Engine downsizing has gone some way to achieving the ideal combination of performance and efficiency. However, this concept presents challenges in both the design and production of the engines. To achieve greater efficiency the engines have to become physically smaller and lighter while
producing acceptable levels of power and refinement without compromising fuel efficiency and emission levels. This usually means greater complexity of the thermal, emission and fuel management systems as well as in the production processes.
Many of the major OEMs have been developing technologies that can be applied to both existing engine configurations and completely new units. Larger capacity, multi-cylinder engines have seen a shift to fewer cylinders and a reduction in capacity which, coupled with the use of forced induction, direct injection and, in some cases, cylinder deactivation systems, provide all the attributes of power and smoothness but with much improved efficiency.
Here we take a look at the engine downsizing strategy of Ford and VW, focusing on two current examples of downsized engines in their ranges.
Ford EcoBoost
This all new, three-cylinder 1.0-litre unit joins Ford’s current EcoBoost petrol engine range, combining turbocharging, direct injection and twin variable cam timing. It incorporates a number of new features including integrated exhaust manifold, offset crank and variable oil pump, dual-split cooling system and a unique unbalanced flywheel/pulley. Currently fitted in the new Ford Focus, it will be available in the B-MAX and C-MAX models later this year.
AMS spoke to Roland Ernst, chief programme engineer for the Ford EcoBoost, to find out how the I-3 EcoBoost engine had progressed from development to production. AMS: Can you offer an overview of the development of the EcoBoost engine.
Roland Ernst (RE): The development of efficient, small displacement engines has been on going for over a decade, but the specific development of the three-cylinder EcoBoost unit began around four to five years ago. This project had a very experienced, single team dedicated to it. Where possible we would try to use existing components but due to this unit’s extremely small scale, almost every aspect of the engine was brand new, with the carry-over of parts probably less than 8% of the total.
AMS: What was the principle aim for Ford when designing this engine?
RE: The wider aim of producing engines like this is the reduction of CO2 emissions across the Ford portfolio. The EcoBoost family is to be one of the key enablers in this process.
AMS: Was there a gap in the Ford engine range that needed to be filled? RE: No, if
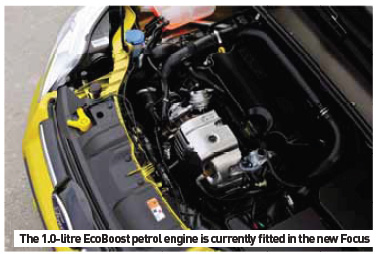
AMS: What were the production/assembly considerations when designing the EcoBoost?
RE: In terms of manufacturing considerations when designing an all new engine like this, and how this transfers to manufacturing facilities, we wanted to ensure as much standardisation as possible; we wanted to set new standards for double process. With the 1.0-litre EcoBoost, we were very keen to minimise the complexity of the engine as it will be rolled out across many markets, with projected production of 800,000 to one million units from production facilities around the world. So standardisation of processes and components along [with] minimised complexity in assembly were key considerations. We currently have production facilities in Cologne and Romania with more to come. Another consideration was energy efficiency in production. For example, at the Cologne plant we have reduced electrical energy consumption in the production of this engine by 60%. Also the water usage to machine the cylinder heads has been reduced by 99%. So this was a key consideration for us in the production of EcoBoost.
Over the period 2012 to 2015 Ford plans to produce more than 1.3 million low-CO2 EcoBoost engines to go into European vehicles. More than 800,000 of these are expected to be the new 1.0-litre three-cylinder unit, produced at the company’s new plant in Craiova, Romania and in Cologne, Germany.
The company has invested €134 million in the new 1.0-litre Eco- Boost production facility to make it as flexible as possible, so that it can quickly be adapted to produce other engine blocks. The 1.0-litre EcoBoost production facility was developed by the manufacturing engineering team, Dunton, UK, using Ford’s virtual manufacturing lab. Four times as much virtual development took place compared with previous projects. Production of the 1.0-litre EcoBoost has also started at Ford’s new facility in Craiova, Romania – boosting European production capacity to up to 700,000 engines.
