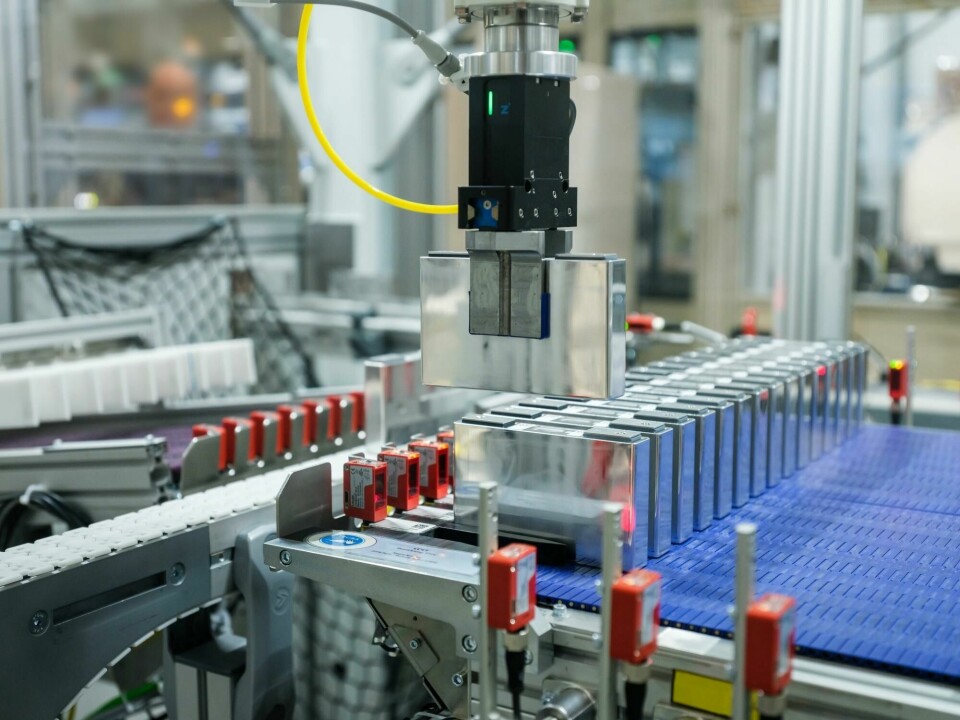
European battery production needs greater speed and agility
Exhibitors at this year’s Battery Show in Stuttgart shared insights into EV and battery production challenges and how the industry needs to adapt with greater speed.
While the media headlines report on a slowing transition to electric vehicles (EVs) there was no sign of any lack of pace in the ongoing developments and innovations that are vital to move to e-mobility. AMS spoke with several leading suppliers offering solutions in the key areas of materials, battery enclosures, digital tools and automation.
Scaling up production of EVs, motors and batteries has seen a lot of investment by OEMs and tier suppliers, but this process has been subject to the market headwinds mentioned above. For the automation developers, suppliers and integrators there has been no slowing down in supporting customers managing changes in volumes.
