保时捷向莱比锡工厂投资5亿欧元进行扩建,这是公司首次在一个生产线上生产3款车型
自2014年保时捷莱比锡工厂开始Macan汽车以来,一直都是成熟的生产厂,拥有现代化喷漆车间和专门的汽车车体修理厂。对Panamera而言,白车身要在汉诺威大众工厂进行制造和喷漆,然后运送到Saxony工厂,进行预装配和总装配。
现在,为了进行新一代Panamera完整的生产,保时捷进行了16年以来的第四次扩建,汽车车体修理厂扩大到56,000平方米。该项目投资5亿欧元,改装了装配线,升级基础设施,又产生600个工作岗位。这种稳步改进状态并没有影响公司理念或生产车型。莱比锡工厂与祖文浩森(在斯图加特附近,是911生产地)工厂的生产理念相同。品牌理念可追溯到公司创始人,Ferry Porsche,他一直坚信“一切都要极致”。
Panamera汽车车体修理厂总经理Christoph Beerhalter说:“这里的生产特点就是流程透明化,并一贯实施精益生产原则。”
"铝是要求非常高的一种材料。使用抛光板和抛光技术,产生的热量可能会是材料变形,要想避免这一点,就需要技术" - Christoph Beerhalter, 保时捷汽车
以准时化顺序方式对预装配和特定车型组件进行送递,可以准确完成装配线订单 — 有时候会直接抵达规定地点和装配线。工厂不断进行改进,减少甚至消除浪费,并继续强调高质量。
首要工作原则就是流程 — 智能物流和IT系统连接了所有创造价值过程。保时捷制造商根据“客户循环” — 生产数量 — 是制造汽车所有工艺的推动力。装配车间的员工们从物流供应中心拿到材料。然后,供应商提供高质量零部件,并满足即时需求,避免生产过剩和不必要的缓冲。最后,零错误原则保证高速而稳定的产品工艺,避免小失误。
高度垂直整合Panamera的车体是在大众集团灵活的模块化标准装备(MSB)基础上制造的。莱比锡工厂新增的MSB汽车车体修理厂是由工厂控制系统监管,负责汽车订单中从第一个组件到白车身的各个方面。
汽车车体是由430个独立零部件,通过热能机械接合方法组装而成,使用200多米长的粘合剂。MSB汽车车体修理厂平均每小时生产13个汽车车体。这里共有475个机器人和189名员工,建造汽车车体,垂直化整合率超过90%。
Beerhalter说,“汽车车体的45%是由铝构成。铝成本很高,需要及高度的模具制造与表面抛光稳定性。”
铝质外壳新款Panamera的整个外壳都是有铝构成的。汽车车体从下到上是由4个主要部分构成:底座、上层结构、附加零部件和表面加工。
首先,车身前部平台、地板和车身后部组装在一起,构成底部线。侧板和顶棚附加在底座上,之后的建构城流程本位三大部分。
在上层结构上,内侧壁被焊接到底座结构上。下一步是安装第二个上层结构,即外侧板 — 这些是外饰板,构成了Panamera设计的主要部分。第三部分,就是将汽车车体完整地安装到顶棚上。
在附加零部件生产线上,车门、后备箱、前翼、和阀盖(这些都是同步提前制造的)就被安装到车身上。机器人将车本和阀盖全自动安装起来,因为曲面之间紧密的间隙尺寸需要自动的方式。工人们使用一个半自动程序装配所有的附加零部件。
第四个,也是最后一个部分就是表面加工。汽车制造商检测表面,如果需要还会进一步加工,并调整附加零部件。这个部分需要的员工最多,因为这部分需要手工技术和肉眼。
Beerthalter说,“铝是要求非常高的材料,很难制成零部件,因为这需要非常熟练地应用抛光板和抛光技术 — 产生的热量可能使材料变形,想要避免这种情况就需要技术。”
空调不仅能冷却这个繁忙而拥挤的生产线,而且让空气中的铝粉尘落下并提取出来。操作员和车辆分别推动皮带,使其倾斜,创造一种优质人体工学高度,适合安装车翼、阀盖和顶棚等。
Beerhalter说,“之后就遇到另一个质量瓶颈。每个车体都需要检查,这就需要喷漆车间完成。”
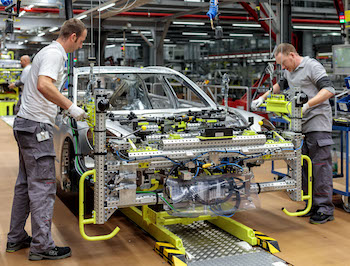
动力和性能2013年,莱比锡首次在Macan汽车车体修理厂安装太阳能技术。工厂顶棚的光伏系统能发电880kWp,每年能发电800,000kWh,相当于150家欧洲家庭一年的耗电量。
还有一个光伏系统,将为新建Panamera汽车车体修理厂供电,这里的耗电量很高,但是比传统的方式节省4千度能量。新厂房里所有的照明都是基于LED技术。
工厂控制系统里先进的网络技术也有助于节能。旁边有供热机组,用于供热供电。新建的汽车车体修理厂的工艺和制造系统有助于降低耗能。这一部分要归功于节能连接技术,比如FDS阀盖不需要预钻孔。