Covering 184,000m2 the Cologne engine plant has produced 26 million engines since 1962. Some 97 new machines – including 55 automations and 14 semi-automations – have been installed on the 580-metre-long production line for 1.0-litre EcoBoost production. Components can be manufactured to tolerances of just 10 microns – 10 to 20% the thickness of a human hair. Engines spend 3.5 hours each on the assembly line.
Ford has spent €1.7 million on employee training, with the 870 employees at the Cologne plant having each spent on average a total of two full weeks training for 1.0-litre EcoBoost production. Ninety seven new machines, including 55 automations and 14 semiautomations have been installed on the 580-metre-long production line at Cologne for 1.0-litre EcoBoost production
AMS: How does the EcoBoost engine reflect Ford’s engineering strategy for the future and how will this technology be transferred across other Ford engine variants?
RE: The 1.0-litre Ecoboost is actually the fourth variant in this ‘family’, with the downsizing concept already being implemented in the US market with the move from eight to six cylinders and six to four cylinders. So the downsizing concept is being rolled out across the Ford engine range. The 1.0-litre EcoBoost is the most extreme development of this, with the highest energy density and highest power output for the swept volume per litre. It features the key elements of the Ecoboost technology (turbo-charging, direct injection and variable valve timing) that are seen across the range but we then rescaled it for the 1.0-litre three-cylinder. This was Ford looking at the next level of engine efficiency. So we had the proven downsizing concept and technology and then looked to develop it further. There were three major areas we wanted to deliver on: very efficient combustion to optimise the energy conversion; very good thermal management, for example where we have used a cast iron block – not just for cost reasons but also to improve warm-up times, as managing the thermal dynamics of the engine is a key to improving efficiency; friction reduction, where we have done a lot of development to optimise any components were moving surfaces are in contact. Together with our lubricant partner, BP, we have developed a specific lubricant for the EcoBoost engine.
AMS: Can you talk us through some of the innovative technologies employed on the EcoBoost engine.
RE: Firstly, none of the technologies are revolutionary; rather they are developments of classic engineering solutions. The internal timing belt was developed with a very good partner and is extremely robust, having been extensively tested for durability. The reason for using this configuration is that it offers a significant advantage in fuel consumption, producing much less friction. The belt is also much quieter than a chain, which contributes to the engine’s overall refinement.
AMS: Did locating a timing belt internally within the engine have any implications when it came to production assembly?
RE: Not really, the process is the same – timing the camshaft to the crank. The belt is still positioned at the end of the camshaft; it’s then enclosed as part of the engine internals.
AMS: You mentioned working on the refinement of the engine. You opted for an unbalanced crank and flywheel to tune out the engine resonances. Did this present any difficulties in production?
RE: This was really dealt with at the design stage; the amount of energy and resource you employ to produce a perfectly balanced component is the same as producing one that is engineered to be unbalanced to a specific degree. So by the time you get to the production process everything has been adjusted and adapted to suit. In terms of the overall acoustics of the engine, the design of the turbocharger also played a part. It ensured that the combustion chamber pressures were very even cylinder-to-cylinder, so this takes away a lot of the roughness from a combustion point of view.
AMS: Can you take us through the block and cylinder head design and materials.
Minimum Quantity Lubrication (MQL) reduces the amount of coolant required to machine 1.0-litre EcoBoost aluminium cylinder heads to just 1 litre for 250 units, compared to up to 500 litres using previous cooling methods – a reduction of up to 99.8%.
Where MQL could not be introduced, Ford has streamlined coolant usage for maximum efficiency. 1.0-litre EcoBoost production in Cologne will use a total volume of 235,000 litres of coolant, compared to 1.25 million litres used in similar high volume production processes. New cold testing technology performs 31 performance checks on completed engines in less than two minutes, without using fuel to run the engine. By limiting the amount of hot testing required, cold testing reduces fuel consumption and CO2 emissions from testing by 66% compared with previous V6 engine production, saving up to 115,500-litres of fuel and roughly 265 tons of CO2 per year at full capacity.