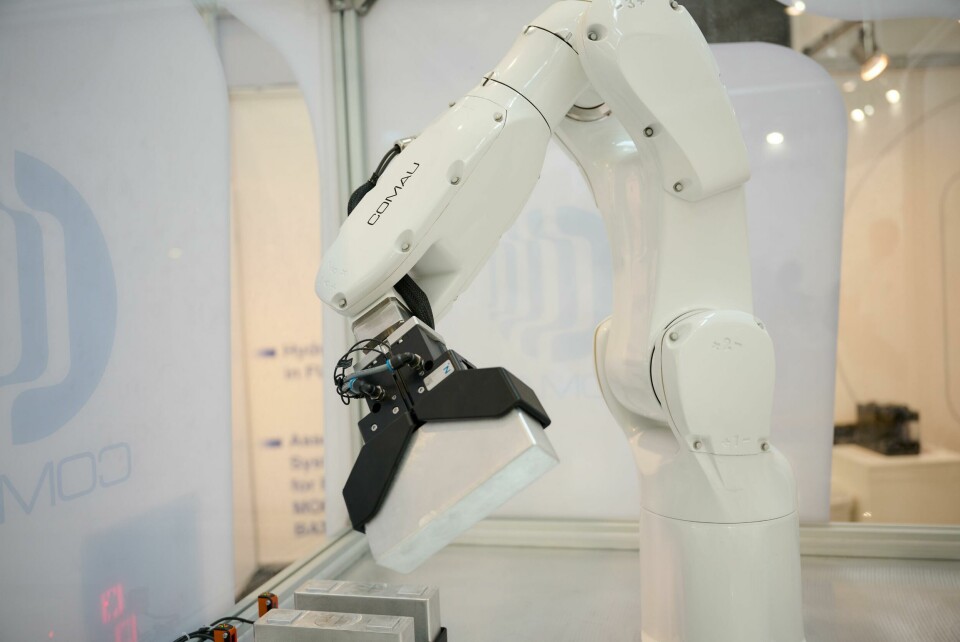
Taking a flexible approach to automation
Comau has been working with a range of vehicle makers on EV production lines covering vehicles, e-motors and batteries, and has itself been investing in a series of new competence centres to meet these new demands. Head of the company’s e-mobility competence centre, Giancarlo Tronzano noted: “Where possible we use a simultaneous engineering approach throughout the development process, starting with the preliminary stages of establishing the feasibility of the project. They ask us for support in understanding the scale of the investment, the size of the project, the technologies needed. Working in this way, starting at the very early stages, we can support in defining the processes and sometimes writing the scope of supply they need to go to market.”
This simultaneous engineering approach is something AMS covered earlier this year with a feature on Comau’s work with Chinese EV manufacturer NIO. This focused on e-motor production and cutting time to market through very early involvement.
The pace of change in the industry is something that continues to be a big challenge and while vehicle makers are looking to regain some stability in markets and production output this is unlikely to be realised any time soon according to Rockwell Automation’s industry strategy and marketing manager, Dominique Scheider. He noted that in recent year OEMs had initially looked to buy-in the more complex EV components, mainly the battery cells, from outside sources, but that with the drive to reduce costs and the growing focus on more control over supply and production, the car makers are now developing in-house battery production operations, building dedicated development centres and pilot lines.
At the same time the OEMs must always look to the latest technologies in both product and production. Scheider stressed this puts an emphasis on the need for agility in production systems and equipment. Noting the challenge of time to market for new vehicle platforms, Scheider observed that OEMs are now working in a much closer partnership with suppliers, in some cases starting with a ‘blank sheet of paper’ approach to the development the necessary production process and being involved much earlier the vehicle development.
He also highlighted that a big demand from customers was for highly adaptable production lines and systems. With volumes EVs proving harder to predict and vehicle platform lifecycles becoming much shorter, it is now too easy for production operations to become obsolete.
“I like the term intractable because no one knows really what a battery will do or how long it last in different scenarios such as operating climate, driving use case, or what the optimal charging strategy is”
Dr. Richard Ahlfeld, Monolith AI
Leveraging the potential of digitalisation
Intractable physics is a favourite keyword of Dr Richard Ahlfeld, CEO and founder of Monolith AI. Artificial intelligence is a much-vaunted digital tool and in this case, Dr Ahlfeld was referencing its application to battery cell production and his perspective on the ‘unknowns’ in battery cell performance, of which there seem to be a lot:
“I like the term intractable because no one knows really what a battery will do or how long it last in different scenarios such as operating climate, driving use case, or what the optimal charging strategy is. And that is because the electrochemical reactions that take place within the battery are so complex, non-linear and convoluted that the only way you can really figure out what the battery is going to do after two years of being used by all your customers, is buying a thousand batteries, putting them into a test lab, and having these test stations simulate two years of usage.”
He noted the cost and time involved in doing this, pointing to the levels of investment being made by OEMs in test facilities. He also highlighted another challenge; the huge amount of data produced in these tests. Dr Ahlfeld attributed this to way that European and US OEMs in particular, approach battery testing, that the lack of experience in this area has seen an ‘over engineering’ of test processes.
“They will just test way too many different cells in different conditions, because they don’t know exactly how to design the optimal test plan.”
