En el nuevo taller de carrocería de Neckarsulm, Audi aplica una innovadora combinación de materiales y tecnologías de unión en su más reciente sedán de lujo.
Con la nueva generación del A8, Audi ha decidido utilizar por primera vez una combinación de cuatro materiales en la carrocería ligera del modelo. La estructura del sedán de lujo es una combinación de cuatro materiales ligeros, aluminio, acero, magnesio y polímero reforzado con fibra de carbono (CFRP). Audi da un primer paso hacia una nueva fase de construcción multimaterial que resuelve no solo los problemas de peso sino que mejora la rigidez torsional, un parámetro crítico para el manejo.
Cuarteto de materialesLa cabina del conductor está compuesta por componentes de acero formados en caliente, esta área la componen la sección inferior de la mampara frontal, los apoyapiés laterales, los pilares B y la sección frontal de la línea de techo. Algunas de las piezas metálicas laminadas se producen en diferentes grosores a medida, otras piezas se someten a un tratamiento parcial de calor. Así se reduce el peso y se aumenta la fortaleza, algo ideal para las áreas de seguridad crítica del vehículo.
Los componentes de aluminio en forma de nudos de fundición, perfiles y láminas extruidos, y elementos característicos del diseño de carrocería unitaria de Audi – Audi Space Frame (ASF) – representan el 58% de la carrocería del nuevo A8. Las nuevas aleaciones de perfiles y aleaciones fundidas con tratamiento de calor alcanzan valores de fuerza tensora superiores a los anteriores sistemas.
"Con la soldadura láser, la lente está cerca de la soldadura en su punto más caliente. Con el humo se ensucia rápidamente. En este caso es remota y puedes utilizar una lente durante muchas horas. No lo pensamos en un principio pero ha resultado ser una gran ventaja". - Dr. Bernd Mlekusch, Audi
En términos de dimensiones totales, el componente más grande en la cabina de pasajeros del nuevo A8 es el panel trasero de CFRP de rigidez torsional y ultra-resistencia. Contribuye en un 33% a la rigidez torsional de todo el vehículo y absorbe las cargas fuerzas de corte longitudinales y transversales.
En la construcción del panel se emplean entre seis y 19 capas de fibra superpuestas, cada capa consta de cintas de 50 mm de ancho. Se trata de un proceso innovador de capas directas de fibra desarrollado para aplicarse junto con el paso intermedio habitual de producir láminas enteras de fibra de carbono. Mediante otro nuevo proceso, la lámina se sumerge en una resina epoxi y se seca en pocos minutos.
Uniendo fuerzasJunto con el rediseño completo del ASF, la planta del A8 también ha reconstruido un taller de carrocería de 41 metros de altura que cubre un área equivalente a 21 campos de fútbol. Dentro del taller de carrocería, se utilizan 14 procesos de unión diferentes, entre ellos el engatillado mediante roldana, el remachado perforante y la soldadura láser remota de aluminio, que Audi afirma ser la primera en el mundo.
El engatillado mediante roldana se utiliza en todo el recorte de las puertas frontales y traseras. La técnica permite a Audi mejorar el campo de visión del conductor entorno al pilar A, los ingenieros han ganado 36 mm en los recortes de puerta respecto al modelo A8 anterior.
El remache perforante fija el marco de la pared lateral en su posición y complementa al proceso de engatillado que a su vez se fundamenta en la unión estructural. El desarrollo y adaptación de estas tecnologías de unión es lo que posibilitó el uso de esta estrategia de materiales en el nuevo A8, para combinar la pared lateral de aluminio con las láminas de acero de alta resistencia y formación en caliente del pilar B, y por otro lado, la línea de techo y los apoyapiés con sus finos flancos.
Dr. Dominik Hussmann, especialista en tecnología de unión en Audi Neckersulm explica cómo el remache perforante siempre ha sido parte del ASF pero Audi ha perfeccionado la geometría de los remaches a tan solo unos milímetros. Comenta: “Hemos conseguido estrechar y cortar el pilar B para que la entrada de la puerta sea más ancha. Los hemos conseguido mediante la combinación de tres tecnologías en aluminio y acero de alta resistencia”.
El lateral se conecta mediante cuatro remaches perforantes en cuatro posiciones y penetrando tres elementos. Dr. Hussmann afirma: “La secuencia de los componentes es crucial para que el proceso sea posible. El material en la parte inferior es maleable, y debe deformarse sin fisuras o roturas mientras que el acero en el medio también debe acomodarse al remache".
[sam_ad id=17 codes='true']Soldadura inteligenteCon la soldadura remota del aluminio, Audi confía en que ha desarrollado un enfoque que no está presente en otros constructores de gama alta. Esta tecnología aporta muchas ventajas.El posicionamiento preciso del haz láser respecto al borde de la soldadura reduce notablemente el riesgo de roturas en caliente porque se controla con precisión la aportación de calor. El tamaño del hueco entre las piezas soldadas se puede determinar inmediatamente y se puede rellenar eficientemente mediante el control de proceso. La elevada tasa de alimentación del haz láser y el reducido consumo energético reducen las emisiones de CO2 en un 25%.
Audi afirma que la soldadura láser remota permite ahorrar un 95% en costes recurrentes en la producción en serie porque elimina la necesidad del costoso control de proceso de la soldadura láser convencional.
