GM prepara un proyecto de taller de pintura doble en Bowling Green con el que pretende alcanzar niveles de calidad y producción sin precedentes
439 millones de dólares es una inversión considerable. Especialmente si este dinero está destinado a la construcción de un taller de pintura automotriz de 46,451 metros cuadrados que podrá procesar tan solo 40,000 vehículos anuales, al menos al principio. Sin embargo, esta es la cantidad de dinero involucrada y la producción prevista para el nuevo taller de pintura que prepara GM en su planta de Bowling Green en Kentucky, EUA, donde produce sus deportivos Chevrolet Corvette de gama alta y sus ‘súper autos’.
El comentario anterior procede de Kai Spande, gestor de planta en Bowling Green y la persona responsable de asegurarse del rendimiento de la inversión. Spande confirma también que la última semana de marzo fue un momento crítico en el proceso con el primer ensayo de dos conjuntos de paneles. Nos explica que una característica diferencial de la pintura del Corvette es el proceso “panel off” en el que se pintan por separado los paneles de fibra de carbono y lámina compuesta moldeada (SMC, sheet moulding compound) antes de unirlos a la estructura de aluminio. El capó y el techo, añade, están compuestos de fibra de carbono y los demás paneles son de SMC, a excepción de los salpicaderos delantero y trasero que son de moldeo por inyección.
[sam_ad id=17 codes='true']
Nueva generación de talleres de pintura A pesar del logro la empresa todavía debe continuar con el desarrollo antes de poder transferir a la nueva instalación los diez colores que actualmente aplica en el antiguo taller de pintura y que lleva activo en la planta desde hace tres décadas. De hecho, comenta Spande, esta instalación es el “el taller de pintura operativo más antiguo de GM en Norteamérica”. Pero añade que durante este tiempo ha habido cuatro generaciones del vehículo y dado que GM no puede interrumpir la producción de vehículos, no era posible renovar el antiguo taller para cumplir con los requisitos actuales.
En términos técnicos, una de las principales características del nuevo taller de pintura será cómo extiende la curación a baja temperatura de los paneles pintados que ya es un identificador del proceso. De hecho, declara Spande, es “un proceso revolucionario” en este aspecto. Concretamente, el taller antiguo realizaba la curación a 129° C, el objetivo es que el nuevo taller pueda realizar el mismo proceso a "107°C o incluso menos". Pero Spande destaca que serán los mismos paneles y no habrá detrimento en la calidad del acabado de pintura desde el punto de vista del cliente. De hecho, asegura que la reducción de la temperatura durante la curación es "inherentemente buena" tanto para los sustratos como para los materiales de pintura.
Sin embargo, habrá diferencia en la "formulación de la pintura" que se alterará para adaptarla a la menor temperatura de proceso. Además, se extenderá tanto la longitud física del horno en el que se realiza la cura como el tiempo que los paneles pasan en el mismo. Respecto a la duración, Spande asegura que el tiempo de curación en la anterior instalación es de 90 minutos, en la nueva instalación podría extenderse "entorno al 25%” aunque todavía habrá que confirmar estas estimaciones.
El proceso de pintura de los paneles continuará siendo el proceso de "tres humectaciones" de GM en el que se aplican el primer, la capa base y la capa transparente sobre mojado sin realizar un secado completo entre capas. También continuará utilizando materiales con base acuosa. Pero según comenta Spande, se han realizado mejoras significativas en otros aspectos. El nuevo taller de pintura utilizará un aplicador de campana vanguardista, controles robóticos y técnicas de transición de color. También destaca que al pintar con materiales no metálicos, no hay posibilidad de utilizar tecnologías de carga electroestática para ayudar a mejorar la adhesión y mitigar el desperdicio.
El hecho de que la instalación gestiona piezas metálicas y no metálicas – la estructura de carrocería y los paneles respectivamente – significa que hay “dos flujos separados de materiales”. Pero aunque se hayan mejorado las técnicas de pintura de materiales no metálicos, según confirma Spande, el proceso de los materiales metálicos es una réplica del proceso de revestimiento eléctrico existente, que destaca porque proporciona al aluminio un aspecto negro en lugar del tradicional color metálico. Pero ambos procesos compartirán en el nuevo taller de pintura el control medioambiental extendido, lo que significa que toda la instalación, y no solo las cabinas de pintura segregadas, cumplirán con los mismos estándares de pureza, humedad y temperatura del aire.
