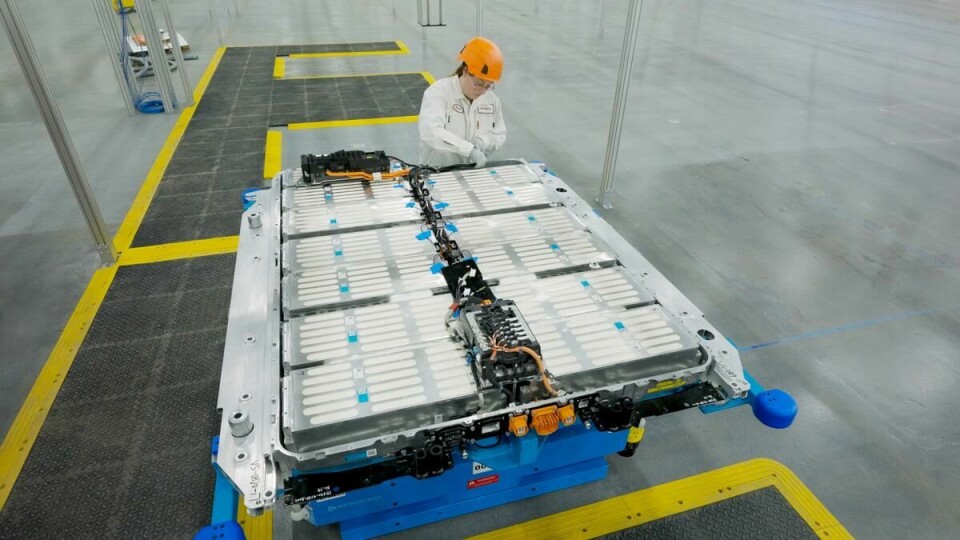
Honda North America’s big investment in flexible manufacturing for EVs, hybrid and ICE vehicles
Honda invests $1 billion in retooling its Ohio manufacturing plants to build ICE, hybrid, and EV models on same production line. New technologies being introduced include megacasting, CDC and friction stir welding.
This investment supports the creation of an EV Hub in Ohio, with Honda reimagining its manufacturing environment, enabling the production of internal combustion engine (ICE), hybrid-electric, and battery electric vehicles (EVs) on the same production lines. This transformation not only allows the company to adapt to shifting market demands but also significantly improves the working conditions for its employees while enhancing sustainability, says Honda.
A flexible manufacturing future
A key feature of Honda’s EV Hub is its ability to produce multiple types of vehicles on the same assembly line. Bob Schwyn, senior vice president of Honda Development & Manufacturing of America, highlighted the importance of this flexibility. “The Honda EV Hub provides us with the adaptability to produce ICE, hybrid-electric, and EV models on the same lines, allowing us to react swiftly to changing customer needs and market trends,” Schwyn explained.
The company’s Marysville Auto Plant (MAP), East Liberty Auto Plant (ELP), and Anna Engine Plant (AEP) are at the heart of this transition. These facilities have undergone significant upgrading and retooling, with new technologies and processes being introduced into the production operations.
MAP, where Honda started vehicle production in the US over 40 years ago, has undergone extensive modifications to support the flexible production approach. This has involved the consolidation of production lines with the removal of Line 2 to create a single, more efficient production line that can accommodate EV, ICE, and hybrid vehicles. Honda says this reconfiguration also creates a more versatile space on the production line for associates to work and more efficient parts delivery.
