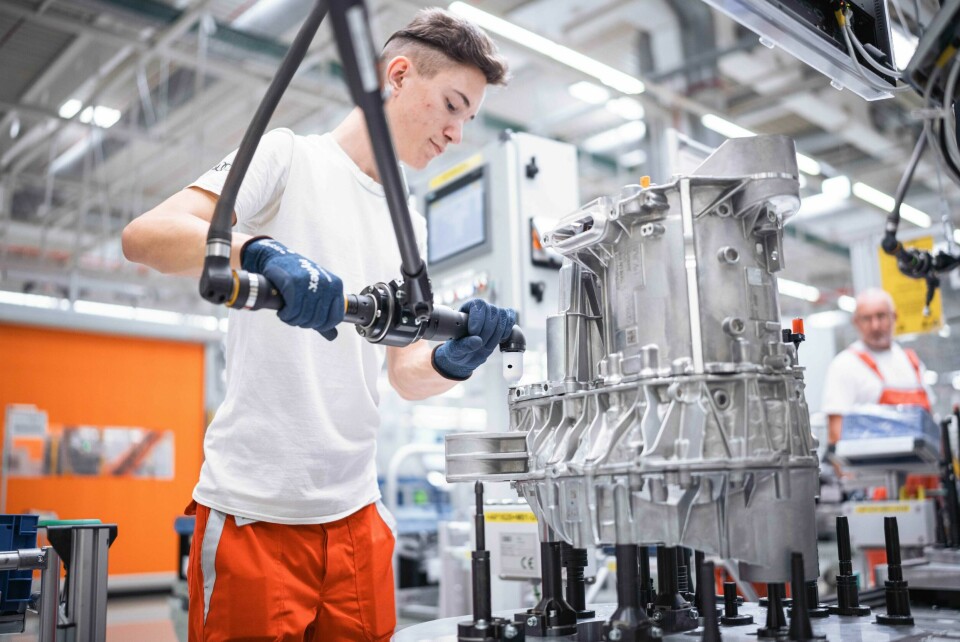
Audi’s electric hopes rest on Györ
Györ plays a special role in Audi’s production network. Just as important as the approximately 176,000 vehicles produced each year are the almost 1.7 million drives produced. Now Györ must make the transition to electromobility.
Audi started production in Györ in 1998 with the series production of the TT Coupé, followed by the TT Roadster models a year later. At the beginning, painted bodies were delivered from Ingolstadt and only assembled in Györ. However, with the opening of the new vehicle plant in 2013, a new era began for the plant: the press shop, body shop, paint shop, assembly and the associated quality assurance were all located at the Györ site, which has now become a full-service plant.
“Series production of the Audi Q3 models began in 2018, which was a big step for us, as this was the first SUV model in Györ that far exceeded the previous TT production in terms of unit numbers,” says Zoltán Les, Board Member for Vehicle Production at Audi Hungaria. “Last year we produced more than 171,000 cars - never before have so many cars been built in our plant in one year.” With around 94,000 units – almost a third of which are hybrid vehicles – the Q3 will continue to account for the lion’s share of vehicle production in Györ in 2023.
One year after the SOP of the Q3, production was expanded to include the Q3 Sportback, the RS Q3 and the Q3 Sportback. The same year, the Q3 and the Q3 Sportback followed as mild hybrids, and in 2020 the plug-in hybrid variants of the vehicles. With the start of production of the Cupra Terramar in 2024, Györ will become Audi’s first production site to manufacture across brands.
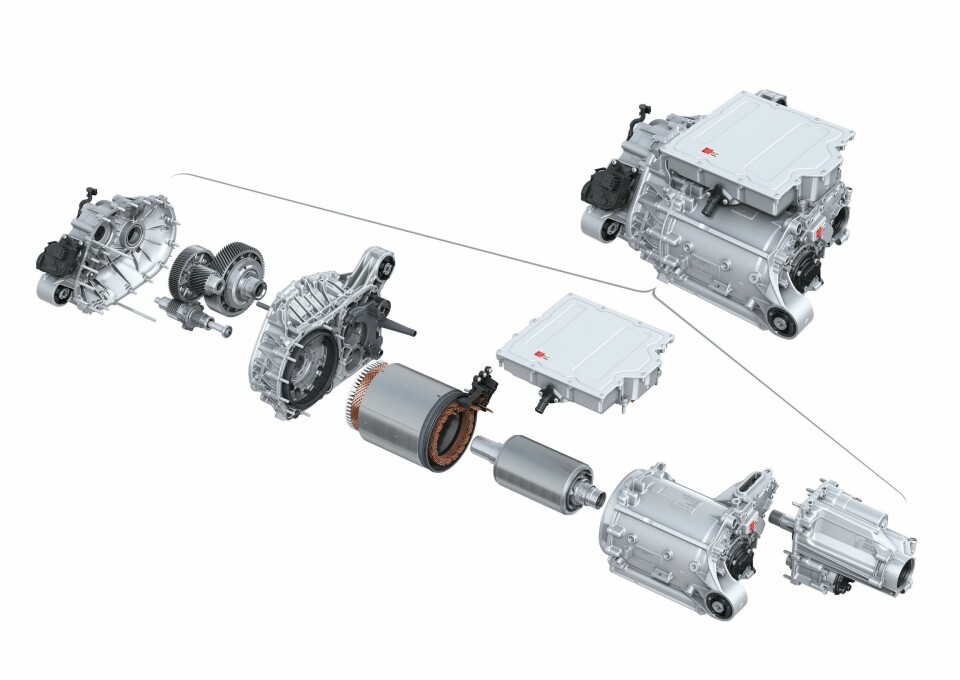
Györs’ focus is on the drives
In 2023, the plant in northwestern Hungary produced a total of 1.66m drives for a total of 35 Volkswagen Group production sites – 1.16m of which were three- or four-cylinder petrol engines and diesel engines. In addition, there are 19,734 five-cylinder petrol engines and 277,0081 six-cylinder petrol engines, 78,905 six-cylinder diesel engines and 6,216 ten-cylinder engines. In addition, 114,058 electric axle drives were built in Györ. These electric motors are installed in the Audi Q8 E-Tron, Audi Q5 E-Tron and Porsche Macan.
