“We have a clear strategy towards electromobility”: Gerd Walker, Audi
Gerd Walker controls production and logistics on the Audi board. In this interview, he explains how Audi flexibly and digitally designs the production network and what role the target image of the 360factory plays.
Mr. Walker, you have been Board Member for Production and Logistics at Audi for a good two years. Your tasks include, among other things, optimal plant utilisation, CO2-neutral production in all plants by 2025, and further digitalisation and flexibility of production. To what extent have you already been able to meet these requirements?
When I joined the board two years ago, we set up a target image for production, the 360 Factory, which is based on the following four pillars: profitability, sustainability, flexibility and attractiveness. We have already taken giant steps forward. It’s good to have a vision, it’s even better when there are concrete goals behind them. But the most important thing is to operationalise such a strategy. That’s what we do: We have all of our goals firmly in mind and work with the entire production team to break down the individual topics so that they can be implemented. This is not theory, we put it into practice and implement our ambitions accordingly. For example, we have decided to halve factory costs and minimise our environmental impact in the sustainability pillar. The attractiveness pillar is about being the best employer and the flexibility pillar puts the issues of equipping and retrofitting flexibility at the top of the agenda.
There have been turbulent times on Audi’s board of directors in recent months. Do you see the management team and personally your area of responsibility now in calmer waters?
We have a very clear strategy towards electromobility. The entire board of directors is behind this and we are driving this strategy forward together. When it comes to production and logistics, I can say that we are well positioned. We are making great progress and are already seeing initial results. At the same time, we are currently facing a major challenge as we are launching the largest model offensive that Audi has ever seen.
The premium segment is highly competitive. Most recently, problems with the development of VW’s own software led to delays in model launches. How is Audi currently doing from your perspective and especially with regard to production?
We are robustly positioned. We have prepared the processes for the new start-ups and made our plants correspondingly more flexible. The Audi Q6 e-tron is the best example of this: It launched in Ingolstadt on the same line as the Audi A4 and Audi A5 models, i.e. together with vehicles with combustion engines.
“The future is electric”
This means we can respond very flexibly to demand and smoothly introduce electromobility here in Ingolstadt. We are also prepared for everything that comes next. So we will quickly follow the Audi Q6 e-tron with the Audi A6 e-tron. And we are planning another electric entry-level model for the Ingolstadt location.
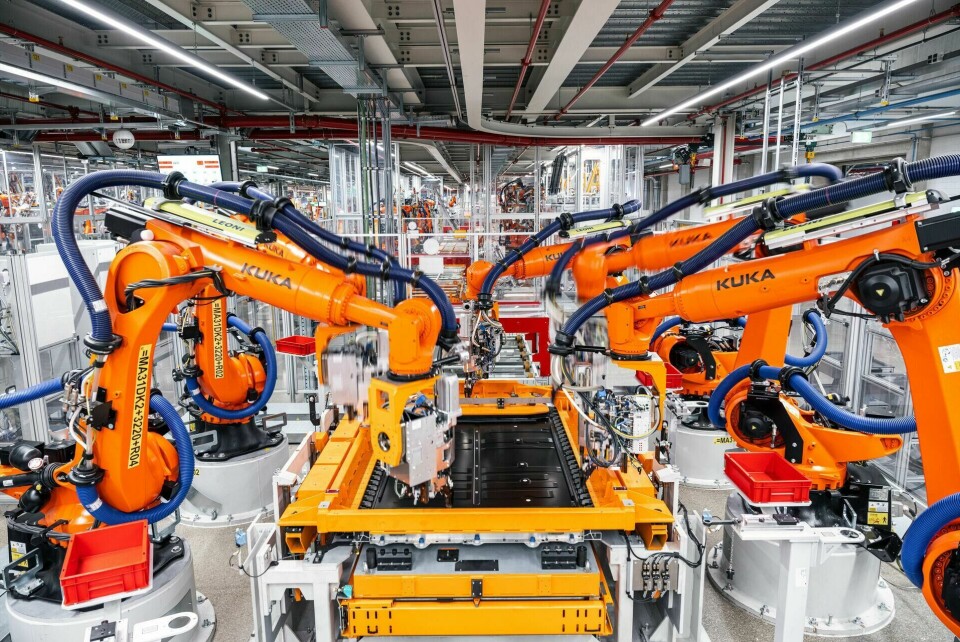
Doesn’t the joint production of pure BEVs together with ICE vehicles amount to a kind of change of philosophy within the Volkswagen Group, which has previously relied on the separate production of combustion engine and BEV vehicles?
We are very flexible in our production network. That’s why we flexibly integrate our vehicles, which are designed for the best vehicle properties, into our production network. At the Ingolstadt location it made sense to choose exactly this solution. Of course, we also have pure BEV plants such as Brussels, where we manufacture the Audi Q8 e-tron and the Audi Q8 e-tron Sportback. Where it makes sense to us, we do one or the other. But we can do both and this is exactly the flexibility we need to maintain.
