Two innovative metal forming techniques could have a significant impact on the press shop of the future
The beginning of the second quarter of 2018 saw the start of a new era for Ford in its application of metal forming technologies. The company started production of hot-stamped metal parts in boron steel for the latest version of its Focus on a new fully automated installation at its Saarlouis plant. Located on the very western fringe of Germany, it is described as ‘unique’ within Ford’s production network.
That claim is verified by Torsten Hallfeldt, stamping engineering launch leader, who is based in Cologne and oversaw the project to commission the new installation. He says the installation comprises two separate lines side-by-side, sharing six dies that are used to produce 11 parts for the underbody area of the vehicle’s safety cage. This is a figure that represents precisely a quarter of the total number of components required, with the other 33 delivered from external suppliers.
The number of dies is set to double during the course of 2019 as other vehicle programmes are added to the installation’s output. Hallfeldt also confirms that Ford has very quickly achieved its initial time ‘per hit’ target of 12 seconds, and is now set on shaving perhaps another couple of seconds more off that. As the end of 2018 approached, the installation was operating at around “three thousand hits per day per line – six thousand in total”.
Perhaps the key feature of the installation – certainly one that is completely new to Ford operations anywhere in the world – is its use of Pressure Controlled Hardening (PCH) technology from equipment supplier Schuler. Indeed, Hallfeldt says the ability PCH provides, to compress the in-die cooling sequence to just three seconds, is the major factor in the overall in-die cycle reduction time.
The other notable ‘first’ that the installation achieves is in its level of automation. Hallfeldt confirms that all operations “from the loading of the blanks to the stacking of the completed parts” are completely automated. He believes that intensity of automation in a forming line is unprecedented not just for Ford but, at the moment, for the wider automotive industry, at least where the material involved is boron steel.
Hallfeldt describes PCH as a “hydraulic technology that operates from the bottom up” in the die. As he explains, the part itself is formed conventionally by the downward force of the die’s upper half. But then cooling is affected by a succeeding process in which the lower half of the die is forced upwards against the workpiece, enabling heat to be conducted away from it very rapidly so that its temperature drops from the roughly 800°C at which it was formed to just under 200°C in about three to five seconds. When the blanks leave the furnace they are at a temperature of around 930°C.
The direct pressure affected by of the lower half of the die is, Hallfeldt says, in the range of 12-15MPa per square metre. This extremely high pressure is critical to the cooling performance; “the higher the pressure the better cooling” he states.
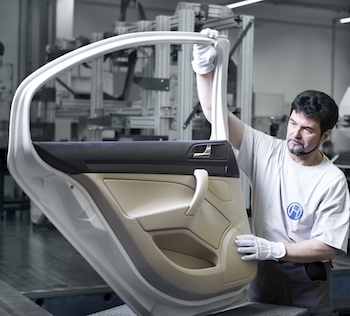
But, crucially, the lower half of the die is segmented so that different areas of the formed workpiece can be subjected to uniform levels of pressure, irrespective of their varying geometry, to help ensure uniform cooling and hence consistent strength in the finished part. Hallfeldt says the technique provides the necessary flexibility by allowing the simultaneous use of different levels of hydraulic force to push individual segments of the lower die against the workpiece. He adds that the use of three different force levels might be typical for the manufacturing of a small part with that number rising to four or five for larger components. The other key enabling factor is that the lower half of the die is cooled by a water-based fluid flowing through a series of channels cut into it.
Tricky positioning
Another unusual feature of the installation is the way in which the two lines are located relative to each other. Though they run in parallel, the two lines are not identical in their configuration. Instead they are “mirrored” so that certain physical features, most importantly in this case the furnaces, are on opposites sides, quite literally as if one line was a reflection of the other. Each line, Hallfeldt explains, is L-shaped with furnaces closer to the outer walls and the press lines closer together in the centre of the building. The simple reason for this is space constraint in the new building that was specially constructed to house the lines and, as he also notes, the subsequent laser cutting equipment made necessary by the hardness of the boron steel material.
But though the furnaces can be positioned in this way, what Hallfeldt describes as the “connection points” for the press equipment itself cannot. A particular challenge this poses, he continues, is that of ensuring ease of transfer of tooling from one line to the other when necessary. He admits that this “took a lot of thinking and designing.” As he further explains, “you have to work out which dies can be just moved from one line to the other and which need to be turned around.”
The blanks are also preformed, so the way they are oriented when fed into a furnace has to be taken into account because the overall layout means that the route from furnace to press equipment negotiates a right-hand turn in one case and a left-hand turn in the other.
Meanwhile, a further aspect of the whole installation that Hallfeldt is keen to pinpoint involves the laser cutting that follows the forming process. This is, he says, a cost-intensive procedure that Ford has sought to minimise as much as possible. In the case of four of the parts made on the new hot-forming line at Saarlouis, it has done so by the simple expedient of obviating any need for laser cutting at all. “They have no holes and no trim and can go straight from the press line to the bodyshop,” he confirms. “That is made possible by a combination of part design, tolerances from the bodyshop and the accuracy of the press tooling.”
In fact, when he reviews the operation of the installation from start-up through to full production, Hallfeldt says Ford is “fully satisfied” with what has been achieved. It has, he claims, “passed all major milestones” with only a few minor glitches of the sort that might be expected with the initial operation of any complex manufacturing process.
The experience gained has been passed on to the US where Ford is planning to start production operations in the early part of 2019 involving three press lines using identical forming technology at its Woodhaven Stamping Plant in Michigan. Nevertheless, Hallfeldt does add that those US lines will not have the same level of automation as their German counterpart, and hence for the moment the Saarlouis installation remains unique within the company even at a global level.