In the future, Hungarian production will focus primarily on Premium Platform Electric (PPE) drives. The machines will initially be used in the Q6 E-Tron series produced at Ingolstadt. Audi has created a total of 15,000 square meters of space at the site to produce PPE drives. In addition to drives, the corresponding stators and transmission components are also manufactured here, and axles are assembled. Audi has put three new lines into operation to manufacture the systems. “The production line for stators has 28 work steps, and transmission production has 15. “More than 190 individual assembly steps are required for axle assembly,” explains Csaba Imre Benke, Head of the E-Drive Product Segment in Györ and responsible for the production of PPE drives.
A total of around 700 employees are involved in the production of the systems; in a three-shift operation, 2,000 electric motors can be built per day. In addition to the electric motors for the PPE, Audi also manufactures the drives for the Q8 E-Tron in Györ. In addition, an additional production area is currently being set up for the electric motors for vehicles based on the MEBeco (Modular Electric Drive Kit) from the Volkswagen Group.
PPE increases the complexity of manufacturing
The new form of drive for the PPE has significantly increased the complexity of production, explains Audi expert Benke. “Due to the technical differences, the lines look completely different. The PPE alone uses 15 automatic bending machines for the three-dimensional hairpin winding and the subsequent laser welding of the ends in two other systems. 140 meters of copper wire are processed per stator. 235 laser welding processes are necessary.” Since there are fewer screw connections but more pressing circumferences compared to combustion engines, a higher level of automation can be relied upon.
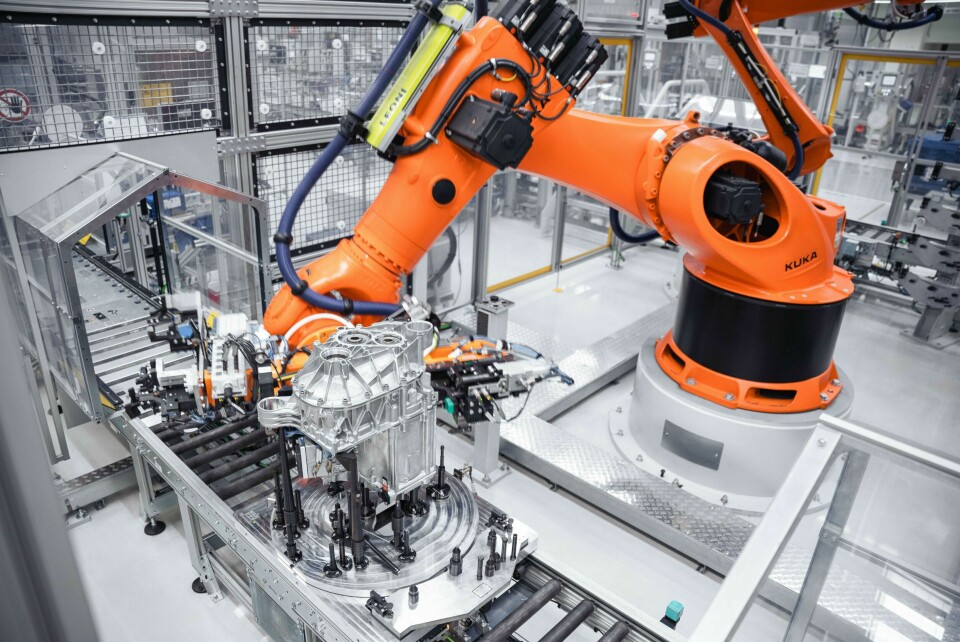
The changeover is not starting from scratch, emphasises Benke. Since 2018, the site in Györ has already built 500,000 electric motors – creating a wealth of experience that the manufacturer is now benefiting from. Nevertheless, employees also must be trained for the new systems. Around 20 days of training are required per employee, says Benke. The qualification is built up at different levels. “At the first level, there are relatively simple basic training courses lasting two hours for employees who work alongside the line,” says Benke. “The work here is not significantly different from that required to build a combustion engine.” The highest level of training is that of the responsible electrician, which can take up to three months. “For this, we mainly rely on existing staff from the combustion engine world. In Györ, around 2,000 employees have been trained in electrification since 2022,” explains Benke.