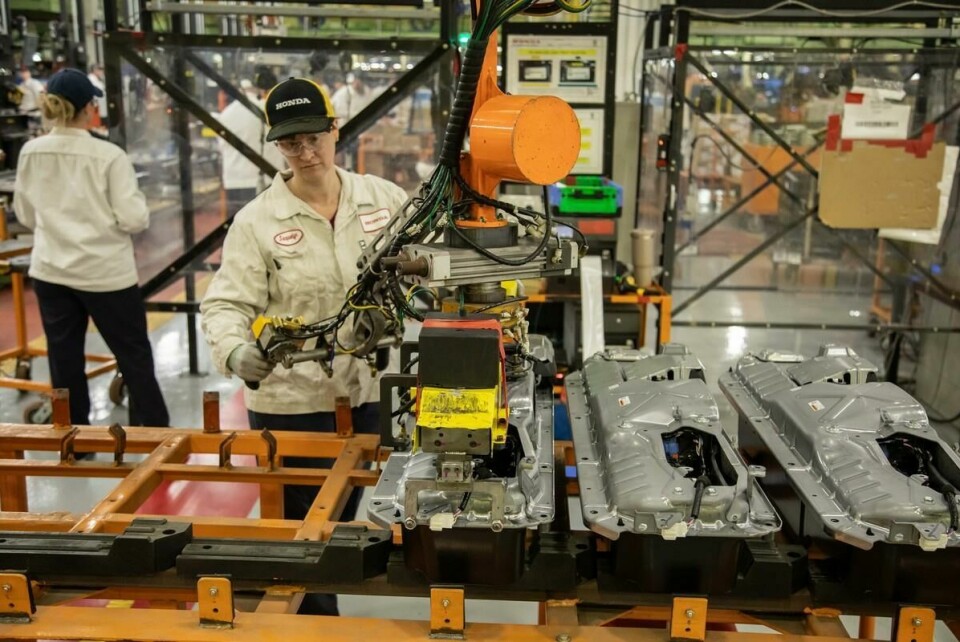
Responding to increased demand for hybrid vehicles Honda has created a new hybrid battery assembly area
Dedicated battery assembly and flexible pack installation
A dedicated workspace has also been established to assemble battery packs for EVs. The packs will be assembled with battery modules supplied by the joint venture battery facility, L-H Battery Company, and battery cases megacast at the Anna Engine Plant. These battery packs for midsize and large vehicles will be used for EV production at both MAP and ELP. The company notes that this battery pack assembly will use the longest automated guided vehicle (AGV) line at Honda.
An important part of the flexibility requirements sees the integration of the battery packs into the EVs being performed with minimum disruption to the production flow, especially when assembling multi-powertrain variants on a single line. Honda says it has established a new dedicated area on the production line that allows for installation of battery packs into EVs with ICE and hybrid vehicles passing through without stopping.
In addition, responding to increased demand for hybrid vehicles Honda has created a new hybrid battery assembly area, which is located closer to the installation area on the vehicle assembly line.
MAP has also seen the upgrades to its welding operations with the retooling one of the plant’s two weld lines. Again, flexibility is a key requirement, and this has involved installing new weld robots and technologies to enable welding both EV and ICE bodies on the same line. This includes changes to secure the EV battery case in the vehicle floor, which requires welding side sills to the floor comp just for EV models.
The welding upgrades also see the introduction of an important new process, Constant DC Chopping (CDC) welding, being used for the first time at a Honda plant. See more on this below.
Advanced quality control for software-defined vehicles
MAP’s Vehicle Quality Department (VQD) has been expanded, to incorporate enhanced quality inspections and include more human-friendly functions. This involves a new optical aiming station improvements to check the alignment and functioning of new safety and connectivity technologies in EVs and the future software-defined vehicles (SDV). It also prepares the plant for the radar and optical aiming verification required for the new L3 automated driving features on Honda 0 Series vehicles.
Cutting-edge manufacturing processes
The Anna Engine Plant (AEP) is also introducing new, advanced production technologies support Honda’s transition to EV production. The plant will produce EV battery cases using a newly installed aluminium megacasting process. Honda is building on AEP’s existing experience and expertise in casting aluminium parts to produce these new components that will form the main structure for the floor of Honda and Acura EVs.
Six, 6,000-ton high-pressure die cast machines, supplied by Bühler Group, will produce the cast cases for Honda’s Intelligent Power Units (IPUs). The IPU case will contain the EV battery module and serve in a structural role as mentioned. Bühler notes that it has also installed a megacasting cell at Honda’s site in Tochigi, Japan for R&D purposes. Honda is conducting controlled experiments under different casting conditions to ensure and improve the quality of their end products.
A Honda spokesperson says: “The R&D cell makes it possible to test process innovations and newly developed parts quickly and efficiently. This rigorous testing allows us to optimise our processes. The expertise and experience that we gain in Japan will be shared across our production network in North America to support our electrified future.”
Honda has opted for the megacasting (6000-ton) approach here as opposed to the 10,000-ton monobloc gigacasting method, as the former allows for different cases to be manufactured, in separate parts, based on the various battery pack specifications. This enables Honda to produce cases in two different sizes for midsize and large EVs – with one-half of the case common to each size.
