Manufacturers can make significant cost and energy savings by building-in efficiencies at plant design stage. And if there is a single automotive manufacturing plant anywhere in the world that can claim to be setting the current benchmark for environmental and energy efficiency, it is very likely the new Volkswagen facility in Chattanooga in the US state of Tennessee.
The plant, which formally opened less than a year ago, in May 2011, employs 2,500 people in the manufacture of the North American version of VW’s Passat vehicle, with a total production capacity of 150,000 per year. Just last December, the plant was awarded Platinum status under the Leadership in Energy and Environmental Design (LEED) building certification programme run by the US Green Building Council (USGBC) – thus becoming the first – and, so far, only – automotive manufacturing plant in the world to achieve that status. Without indulging in any hyperbole, Volkswagen is confident in its own estimation of the facility’s genuinely high environmental performance: “Yes, we are confident it represents the state of the art,” says Dr Jan Spies, head of global construction for Volkswagen. According to Dr Spies, who works out of the company’s headquarters in Wolfsburg, Germany, the plant itself is the culmination of around 30 months of planning and construction with a total project cost of some $1 billion (€753 million). The environmental and energy efficiency of the plant is not coincidental – it was, he confirms, designed in right from the start of the project. Moreover the plant represents a deliberate attempt to raise the bar as far as the environmental and energy efficiency of the company’s manufacturing facilities are concerned. “We have a set of standards on which we base all our building designs, but this plant also introduces some innovations,” confirms Dr Spies. “The concept for the basic layout, for instance, is completely new.”
Efficiency of function as well as form
As Dr Spies indicates, the objective of environmental and energy efficiency has been pursued in more than just the use of materials and the deployment of particular technologies. The layout of the plant, for instance, emphasises compactness in order both to reduce the “footprint” of the facility and to minimise internal travel for parts and assemblies. “The body and assembly areas are wall-to-wall with each other,” he confirms. “In addition the paint shop is within a hundred metres of the body shop.”
Proximity is an issue which crops up again when he describes a quite conscious policy of centralising operations as much as possible. “The people who run the process are right in the middle,” Dr Spies notes. “All the checkpoints are within a radius of a hundred metres of each other.” A glance at a floorplan shows the assembly and body shops, for instance, do not follow on from each other in sequence but are slightly offset so that about a quarter of their respective lengths are contiguous and overlapping. The paint shop is then, as far as possible, within the angle between them and several other key checkpoints – including those for driving test and water test – are neatly placed in the narrow gap between those three major production areas. Possibly this layout is, in part, a response to the particular challenge set by the topography of the site, which is in what Dr Spies describes as a “valley” rather than on the sort of flat plain that, he concedes, provides the ideal location for a car manufacturing plant. A lot of earth had to be moved, he observes, to make the location suitable and even now an interesting fact that illustrates the somewhat unusual nature of the site is that the employee entrance to the production building is 16 metres above the shopfloor level. But – and this is a point on which Dr Spies is quite emphatic – local climate and geography can never be absolute determining factors in determining the location of a new production facility. “We are in the business of making cars,” he states, “and, as such, relevant decision-making is market driven.
Natural selection
In reality, therefore, car plants will get built where they can best satisfy a demand and whatever problems the sites presentwill just have to be surmounted. For example, Dr Spies says, sites in Russia may well involve dealing with extreme cold and in India with dry and rocky conditions. Yet VW’s immediately preceding projects have been for car plants in those two countries – Kaluga and Pune, respectively. Meanwhile in Mexico, where VW is currently constructing a new engine plant in Silao, that other essential requirement for a car plant – water – can usually only be obtained by drilling into the ground.
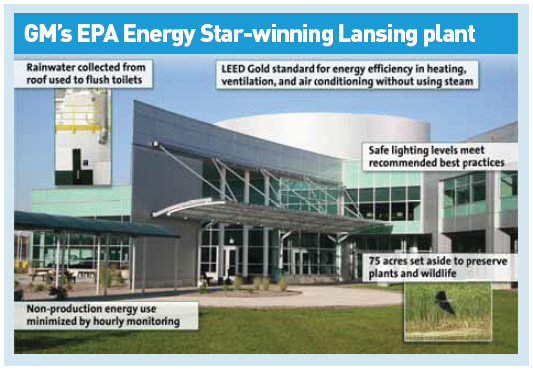
In the case of Chattanooga the availability of water is not itself a problem, but in line with the company’s policy to make the plant an exemplar of current best practice, rainwater collection and storage is strict policy. The technique in itself is fairly routine but at Chattanooga this entirely free and renewable source is still used sparingly to ensure usage is as efficient as possible At the most basic level, low-flow fixtures are used in all the restroom blocks in addition to localised water storage. Stored rainwater is used wherever possible as a substitute for mains water supply in production-related cooling operations.
Where there is some real technical innovation, though, is in the paint shop where the process in place obviates Moreover the LED lighting used in all external locations also minimises light pollution as well as being energy-saving. Dr Spies indicates this is one of the more experimental aspects of the whole project and that in the event it has proven a great success. “It is much better than we expected,” he says, adding that it is even used to illuminate the company logo that identifies the complex to outsiders.