For Monolith this is where AI can be an important tool, to not just manage terabytes of data but to ‘learn’ what tests are needed and perhaps more importantly which tests are not necessary. Dr Ahlfeld noted that this could also support faster speed to production for those setting up cell production operations and help reduce the high scrappage rates currently being experienced around production.
Managing battery pack materials
The need for sustainable materials in the battery assemblies also loomed large in conversations and was a key topic for many of the sealants, adhesives and filler suppliers exhibiting at the show. While much has been covered on the thermal and adhesive performance requirements for the battery pack assemblies, there is now a big focus on de-bonding these materials, particularly to support battery recycling processes.
As we’ve seen with the automation developers, a common development across system, equipment and materials suppliers has been to establish dedicated teams or technical centres to manage EV related projects, and materials science company Dow is no exception. The company has established its Mobility Science unit to support OEMs and tier suppliers and Jon Penrice, president of Dow Mobility explained the company’s approach to this:
“We set up Mobility Science to provide a one stop shop for the automakers and the tier structure, who are not always the experts in materials and their properties but understand what they want to achieve.”
Penrice highlighted another interesting development in how the business had restructured its R&D teams, describing how they have become more application focussed:
“We used to do our business development and R&D based on individual product lines, polyurethane, silicones, plastics. But now we’ve consolidated them all under one platform called mobility science, which really improves the collaboration and the sharing, because often now a project can require a hybrid chemistry and we could have two or three different chemistries being developed. So, we need the teams to have battery knowledge, not just polyurethane knowledge or silicon knowledge.”
This example highlights an important trend we see across the industry; the breaking down of departmental silos and the better sharing and utilisation of experience and competences within businesses.
Something else we’ve been hearing more about is high throughput research, this was mentioned several times in conversations and interviews, and highlights the growing focus on speeding development of systems, materials and products without compromising quality or performance. However, as previously noted by Dr Ahlfeld, current testing and process development is in some cases ‘over engineered’ leading to more complexity and lengthening time frames.
Penrice explained Dow’s approach to this: “We are applying something we all predictive intelligence, which is bringing AI to support the choice of [chemical] combinations you make, as both deciding the starting points of the different materials and property set that you’re looking to achieve is extremely complex.
“The traditional way of doing this is essentially informed trial and error, which is a good experience. People putting together a formulation they think will work, testing it and then going back and optimising it because it was close, but not close enough. Now, the predictive intelligence tool will do that automatically. We have taken all our formulations and put them into the database against the properties that they develop, this is our high throughput research, which means rather than humans running experiments, we have a robotic system which can run thousands of experiments simultaneously, so you are significantly faster in terms of getting to the result that you need.”
Another big talking point across all the materials suppliers was sustainability. For the vehicle makers and tier suppliers the entire battery assembly (cells, enclosures, electronics, sealants, adhesives, gap fillers, etc.) has created a whole new challenge around end of life and recycling. So, while the initial phase of development for these components was focussed firmly on optimising the performance of the vehicle’s battery, sustainability has now become a major consideration in the design, materials choices and manufacturing for these components.
For Dow developing materials that will fit into a circular economy approach is an import area of focus. Penrice highted the challenges in this:
“Making a circular economy work means getting a second life from our materials. Traditionally what our technicians are good at is taking some molecules, building those into a system that is fit for purpose. But now we’ve layered on top of that challenge to do that with materials that are inherently lower carbonous, and then build those systems in a circular way, to reclaim those materials and put them back into the production cycle. Our belief is that 80% of it will need to be what we call advanced recycling, which is essentially starting again. You take it back to the molecule, and you make a new material with it.”
“You need to sit at the design table, and I see it as a positive challenge to develop over two to three years, good solutions which are validated with the customer, minimising any risk at later stages of the vehicle project”
Andreas Lutz, DuPont
Similar considerations were voiced by Andreas Lutz, director Global Technology Adhesive & Sealants at DuPont. Lutz also noted the need for speed in the development of materials related to battery assemblies and the need to invest in dedicated teams to support EV production:
“The battery world is very dynamic, and we are seeing B, C and D sample stage changes are already coming. If you want to support your customers, you need to be agile and react in the right time and at the right speed, without losing quality.
