Audi is transforming vehicle production with AI-powered image processing, eliminating errors and setting new standards for quality control and smart factory innovation
Artificial intelligence is accelerating transformation in automotive production. Audi’s Industrial Computer Vision is proving how AI-driven image processing enhances quality control, minimises defects and paves the way for scalable smart factory innovation.
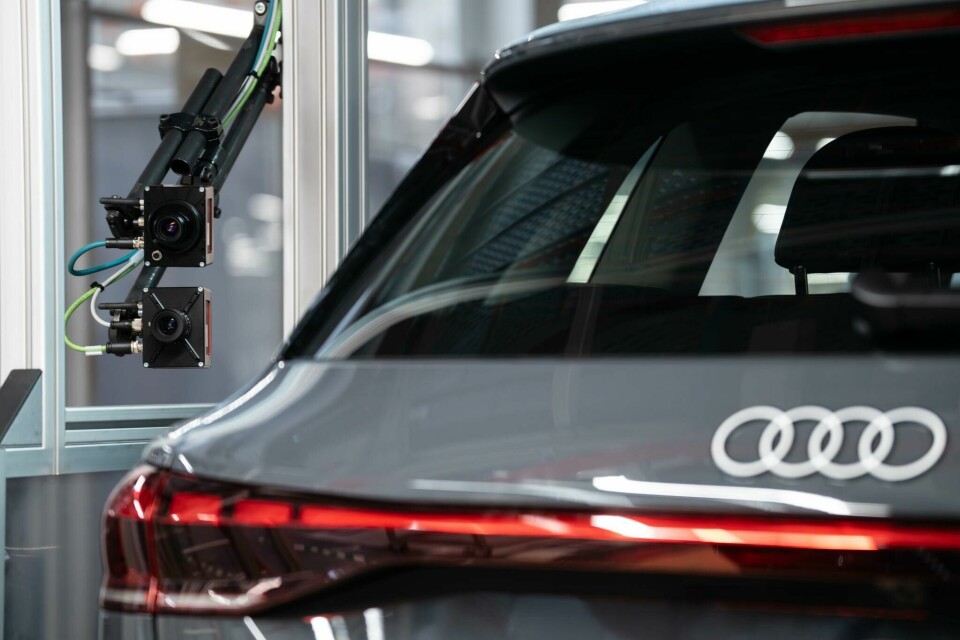
Artificial intelligence is changing automobile production faster and more radically than many people have previously assumed. With Industrial Computer Vision, Audi is showing how AI-based image processing eliminates production errors and enables new standards.
A study by the Bosch Tech Compass, for which more than 11,000 people were surveyed by the Society for Innovative Market Research in autumn 2024, confirms once again what has long been clear to all observers of the IT and technology industry: the importance of artificial intelligence is increasing.
”According to Bosch 67 percent of people worldwide already believe that AI will be the most influential technology in their country over the next ten years”
According to Bosch, 67 percent of people worldwide already believe that AI will be the most influential technology in their country over the next ten years. “Generative AI will influence the way we learn, work and cooperate - this will significantly change the procedures and processes in companies,” says Tanja Rückert, Bosch’s digital director and managing director, once again emphasising the inevitable.
The use cases in which AI optimises processes in the automotive industry are numerous and often have been tried and tested and established for a long time. For example, the technology is already actively supporting quality assurance at several car manufacturers’ locations. At the 2024 Assembly Congress in Munich, Wendelin Schmid, Head of Digital Technologies in Production and Logistics at Audi, gave a deeper insight into the role of AI-based image processing in vehicle production. Schmid emphasised the central role of innovation, especially in quality control as the last step in vehicle production.
Comparison of conventional and AI-supported image processing
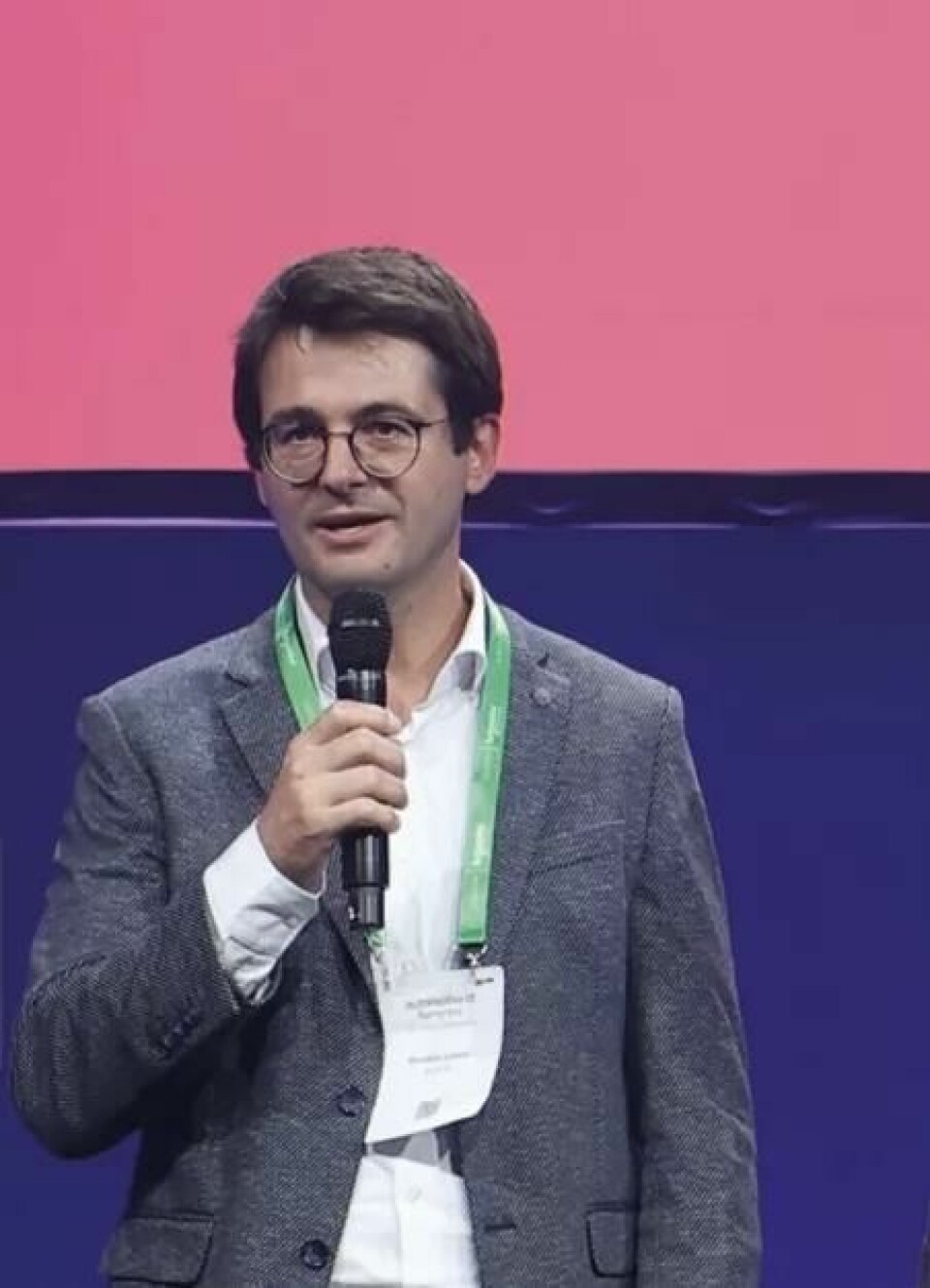
According to Schmid, compared to conventional image processing, AI-supported systems are used for more demanding tasks that require a higher level of trust. For example, checking vehicle-specific labels for correctness, position, content, orientation, freedom from errors and integrity, as errors in this area could have serious consequences, including the vehicle being blocked from the market.
“Our solution portfolio includes various technology variants that are selected depending on the requirements of the inspection task or the data volume and real-time capability. In the majority of cases, solutions managed by us make sense, but often the use of standalone purchased solutions is also the right choice,” explains Schmid. The expert also emphasises that industrial image processing has a fairly large field of application, in which it is all the more important to concentrate on implementing the right use cases.
