Sames solves for BMW & Mercedes: Adhesive tech in bodyshop & glazing
Sames’ innovations support high-quality adhesive bonding in automotive manufacturing, optimising efficiency and standardisation across bodyshop and glazing processes.
PARTNER CONTENT
This content was produced by Automotive Manufacturing Solutions in partnership with SAMES
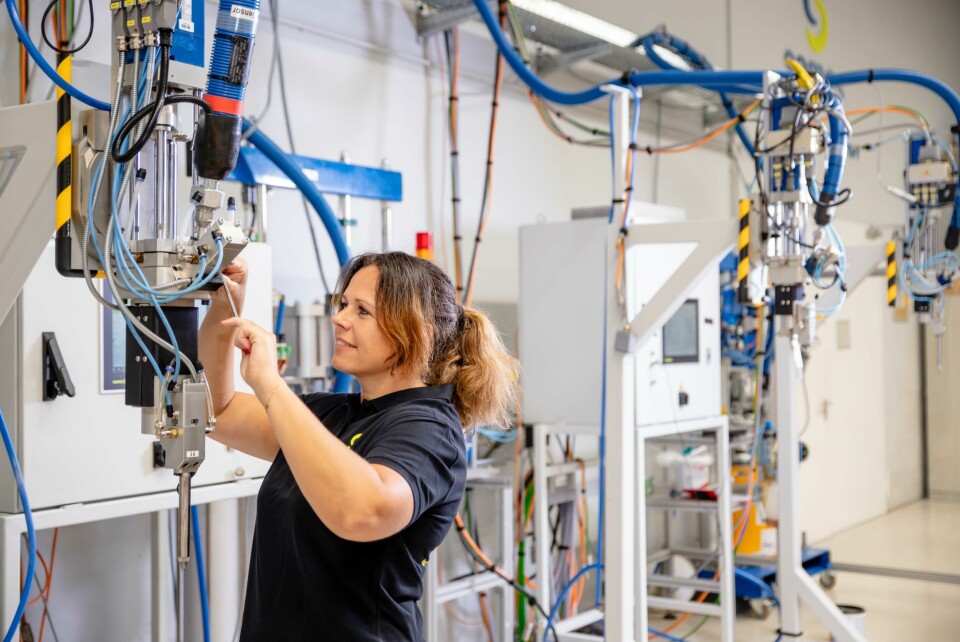
In 2012-2013, BMW began producing the i3 and i8 models at Leipzig, two models which featured carbon fibre bodies. The carmaker needed a special adhesive to join components for these models, as traditional methods were unsuitable for carbon fibre. A standard steel automotive carcass is traditionally adhered with a one-component adhesive; later made to harden in an electrocoating (also, ‘KTL’ - Kathodische Tauchlackierung) oven at 140 degrees centigrade. But since KTL ovens are not suitable for carbon fibre bodies, a different solution was needed.
BMW opted for a two-component adhesive, which meant the added requirement of thorough surface cleaning from dust and oil, but no such system existed at the time.
“So they looked to us,” says Mario Pauli, World Account Manager, High Viscosity, Sames, in an interview with AMS. “And we developed a cleaning system to meet their needs, undergoing extensive testing, both in our own laboratory and BMW’s.
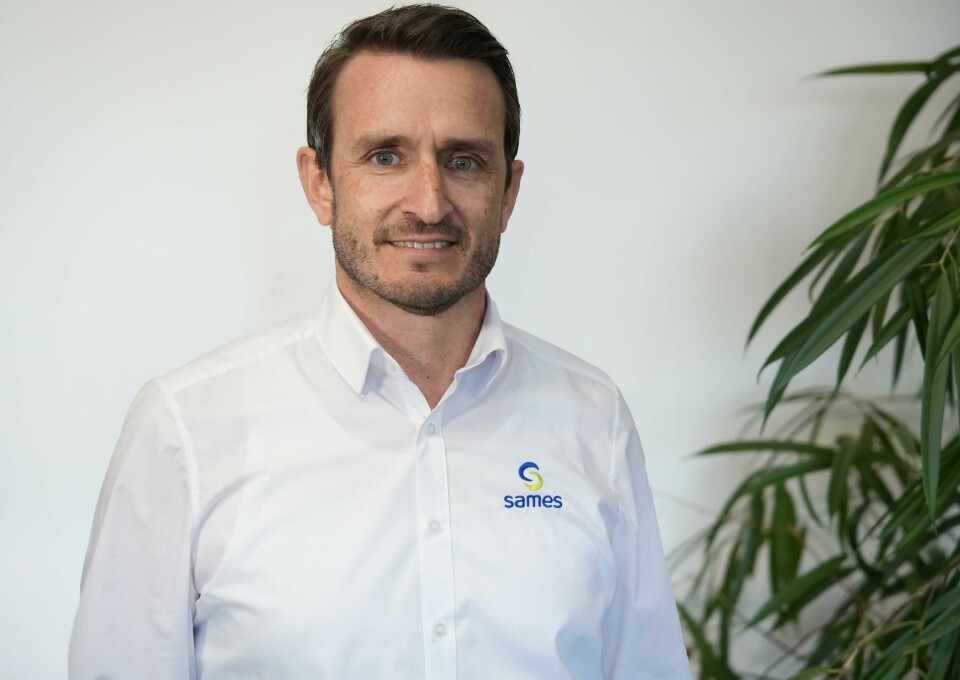
“We were trying to discover exactly how much pressure was needed to clean the surface, and then how much cleaning fluid we need to purge the felt during the cleaning process.“ Pauli says this was actually a major topic at the time. The question was, what kind of felt would be the best material for this particular cleaning process? “So there were numerous tests,” he says, “and in the end, we developed this system; which is now the same system that’s being deployed for the battery market.”