Spande destaca esta cuestión. “Todo el taller de pintura es una sala blanca”, comenta. Esto significa que solo hay una entrada y salida para los trabajadores en toda la instalación. Además, comenta Spande, una vez estén en la instalación y hayan "atravesado el lavado de aire, caminado sobre el papel pegajoso y se hayan colocado sus trajes sin pelusa" este será "su entorno y así permanecerán durante todo el día”. Cuando esté a pleno rendimiento contará con 125 trabajadores de planta por turno en contratos por horas y unos pocos técnicos "asalariados".
También significa que las estructuras secundarias que envuelven las cabinas de pintura no necesitan garantizar la calidad del aire en el punto de aplicación. En su lugar, comenta Spande, su función es controlar el exceso de aplicación en el primer paso en un factor en el que establece un nuevo estándar para la empresa en su continente de origen. Se trata del uso del 'cepillado en seco' para capturar y eliminar el exceso de pintura del aire en las cabinas de pintado. De hecho, confirma Spande, la línea de pintura del nuevo Corvette en Bowling Green “será la primera fábrica de General Motors en Norteamérica que utilice el cepillado en seco", aunque comenta que la empresa ya utiliza la técnica en un par de plantas en China.
"Le debemos a nuestros clientes que cuando compran un deportivo de 140,000 dólares tenga un acabado de pintura de calidad" - Kai Spande, GM Bowling Green
Spande es completamente claro con que esto debe ayudar a GM Bowling Green a alcanzar “niveles sin precedentes de calidad y producción. El motivo es la dramática restructuración en la manera en la que el taller de pintura interactúa con el subsiguiente proceso de ensamblado, especialmente en la enorme reducción de almacenamiento intermedio entre dos conjuntos de operaciones.
La práctica habitual de GM, comenta Spande, es contar con “gigantescas instalaciones de almacenamiento para carrocerías pintadas”. Pero un sistema eficaz en un entorno de producción en gran escala no sirve para la producción del Corvette, ya que trabaja en una "ventana de tres semanas de carrocerías secuenciadas" y tan solo produce "12 vehículos por hora”. Como tal, la empresa anteriormente funcionaba en lo que GM define con un ya exigente valor de 12 horas de piezas entre la pintura y el ensamblado. Pero con la nueva configuración el margen de seguridad será de tan solo una sexta parte - “tan solo dos horas de piezas pintadas”. Se trata de una "operación muy simplificada", lo que significa que no podremos "soportar tiempos de parada de más de dos horas".
En la actualidad el énfasis está en completar el proceso de comisionado y en la transferencia de operaciones desde la instalación antigua. En ambas cuestiones Spande considera que el objetivo es que el nuevo taller de pintura aplique "cuatro o cinco colores para otoño de este año”. Los colores restantes se aplicarán en otros seis meses, cuando ya se podrá cerrar por completo la instalación antigua. Es interesante, agrega Spande, que para la nueva instalación "estamos trabajando en cuestiones que no son convencionales", aunque no pueda comentar más al respecto.
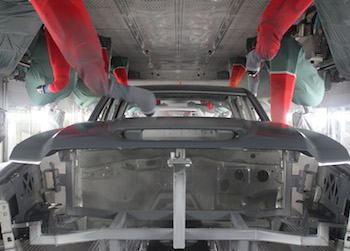
Un nuevo taller de pintura en Flint En la planta de camiones de GM en Flint, Michigan, el nuevo taller de pintura lleva un año operativo, según nos confirma el director de área Craig Jones. Al igual que en Bowling Green, la nueva instalación de Flint sustituye a la instalación previa que se cerró finalmente en octubre del año pasado después de un periodo de transición de seis meses. De hecho, comenta Jones, la anterior instalación era de la década de los 40 y no se acercaba a los estándares de sala blanca que GM exige en sus instalaciones de pintura. “Más de la mitad estaba al aire libre", nos informa. En contraste, el nuevo taller de pintura que representa una inversión de 600 millones de dólares es una "sala blanca completamente cerrada de extremo a extremo y con la última tecnología”.
