Cada vez es mayor la presión de reducir el peso de los vehículos, lo que significa que los proveedores de materiales que producen paneles de carrocería, interiores, ensamblados, etc. tienen que seguir innovando en el uso de los plásticos reforzados con fibra de vidrio (GFRP).
Los materiales de fibra carbono tienen una mayor elasticidad y mejores propiedades de fatiga pero las fibras de vidrio tienen una gran resistencia tensil, una gran resistencia al impacto y una gran resistencia química, pero sobre todo, son más económicos. Los materiales reforzados con largas y continuas fibras de vidrio se pueden utilizar en procesos de moldeado por compresión, mientras que los materiales con fibras de vidrio troceadas son adecuadas para el moldeado por inyección y ambos procesos son muy utilizados en la producción en masa.
Soluciones de fibra de vidrio Estos factores permiten que los GFRP sean especialmente adecuados para la producción de paneles de carrocería. General Motors fue una de las primeras marcas en reconocer sus ventajas y ya en 1953 produjo el Chevrolet Corvette con una carrocería por completo de GFRP. Los diseñadores de GM apreciaron la oportunidad de ahorrar en peso con un material inoxidable no metálico que ofrece la oportunidad de crear reducidas unidades del Corvette sin necesidad de invertir en enormes moldes de estampado de láminas metálicas.
[sam_ad id=17 codes='true']Todos los Corvette desde entonces cuentan con carrocerías de materiales compuestos, aunque la tecnología ha evolucionado considerablemente desde los procesos rudimentarios utilizados en la década de 1950. Por ejemplo, el uso de un compuesto de moldeado en lámina (SMC) de Continental Structural Plastics (CSP) redujo el peso del Corvette Stingray Coupe de 2016 en 9 kg. Se construyeron un total de 21 ensamblados de paneles de carrocería, incluidas puertas, tapas de maletero, paneles frontales y guardabarros con el material TCA Ultra Lite de CSP.
“Gracias a un esfuerzo conjunto de mejora continua, Chevrolet y CSP han reducido significativamente la densidad de los paneles de carrocería del Corvette de una gravedad específica de 1.9 en el modelo de 2013 a una gravedad específica de 1.6 en el modelo 2014 y 1.2 en el modelo del año 2016”, afirmó Christopher Basela, ingeniero principal de Corvette Body Composites.
TCA Ultra Lite contiene burbujas de vidrio tratadas como sustitución parcial del relleno de carbonato cálcico empleado en SMC, lo que reduce la densidad del material. Esta tecnología resulta también en una mezcla de resina más robusta que hace que las piezas moldeadas sean más resistentes a los daños en en la manipulación, también previene las micro-fisuras que producen burbujas, fisuras y ampollas. Las burbujas tratadas ayudan con la adhesión de la pintura y las características de unión.
El material está reforzado con la fibra de vidrio Advantex de Owens Corning, cuya producción tiene un menor impacto medioambiental que otros tipos de vidrio, según CSP. Adicionalmente, el potencial de cambio climático del material puede ser inferior al acero en las fases de producción y uso cuando se emplean en partes de la carrocería.
Cuando se combina con los procesos de unión y vacío de CSP, la empresa asegura que TCA Ultra Lite ofrece un acabado prémium de Clase A con pintura y lustre equiparables a los metales, incluido el aluminio. El material puede resistir los procesos de revestimiento con pintura electroforética y supera todos los ensayos de pintura de los constructores automotrices.
CSP asegura que en los volúmenes de producción inferiores a 150,000 unidades, los costes de utillaje de materiales compuestos pueden ser un 50–70% inferiores al estampado de acero o aluminio. Las piezas con perfil profundo y características de diseño agresivas se pueden alcanzar con una herramienta en un molde de compresión, mientras que el metal puede requerir varias herramientas y estampados diferentes para obtener el mismo diseño.
Ligero pero con extremos resistentes Los materiales compuestos son también cada vez más populares en la producción de módulos frontales y los procesos utilizados en su producción permiten integrar varias funciones en una única pieza. Se puede emplear una combinación de refuerzos continuos y discontinuos para garantizar que estos soportes sean resistentes donde haga falta sin tener un diseño demasiado complejo. Por ejemplo, los termoplásticos reforzados con fibra de Lanxess se utilizan para reforzar los frontales de moldeo de inyección de los SUV de Volkswagen Atlas y Teramont, que se producen en Estados Unidos y China respectivamente.
Arkal Automotive produce el frontal del Atlas y desarrollo ambos frontales en cooperación con Volkswagen. El frontal del Teramont lo produce Changchun Engley Automobile Industry Company.
Los frontales de ambos SUV se producen a partir de polipropileno moldeado por inyección. En el área entorno a la cerradura del capó están reforzadas con Tepex Dynalite 104-RG600. La matriz del compuesto semiacabado es de polipropileno y está reforzada en un 47% por volumen con mechas de fibra de vidrio continuas en forma de tejido.
“Ambos frontales utilizan insertos de Tepex que son un 50% más ligeros que los insertos comparables de lámina de acero. Además el áreaareforzada puede resistir más esfuerzo”, afirma el desarrollador de aplicaciones de Lanxess, Harri Dittmar.En ambos lados del frontal, los pilares Z están reforzados con un inserto perfilado producido con el mismo material de Tepex.
Lanxess asegura que el proceso de moldeo por inyección utilizado en estos frontales es muy eficiente. Los insertos laterales se calientan y se perfilan fuera del molde, luego se recalientan a 140°C y se colocan en el molde por un lado. Al mismo tiempo se calienta el inserto central y luego se sobremoldea con los insertos exteriores. “A pesar del complejo ensamblado de los componentes, el resultado es un proceso de producción eficiente con tiempos de ciclo reducidos”, explica Dittmar.