Dr. Bernd Mlekusch, director del centro de diseño de peso ligero de Audi, afirma que "es más barato por dos factores: el flujo (requiere menos sustancia) y la lente Con la soldadura láser, la lente está cerca de la soldadura en su punto más caliente. Con el humo se ensucia rápidamente. En este caso es remota y puedes utilizar una lente durante muchas horas. No pensamos en ello en un principio, pero es una gran ventaja”. El haz no perfora el material ni siquiera en la emisión inicial — el algoritmo de sistema de Audi controla la salida de energía.
Dr Mlekusch añade: “Con las nuevas tecnologías siempre estamos pensando en el siguiente proyecto. La gente de producción también tiene que saber que funciona en serie con un 99% de fiabilidad. El proceso de implementación es constante, por lo que ocasionalmente interrumpimos su trabajo normal en la línea con algo nuevo que queremos probar".
Neckarsulm adoptó un nuevo proceso de soldadura MIG de aluminio en base al establecido proceso de CMT (cold metal transfer, transferencia de metal en frío) que utiliza en los canales de drenaje del agua en la parte inferior del nuevo A8. El enfoque es una modificación geométrica de la boquilla de gas inerte que permite alcanzar velocidades de proceso de hasta 50 mm/s y un hilo de soldadura de apariencia muy fina. En comparación con la soldadura MIG convencional, triplica la velocidad de aplicaciones equivalentes, con una menor aportación de calor y un menor riesgo de deformación del material. Para garantizar que el hilo de soldadura esté colocado en el extremo del componente con la precisión necesaria, el proceso se realiza en combinación con un sistema de detección y seguimiento automático de hilo.
Audi considera que la soldadura de resistencia por puntos (RSW) del aluminio es un proceso de unión muy versátil y que ofrece mejoras en la estabilidad de proceso y la reproducibilidad de los resultados. El uso de pinzas de soldadura con fuerzas superiores de electrodo permite reducir la adhesión no deseada del electrodo de cobre en el componente de aluminio. Finalmente, la soldadura láser, considerada por Audi una tecnología tradicional en sus talleres de carrocería, se utiliza para unir el techo a las paredes laterales.
La construcción del nuevo edificio en la planta de Neckarsulm ofreció a Audi la oportunidad de adoptar nuevas tecnologías destinadas a un flujo de producción más automatizado y complejo pero eficiente. El resultado es una planta con 500 robots, 90 sistemas adhesivos, 60 máquinas para tornillos autorroscantes, 270 sistemas de remache perforado y 90 pinzas de soldadura de resistencia por puntos.
Las nuevas pinzas de soldadura por puntos se alimentan con motores eléctricos y pesan 35 kg menos que sus antecesoras, lo que permite robots más pequeños y por lo tanto un menor consumo eléctrico. La iluminación LED, los conceptos inteligentes de ventilación y el apagado de equipos ayudan también a reducir el consumo de energía.
En términos humanos, trabajan cerca de 500 personas en tres turnos en el nuevo taller de carrocería del A8. La mayoría trabajan en el área automatizada junto con los robots, otros en el área manual en las líneas de atornillado y acabado.
Coser y cantarLa superestructura de la carrocería del ASF comienza con los ensamblados soldados inferiores, incluidos los miembros longitudinales que forman la base de los módulos frontal y trasero de la carrocería. Este último se produce en un nivel separado en el lugar. El siguiente paso es la fusión de ambos subensamblados con los paneles de suelo.
La cabina del conductor toma forma en esta base de la carrocería: los pilares A, B y C seguidos de los paneles laterales internos y externos, luego la instalación del techo.
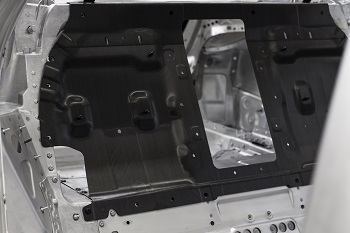
En las estaciones de geometría y enmarcado, las piezas se posicionan y alinean para el proceso de soldadura. El armazón de la carrocería se transporta a un edificio adyacente donde las puertas y las tapas (construidas allí) esperan para ser encajadas.
La carrocería avanza por la línea de acabado en el nivel inferior y se transporta al taller de pintura adyacente. Después de la pintura por cataforesis, se seca el metal ASF para que la aleación de aluminio alcance su fortaleza final.
Verificaciones cruzadasEn los 20 portones los 20 los equipos de medición de línea comprueban la precisión dimensional de la carrocería ASF. La primera estación examina la subestructura del módulo trasero, y la estación final examina la superestructura finalizada. Además de estas mediciones, Audi Quality Assurance realiza pruebas aleatorias de componentes, subensamblados e incluso carrocerías completas.
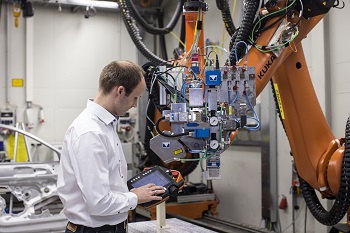
Desde la primera generación del Audi A8, la estructura Audi Space Frame (ASF) ha ido ganando protagonismo como diseño ligero para automóviles. Desde su implementación la marca ha producido más de un millón de automóviles según este principio de diseño y ha ido trabajando consistentemente sobre el conocimiento adquirido en el uso de materiales y técnicas de unión. El resultado son carrocerías cuyo ligero peso y gran rigidez ofrecen un gran rendimiento, eficiencia y seguridad.