Jones asegura que la instalación está diseñada para la próxima generación de camiones GM, pero que no comenzarán a producirse hasta que se finalice la modernización de las áreas de ensamblado en 2019, en cualquier caso se tomó la decisión de poner en marcha el nuevo taller de pintura. En la actualidad la instalación procesa la serie de camiones de carga pesada K2xx con 32 unidades por hora, aunque Jones añade que la producción máxima proyectada podría alcanzar los 47 vehículos por hora.
Jones también confirma que el antiguo proceso utilizaba un primer y capa base de base disolvente y que se acaban con una capa transparente 1K también de base disolvente. En la nueva configuración, GM sustituyó las capas primer y base con pinturas de base acuosa, mientras que la capa transparente continúa siendo de base disolvente, esta vez 2K. La nueva pintura, comenta Jones, es más resistente y proporciona un mejor aspecto visual.
También ha habido cambios notables en el proceso. Jones explica que en la antigua instalación había una fase de inspección y reparación manual, también una fase de horneado entre la aplicación del primer y la capa base. Esta fase se ha eliminado por completo y ahora se trata de un proceso continuo de tres humectaciones. Los beneficios inmediatos son la reducción del consumo de energía y generación de residuos, aunque el control de exceso de pintura continua siendo acuoso y no 'seco'.
Jones apunta que la configuración de las cabinas de pintura es ahora más "larga y estrecha", para proporcionar una mejor "eficiencia de transferencia y equilibrio". La instalación también cuenta con dos cabinas en paralelo a diferencia de la cabina única de antes, este cambio permite aumentar la producción y permite continuar trabajando si una de las cabinas no es operativa. Pero fuera de las cabinas en las áreas donde trabaja la gente se ha tomado la oportunidad de implementar técnicas de 'gestión visual' que GM pretende sean rutinarias en todas sus plantas.
Un aspecto visual de la instalación es una pared de partición metálica que demarca el área operativa donde trabaja la gente y donde se producen los procesos de pintura, del área que contiene los depósitos de almacenamiento y los equipos de procesamiento como el fosfatado. El motivo no es evitar que la gente entre en áreas restringidas, sino aumentar la efectividad de la recirculación interna de aire. Tal y como explica Jones, el aire dentro del taller de pintura se recircula entre dos y cuatro veces, pero cuando entra a la instalación lo hace en el área operacional "donde está la gente" y luego avanza a las demás áreas donde no hay gente. Esto mejora la comodidad de los trabajadores ya que el aire no se ve afectado por el aumento de temperatura al contacto con los equipos u otros gases que pueda acumular. En lo referente a la temperatura, Jones estima que la temperatura del aire en la parte más alejada de los trabajadores es de "cinco a diez grados superior" que cuando entra. Las cabinas de pintura están en el área de las personas, pero están cerradas de manera convencional para minimizar su efecto en el entorno.
Menos consumo energético – mayor moral Después de un año de funcionamiento Jones asegura que GM tiene varias referencias para demostrar la eficiencia del nuevo taller. Seguramente la mejora más básica está en el consumo de energía por vehículo que es de 0.6 MW. El potencial de producción, aunque en la actualidad no se esté explotando al máximo, es un 50% superior al anterior ya que el máximo de vehículos por hora del anterior taller era de tan solo 30 unidades.
No es rápido alcanzar esta posición. Jones estima que se necesitan por lo menos seis meses para que la gente se acostumbre al nuevo entorno de trabajo y añade que la transición es complicada para el personal técnico y de mantenimiento que se enfrenta a una mayor sofisticación técnica, con por lo menos 100 robots vanguardistas. Pero la mejora es evidente en el día a día, comenta Jones, que ocupaba el mismo cargo en el anterior taller, en la forma en la que la gente realiza su trabajo. “Están mucho más involucrados y son más felices”, declara. “Ha mejorado la moral, ha aumentado la producción. El anterior taller tenía buena calidad, pero el nuevo es muchísimo mejor".