“And to support this DuPont has invested a lot of automotive expertise in recent years to become very agile in our work with customers.”
Echoing the comments from Comau, Lutz highlighted the importance of being involved in vehicle and component design at an early stage in the process:
“You need to sit at the design table, and I see it as a positive challenge to develop over two to three years, good solutions which are validated with the customer, minimising any risk at later stages of the vehicle project.”
Digital tools also play an important role for DuPont in speeding up the development of new formulations, according to Lutz. Simplifying manufacturing processes (another important trend) is another area of focus for the company, looking into the curing kinetics of adhesive materials that can offer manufacturers long open time, fast cures, the ability to shape the adhesive profile, which gives more flexibility in manufacturing.

De-bonding adhesives in EV battery enclosure applications
There were several goals all the materials suppliers referenced during the meetings and high on the list was de-bonding. This was also referred to as the ‘holy grail’ of adhesives for battery packs, encompassing the need for easy removal of the material at the end of the battery pack lifecycle without compromising the performance levels required over the component’s service life. At challenge that has become a major focus of development.
Holger Schuh global senior manager for Thermal Technologies & Equipment Partners at Henkel, noted some of the considerations relating to this requirement:
“A key requirement is that it’s still structurally relevant, so you cannot compromise on the bonding performance. But you need to make sure that, for example in eight years’ time, whatever de-bonding mechanism we built-in will still work, so, we rely on stress testing, accelerated testing, to see what happens to the material’s performance across different use and environmental scenarios. This is challenging because we don’t have long term experience or data on a mechanism’s performance, say over 20 years. What I’ve seen in the last 20 years in automotive, is that the best is really the feld testing, but we don’t yet have this for e-mobility.”
While the recyclability of plastic components has advanced, there remain challenges. With a growing focus on creating circular economies within production operations, plastics need to develop to go beyond being recycled for alternative (outside automotive) applications, according to Trinseo’s CTO, Han Hendriks. He emphasised the need for plastic automotive components to be processed back into a raw material for continued production of those components.
Hendriks shared some examples including polycarbonate (PC) headlamp units and EV battery tray covers. He noted to company had developed a dissolution process where the scrap components (in this case headlamp units) underwent what he described as a physical recycling process rather than a mechanical process. This breaks down the various parts and separates the PC or ABS materials for reuse. Hendriks noted the potential for this process to support a circular approach to recycling:
“This dissolution process ‘upcycles’ the quality of the waste, so you can use low-quality waste and turn it into a new headlamp. Plus, the CO2 reduction versus producing virgin quality material is 70%.”
Bringing EVs back into focus, the company has been developing and supplying thermoplastic parts for battery enclosures. This a component of EVs that continues to see a lot of development as battery cell chemistries, formats and approaches to integration change. As well a having good thermal resistance properties Hendriks pointed to the material’s recyclability as another important feature.
“The OEMs that we speak to know 2030 is around the corner. They must achieve 25% circularity for the entire vehicle. The battery casing lid is a 20kg part. So, if that part can be 50% circular, it’s a good contribution to their targets.”
In common with other materials suppliers Trinseo has restructured its technical teams and data management to support the transition to e-mobility and sustainable production operations. According to Hendriks the company previously used four separate lab information management systems, known as LiMs, to store all the data from experiments and formulations. He noted that the process had become too fragmented. So, the company has started a process to centralise these operations using a single LiM that features AI functionality, which it is currently rolling out across its network.
