El aumento en el uso de este material ligero representa nuevos y mayores desafíos técnicos para los fabricantes de esta aleación
Para el observador casual no hay nada extraordinario en el anuncio de Ford de que utilizará aluminio en lugar de acero para producir la carrocería de su camioneta pickup F-150 2015.
Al fin y al cabo se utilizan metales ligeros para fabricar componentes de automóviles desde hace décadas. Por ejemplo, Audi – en colaboración con Alcoa – comenzó a desarrollar el chasis de aluminio del A8 en 1982 y la producción en serie de dicho vehículo comenzó en 1994.
Adicionalmente, Jaguar Land Rover (JLR), actualmente en la vanguardia del desarrollo de aluminio para automóviles, utiliza extensivamente el aluminio en sus modelos XJ, F-Type y Range Rover. La marca empleará una arquitectura de aluminio completamente modular en su próximo sedán XE y gestiona el que es según ellos el mayor taller de carrocería de aluminio del mundo.
Sin embargo, esta oferta es siempre de automóviles de lujo con producciones anuales de decenas de miles. Pero el F-150 de Ford ha sido el coche de cualquier tipo más vendido en EEUU durante los últimos 32 años. Solo en EEUU se vendieron 760.000 camionetas pickup serie F en 2013.
El director de marketing de automoción en Alcoa, Randal Scheps, nos comenta: “Estamos al comienzo de un cambio histórico en la manera de fabricar coches. La fabricación de la carrocería completa en aluminio del Ford F-150 es solo la punta del iceberg”. La industria del aluminio predice que la demanda de este metal por parte de los fabricantes de coches se duplicará para 2025, debido a las exigencias de consumo de combustible tanto en EEUU como en la Unión Europea.
El presidente de la unidad de negocio de Embalaje y productos de automoción enrrollados, Laurent Musy, dice: “En los EEUU, las normas actualizadas sobre consumo medio de combustible corporativo (Corporate Average Fuel Economy, CAFÉ) se aplican ahora también a los camiones de servicio medianos y pesados, motivo por el que seguramente Ford ha decidido utilizar aluminio en su nueva camioneta pickup F-150. Los estándares de CAFÉ, que serán más estrictos a partir en 2016, también están empujando a los fabricantes de coches a reducir el peso de los vehículos de gran volumen”.
Constellium estima que el mercado estadounidense de productos de aluminio laminados a utilizar en carrocería en bruto (body-in-white, BIW) podría crecer desde las menos de 100.000 toneladas en 2012 a aproximadamente un millón de toneladas en 2020. En Europa, se espera que el mercado de BIW crezca un 12% al año hasta alcanzar las 600.000 toneladas en 2020. Scheps, de Alcoa, nos dice: “El principal cambio es la transición de capós de aluminio a puertas y carrocerías completas”.
Desarrollo de aleaciones
Los proveedores de aluminio y los fabricantes están trabajando a un ritmo vertiginoso en el desarrollo de aleaciones con el aumento de resistencia y maleabilidad necesaria en estas nuevas aplicaciones.
Las principales aleaciones utilizadas en las chapas de carrocería y carrocerías en bruto son de las series 5000 y 6000. Las aleaciones de la serie 5000 contienen magnesio y representan un 37% del peso de la carrocería del Range Rover de JLR. La serie 6000 son aleaciones con magnesio y silicio, son fáciles de mecanizar, se pueden endurecer por precipitación y se están utilizando cada vez más en aplicaciones automovilísticas. Representan otro 37% del peso de la carrocería del Range Rover (el restante de la carrocería es un 15% de fundiciones y un 6% de extrusiones con equilibrados de acero).
JLR utiliza aluminio anticorodal (AC) 600PX de Novelis para la producción del prensado de carrocería del Range Rover, la mayor placa de aluminio de una pieza para carrocería de la industria del automóvil. Se aplica un tratamiento anti-envejecimiento, por lo que la aleación mejora su resistencia cuando pasa por el taller de pintura donde se calienta a 180ºC, mayor resistencia que una aleación de la serie 5000. Además es más dúctil, lo que significa que se pueden producir piezas con una geometría más compleja.
La aleación AC300T61 de alta resistencia de Novelis se utiliza para producir la estructura de choque fundamental para la seguridad del Range Rover. La aleación demuestra una resistencia típica en servicio de entorno a 225 MPa, 85 MPa más que la aleación NG5754 predeterminada de JLR. En comparación con NG5754, AC300T61 absorbe un 30% más de energía por unidad de longitud, lo que permite su uso en gálibos más finos. Como resultado, JLR dice que puede hacer componentes un 20% más ligeros y un 9% más baratos que los producidos con NG5754. Las estructuras de asimilación de impacto podrían ser un área de gran crecimiento para el aluminio. El presidente de la unidad de negocio industrial y estructuras de automóvil de Constellium, Paul Warton, dice: “Los analistas prevén que el aluminio representará el 30% del mercado de estructuras de asimilación de impactos en la UE y el 20% en EEUU para 2018.”
Aluminio de alta resistencia
En febrero de 2014, Constellium anunció el lanzamiento de una tecnología de asimilación de impactos con aluminio de alta resistencia diseñado para su aplicación tanto en el frontal como la parte trasera del vehículo. Según la empresa, sus sistemas de asimilación de impacto demuestran una gran resistencia y propiedades físicas similares a las aleaciones de aluminio de la serie 6000, incluida la maleabilidad, la resistencia a la corrosión y la absorción de energía.