From aero to auto
One of the most flexible forming processes in the automotive industry, in the most literal sense of the term, is the Flexform technology from Swedish company Quintus Technologies, based in Västerås, around 100km west of the capital Stockholm. Instead of shaping sheet metal between two heavy machined steel dies, only one such hard die surface is employed with the other being replaced by a rubber diaphragm, which is then forced against the surface of the blank by hydraulic pressure.
The technique is not in itself particularly new – the company has been offering it for around 20 years – but according to head of business development for metal forming, Sture Olsson, what was at first primarily a focus on aerospace applications has more recently started to broaden out to include the automotive industry.
“The automotive sector is becoming increasingly important to us,” he confirms, adding that an initial take-up of the technology predominantly by OEMs is now being followed by increasing use by tier suppliers.
Nevertheless, Olsson also makes it plain that the technique is not really suitable as a means of mass production. “It is for prototyping and low volume applications,” he states. In that context, he continues, low volume can mean anything from “a single part to between 5,000-10,000 parts per year per component”.
But within those parameters, Olsson says the technique offers a number of distinct advantages over the counterpart approach involving two machined die sections. The use of a soft-contact surface on the face of the blank, for example, reduces the risk of scratching the workpiece. The technique also obviates the need for the precise alignment of the two die halves that is required when both are hard machined elements. In addition, it lends itself to the forming of more complex shapes. “It can form undercuts without the need for sleeves to come in from the sides,” he explains.
The most immediate benefit, though, is simply the reduction in the capital outlay involved in machining only one steel die half instead of two. “We can cut that by at least 50% and sometimes by as much as 90%,” Olsson states, explaining that the latter margin is made possible by the fact that the hard die half can be made from a material such as wood or plastic for some applications. Certain automotive-related users, he says, utilise dies in which the machined half is made from a zinc alloy that can be re-melted and then re-used repeatedly with a different profile. This further enhances overall cost-effectiveness in contrast to a steel die that would instead have to be scrapped completely. The maximum pressure the technique can exert on a part is currently around 1,400bar or 140MPa.
Alleviating limitations
The factor that inhibits the adoption of the technique in high-volume environments is simply that of speed. Conventional stamping can form a part in seconds, Olsson points out, whereas the Flexform process is much slower and may, in contrast, take “a few minutes”. But this can be partly offset by the fact that the technique does offer the opportunity to make multiple parts simultaneously. “We have a rectangular forming bed with a maximum size of close to two metres in width and four metres in length, on which we can place multiple forming tools side-by-side,” he explains. Maximum part depth in that case is 350mm.
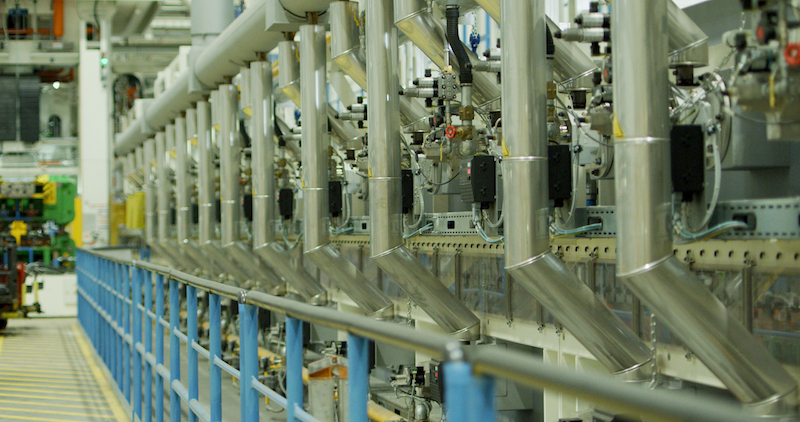
While as many as 15 parts at the same time has been achieved elsewhere, four is the commonplace upper limit for automotive applications. A typical instance, Olsson says, might involve a set of doors – left and right and front and rear. The technique is, he confirms, used to make parts for on-road vehicles and is particularly favoured by high-end marques. Daimler, for example, uses it to produce the roof of its Maybach vehicle, and Bugatti uses it to make doors. Volvo also currently uses the technique “for almost all its prototyping involving mild steel” plus a very small amount of end-product applications.
As for the materials the technique can be used to form, Olsson says that while it is used to create parts from relatively exotic materials, such as Inconel in the aerospace industry, its use in automotive applications has so far been confined to conventional mild steel. A primary reason for that is that the use of the rubber diaphragm has restricted it to cold-forming applications with no heating of the metal possible.
But, intriguingly, those limitations could now be set for change. On the first count, Olsson says recent development work has shown that the technique can be applied to high-strength steels of up to 1,200MPa. On the second, the company has now released a new version of the technology called High Pressure Warm Forming (HPWF). This can cope with workpiece temperatures as high as 300°C to replace previous techniques involving two steel die halves operating at temperatures as high as 700°C.
The precise details of how the technique has been adapted for use at elevated temperatures remain confidential, though Olsson does concede that the essential new feature involves the use of a flexible insulating layer between the workpiece and rubber diaphragm to protect it, and the hydraulic oil behind it, from temperature-related degradation. It has been developed, he states, specifically to satisfy an aerospace industry requirement for the manufacture of titanium parts. But experimental work has indicated that it could be used to make magnesium parts – something that may, at some future point, make it relevant to automotive manufacturing requirements.