A Porsche investiu €500 milhões para construir uma oficina dedicada de pintura para o SUV
'Made in Germany' foi assim por muito tempo considerado como um marco de qualidade na fabricação de automóveis que o uso dessa marca possui, por vezes, se estendia a credibilidade, confiando mais no emblema que qualquer outra coisa. Mas 'Made in Germany' será uma reivindicação justa para novo Macan SUV da Porsche, após um investimento de €500 milhões pela montadora prêmio para estabelecer uma oficina de 35.000 m² e uma de pintura de 60.000m² na sua fábrica de Leipzig. Inaugurada em fevereiro, após um período de construção de dois anos, estas instalações permitirão que a Porsche produza o novo Macan sem transporte de carrocerias de outros lugares. Somente as prensagens virão de fornecedores externos - e da Volkswagen - uma vez que não há oficina de prensa em Leipzig; as transmissões darão origem a partir Audi, VW e Porsche locais.
Porsche Leipzig, criada em 2002, já reúne o Cayenne e o Panamera, mas as carrocerias para estes primeiros são atualmente enviadas a partir de uma fábrica da VW em Bratislava, Eslováquia. As carrocerias Panamera são feitas na Alemanha VW Hanover; no entanto, a partir de 2016 este modelo também será levado para Leipzig, depois que a Porsche tiver concluído a construção de uma outra oficina - esta medindo 70.000 m².
Tendo duas vezes o tamanho da nova oficina Macan, esta instalação planejada gerou especulações de que a Porsche também trará a produção do Cayenne inteiramente para Leipzig, embora o fabricante não possa confirmá-lo. Em declarações à AMS, o diretor de tecnologia e montagem Martin Kahmeyer diria apenas que a maior oficina Panamera será capaz de acomodar tecnologias de alumínio e que, ao contrário da oficina Macan-específica, fornecerá mais flexibilidade para integrar as novas "ideias".
Certamente, um dos motivos pelos quais a Porsche selecionou Leipzig como o local de produção para o novo Macan foi a facilidade de expansão. A principal fábrica, em Stuttgart já produz o Boxster e 911, enquanto em Ingolstadt, que também faz o Audi Q5, foi sentida a falta de capacidade para adicionar o Macan, bem como as operações altamente automatizadas que faria a integração de um modelo adicional mais difícil. Além disso, ao trazer o novo Macan para Leipzig, a Porsche está unindo seus carros com motor dianteiro.
Com a ambição de produzir 50.000 novos Macans a cada ano, a Porsche está incrementando o volume, iniciando com cinco unidades por dia, no final de 2013. Em linha com um aumento semanal de volume, Leipzig está agora construindo de 210 a 250 por dia e isso aumentará para 300 a 330 até meados do ano.
Norbert Wagner, chefe da oficina do Macan, descreve com franqueza o seu novo domínio como "muito normal", que se baseia em um princípio do tipo "fishbone", com percursos angulares e alimentação na linha principal, localizada no centro. No entanto, ele diz que a Porsche ampliou a oficina com uma plataforma inteira por causa do capô de alumínio envolvente do Macan, que requer um forno para curar os adesivos e coligar suas folhas internas e externas. O painel externo para este componente é feito em Bratislava, mas cuidadosamente reformulado em Leipzig para satisfazer suas necessidades especiais de design. Demonstrando que nenhuma quantidade de esforço é demais na fabricação de ponta, a sua explicação é simples: "o cliente gosta".
Radical, pode não ser, mas a nova oficina da Porsche é certamente moderna e de alta tecnologia, com os mais modernos sistemas de produção e construída de acordo com os princípios da sustentabilidade. Assim como a nova oficina de pintura e sala de montagem, ela usa um sistema de controle de qualidade sem papel, que pode ser usado para falhas, como pregos ou ajustes para fechamentos. No que diz respeito a sustentabilidade, um sistema fotovoltaico foi instalado no telhado para gerar 800 mil kWh por ano. Há também um novo sistema de refrigeração para as pistolas robóticas, reduzindo o consumo anual de energia em mais de 365 mil kWh.
Na ocasião que a AMS visitou a fábrica em abril, os construtores de linha ainda estavam fazendo adições finais para a oficina, por exemplo, adicionando sistemas de exaustão para remover os gases adesivos.A instalação em sua primeira semana executava três turnos por dia, que Wagner descreveu como "um grande passo para todos os membros da equipe". De fato, enquanto o processo de construção pode ter sido, em grande medida convencional, o aspecto humano da introdução do novo Macan em Leipzig era uma tarefa considerável.