Rather than testing for leaks in high pressure fuel systems using air, Ford has invested in equipment that can test using helium, which enables detection
RE: In terms of the block, cast iron is heavy but from the start we set ourselves a very ambitious target of making the EcoBoost engine comparable with the best aluminium block engines. To do this we have optimised every component for weight. This required us to see how we could save a few grams of weight on each part. For the block we looked at structural optimisation of the casting; whereever we didn’t need any material, we took it out. So if you look inside the block, in place of webbing and bulkheads we have ribbing. The result is a very lightweight cast iron block that still has the necessary strength and rigidity.
For the cylinder head we had the expertise of the Ford materials lab in Dearborn MI. (US). We have used the best material for this, again optimised for weight. An important factor was the thermal loading, since the 1.0-litre EcoBoost is the highest performing engine, per litre, of any in the Ford range. A key design feature was to optimise the temperature loading in what is a very compact head. A key driver was fuel economy. The better the air/fuel ratio, the hotter the combustion. The very high exhaust gas temperatures would damage the turbocharger over time so the head has the exhaust manifold integrated into the casting and features a water jacket to cool the exhaust gases.suit. In terms of the overall acoustics of the engine, the design of the turbocharger also played a part. It ensured that the combustion chamber pressures were very even cylinder-to-cylinder, so this takes away a lot of the roughness from a combustion point of view.
AMS: Can you take us through the block and cylinder head design and materials.
RE: In terms of the block, cast iron is heavy but from the start we set ourselves a very ambitious target of making theEcoBoost engine comparable with the best aluminium block engines. To do this we have optimised every component for weight. This required us to see how we could save a few grams of weight on each part. For the block we looked at structural optimisation of the casting; whereever we didn’t need any material, we took it out. So if you look inside the block, in place of webbing and bulkheads we have ribbing. The result is a very lightweight cast iron block that still has the necessary strength and rigidity.
AMS: Did you need to use any special materials or casting techniques in producing the block and head?
RE: There weren’t really any special requirements here. We have some very good, very experienced partners supplying our castings and there was a lot of knowledge-sharing between them and Ford. They provided the best materials for cost and performance.
AMS: What were the biggest challenges in designing and producing this engine?
RE: There was no one area where we had major difficulties, but obviously there were multiple challenges in trying to achieve the high levels of performance, refinement and fuel economy in one very compact package. It had to meet the EcoBoost concept requirements and be viable to mass produce. So each part of the engine was considered and thoroughly researched and tested.
AMS: At what point did the production department become involved?
RE: We had representatives from production involved from the very beginning. Their input was very important – asking questions, pointing out potential problems in production and offering solutions.
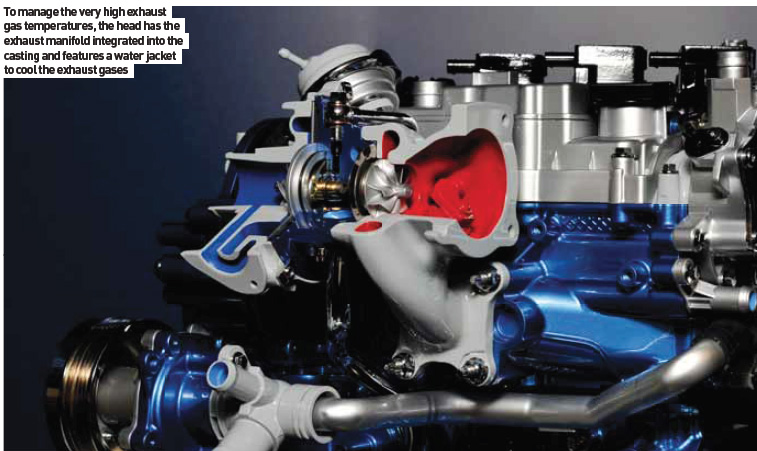
Fiat Powertrain Technologies has taken the downsizing philosophy one step further by developing a twin-cylinder engine. As for all vehicle makers the aim is to reduce fuel consumption and CO2 emissions, in respect of future Euro 5 and Euro 6 emissions standards, but offer the same performance as a large engine.
