inos took on the task of integrating a new gap and flush system into an existing production line shared by two separate and distinct vehicles
As modern vehicle design responds to the customers’ growing expectations on fit and finish quality, the demand grows for increasing sophistication in manufacturing techniques. Semi- or fully-automated assembly operations for vehicle panels, such as doors, fenders, hoods and roofs, are considered typical by today's production standards. A variety of different materials, complex geometries, and diminishing tolerances for gap and flush metrics are all factors which must be take into account when deciding on a suitable approach to closure load.
However, defining a strategy for automated closure load and being able to successfully manage and optimise the resultant manufacturing process represent two very different challenges. To that end, inos G-Gauge Gap and Flush Solutions have become indispensable tools for manufacturers striving to ensure a consistent, world-class product and a robust, reliable manufacturing process. In addition to delivering precise dimensional information on every single vehicle produced, the inos systems also allow users to set customised limits and alarms on the ensuing measurements and conduct valuable root cause analysis studies from anywhere on the customer’s network using the on-board SPC reporting package.
Case study: Initial RequestA customer approached inos about integrating a new gap and flush system into an existing production line where two separate and distinct models were being built. The initial concept called for two robots, each equipped with an inos G-Sens Dual View Sensor, to be placed on opposite sides of the production line and measure the vehicles as they moved through the cell. The robot-mounted sensor configuration offered the flexibility to support multiple vehicle models, the ability to easily add and/or alter inspection locations, and the added benefit of optimally positioning the sensors throughout the entire measurement cycle.
However, a detailed investigation into the viability of this configuration presented considerable challenges. Significant modifications to the existing cell and the surrounding environs would be necessary to accommodate the addition of the robots. The cell’s overall footprint would need to be expanded and the mandatory safety infrastructure (fencing, light screens, pressure pads, etc.) would need to be installed. Furthermore, it was determined that it would be very difficult to conduct the total number of desired inspections within the available cycle time. Finally, and perhaps most decisively, the scope of work to support this configuration would exceed the customer’s funding level.
An innovative, custom designUndaunted, inos engineers continued to work with plant team to customize a gap and flush solution which would fulfil all of the technical requirements and still fall within budget. The result was an alternative, stationary-mounted sensor configuration which would require less space, decrease the complexity of the system, reduce the modifications to the cell, and provide a significantly lower price – while simultaneously allowing for an increased number of inspections within the allotted cycle time.The interesting aspect of this system was the requirement that the plant team be allowed to safely travel between the moving vehicles and the sensor structure, if needed. A detailed CAD layout of the proposed system was performed to determine the specific inos sensors that would be necessary to successfully commission the cell. inos offers a wide spectrum of options across multiple sensor families: laser-triangulation, greyscale, 2D, 3D, single laser, multi laser, and more. While sensor standoffs (the distance between the face of the sensor and the feature being measured) can vary between 150mm and 1,600mm, the virtual lay-in concluded that 1,200mm would be the optimal distance for this application. The upfront simulation also provided engineers with the exact quantity, arrangement, and positioning of the inos sensors, which enhanced the efficiency and effectiveness of the onsite system implementation.
Typical measurement cycleThe measurement cycle is automatically triggered when a car body enters the cell. As the vehicle travels down the assembly line, its exact position is continuously tracked by means of a high-resolution encoder. This ensures that the stationary-mounted sensors can conduct their measurements down to the millimeter – even on a moving vehicle. Images are collected and the inos G-Gauge Gap and Flush software executes proprietary inspection algorithms, generates precise dimensional data, applies tolerances, and notifies plant personnel if any inspections have exceed their desired limits.
Commissioning and implementationAs previously mentioned, the virtual design process greatly aided efforts to commission the system in the shortest amount of time possible. Small windows in the facility’s production schedule necessitated that resources be utilised extremely efficiently and, to the extent practical, tasks be performed proactively, in advance of any onsite work. Information obtained during the CAD lay-in procedure made it possible to “virtually install” the gap and flush cell before ever setting foot in the plant. The simulation enabled inos engineers to pre-configure measurement algorithms, coordinate timing for sensor triggers, and enter customer tolerances and alarm settings. Even the sensor framework and mounting structure could be constructed offsite and ahead of schedule. In effect, the vision system implementation was already complete before delivery of the equipment to the end-user facility.
Data analysis and processingOnce the system is up-and-running, inos turns its attention to helping customers derive value from the cell and quickly turn data into actionable information. Innovative inos web-based SPC Reporting Software allows users to evaluate and analyse measurement results from anywhere on the customer’s network – without the need for any local software installation – on desktop, tablet, or mobile phone.
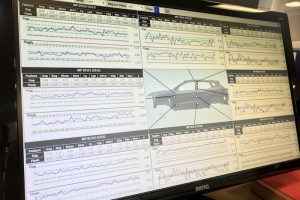
Areas downstream of the gap and flush cell utilise inos Vizualization Software to easily and intuitively display unit-specific measurement results on large, industrial, flat screen monitors. The data shown offers a reliable, objective, and accurate assessment of every single vehicle’s fit and finish. That data can then be used to guide finesse and fitting operations in order to ensure the best possible product reaches the end customer.
Upstream locations can also take advantage of the tremendous amount of information provided by the inos cell. Trends, outliers, and patterns in the gap and flush data can be used to make precise adjustments in the closure load process, thus completing a valuable closed-loop of quality management. Advanced users have also employed the gap and flush systems to validate upstream tooling adjustments, verify the effectiveness of maintenance operations, and avoid costly downtime and potential lost production by the constant monitoring of key, quality-indicator features.