A contratação de empregados, diz Wagner, foi "um dos maiores desafios" e exigiu o recrutamento de cerca de 500 pessoas apenas para a oficina de carroceria; a força de trabalho total em Leipzig cresceu de 950 para 2.500. Consequentemente, a Porsche gastou muito tempo e dinheiro em treinamento. Além de academias externas que operavam em colaboração com a VW, a Porsche instalou áreas especiais para a aprendizagem "no local de trabalho", não só na oficina de pintura, mas na montagem. De acordo com Kahmeyer, parte deste método de treinamento será agora transferida para Stuttgart.
Rumo ao sul
A oficina é organizada ao longo de uma orientação norte-sul, e é alimentada por um novo centro de abastecimento de 10.000 m² para chapa de aço, além de alumínio para o capô e porta traseira. Peças chegam de fornecedores de acordo com os ciclos específicos, um conceito de logística que permite o rápido giro dos produtos prensados (sendo que 400 destes são necessários para o Macan). No centro de abastecimento, eles são registrados eletronicamente antes de serem entregue para a oficina por trens tugger.
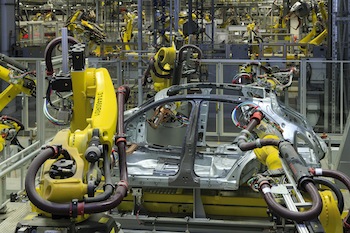
Há cerca de 6.000 soldaduras por Macan, sendo que a soldadura a laser é usada para as paredes laterais e o telhado para evitar qualquer junta visível. As soldas são completadas por 387 robôs Kuka, mas as peças são verificadas diariamente quanto a qualidade em um processo de ultrassom manual; de acordo com Wagner, componentes anteriormente tinham que ser destruídos durante os testes.
Enquanto a parte inferior da carroceria e superestrutura estão sendo feitas, as portas, tampa do porta malas, para-lamas dianteiros e capô especial são fabricados paralelamente, prontos para a integração na carroceria na linha de adicionamento de peças. As portas e capô são montados em um processo totalmente automatizado, devido às dimensões de lacuna apertadas e às transições entre as superfícies; a tampa do porta malas e os para-lamas são adicionados com alguma ajuda do pessoal. Várias vezes ao dia, esses componentes são retirados da linha para verificação de qualidade, por exemplo, para medir lacunas.
No final, as peças adicionadas são afinadas e todas as superfícies verificadas em termos de qualidade. As carrocerias completas são medidas na estação por uma equipe de quatro robôs Kuka com câmera e à laser. Aqui, um posto de calibração de temperatura ajuda os robôs a explicar as flutuações sazonais e assegurar a coerência de medição. Se um problema de qualidade é detectado, os carros podem ser movidos para fora da linha para uma área de retrabalho.
Duas vezes ao dia, uma carroceria é selecionada para uma auditoria completa em uma sala especialmente iluminada. Sob condições análogas à iluminação da oficina de pintura - "melhor do que a luz do dia", diz Wagner - dois trabalhadores usando luvas brancas inspecionam ao longo da carroceria, verificando manualmente se há defeitos. Assim, fora desta área, há também uma carroceria negra, que é usada para demonstrar áreas de melhoria. A coloração escura destaca defeitos mais claramente, e estes são marcados com pontos coloridos indicando a origem da falha (vermelho para as peças prensadas, verde para oficina de carroceria e amarelo para oficina de pintura), além de cartas de classificação de gravidade. Wagner reúne sua equipe semanalmente para discutir questões de qualidade e organizar qualquer formação adicional que for considerada necessária.
Se tudo correr bem, as carrocerias do Macan são transportadas por elevador e através de uma pequena ponte para a oficina de pintura. Existem 100 ciclos na nova oficina de carroceria, com um tempo de ciclo de 154 segundos por estação; na tarde na qual AMS visitou a fábrica, 111 carros já haviam sido produzidos, sendo que a meta diária era 54, mas Wagner disse que isso era para compensar 100 veículos "perdidos" por um problema técnico no dia anterior.