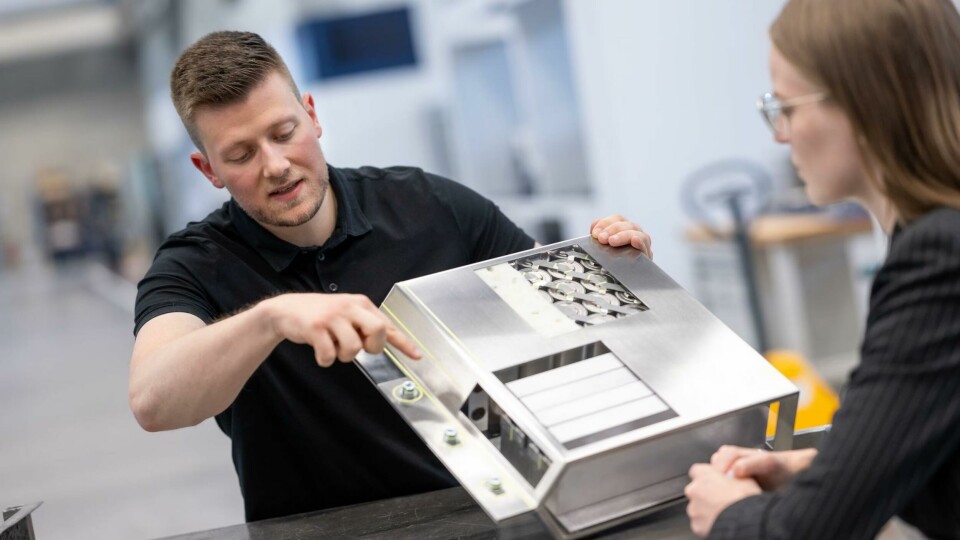
Making experience count
Other companies leveraging their respective expertise to support the transition to e-mobility include PPG and Trumpf. The coatings producer provides products across a number of industries and has successfully transferred some of the knowledge and experience gained to applications in automotive EV production. These developments have focussed on advanced materials and coatings for EV battery packs with PPG venturing into thermal management materials, such as conductive gap fillers and adhesives. In addition, the company has as developed dielectric coatings to insulate components such as battery cells, metal module housings and pack shells. PPG’s global director for product development, automotive coatings and mobility, William Brunat, commented that these materials must meet a complex range of criteria from insulating properties and thermal management to structural bonding and fire retardance. Although well known in the automotive industry for its vehicle paint finishes, the company has been able to leverage its extensive experience and expertise from its industrial coating side.
Trumpf is another company, well known in the automotive sector, that has been leveraging its technology for battery production applications. Johannes Jakob Buehrle, the company’s director for global business development – mobility, noted some of the areas where Trumpf had seen new EV related applications for its laser technology, including drying, welding and cutting. Buehrle highlighted drying applications as one that had been derived from mobile phone technology:
“The drying process is a roll-to-roll process with speeds from 60 to 100 meters per minute, and it’s a very CapEx and OpEx intensive process. And the process systems can be up to 100 metres in length using an electrical gas oven with conventional convection technology as the heat source.
“Our solution is to use vertical emitting, infrared lasers to irradiate a big area to dry it. These are micro lasers operating at a very low power level, and these are commonly used in mobile phones, for telecommunication, for sensor technologies. We stack them together creating a single unit that features hundreds or thousands of tiny little lasers to irradiate the surface.
“We have done trials with customers, and we have this technology in the implementation phase. This has allowed the customer to reduce the footprint of oven by 60% but producing the same drying results.”
The company also sees opportunities for lasers in battery production in the more familiar areas such as welding and cutting. Trumpf has been developing its welding processes to meet the requirements for attaching cooling blades to the battery pack, and at the other end of the battery’s lifecycle, offering precision cutting to dismantle components for recycling making it easier to separate the valuable materials. Buehrle revealed another interesting area of development:
“We have found a way to separate active material from the carrier foil. Today they are just mixed, they grind it and then they separate the metal, the aluminium copper from the active material and try to recycle part of it. Our approach is to use a special thermal laser, that delivers high energy, short pulses to shoot off the active material from the carrier foil, however this is still under development.”
New approaches to meet new challenges
What becomes increasing clear is that like the vehicle makers, suppliers, across the spectrum of systems, materials and equipment, are also in transition, in this case rapidly shifting their role from supplier to technical partner and solution provider. The transition to EVs continues to present challenges in managing new technologies and scaling production and while the supplier sector can leverage much of its experience and expertise, it must also find ways to speed product development and delivery, while also being agile enough to quickly adapt volatile markets and customer demands.
Some definite highlights include making automation truly adaptable, speeding development processes with AI increasingly providing vital support and sustainability taking big steps towards a circular economy in the automotive industry. However, although the transition to e-mobility is now well underway, some of the experts observed that: “This is not the end, we’re still at the beginning.”