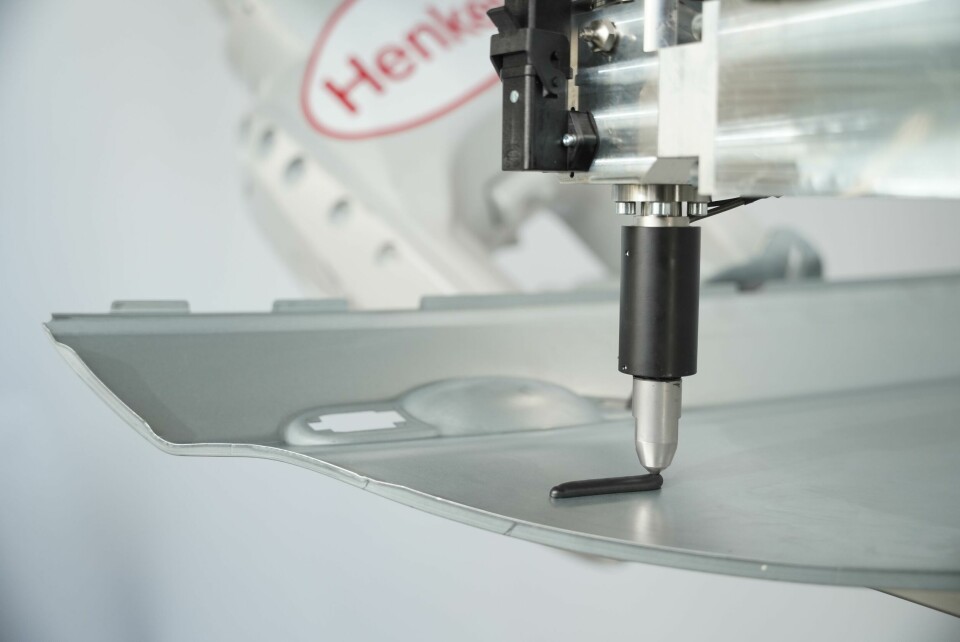
Henkel celebrates 100 years of automotive innovation and sustainability
PARTNER CONTENT
This content was produced by Automotive Manufacturing Solutions in partnership with Henkel
Henkel is celebrating its 100-year anniversary serving the automotive industry. To mark this milestone, the company speaks to AMS about its heritage, its impact on the industry today, and how Henkel will shape the vehicles of the future.
Henkel’s Adhesive Technologies business unit, a global market leader in adhesives, sealants, and surface treatment technologies, has celebrated its 100th anniversary last year. The company’s journey already began in 1876, when its founder, Fritz Henkel, started to market a universal detergent based on silicate. From its humble beginnings as a small business specialising in laundry detergents, Henkel has grown into a multinational powerhouse, with its influence reaching far beyond its original scope. Over the years, Henkel expanded into various sectors, including beauty care, laundry and home care, and adhesive Technologies with a notable footprint in the automotive industry.
Henkel’s automotive division, part of the Adhesive Technologies pillar, has become a key player in the automotive OEM business. Through this division, Henkel provides adhesives, sealants, and functional coatings that are vital to modern vehicle design and production. A significant portion of their contributions lies in supporting automakers with lightweighting solutions, enabling the use of materials like aluminium and composites, which improve fuel efficiency and reduce CO₂ emissions. Henkel’s early partnerships with automotive manufacturers laid the foundation for their continuing leadership in both traditional and electric vehicle (EV) technologies.
125 years of Teroson - From humble beginnings to automotive pioneer
One of Henkel’s automotive OEMs business’ prominent brands shaping the automotive industry is Teroson, which already has celebrated its 125-year anniversary.
Teroson’s journey started in 1898, in a small shop in Mannheim, Germany, founded by Theodor Ross. Originally, the business focused on household products like floor wax. However, with the rise of the automobile in the early 20th century, Ross saw an opportunity to adapt. Recognising the needs of the emerging automotive industry, he began to shift his focus towards developing adhesives and sealants specifically for mass-produced vehicles. This foresight was the foundation of what would become a global brand in automotive solutions.