The concept behind this engine is the downsizing from a conventional 4-cylinder engine to a 2-cylinder turbocharged engine that incorporates the company’s MultiAir electronic inlet valve control system. As well as reducing fuel consumption, the twin-cylinder engine configuration also results in a 20% reduction in weight and 25% in volume inside the engine bay compared to a 4-cylinder engine with the same power output.
This twin-cylinder engine can achieve a maximum output of 105bhp in the Mono Fuel petrol version (a 65bhp aspirated version, also equipped with the MultiAir system, is also under development). The SGE engine family uses a crankshaft balancing system to reduce vibration and noise levels compared to other 2- and 3-cylinder engines.
The MultiAir system controls the air in controlled-ignition petrol engines without the usual throttle valve, providing a greater degree of fl exibility than with mechanical timing systems. This electrohydraulic valve activation technology is operated by introducing an amount of oil into a high pressure chamber between the camshaft and the engine inlet valve. This can be varied by a valve, which in turn is controlled by a specifi c electronic control unit.
This allows the opening profile of the valve to be modifi ed in response to the request for air from the engine and to the running speed. Different strategies can be employed (Early Inlet Valve Closing – EIVC, Late Inlet Valve Opening – LIVO, or Multi-Lift) to optimise combustion effi ciency, improving power output, torque, consumption and emissions. Another advantage of this system is that the air pressure upstream of the valves is always constant. This characteristic allows the torque response of the engine to be increased without any delay, on both aspirated and a turbocharged engines.
Volkswagen EA211 engines
Volkswagen has similarly opted for small displacement engines with turbochargers. The company’s new EA211-series petrol engines are made up of both three-cylinder and fourcylinder configurations and are part of a new vehicle production structure known as Modular Transverse Matrix (MQB).
Component optimisation
The EA211 is a complete redesign with only the cylinder spacing of 82mm carrying over from the previous EA111 engine series. Weight optimisation was a key factor in the development of this engine series. Materials and integration of components were a major consideration. For example the 1.4-litre TSI engine uses an ultra-rigid die-cast aluminium block, which gave a 22kg weight advantage over the grey cast iron block from the EA111 series units. This attention to lightweight construction extended to every part of the engine, with the developers reducing the main bearing diameter of the crankshaft on the 1.4 TSI from 54 to 48mm. The crankshaft itself was lightened by 20%, while the weight of the connecting rods was reduced by 25%. The rod bearing pins are bored hollow and the aluminium pistons have also been weight optimised.
Dual-loop cooling
Considerable development has gone into effective thermal management. To both fully utilise exhaust energy in hot operation and cool more effectively at high loads, the exhaust manifold of the new EA211 engines was fully integrated in the cylinder head complete with its own cooling jacket. Volkswagen engineers also devised a dual-loop cooling system, with the base engine cooled by a high-temperature loop with a mechanically driven coolant pump, while a low-temperature loop, powered by an electric pump, circulates coolant to the intercooler and turbocharger housing when needed. Due to the construction of the exhaust manifold, Volkswagen was able to use a very narrow single-scroll turbocharger. This reduced the weight of the cylinder head/turbocharger component group.
The intercooler has been integrated in the induction pipe which is made of injection-moulded plastic. This helps to significantly accelerate the pressure build-up, which makes this small engine very responsive.