“The felt cleaning system developed during this project is still in use at the BMW iX’s automotive bodyshop, where it is used for cleaning the carbon frame which is the inlet between the front and rear doors,” says Carsten Müller, Head of Sales, Sames. “And this system has not only persisted, but has also been iterated and adapted for use in several new projects, some of which are, (I’m afraid to say), presently confidential. However, make no mistake; the system has several use cases and has widespread distribution.”
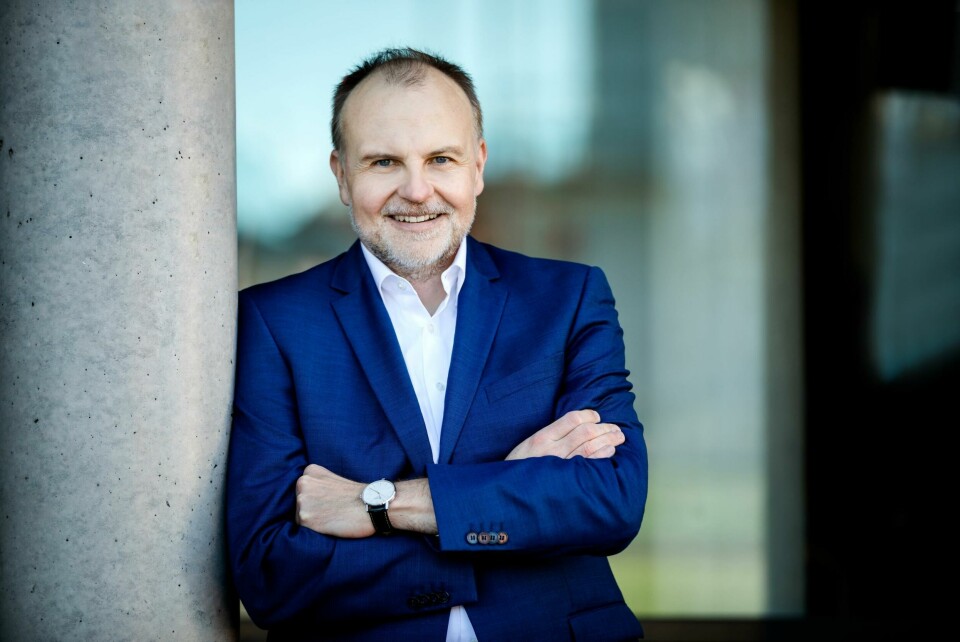
The challenges and solutions of seam pre-cleaning in automotive bodyshop
Pauli says that customisation is key for each project. Unlike ten years ago, when the pre-cleaning technology consisted of a single standard head, in a single shape with a single configuration, today’s customers require tailored solutions for varying part sizes.
“And so the challenge is that we must customise and tailor our system for every individual project,” he says. “Sometimes the customer will require a large felt to clean a large part, and sometimes a small felt for a smaller part. And this level of customisation is probably one of our biggest challenges.”
Another significant challenge Pauli points to, is that Sames’ systems require training for customer operations. “This necessitates numerous meetings to demonstrate to the customer how the system works and how to integrate it into their production system or cell,” he says. “Over the past few months, we have had many of these meetings to integrate our system into the customer’s production cell, customise it, and ensure that the shape of the cleaning head is suitable for the exact task at hand. We also, of course, need to ensure it does not damage the part or crash the application head. These are some of the biggest challenges we face”
Despite these challenges, Sames is able to successfully customise its systems to meet these diverse needs and integrate its systems into customers’ production lines.