因为轻质汽车车体混合了多种材料,铆接和铆钉接合技术明显降低了汽车车体修理厂的耗能。工厂里的所有机器人和设计都采用节能技术。
保时捷生产规划部长Thomas Riediger说,“特别要指出的是,焊钳采用了伺服气体力学。选中的组件现在不需要任何压缩空气,这显著降低了耗能。”
Riediger说,“在装配方面还会有更多改变。”
在制造、生产设备以及汽车之间的只能联网可以实现装配过程中对重量的控制。
他还说,“仅仅是间歇时间的关机每年就能节能80MWh。只要可能,卤素聚光灯就用LED灯所代替。根据工作量和汽车类型,照明只在需要的地方提供,因此能大量节省耗能。”
此外,Macan汽车车体修理厂里,机器人焊枪上的现代化冷却技术也能降低耗能,每年能节省365,000kWh。
在喷漆厂,石粉过滤系统相比水性系统节能60%。在流程的最后,保时捷还继续可持续性发展,因为莱比锡工厂里70%的车辆都是从现场铁路仓库直接运输的。
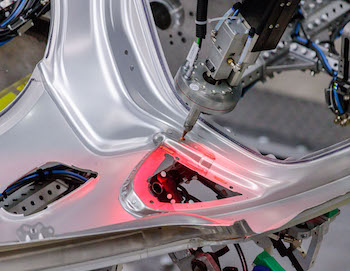
一天工作的开始,就有550辆重型货车将17,000个货盘送往装配厂,8,600个货盘送往汽车车体修理厂。货盘上的材料经过拣货、排序和归类进入汽车车体修理厂和装配物流供应中心,进行生产。Panamera加上Macan和 Caynne汽车,莱比锡装配线共有235个独立循环。循环时间大约是两分钟。装配线上的车体用带有升降台的板线上或旋转悬吊管金兴运输。装配车间被分为不同的生产线,Macan和Panamera一同运输,但在安装发动机和底座的时候,就会与Cayenne生产线合并。
车门生产线:进入内饰生产线开始,车门就从车体上移除,并且运输到车门生产线上。车门上会安装电气系统、车窗马达和车门饰件(包括扩音器)。之后,车门被送到新的装配线托盘上,然后重新安装到车体上。
第一和第二内饰生产线:汽车在这里安装所有内饰零部件,包括沛县,这是最重要的组件之一。驾驶舱也会整合,而驾驶舱是汽车内最大的完整模块。驾驶舱是在外部组装,如果汽车订单做了特殊要求的话,上面部分会用皮革软包。
下一个阶段里,开关会被安装。车辆离开升降台,然后用旋转吊架悬挂起来,以便车体下半部分的任务以人体工学完成。
底部生产线:两个底部生产线与车门生产线同步进行装配。在这里安装的组件由刹车油管、空气弹簧蓄压器(如果工作步骤里包括这一项)和燃料箱。在送往外饰生产线的途中,车辆被送回升降台进行运输,这样装配任务就更加符合人体工学。
外饰生产线:挡风玻璃和后挡风玻璃由机器人安装。此外,汽车上海会安装地板、刮水器系统、电子旋转牵引杆单元、侧面安全气囊、电池,以及阀盖上的保时捷标记。
发动机组装:发动机和变速器通过侧臂向装配流程送料。发动机组装中的主要工作就是给变速器装凸缘,以及铺设电缆线。之后安装汽车变速器的离合器片、起动机和空调压缩机。发动机预装配快结束的时候,会安装氧传感器。整个汽车下段部分结束之后,会用一个大型模块运输机或无人驾驶运输系统送去组装。在这个阶段,汽车车体仍然与汽车下部是分开的。

底座组装:在发动机安装完毕之后就是底座安装了,组装上去的组件有传动轴和驱动轴。第一个循环里,会预先构造大型模块传输机的悬吊和机轴。在下一个循环里安装消音器,然后安装传动轴,最后是驱动轴。
混合生产线:莱比锡工厂的组装是在混合生产线上完成的。这是保时捷首次将三个车型 — 即Macan, Cayenne和Panamera — 选择同一个线路,通过相同的工作站。装配完成的车体从去耦模块经过高架输送器抵达混合流程,并放下,置于装配线上。这时Cayenne汽车就如装配线。
合并:大型模块输送机在构架下面移动,然后抵达合并区。上层结构和下部自动完成螺钉连接。此外,悬吊系统要通过人工安装到顶棚。之后,保时捷汽车就会从电器单轨回到托盘线上。
装配线托盘一和二:在车辆抵达装配线托盘传送带上之后,内饰装配也完成了,中心仪表台和座椅也安装完毕。然后,汽车就会接受前端模块。在装配线第二货盘上,员工提前把车门安装到相关车辆上,并进行质量控制。
最后装配线:在最后的装配线上,最后的任务包括轮舱、给车装上燃油、制动液、冷却剂和挡风玻璃清洗液。最后,轮胎被安装到钢圈上。之后,Macan, Cayenne和Panamera就立在4个车轮之上了。
测验阶段和精加工:在最后的装配循环里,将完成新车启动、测试和最后检测。像刹车这样的驾驶功能会在滚动测试站中进行。此外,会有一个员工首次启动发动机。最后的调整包括底座、千灯,并校准驾驶员辅助系统。然后汽车会在短距离测试轨道上展示,所有相关组件要完美完成操作。之后,汽车外饰要经过清洗,还要完成密封实验。所有的事情都已完备。