Györ goes beyond climate neutrality
As part of the 360factory strategy, Audi is not only focusing on automation and digitalization at the Györ site - sustainability is also a focus of its efforts. The plant has been carbon neutral in its production operations since 2020. This is made possible using industrial geothermal energy and the largest photovoltaic roof length in Europe. But they are not resting on their laurels: In June 2024, Audi Hungaria signed an agreement with the energy company Smart Solar for further expansion. In addition to the 160,000 sq. m of solar panels in the logistics centre, almost 85,000 sq. m are to be added to the assembly hall and 75,000 sq. m to the plant’s green areas. By using “innovative solar tracking technology with active inserts on both sides”, the amount of energy generated on the same area is almost 30% higher than with conventional systems, according to the carmaker.
For vehicles based on the PPE, DB Cargo also delivers the engines built in Györ to Ingolstadt in a CO2-neutral manner. “Flexibility between rail and road is also important. Since April, we have been using a ‘green’ train with an innovative loading concept for logistics transport between the Neckarsulm, Ingolstadt and Györ locations ,” explains Audi’s Production Director Gerd Walker in an interview with Automobil Produktion . “Truck trailers are put on the rails in a smart way, without us needing complex infrastructure. Combined transport from trucks and rail saves up to 11,500 tons of CO2 per year.”
Other projects include the transformation of green spaces into flower meadows and a recycling cycle for aluminium, which Audi has been operating since 2017.
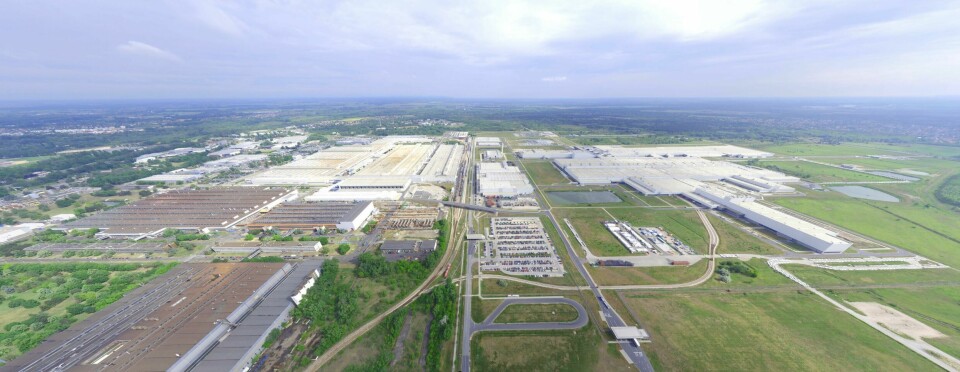
Györ is more than just a production site
However, reducing the role of Audi’s Hungarian location to just production does not do Györ justice. Audi’s technical development has also been based in northwest Hungary since 2001. With 673 employees, the driving system and complete vehicle development departments are Audi’s third-largest TE unit and provide the entire Volkswagen Group with development services. The scope includes complete development projects for drive modules and their vehicle integration as well as chassis system development.
From design to thermodynamics and numerical simulation to testing on the test bench and in the vehicle, Audi Hungaria covers the entire development spectrum, the company says. For this purpose, Audi in Györ can rely on 18 combustion engine and four electric axle drive test benches – including two acoustic test benches and four air-conditioned test benches. The site focuses on complete vehicle development in the area of virtual development with the help of numerical simulations and E/E integration with hardware-in-the-loop (HiL) applications. In the coming years, Audi plans to invest a double-digit million amount in Technical Development Györ.
The toolmaking department, which has been active at the site since 2005, currently employs around 700 people who work in an area of around 60,000 sq. m. The service portfolio of the three business areas of press tool construction, plant and fixture construction and exclusive series production covers a spectrum from design and feasibility assessment and production simulation to method planning and construction, equipment production, commissioning and series handover as well as the production of body components.
The division has recently recorded significant growth, particularly in exclusive series production: a total of around 41,400 add-on parts sets were delivered in 2023. The core of production is a flexible manufacturing concept that is intended to enable the economical production of body add-on parts in small series. The main customers include Audi Sport with the RS models, the Audi R8 and the Audi E-Tron GT Quattro, which accounted for 10,000 add-on parts sets last year alone. The division also supplies aluminium add-on parts to Lamborghini, which are used in the Huracán and the Revuelto, among others. Parts of the Bentley Bentayga also come from Györ.
This story was first published in Automobil Produktion