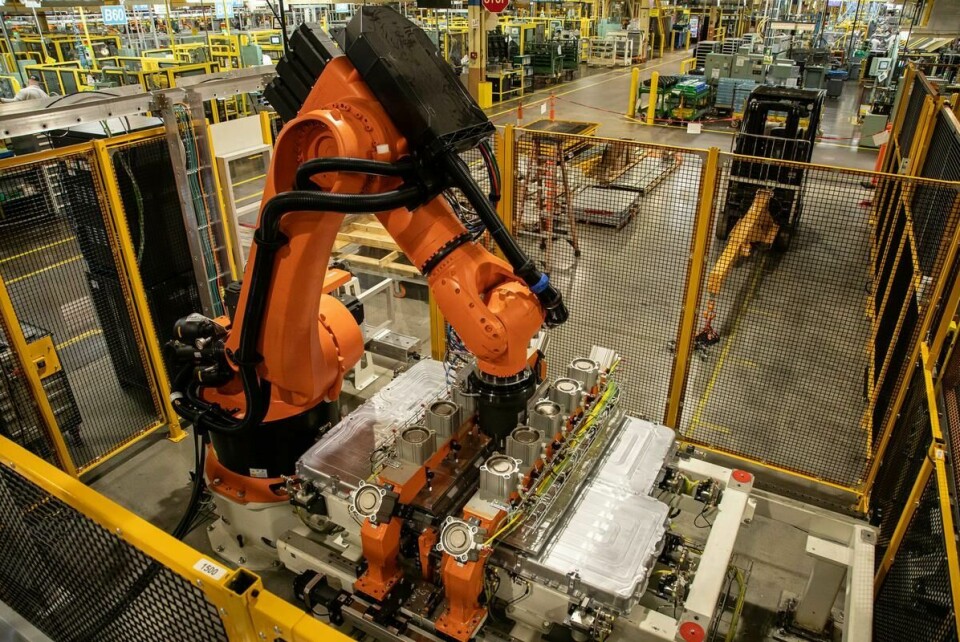
The two-part megacast battery casings will be joined using another advanced technology, friction stir welding
These two-part casings will be joined (butt joint) using another advanced technology, friction stir welding (FSW). This process will also be used to attach the aluminium water jacket (lap joint) which is stamped at MAP.
Honda already has considerable experience with this joining technology. In 2000, it was applied to the aluminium wheels of off-road four-wheelers, and in 2012, it was used for the first time to join steel and aluminium materials for structural parts of mass-produced vehicles. The company has also developed a new method to shorten this joining process. In conventional FSW, machining is required before the joining steps to cope with gaps and misalignment between parts and any waviness on material surfaces. In addition to the higher precision of parts provided by the megacasting technology, Honda says it has developed jigs and tools that can apply FSW directly on the material surface of aluminium parts without performing machining processes, except on butt surfaces. This has removed the need for three machining processes and still delivers high-quality joining in a shorter process.
New quality control technology and process steps
Ensuring the high-quality standards for these components are being met, AEP will use Photogrammetry, employing a new multi-camera machine to quickly and accurately visually analyse the quality of each battery case. Photogrammetry is the science and technology of obtaining reliable analysis of physical objects through the process of recording, measuring and interpreting photographic images and patterns and this will be used in two locations to achieve 100% quality confirmation.
Following the die-cast process, four machines equipped with 90 cameras will visually analyse the part shape to ensure 100% quality of the surface of the battery case surface. After final assembly and prior to shipping of the case to the assembly plants, two machines equipped with 120 cameras will visually analyse each case to ensure its mountability to the vehicle frame at MAP and ELP.
East Liberty Auto Plant (ELP) retooled for EVs
ELP has also been retooled to accommodate Honda’s next-generation EV production. This includes a new paint department with reinforced carriers for heavier EV bodies and expanded phosphate and E-coating.
The reinforcement of drop lifts, conveyors, and support beams is carried over into the assembly area, with these also being strengthened and improved to handle the additional weight of heavier EV models and offer the flexibility to produce hybrid-electric and ICE models. AGVs are also being deployed on the final assembly line to provide a stronger, larger body carrier for EVs.
To manage the EV models a battery pack mount mezzanine has been created to enable these vehicles to disengage from the main assembly line for EV battery pack installation. Once the battery pack is installed, the EVs rejoin the shared assembly line along with ICE and hybrid-electric models.
A new building will be constructed at ELP to house the expanded VQD quality control team. In line with the changes at MAP, the new operation will include a new optical aiming station to check the alignment and functioning of new safety and connectivity technologies in EVs and the future SDVs. Honda notes that the new building provides more space for VQD associates and for vehicles, to create an improved flow to easily conduct quality checks on 100% of the vehicles produced at the plant.
The future of Honda manufacturing
Honda says this investment in creating highly flexible and efficient manufacturing operations will support the start of production of the Acura RSX EV in late 2025, followed by models based on the Honda 0 Saloon and Honda 0 SUV prototypes unveiled at CES 2025.
The company notes that this investment in Ohio is not only about producing the next generation of EVs but also about pioneering a new way of thinking about automotive manufacturing. And in establishing the Honda EV Hub, the company is creating a model that can be replicated across North America and beyond.