“We cannot afford to make any mistakes” - Volkswagen’s Portugal boss Thomas Hegel Gunther
It’s not easy being the manager of a VW plant these days. In an interview, Volkswagen’s Portugal boss Thomas Hegel Gunther explains what makes the home of the T-Roc so special and how his team is continually increasing effectiveness through various lean principles.
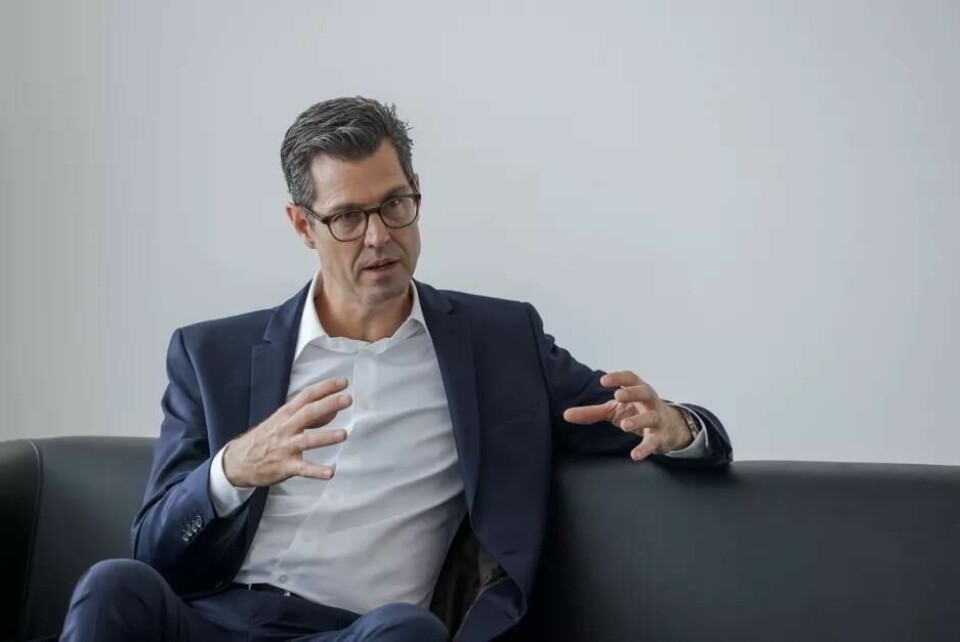
Mr. Hegel Gunther, your plant was awarded the Automotive Lean Production Award in 2023. In addition to lean practices, what characterises the spirit of your factory?
Volkswagen Autoeuropa was founded in 1991 and we have been building vehicles here in Portugal since 1995. Today we are the only car manufacturer that produces in Portugal. We also play a major role in the Portuguese economy: Volkswagen Autoeuropa accounts for around 1.5 percent of Portugal’s gross domestic product, not including suppliers. In addition, we are the largest foreign investment in Portugal and are responsible for four percent of the country’s exports.
Thanks so much for the classification. But the question remains: What characterises the spirit of the employees here? How do you manage to achieve such success in an existing factory that is already more than 30 years old?
We are part of the Volkswagen Group, but geographically we are located in the south-western corner of Europe. This brings with it logistical challenges, especially compared to plants in Central Europe. However, we try to make up for this disadvantage by optimising logistics, productivity and continuous improvement.
Can you be a bit more specific? What makes it particularly challenging to be located here in Portugal? What are the biggest logistical challenges?
People often talk about the Iberian Peninsula and think that everything is close together. But our Spanish plants in the Group, such as the one in Pamplona, are almost 1,000 kilometres away from us. Our plants in Germany are more than 2,500 kilometres away. In our production network, there are many parts that we import from Central and Eastern Europe. Logistics inevitably plays an important role. For example, we receive our engines, most of which come from Germany, by sea. This enables us to reduce logistics costs and our carbon footprint.
Demand for the T-Roc is high. They should be able to work almost non-stop, right?
We work seven days a week, in 19 shifts out of 21 possible. In the two shifts in which we are not producing cars, we have a team that carries out maintenance work, but also a lot of optimisation and preparation work.