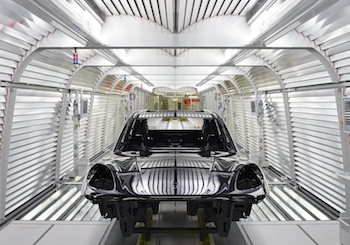
A oficina de pintura foi desenvolvida ao longo das linhas da fábrica de Stuttgart, em colaboração com Dürr. De acordo com Marcel Förster, um planejador na oficina de pintura, o objetivo é pintar 30 carrocerias por hora, embora esta taxa dependa necessariamente da saída da oficina, que atualmente está se tornando mais veloz. De acordo com Wagner, uma carroceria é feita a cada três minutos; acrescentando que, enquanto a oficina de pintura poderia processar 300 veículos por dia, seria difícil para a oficina de carroceria produzir 200. No entanto, ele diz que a Porsche alimentará a oficina de pintura, com mais oficinas de carroceria no futuro.
Na "entrada da oficina de pintura" fase no Nível 1, as novas carrocerias do Macan passam por duas estações nas quais as dobradiças das portas, tampa do motor e tampa do porta malas são firmemente fixadas. Eles também são transferidos de plataformas deslizantes da oficina de carroceria para plataformas deslizantes KTL (KTL significa 'Kathodische Tauchlackieurung', ou "imersão catódica").
As carrocerias, em seguida são submetidas a um pré tratamento em um tanque de imersão aquecido a 60° C, a fim de remover a gordura das prensas, pó e outros contaminantes de soldadura. A fase de fosfatização de zinco é implantada para assegurar a aderência ideal para um revestimento de proteção anticorrosiva; as carrocerias são mergulhadas e giradas a 360°, de modo que todas as cavidades sejam inundadas.
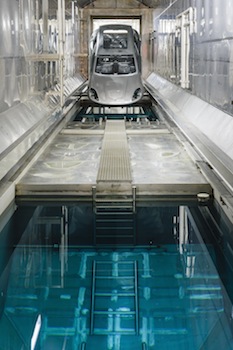
Depois de viajar por 280m durante a fase inicial, as carrocerias voltam para a linha de 360m da fase 3 para a secagem. O primeiro dos quatro secadores, é o secador de revestimento por imersão catódica, o qual atinge um pico de temperatura de 185° C. As carrocerias são, então, armazenadas em uma área isolada com capacidade para 80 unidades, onde são classificadas pela cor que deverão receber.
O quarto estágio envolve a selagem automática das costuras e das flanges, e a aplicação da proteção inferior com materiais de PVC especiais. Aqui, a carroceria é colocada em um hangar, antes de ser devolvida para uma unidade deslizante para o revestimento superior primário.
No estágio cinco, o enchimento ou revestimento primário, camada de base e camada clara ou superior, são roboticamente aplicadas utilizando carga de tinta eletrostática. Embora a oficina de pintura tenha 81 robôs, a primeira estação é uma oficina na qual os trabalhadores de limpeza limpam as carrocerias manualmente com panos, gastando cerca de seis minutos por veículo e com foco em áreas específicas, tais como as portas. As carrocerias progridem através de um portão de ar que sopra as partículas restantes antes de chegar à primeira estação de robô, onde os robôs Dürr com cabeças de escova saturadas, limpam-nas completamente. Nas próximas estações, pequenos robôs de gancho abrem as portas, capô e porta malas antes das unidades maiores, com pulverizadores para realizar o revestimento.
O material de enchimento, corresponde à cor de acabamento final, e é aplicado a uma espessura de 30-35μm; a camada de base é de 12 18μm de espessura, e a de revestimento claro é de 40-45μm. As fases de secagem são nas temperaturas respectivas: 160°, 80° e 140° acompanhando cada aplicação, os últimas levam 45 minutos.
Finalmente, as carrocerias alcançam os dois túneis de luz Wenker que são usados para verificar a qualidade do acabamento. As carrocerias são divididas em duas linhas, a primeira é verificada em um túnel, a segunda em outro túnel no qual a luz é refletida em uma direção diferente. Uma combinação de LEDs e espelhos ajustáveis é usada para simular a luz forte do dia, permitindo que os trabalhadores detectem até mesmo pequenas imperfeições na superfície, as quais são lixadas e polidas.
Depois de passar 15 horas na oficina de pintura, cada carroceria terminada segue para uma estação de medição em linha para ser verificada, antes de ir para a sala de montagem de 21.600 m². O novo Macan exigiu a integração de um terceiro modelo para as operações de montagem existentes para o Cayenne e o Panamera, incluindo uma transição para três turnos e despesas de €40 milhões em novos equipamentos; além da criação de uma nova oficina de pintura. Mas fazer jus a descrição 'Made in Germany', certamente valeu a pena.