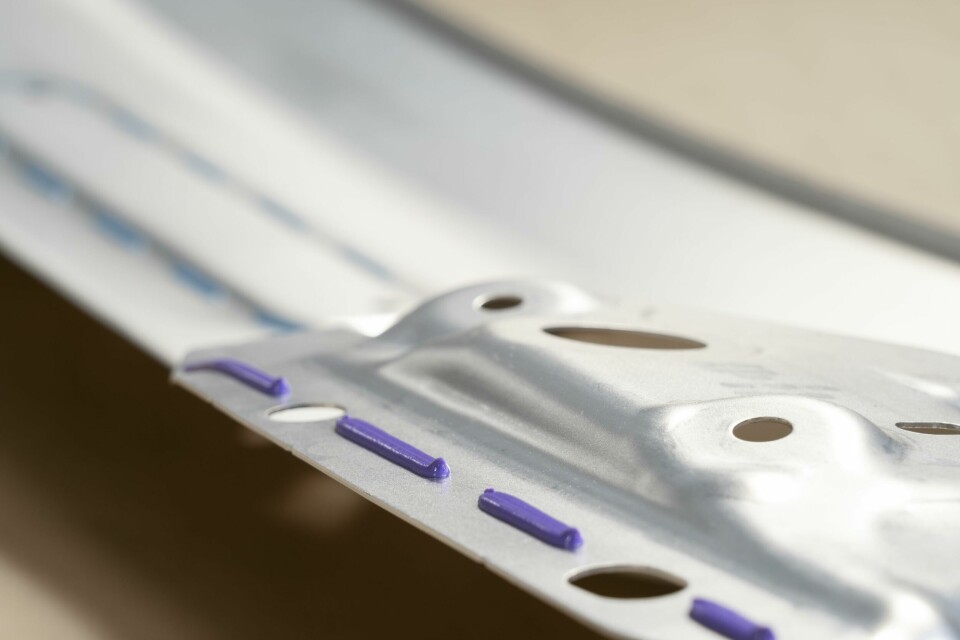
In 1924, Ross relocated his operations to Heidelberg, where he started developing solutions for the automotive industry and made a significant breakthrough by patenting his first adhesive product in 1926. This marked a major turning point for the brand, leading to the official registration of “Teroson” in 1933, a name derived from “Theodor Ross & Son,” reflecting the company’s family roots. This registration symbolised the formal establishment of Teroson as a dedicated brand for innovative bonding and sealing solutions in the automotive market.
As the years passed, Teroson expanded its product range to include bonding, sealing, and coating solutions tailored for OEM transportation assembly, vehicle repair, and industrial applications. In 1991, Henkel acquired Teroson, integrating it into its global operations and sparking further innovation. One of the most notable achievements during this time was the development of sustainable processes, including methods to recycle polysulfide in the mid-1990s, a major advancement in reducing the environmental impact of Teroson products.
Today, the Teroson brand remains a key player in Henkel’s strategy to navigate the rapidly changing automotive industry. As the industry moves toward electrification and sustainability, Teroson products play a pivotal role in lightweight construction, improving vehicle performance, and reducing carbon emissions. Henkel’s Teroson solutions continue to assist automakers meet the demands of a greener future while maintaining the high standards of quality and performance expected from the automotive industry.
Automotive industry trends and Henkel’s role
The automotive industry is undergoing a significant transformation, driven by trends like the rise of electric vehicles (EVs), autonomous driving, and a focus on sustainability. Major automotive companies are increasingly investing in electrification and advanced safety systems while adopting lightweight materials and exploring new digital technologies.
Key Industry Trends | Details |
---|---|
Electric Vehicles (EVs) | |
EV Production Growth | EV production will rise from 5M units in 2018 to over 18M by 2024, capturing 25% of the market. |
Battery Innovation | Advancements in lithium-ion batteries are improving range, reducing charging times, and lowering vehicle weight. |
Autonomous & Connected Vehicles | |
Vehicle Connectivity | Cars are becoming connected hubs, integrating IoT and infotainment for enhanced driving experiences. |
Sustainability & Lightweight Materials | |
Material Shift | Lighter materials like aluminium and composites are improving EV range and performance. |
Sustainability Practices | Automakers are adopting eco-friendly materials and processes to lower CO₂ emissions throughout vehicle lifecycles. |
Battery technology for EVs
One of the key areas where Henkel is making an impact is thermal management. Henkel’s advanced thermal interface materials, such as Loctite EA9400, are designed to optimise battery cooling, prevent overheating, and extend the life of EV batteries, ensuring that the batteries can operate safely under extreme conditions. In addition to heat management, Loctite EA9400 provides crucial fire protection for up to 10 minutes in the event of battery failure, offering enhanced safety measures for both passengers and the vehicle’s infrastructure.