Does this also mean that they could switch to a purely combustion engine factory in the future or at least add BEV vehicles?
That’s exactly what we can do. And we always do it where it makes sense.
A credo issued at the end of 2022 is that all production sites will produce fully electric vehicles by 2029. Are you on track and how realistic is this target?
As I said, we are facing the biggest model offensive in our history. We will manufacture these more than 20 new models in our entire production network. By the end of the decade, we will have made all of our locations fit for electromobility and will gradually produce the new electric vehicles there and bring them onto the market.
The current reluctance to buy electric cars doesn’t scare you from continuing to rely entirely on electric drives?
Absolutely not. The future is electric. In the end, of course, customers decide based on their demand which vehicles we build and how quickly the changeover takes place. Our production network is designed to be flexible for this purpose. But that doesn’t change the overall direction of electromobility.
The Audi production network includes 16 factories worldwide. The most important locations in terms of numbers and importance are now Ingolstadt with the new Q6 e-tron including battery assembly and the Chinese joint venture FAW-Volkswagen Changchun. How are these locations prepared for the future?
We produce Audi models in a network of 16 factories. There are also the factories of Bentley, Lamborghini and Ducati. Basically, we are positioning the regions of the world to be sufficiently strong, independent of one another. Within our network, every location produces Audi models of the same high quality. That’s why we’re also very strong in our joint venture plants.
Because you are talking about China: We are currently setting up a new plant there with the Audi FAW NEV Company, which will logically be at the forefront in terms of standards. From the end of the year we will begin producing three models from the A6 e-tron and Q6 e-tron series specifically for the Chinese market.
Despite advancing electrification, the market continues to demand combustion engines. In addition to Q3 production, Győr in Hungary is now the largest location for combustion engines. How flexible are you with regard to the vehicle models and engines?
In addition to the vehicle production you mentioned, Audi Hungaria is the largest power plant in the world. This is no longer just for combustion engines, but also for the drives of electric models. Győr has been producing the drives for the Audi Q6 e-tron from Ingolstadt since the end of 2023 and for the Audi Q8 e-tron from Brussels for a little longer. With the new e-platform PPE (Premium Platform Electric) and the ramp-up of electromobility in general, this location is developing splendidly and the employees are acquiring the necessary new skills with great commitment.
The Q6 e-tron is currently being launched, which is powered by the aforementioned newly developed electric motors for the PPE platform. These drives also come from Győr, where three new lines were added. The production line for stators has 28 work steps and the gearbox production has 15 work steps. 190 individual assembly steps are required for axle assembly alone. Sounds complicated…
… and is therefore proof that electromobility continues to ensure a high level of employment. With up to three electric machines in the SQ6 e-tron, for example, we generate a high level of employment and thus also achieve the transformation in our drive plant in Hungary.
Gerd Walker controls production and logistics on the Audi board. In this interview, he explains how Audi flexibly and digitally designs the production network and what role the target image of the 360factory plays. numerous work steps for the electric drive sound very complex. Can you make a comparison between the steps and cycles for combustion engines and BEVs in production?
The production of a vehicle with electric motors, such as the aforementioned S variant of the Q6 e-tron with its three electric machines, differs from that of a vehicle with an internal combustion engine, especially in the individual production steps. Some features are eliminated with the electric drive, others, such as the battery, are added. One can therefore also speak of a shift. That’s why it’s so important to take people along with you during the transformation, to qualify them and to build up their skills. This has already been done very extensively, especially in Győr, Ingolstadt and Brussels.
Neckarsulm with the Böllinger Höfe is one of the image carriers in the network. Where the R8 and e-tron GT are built, digital projects have also been initiated again and again, for example with 3D printing tools. What role will Württemberg production play in the future?
The Böllinger Höfe is our sports car factory and is a kind of technological laboratory in which we try out new technologies before they go into series production. We are currently implementing numerous new projects there. One of the most exciting and with the greatest potential at the moment is the so-called “Edge Cloud for Production”. Behind this lies the virtualisation of the shop floor IT structure. Computers that were on the line are virtualised and work on the relevant topics in the cloud. This allows us to achieve extremely fast response times when it comes to maintenance or installing new software. When we roll out this technology - and we are close to doing so - then we are talking about a real game changer for the automotive industry. The Edge Cloud for Production is already running in series at Böllinger Höfe and we can then use this experience for the entire production network.
According to media reports, Audi capacities in Europe could be reduced. One production facility up for consideration could therefore be Brussels, which is currently well-used with the Q8 e-tron. What can you say about that?