Los productores de aluminio y los fabricantes de coches que utilizan este material están también reduciendo las emisiones de carbono dióxido relacionadas con la producción de componentes de aluminio. Con este fin, JLR ha desarrollado RC5754, que contiene un 50% por peso de materiales reciclados de sus procesos internos. RC5754 se convertirá en la calidad predeterminada en todos los vehículos futuros de JLR, incluido el XE, y remplazará a la calidad NG5754. Adicionalmente, la empresa planea introducir esta aleación reciclada de forma retroactiva en sus modelos actuales.
La demanda de aleaciones fundidas de la industria del automóvil evoluciona de manera similar. La empresa JVM de fundiciones con base en el Reino Unido realiza componentes fundidos para JLR, Ford y BMW. El director de diseño del grupo Simon Ruffle, comenta: “Los componentes fundidos deben ser cada vez más finos, ligeros, resistentes y deben tener una mayor integración de sus características”. JVM lleva más de 50 años produciendo piezas para JLR, comenzó produciendo pilares B para el modelo XK de Jaguar mediante una combinación de postes B y fundiciones de cuello de cisne.
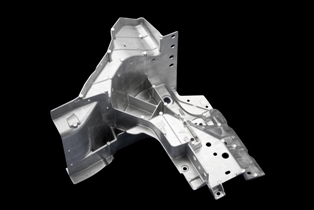
Cuando Jaguar anunció sus planes para fabricar el modelo F-Type en 2010, encargó al equipo de JVM el rediseño de la estructura del pilar B como un único molde que evitaría el ensamblado. “Nuestros diseñadores se enfrentaban al desafío de crear un sistema de suministro y canal que pudiera crear con éxito dos fundiciones diferentes al mismo tiempo. Nuestro diseño final redujo el peso total del ensamblado en más del 50% y eliminó los costes y peso de siete prensados de acero, así como el coste de ensamblado. Nuestro nuevo pilar B solo requiere un juego de matrices en comparación a las dos matrices y siete herramientas de troquelado”.
Fundición de grandes componentes
JVM está trabajando en la actualidad en varios proyectos de investigación, cuyos resultados podrían ayudar a cumplir con las demandas de la industria del automóvil. Por ejemplo, se ha asociado con JLR y Aeromet International con sede en Worcester, para diseñar métodos para la fundición casting de grandes componentes fabricados con una aleación de alta resistencia denominada A20X. A20X ha sido desarrollada por Aeromet, una versión modificada de la aleación aluminio/cobre A201. Demuestra un límite elástico de hasta 440Mpa, una fuerza tensora de 500Mpa (lo que la convierte en la aleación de fundición más resistente disponible) y un alargamiento del 3–5%. Según Aeromet, la aleación A20X elimina los problemas asociados con la limitada capacidad de fundición de las aleaciones de aluminio/cobre, y sin embargo cuenta con una fluidez comparable a las aleaciones de aluminio/silicio como A357.
A medida que aumenta el uso de estructuras de carrocería de aluminio, se tendrán que desarrollar y mejorar los métodos de unión y ensamblado. Los métodos de unión adhesiva son cada vez más populares, pero una característica intrínseca y beneficiosa del aluminio, el hecho de que se forma una fina capa de óxido de aluminio en su superficie con el contacto al aire y que aumenta la resistencia a la corrosión, puede perjudicar a la calidad de estas uniones, lo que significa que debe someterse el metal a un tratamiento previo.
Alcoa asegura haber desarrollado un tratamiento previo, denominado Alcoa 951, que aumenta la duración de las uniones adhesivas hasta nueve veces cuando se compara con sistemas de revestimiento de conversión como el titanio circonio. El tratamiento no incluye metales pesados que podrían ser perjudiciales para el medio ambiente y se aplica mediante inmersión o rociado. Alcoa dice que el tratamiento 951 es esencialmente ‘transparente’ para los siguientes pasos en el proceso de fabricación del vehículo, como el moldeado, formado, soldadura por puntos de resistencia y pintura. La empresa ha otorgado la licencia del producto a Chemetall para su distribución global.
Parece que el aluminio podría convertirse en el material elegido por los fabricantes de coches que buscan reducir el peso de sus vehículos, pero, ¿qué desafíos debe superar para convertirse en un auténtico material para mercados de masas? El mayor coste del metal en comparación con el acero es probablemente un problema. Ruffle dice: “Sin embargo, cuando se tiene en cuenta el coste total, sumando factores como capacidad de reciclaje y polución, entonces el uso de aluminio en el sector del automóvil es cada vez más competitivo”.
Scheps es más optimista. Considera que el mayor reto de Alcoa es tener una capacidad de producción suficiente para cumplir con el aumento de la demanda de sus productos por parte de los fabricantes de coches. En enero de 2014, completó una expansión de 300 millones de dólares de su instalación de láminas de aluminio en Iowa y en agosto de 2013 realizó una expansión de 275 millones de dólares en sus operaciones automovilísticas en Tennessee. En los últimos doce meses Novelis y Constellium han invertido millones de dólares en la producción de aluminio para aplicaciones automovilísticas.
Musy de Constellium comenta: “Creemos que hay una gran oportunidad para el aluminio avanzado en el mercado del automóvil, tanto a corto como largo plazo y hemos realizado inversiones notables para maximizar esta oportunidad”.