Adhesive and sealant technologies
As automakers continue to prioritise weight reduction to improve fuel efficiency and lower emissions, Henkel’s adhesive solutions are playing a critical role in enabling the use of lighter materials like aluminium and composites.
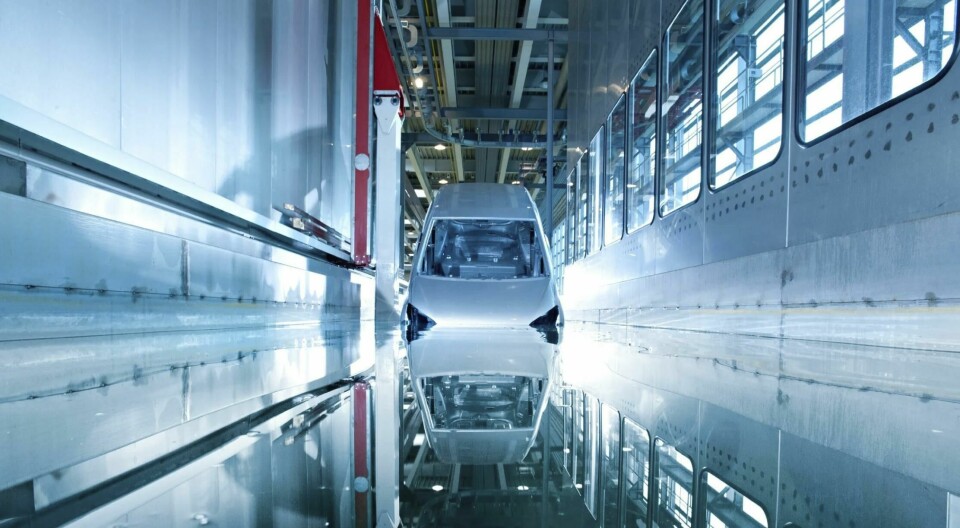
One example of this is the use of Henkel’s TEROSON® structural inserts to replace traditional metal reinforcements in vehicle designs. These inserts, made from glass fibre-reinforced nylon paired with structural foam, help automakers reduce the vehicle’s weight while maintaining crash performance and lowering supply chain CO₂ emissions by up to 33%. By reducing the use of heavier metal components, Henkel’s structural inserts enabled the automaker to meet its sustainability goals without compromising the strength and safety of its vehicles.
Sustainability and innovation
Henkel’s commitment to sustainability extends beyond the vehicle itself to the entire manufacturing process. One of the company’s most significant contributions in this area is its peroxide-cured anti-flutter technology, which reduces CO₂ emissions during the assembly process. This technology also allows manufacturers to operate at lower curing temperatures, decreasing energy use and further reducing the carbon footprint of vehicle production. Henkel’s innovations in this area are designed to help automakers meet the rising demand for eco-friendly products while maintaining high levels of performance and safety.
Henkel’s focus on sustainability aligns with the broader industry shift towards a circular economy. The company is actively involved in developing solutions that support the recycling and repairability of EV battery packs, ensuring that these vital components can be reused or safely disposed of at the end of their lifecycle.
Another of Henkel’s innovative contributions to sustainable manufacturing is its Thin-film TecTalis process powered by Bonderite. This advanced metal pretreatment process significantly reduces CO₂ emissions by operating at ambient bath temperatures, cutting energy consumption by up to 32%. By replacing traditional zinc phosphate pretreatment methods with the TecTalis process, automakers can reduce both water and energy usage while eliminating hazardous waste products like heavy metals.
Henkel’s 100-year journey of innovation for the automotive industry continues to make a profound impact for modern cars. Through its market-leading adhesive technologies, thermal management solutions, and commitment to sustainability, Henkel is guiding automakers to navigate the challenges of electrification and environmental regulations. As the automotive industry evolves with trends like electric vehicles, autonomous driving, and the pursuit of eco-friendly manufacturing, Henkel remains a crucial partner in shaping the future of mobility.
With its advanced technologies and forward-looking approach, Henkel is poised to remain at the forefront of automotive innovation for years to come.