We only started production of the Audi Q8 e-tron in Brussels in December 2022 and are still at the beginning of the product life cycle. With the ramp-up of electromobility, we have great expectations of this wonderful vehicle. That’s why we have a robust position in Brussels. In our planning sessions we look into the future, this is a completely normal process. We are examining various scenarios – including for the Brussels location.
What strategy are you pursuing with regard to the mega topics of Smart Factory, Industry 4.0 and artificial intelligence?
For me, digitalisation is the enabler for every pillar of our strategy. Digitalisation helps to reconnect existing knowledge and thus support people. There are a wide range of possible applications, especially in the area of AI. In series production, we primarily use AI in quality monitoring, for example in the form of camera-based crack detection in body construction. Or in the paint shop: Robots use scanners to check the quality of the painted body for the Audi Q6 e-tron. There are also many use cases in logistics and planning. A broad field with a lot of potential for the future.
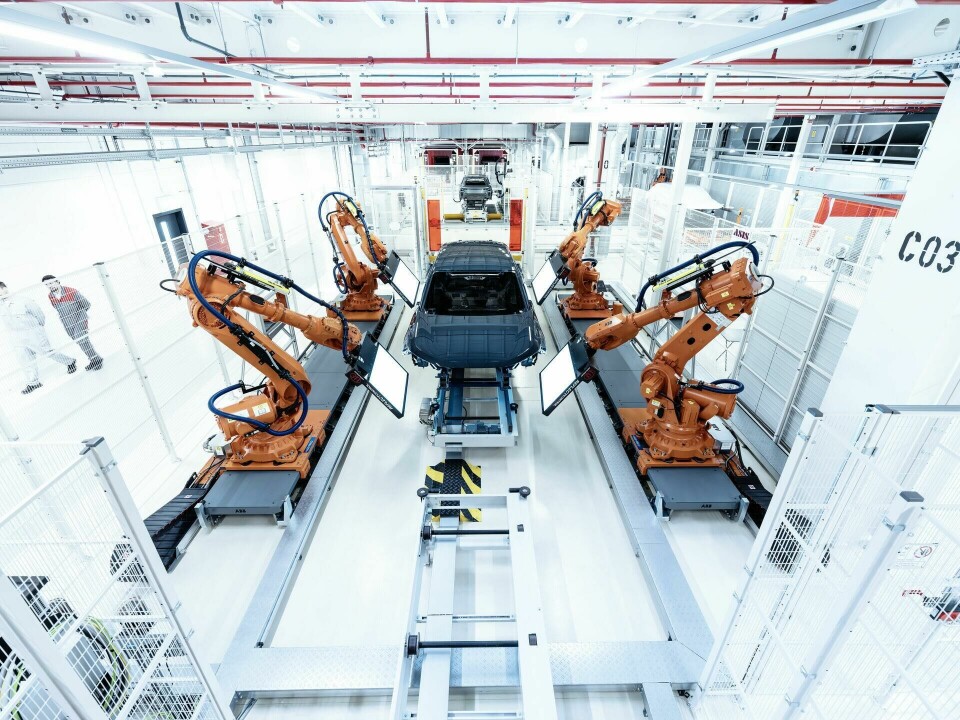
Which digital methods do you use in logistics?
We focus primarily on creating complete transparency across the entire process chain and thus making the supply chain more resilient and efficient. AI applications can help to identify bottlenecks at an early stage and find solutions automatically. But we also focus on sustainability in logistics: our approach is to transport as much as possible by rail. With DB Öko Plus we have a CO2-neutral product that we like to use to organise our transports - for example between the Győr drive plant in Hungary and our other plants in the production network. Flexibility between rail and road is also important. Since April, we have been using a “green” train with an innovative loading concept for logistics transport between the Neckarsulm, Ingolstadt and Győr locations. Truck trailers are put onto the rails smartly, without us needing any complex infrastructure. The combined transport of trucks and trains saves up to 11,500 tons of CO2 per year.
In addition to a conversion of the paint shop in Neckarsulm and the loop for aluminium, Audi also stands for commitments that extend to glass recycling. What else do you have in the pipeline for the major areas of sustainability and environmentally friendly manufacturing?
Basically, we renew ourselves from within, which means we use our existing production network, transform our workforce through further training and have alone
This provides a good starting point for driving forward the renewal of what already exists. In production, our Mission:Zero strategy specifies the areas of action. It takes into account the pillars of decarbonisation, water use, resource efficiency and biodiversity. As with all strategies, we have a roadmap for all locations. One core is the balance sheet CO2 neutrality by 2025. We have already achieved this goal in Ingolstadt, Györ, Brussels and the Böllinger Höfe. Neckarsulm and San José Chiapa in Mexico will follow at the turn of the year.
This interview was taken from AMS sister publication, Automobil Produktion, and was written by Götz Fuchslocher. You can find the original here.