Inside innovation
The internal environment is managed in a manner intended to minimise energy usage – perhaps more of a challenge in the US than in other parts of the world, Dr Spies observes, simply because of the higher comfort levels generally expected by the workforce, not least for icy cold and therefore energy-intensive air conditioning levels. Several tactics are employed. The reflective roof membrane – which is made from a PVC-free material - is, quite literally the most visible aspect, but is not the only way in which light colouring has been used to counter the absorption of solar energy. The naturally dark hued asphalt in the driveways and parking lots in exterior areas have actually been painted in a similar tone, says Dr Spies, though in this case the immediate advantage is to avert the heating of ground water.
As far as air conditioning is concerned, VW avoids the usual expenditure of energy by not actually providing it – or at least not to the degree that might once have been the case. The working areas are not air conditioned in the conventional sense at all, explains Dr Spies. Instead there is what he terms “cold ventilation”, with cooled air fed into the working areas in a manner that ensures that the temperature in the first four metres above floor level – the space in which people are actually located – is suitably modified, while no attempt is made to alter the volume above that. “We are not changing all the air in the plant,” states Dr Spies emphatically, adding that in the context of a workforce that knows that the plant is striving to achieve extreme energy efficiency, the extra few degrees of temperature that a thermometer might show are simply “not a problem”.
Nevertheless the target working temperature is not quite as low as it might be. Instead of cooling air down to the 16-17°C as would be the norm, explains Dr Spies, the working environment at Chattanooga is more likely to be in the range 20-22°C and might even on a very hot day be allowed to creep up to something like 24-25°C. The policy still provides for perfectly acceptable working conditions. Meanwhile internal lighting also achieves high levels of energy efficiency even though brightness requirements to ensure safe working preclude the use of the LED technology used externally. Dr Spies says that the plant makes use of the T5 system from Schneider Electric and achieves an appropriate illumination level with an energy expenditure of “less than 4W per square metre” of floorspace. Procedure also plays a part in achieving the relevant energy savings. Dr Spies explains that lighting in the factory itself is managed on a strict “zonal” basis, so that it can be switched on or off according to requirements in particular areas without affecting work elsewhere. “It is not a question of switching the whole factory on or off,” he states.
Setting standards
While the Chattanooga plant currently represents the leading edge of what VW can achieve in terms of overall plant efficiency, Dr Spies is adamant that it is setting a standard that will stand for some time. “This is the blueprint for what will follow,” he says. “Standing still is simply not an option.”
But Volkswagen is not the only car maker in the US to claim external recognition for its energy efficiency. In October last year the Lansing Delta Township (LDT), Michigan, assembly plant of the newly restructured GM organisation became the first automotive plant in the country to receive Energy Star certification from the US Environmental Protection Agency (EPA). The award officially puts the operation – which builds the Buick Enclave, GMC Arcadia and Chevrolet Traverse – in the top 25% of similar facilities across the country.
The plant is the newest GM production site in the country and received the LEED Gold Standard for energy efficiency in heating, ventilation and air conditioning when it opened in 2006. At that point it was, says GM, the largest and most complex manufacturing site to receive any form of LEED certification.
As the company presses on into the second decade of the 21st century, much of the responsibility for ensuring that it
remains at the forefront of energy efficiency – not just in the US but worldwide – falls on energy manager Al Hildreth. “We want energy management to be integrated into the business,” says Hildreth, adding that while he has counterparts in Europe, Asia and South America with similar regional responsibilities to those he exercises in North America he also has a global coordination role. The latter, Hildreth explains, is based on continuous reporting and monitoring of energy performance at individual plants. Doing so is very much a matter of organisation and procedure rather than of significant capital investment. By definition, he points out, any PLC (programmable logic controller) gathering data from a shopfloor machine or process to transmit to a local network management system provides a means of gathering relevant energy-related data – temperatures or opening and closing of valves, for instance. More prosaically, though, the whole process starts, pretty much as a purely domestic energy efficiency drive might, with “good meter data”. By collating such information centrally through what he describes as an “energy dashboard” approach, Hildreth indicates that the central team in the US is able to provide individual plant managements with an assessment of their performance. As such, he notes, a lot of the reporting is “us to them” and not the other way round. He estimates that the company saves around $3 million (€2.25 million) a year at a global level by this means.
Hildreth also makes the point that while upgrades to existing plants and processes are always possible, the key opportunities for major shifts in efficiency levels occur when new facilities – whether whole plants or particular operational areas within a plant – are planned. “Energy efficiency is built in at the design stage,” he states. “That is where our strategic efforts are focussed.”
Process of change
Details of the Lansing plant make the point and as Hildreth describes its features it becomes evident that some techniques – such as the use of a light, coloured, reflective roof covering – are precursors to those employed elsewhere, for instance at VW Chattanooga. Another is the deployment of clever air-cooling and distribution techniques, which Hildreth describes as “air tempering” rather than air conditioning. Some air from the main plant area is “cascaded” into the paint shop – a space that is usually strictly segregated from other production areas. Hildreth also highlights the fact that there is no use of steam to heat the building. Instead “direct fired gas and direct hot water” are employed.