“For each type of car, our customers typically require 60 to 120 gluing systems for bodyshop applications”
Mario Pauli, World Account Manager, High Viscosity, Sames
Ensuring consistent surface preparation for BMW
Consistent surface preparation is critical to ensuring adhesive application and bonding quality. Pauli explains that in these production plants, only a few people are responsible for hundreds of robots and automatic systems. “This makes it crucial for our customers to have a comprehensive monitoring system,” he says. “All of our systems are equipped with numerous sensors that continuously check if everything is running smoothly.”
If there is a malfunction, the issue is sent to a control centre; allowing the customer constant acess to the system’s status.
“Additionally, joint components are destroyed to test the quality of the impact of cleaning and robustness of adhesive bonding,” he says. By destroying the glue bead and measuring the forces, the client can determine if the bonding is of high quality or if there are any structural compromises. And the same principle applies to the cleaning process; “if the cleaning is not done correctly,” says Pauli, “the bonding process will also encounter issues.”
Mercedes Benz’s adhesive application profile: Glazing
But BMW is not the only major OEM known for utilising Sames’ adhesive technologies. Mercedes’ glazing systems also rely on Sames’ adhesive tech across glazing applications, particularly in terms of achieving the desired adhesive bead profile and ensuring a reliable bond. Pauli notes that Sames’ primary business is in bodyshop. “For each type of car, our customers typically require 60 to 120 gluing systems for bodyshop applications,” he says. “This means the technical standard for bodyshop is the highest in our business, with every detail documented and fixed, from screws and software to buttons in our Human-Machine Interface (HMI).”
”Sames contributes to Mercedes’ state-of-the-art factory in Sindelfingen. […] our systems play a significant role in glazing, particularly for components like the windshield and sunroof”
Carsten Müller, Head of Sales, Sames
Pauli says a few years ago, Mercedes realised that “since we have such a good standard for bodyshop, we should use it for glazing as well, as many parts are the same.” So Sames transferred the bodyshop standard to glazing and combined the two standards. “This approach saves our customers a lot of money because they only need one spare part for both techniques - and only require a single training session,” he says. This standardisation simplifies things for Sames as well. “We send just one type of control cabinet, one type of pump, and use the same hoses and cables, streamlining the entire process.”
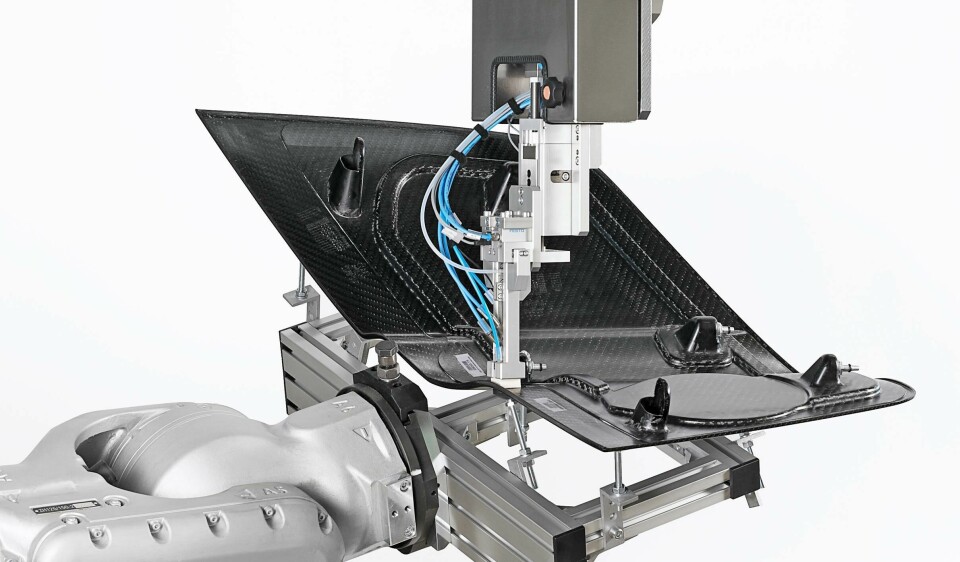
Müller says, ”Sames contributes to Mercedes’ state-of-the-art factory in Sindelfingen. Although Sames is not the sole supplier, our systems play a significant role in glazing, particularly for components like the windshield and sunroof.”
Digital production and process automation
Pauli explains that unlike bodyshop, glazing lines cannot afford downtime as there are no spare bodies to continue production. So Sames’ systems must have an availability rate of 99.6 percent or higher. The materials used for glazing are highly viscous, requiring powerful pumps and dozers to handle the large volumes needed.
“Our systems are designed for strength and longevity to meet these demands,” he says. In terms of the digital production network, Sames’ systems are fully monitored by sensors that check every aspect of the adhesive bead. External monitoring systems, such as cameras and lasers, ensure the diameter and shape of the bead are consistent. These systems are integrated into Sames’ control software, providing seamless monitoring and quality assurance.