Read more Artificial Intelligence stories
- The robots are here: How humanoids are changing auto production
- AI: Enhancing predictive maintenance in production lines
- Data-driven decision-making for sustainable automotive production
- Stellantis turns to AI tools and fast deployment to cut production costs and launch times
Standardisation as an important enabler of the Smart Factory
In the Industrial Computer Vision (ICV) project, Audi has been using AI-based image processing in production and logistics for several years. In keeping with the spirit of the Smart Factory, however, the work of the ICV team goes beyond developing the technology to detect anomalies: Schmid and his team secured first place in the Smart Factory category at automotiveIT ’s IT Team Awards 2024 for the concept development and cross-site scaling of AI-based image processing.
“It obviously took some initial effort to get an overview of the various solutions that are already in the production network. Another challenge was to evaluate the numerous existing technologies and possible applications in relation to previously defined standard solutions,” recalls Schmid. Before a technological development plan could be drawn up, including a corresponding blueprint for individual plants, extensive analyses had to be carried out.
”It is important that certain standards are adhered to - be it in the area of hardware, software or architecture”
Wendelin Schmid, Head of Digital Technologies in Production and Logistics, Audi
These, in turn, now serve as the basis for establishing ICV solutions as a standard on the greenfield from the outset or for gradually integrating them in the brownfield. According to Schmid, the latter requires active communication and central support in particular in order to clarify the advantages of the new standard and ensure successful implementation.
What’s next for Industrial Computer Vision ?
“This collaboration was a union of motivated and committed colleagues who worked together towards a common goal. The different perspectives of the team members complemented each other excellently, and it is particularly valuable to combine the different perspectives from different specialist areas and thereby develop innovative solutions,” comments Schmid. “However, it is important that certain standards are adhered to - be it in the area of hardware, software or architecture.”
Among other things, automatic training pipelines with synthetic data are planned. The focus is on expanding capabilities, optimising performance and reducing the integration effort of industrial computer vision products. “In addition, we also want to develop standardisation and modularisation within our solution portfolio because we can leverage corresponding synergies from this. The path to this leads via an ICV architecture defined by us, in which the interfaces and protocols to be used are specified in order to create a consistent overall system,” adds the Audi expert.