In fact Lansing has acted as a trailblazer for the company. Within a couple weeks of the announcement of the EPA award GM revealed that 30 of its North American plants had succeeded in cutting “energy intensity” by an average of 25%, thereby saving the company a total of $50 million (€37.6 million). Detailed information has not yet been released but GM’s official statement highlights benchmarking energy use through energy management systems, automating shut-down of equipment and upgrading to energy-efficient lighting and more-efficient heating and cooling systems. For the future, Hildreth indicates that “processes” will now come under increasingly intense scrutiny. One he pinpoints is the melting of aluminium. At present the standard technique is gas reverbatory melting but Hildreth says GM has carried out some pilot testing of more efficient isothermal procedures, though he stresses that in this context efficiency is defined to include and reflect material losses as well as energy consumption.
Plant comes clean
Meanwhile, on the other side of the Atlantic, a manufacturing plant that this year marks its 20th anniversary as a production site has recently taken a further step in the drive for energy efficiency that has marked all of its two decades of operation so far. This is the Burnaston, UK, plant of Japanese multi-national Toyota, the production site for the Avensis, Auris and Auris Hybrid vehicles and one of five sites worldwide that is designated as a flagship Eco Factory’by the company.
Though process optimisation is very much the basis of the company’s approach to all matters of energy efficiency, the middle of last year saw the commissioning at Burnaston of a major capital project to support the on-site generation of “clean” electricity. This a huge solar power installation comprising some 16,800 photovoltaic (PV) panels located within the perimeter of the factory on a previously unused patch of ground measuring 330x320 metres.
Over the course of a year the installation, which cost £11.4 million (€13.5 million), can generate around 5% of the total energy requirements of the whole plant. Moreover the main array is supplemented by four smaller PV installations much closer to the main production site – indeed in some cases actually integrated into the building structure. Toyota’s decision to embark on large scale PV exploitation is explained by deputy managing director Tony Walker, who says the company had been investigating the possibilities of on-site renewable energy generation for some time – it had previously sought planning permission for a biomass incinerator but was refused on the grounds of opposition by local residents concerned about visual blight. In contrast the main PV installation, despite its horizontal dimensions, is completely invisible from outside the site boundaries. “You can’t see it from anywhere unless you go up in a plane,” confirms Walker.
Another interesting attribute of the installation is its financing – it has not actually cost Toyota anything at all. Instead, the car maker has formed a partnership with UK energy supplier British Gas in which the latter has put up the cash in return for a 25-year lease on the site for a peppercorn rent. British Gas actually gets the return on its investment through a “feed-in” tariff scheme under which it is paid a preferential rate from public sources for the “clean” energy involved to allow for the fact that an equivalent amount has not been drawn from the UK’s national electricity grid. In reality, though, all the electricity actually generated by the installation is used by Toyota. Enabling that to happen requires some further hardware – the electricity has to go through DC to AC conversion and voltage step-up from 400 to 11,000 volts before entering the site’s network, but those are essentially automated processes. The important thing, confirmed by Dave Chapman, assistant general manager for facilities and environment, is that over the first half-year of its operation the installation has proven robust and reliable. According to Chapman, output from the main installation has varied from a low of around 1MW in poor weather conditions to a high of as much as 4MW in bright sunshine. But, he says, providing there is daylight then there will always be some output. “It still works even when it is raining,” he states, adding that by the middle of January this year, total output from the installation amounted to around 1.5GWh. Total annual output is expected to in the region of 4.6GWh, which Toyota estimates should be enough to support the manufacture of 7,000 Auris hybrid vehicles as well as saving around 2,000 tonnes of CO2 emissions over the same period.
Being seen to be green
Walker describes the move into on-site renewable energy generation as a natural progression from the Japanese ethos of continuous improvement that has ensured a series of major reductions in energy and material usage per vehicle manufactured since the factory opened – for instance energy over 65%, general waste again over 65% and water over 69%. But, in a sense, the literal physical concealment of the main installation runs counter to the spirit of the “kaizen” approach, which is not just about doing things but about being seen to do things, hence helping foster wider supporting attitudes and enthusiasm.
As such, and this is a point on which Walker is quite explicit, the other PV installations on the site are as much about advertising the company’s commitment to green energy as they are about actually generating electric power. “We want to be a showcase for the technology,” he states. “The intention is that people should notice the fact.” Needless to say this venture into hardware rather than procedure is not regarded by the company as marking any sort of shift in priorities. Both Walker and Chapman are absolutely emphatic in their rejection of the notion that the company has reached any sort of limit to what can be gleaned from traditional continuous improvement techniques.
Instead it is just an element in a broader “sustainability strategy” that the company is pursuing which seeks to increase the awareness of employees to relevant concerns – even when they are at home. A system of “green” and “silver” cards – completed by, respectively, 98% and 50% of the site’s employees – for instance, encourages them to consider the energy efficiency of such matters as their means of travel to work and their domestic appliances. As Walker explains, a workforce with that cast of mind naturally becomes one that is appropriately efficient in its working practices: “That understanding becomes an input to the achievement of our objectives.”