que viaja com o carro ao longo da correia transportadora de montagem. O contêiner de kitting é entregue no início da área de montagem pela frota Valladolid de 210 AGVs (veículos guiados automáticos), que seguem tiras magnéticas no chão para ao lado da linha dos reboques. Os trabalhadores apanham as peças de que necessitam e as encaixam na linha de montagem enquanto estão de pé na correia por 20 a 50 metros, dependendo da estação (dos quais 260 estão no salão de montagem). De acordo com o Marchiol da Renault, isso transformou a linha de uma "selva de peças" há cinco anos para uma operação muito mais enxuta.
Marchiol diz que para os AGVs, a Renault testou veículos autônomos para fornecimento de peças, mas eles mostraram-se muito caros em comparação a aqueles que seguiram a banda magnética. A maioria dos AGVs são versões baixas e estilo skate feitos pelo especialista espanhol Kivnon, que empurra carrinhos de rodas por baixo.
Oficina de pintura de dois tons
A fábrica de estampagem, a área de moldagem de para-choques e carroceria, bem como as oficinas de pintura estão todas localizadas em um site separado, próximo, mas não anexado. A oficina está em uma configuração de 2.5 turnos como todas as principais operações dentro do site de montagem de carro (a mudança para "meio" refere-se a metade do pessoal, e não a metade do tempo). A execução de três turnos em toda a planta elevaria a capacidade em 50 mil por ano para 300 mil, diz o diretor da fábrica, Rafael Vazquez. No entanto, a oficina é 99% automatizada com 468 robôs no local.
Como a oficina de carroceria, a oficina de pintura funciona com 62 veículos por hora com 106 robôs pintando 11 cores diferentes. A dificuldade aqui é que 79% de todos os Capturs são ordenados em dois tons com um telhado colorido diferente. Isto duplica o tempo que o carro gasta na oficina de pintura porque uma vez que foi pintada a carroceria tem que ser mascarada e correr novamente para pintar o telhado.
O salão de montagem do Twizy é mantido separado das operações do Captur e tem uma capacidade de apenas 12 veículos por hora. Uma equipe de 30 constrói o carro e o chassi é soldado à mão - um método de baixa tecnologia para um carro tão futurista. O salão de montagem da Captur possui apenas 10 robôs e, como a oficina de carpintaria e de pintura, constrói cerca de 62 veículos por hora em dois turnos médios por dia. Ele ocupa o mesmo prédio vintage de 1972 que a planta começou a usar, completo com telhado tradicional serrilhado com painéis de janela, mas desde então foi dividido em dois andares. As portas e os painéis têm suas próprias linhas de subconjuntos.
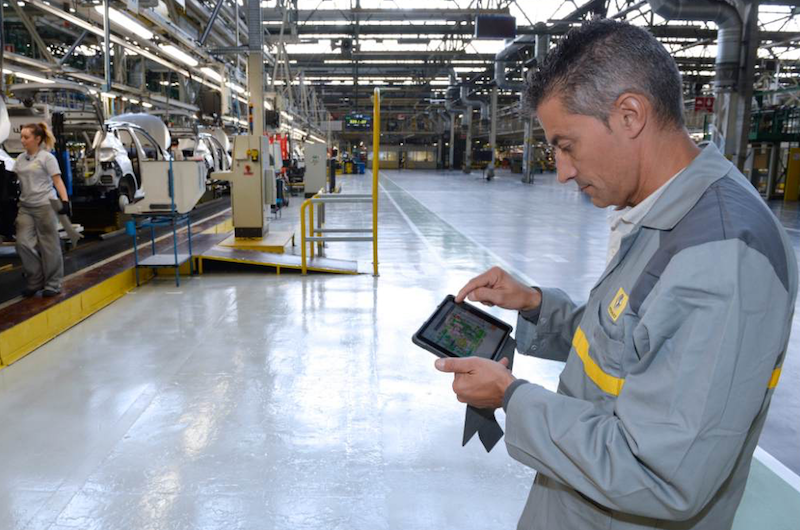
A linha de montagem Captur será ligeiramente estendida para 2019, quando a planta introduzirá um segundo modelo na linha, outro SUV do segmento B, revela Vasquez. Não há mais informações disponíveis sobre o carro, mas é provável com base no Captur, possivelmente um pouco maior, com o nome Grand. O lançamento do novo modelo complementará a demanda pelo Captur, que, em seguida, ficará ultrapassado, então o resultado geral não vai mudar, acrescenta Vasquez. O novo carro (mas sem data ou o modelo exato), foi anunciado no ano passado como parte de um novo "acordo de competitividade" assinado com os sindicatos espanhóis para cobrir 2017-2020, que inclui maior flexibilidade do tempo de trabalho e aumentos salariais limitados até 3,5% em quatro anos.