Less friction
Another goal was to significantly reduce the internal friction of the engine. To this end, the camshafts are driven by a single-stage, low-friction toothed belt design with a 20mm wide belt and load-reducing profiled belt wheels rather than a chain. Actuation of the valve drive via roller cam followers and an anti-friction bearing for the highly loaded first camshaft bearing also reduces friction resistances. To reduce the engine mounting space, the ancillary components such as the water pump, air conditioning compressor and alternator are screwed directly to the engine and the oil sump without additional brackets.
To reduce emissions and fuel consumption further, and to improve torque in the lower rev range, the intake camshaft on all EA211 engines is adjustable over a range of 50° crankshaft angle – on the 103kW / 140PS 1.4 TSI, an exhaust camshaft adjuster is added. Now the TSI sixteenvalve, four-cylinder engines of the EA211 series feature a cylinder deactivation system in the form of Active Cylinder Management (ACT). Volkswagen is the first carmaker to introduce this technology in a mass-produced four-cylinder engine. At low and medium load, two of the cylinders are shut off by the ACT system, which reduces fuel consumption in the EU driving cycle by 0.4 l/100km. Weight is still a consideration here, with the components of ACT system weighing just 3kg. Their actuators, the camshafts and their bearing frames are integrated in the cylinder head; two lowfriction bearings reduce friction of the shafts.
Modular matrix
Volkswagen has developed different modular component sets. The most recent of these is the Modular Transverse Matrix (MQB). This enables the integration of drive systems – in an identical mounting location – that range from two newly developed, modularly constructed engine petrol and diesel series (EA211 / EA288) and alternative drives such as CNG (natural gas), hybrid or drive components for electric vehicles.
As part of this, the EA211 series engines have a ‘rotated’ cylinder head – the exhaust side now to the rear as opposed to the orientation of the previous EA111 series, with the ‘hot’ exhaust side at the front. Also, the engine is tilted towards the firewall – bulkhead between engine compartment and passenger compartment – at an identical angle of inclination (12°) to the diesel engines of the EA288 series. This offers the advantage that the exhaust line, driveshafts and gearbox mounting position can be standardised, also the engine’s mounting length that has been shortened by 50mm providing more interior space.
VW’s same-parts principle, through its MQB strategy, is clearly demonstrated by the EA211 engine series. As well as the standardisation (of production) of the cylinder head, engine block, crankshaft, connector rods and bonnet modules, it also follows through to other components. The fuel induction system (such as the charge air pathway, the air filter, induction pipe, intercooler, throttle valve and control drive) is also identical across all variants. Adopting this uniform basic architecture enables greater efficiency in production and assembly as well as global procurement.
engines, finds Frost & Sullivan
Engine downsizing, which has been a major trend in European diesel engines over the past decade, is poised to have a major impact on gasoline engines. This trend will also have a positive impact on the demand for technologies supporting downsizing, such as turbochargers and variable valvetrains. “Due to comparatively lower CO2 emissions, diesel engines will not face a challenge in complying with CO2 limits; hence, the limitations in downsizing diesel engines will not be an issue,” notes Frost & Sullivan senior research analyst Bharath Kumar Srinivasan. “Reducing the level of downsizing will also help control NOx emissions from these engines, which are being tightened for Euro 6 (to be enforced in 2014).” The number of cylinders in gasoline engines is likely to decrease only for engines below 1.2 litres. About 35-38% of gasoline engines are likely to be turbocharged by 2018. This high level of turbocharging by European OEMs is likely to help in the market growth of boosting technologies. Legal regulations and end-consumer environmental awareness will motivate the sales of vehicles with small engines. For example, the car scrappage schemes in 2009 reduced the average displacement of engines in Western Europe. Such initiatives will help boost engine downsizing. The addition of supporting technologies such as turbochargers and variable valvetrain technologies are expected to drive costs and this is likely to impact take-up rates in cost-sensitive segments. “With improved emissions and performance, without drop in fuel economy, being the key drivers, engine downsizing is all set to have a major impact towards achieving emissions of less than 120g/km CO2 in two-thirds of new car sales by 2016,” concludes Srinivasan. www.frost.com