El posicionamiento y conformado de los insertos de Tepex en el molde se puede reproducir fácilmente. Además, las perforaciones en el material compuesto muestran la integridad estructural necesaria.
Aplicaciones de interior En los interiores también se utilizan materiales compuestos para reducir el peso de varios componentes, incluso respecto a las piezas de plástico. Por ejemplo, el Mini Countryman de 2017 cuenta con un soporte para el panel de mandos producido por International Automotive Components con polipropileno reforzado con fibra de vidrio.
El polipropileno utilizado en la pieza moldeada por inyección es Stamax de Sabic y permite que la pieza sea un 15% más ligera que si estuviera producida en plástico sólido.
La pieza se produce en una herramienta de Siebenwurst mediante un proceso de espumación estructural. En este proceso el material se inyecta dentro del molde y lo llena por completo, luego el molde se abre para que se produzca la espumación en el núcleo. La espumación aumenta el grosor de pared de 1.9 mm a 4 mm, por lo que proporciona la resistencia y rigidez necesarias sin añadir peso. Según Sabic, el proceso consume menos material que los procesos estándar y permite tiempos de ciclo más cortos. La empresa realizó un análisis exhaustivo para predecir la deformación de la pieza. Esta evaluación se realiza en la fase inicial de desarrollo y proporciona una información valiosa para el diseño de la pieza y el molde, lo que permite construir el molde correctamente en el primer intento.
“Este tipo de simulación computerizada está estandarizada cuando se trata de piezas de plástico sólido, pero todavía estamos en la fase inicial de desarrollar herramientas de simulación para piezas de espuma plástica. Tal y como se demostró en este programa, tenemos capacidad predictiva que podemos aplicar a día de hoy”, afirma el director global de automotriz en Sabic, Scott Fallon.
Hacia la producción en masa Uno de los ejemplos más impactantes de lo que se puede hacer con los materiales GFRP es la del proveedor de autopartes Benteler-SGL. La empresa produce las ballestas transversales con poliuretano reforzado con fibra de vidrio para el SUV crossover XC90 de Volvo (el primer modelo producido por la marca en la arquitectura Scalable Product Architecture, SPA), el sedán de lujo S90 y la camioneta V90. Las ballestas son una parte integral de la arquitectura SPA y es probable que estén presentes en otros modelos. Desde finales de 2017 han producido ya más de 200,000 unidades y Benteler-SGL afirma que alcanzarán las 500,000 unidades para 2018, por lo que será el mayor proyecto por volumen de componentes de materiales compuestos en la industria automotriz.
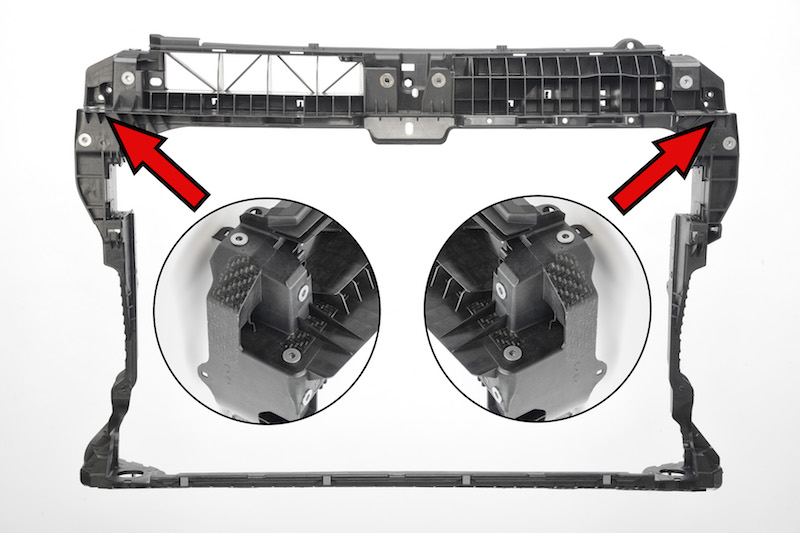
La ballesta de materiales compuestos se utiliza en lugar del habitual conjunto de muelles espirales. El resultado es un diseño compacto que ahorra unos 4.5 kg respecto a los modelos convencionales. Ofrece otras ventajas como una conducción más suave y menos ruido, vibraciones y dureza. También se aumenta el volumen disponible en el maletero porque no tiene torretas de suspensión.
La matriz de poliuretano utilizada en la ballesta es Loctite Max 2 de Henkel, que colaboró con Benteler-SGL para desarrollar un proceso de moldeado de transferencia de resina de gran velocidad y muy automatizada para producir los componentes.
Gracias a su reducida viscosidad, la resina llena el molde de transferencia de resina e impregna el refuerzo de fibra rápidamente, lo que resulta en tiempos inferiores de inyección. La velocidad de secado también es mucho más rápida que con las resinas epóxicas, por lo que los tiempos de ciclo son más rápidos en conjunto. Cuenta también con aditivos que permiten un proceso de secado más rápido y flexible.
El director de desarrollo empresarial de Benteler-SGL Automotive Composites, Frank Fetscher, afirma: “El ejemplo de nuestra ballesta para Volvo Cars demuestra que la producción en masa de materiales compuestos de fibra es ya una realidad. Es más, con este diseño flexible de componentes, somos capaces de asumir toda una plataforma con un número reducido de variantes de suspensión”.