Uma atualização interessante para a fábrica ocorreu em 2012, quando a Renault instalou 50 mil metros quadrados de células fotovoltaicas como parte de uma mudança mais ampla para a energia solar. Eles foram instalados em cima de novas baías de armazenamento de veículos cobertas, que foram construídas depois que a Renault identificou granizo como "de longe" a maior ameaça financeira ambiental para a planta.
Aumento da produção de motores a gasolina
O grande consumidor que se deslocou do diesel para carros com motor a gasolina em toda a Europa, provocado pelas consequências da crise das emissões a diesel, forçou a Renault a mudar drasticamente sua produção na planta do motor. Atualmente, 70% da produção na planta de motores de Valladolid são diesels, mas não por muito tempo. "Nós achamos que precisamos aumentar a gasolina para 50/50 o mais rápido possível. Provavelmente faremos isto até o final deste ano", diz a gerente da fábrica, Anne Catherine Brieux.
As vendas de automóveis a diesel na Europa Ocidental neste ano caíram para 46% nos primeiros oito meses, abaixo de 50% em relação ao mesmo período do ano passado, de acordo com dados dos analistas LMC Automotive. O declínio eliminou um quarto de milhão de vendas de diesel para levá-los ao nível mais baixo desde 2003, forçando fabricantes como a Renault a mudar para se ajustar. "O mercado está mudando muito rapidamente", diz Brieux.
O motor mais importante da planta atualmente é um diesel de 1.5 litros usado em todas as marcas da Alliance e na gama Mercedes A-class. Ele é construído em duas de suas três linhas, com a terceira linha recentemente revisada produzindo as unidades a gasolina de três cilindros de quatro cilindros e 0.9 litros de 1.2 litros. O impulso agora é tornar as linhas a diesel flexíveis como a nova linha a gasolina, implantando o mesmo tipo de tecnologia e permitindo que os motores a gasolina e a diesel sejam feitos em ambos. "Flexibilidade significa a possibilidade de fazer uma virabrequim para diesel, depois um para gasolina, depois para gasolina de três cilindros", disse Brieux.
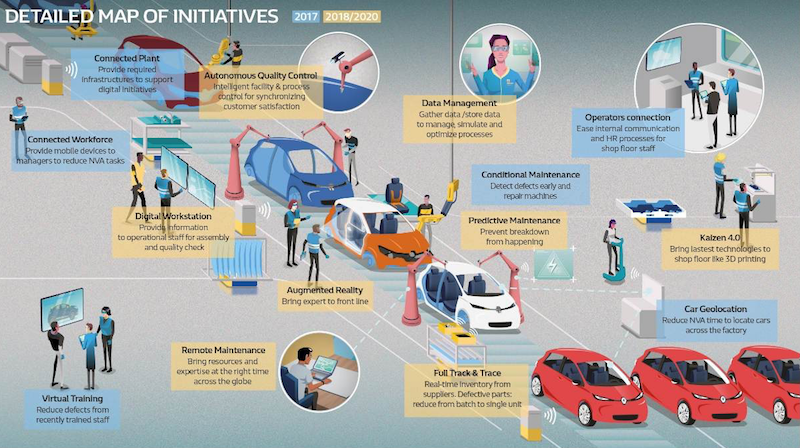
A linha de gasolina também está mudando para o mesmo processo de kitting visto no salão de montagem de veículo, que comercializa peças para um motor específico no início da montagem e depois segue a linha de produção, outra mudança que ajudará quando as linhas a diesel se tornarem mais flexíveis. A planta também foi agraciada pela expectativa da Renault de investir em uma nova fundição para fazer blocos de alumínio para os motores a gasolina, anunciado no ano passado como parte de uma expansão mais ampla de 600 milhões de euros da instalação que inclui a adição de outro modelo à planta de montagem de veículo, conforme referido acima. Atualmente, os blocos de motores de gasolina vêm de Cleon na França ou Pitesti na Romênia, mas isso mudará quando a fundição abrir no próximo ano. Os blocos de motores a diesel provêm de fornecedores, observa Brieux. "Precisamos de mais capacidade à medida que a demanda de gasolina aumenta", disse ela.
Este é um movimento de localização chave para a planta, mas não é o único. Brieux quer mais de 350 fornecedores da fábrica de motores mais próximos da fábrica, o que significa dentro da Espanha ou perto em Portugal. Atualmente, os fornecedores podem estar tão distanciados quanto os EUA e a Coreia do Sul. "Trata-se de reduzir os caminhões na estrada e reduzir os estoques", diz ela. A Renault planeja expandir o parque de fornecedores nas proximidades da planta de motores e da fábrica de montagem.