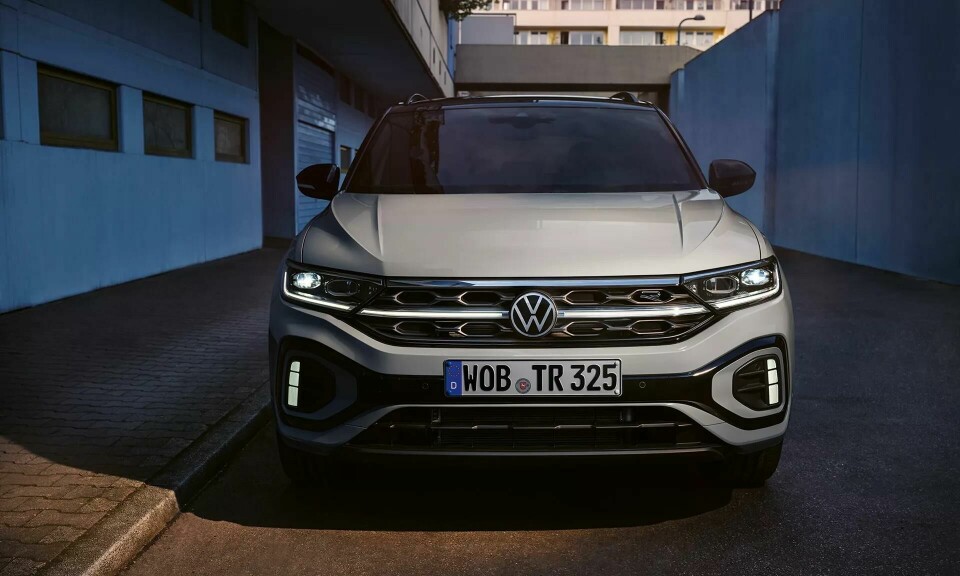
The T-Roc is in high demand and brings with it various production challenges and opportunities
Basically, regarding the structural organisation: You are at the top, how else is the plant organised?
We have a structure within the brand that is basically standardised across the plants, but has some differences depending on certain characteristics of the plants. The size of the plant plays a role, as does the number of models produced locally and what additional activities are carried out in the plant. One special feature of ours in Palmela is that we have our own toolmaking facility and manufacture press tools. And not just for ourselves, but also for other plants in the group. And a large proportion of the parts that we produce in our press plant are also exported to other plants.
What are the biggest challenges for you as plant manager at this time, especially at this location?
My job as plant manager is to support and motivate the team to continue to optimise our processes. Because the better the processes, the better our performance. Ultimately, it is my responsibility to continue to develop the site so that it is well positioned for the future.
To what extent did your previous positions help you to gain a foothold here? It is certainly different whether you work in a factory in Germany or here, for example.
I have worked in various departments at Volkswagen. Whether in component production, seat production or logistics – in all of these departments we always worked in a very cost-sensitive and efficient manner. I learned a lot that I can apply here in Portugal.
Many improvements in Palmela come directly from the shop floor. Was this already the case before you started working here or did you have a strong influence?
Even before my time, Volkswagen Autoeuropa was one of the most productive plants of the Volkswagen brand. I motivated the team not to rest on their laurels. We developed our own plant strategy, in which our managers were involved, and which shows where the plant needs to develop. Guardrails and strategic goals were then set. One of these was that we wanted to increase the number of cars produced daily in order to be able to meet the high demand for the T-Roc. We want to increase our productivity by building more cars with the existing team, instead of increasing productivity by reducing staff. This also had a positive impact on factory costs.
Read More Volkswagen Stories…
- Volkswagen invests $5B in Rivian to forge EV-software Joint Venture
- VW in cooperation to develop sustainable materials for vehicle interiors
- In Emden, Volkswagen wants to leave the Passat behind
- VW’s plant closures illustrate industry’s existential crisis
On our factory tour you described the paint shop as a bottleneck. How were you able to resolve this bottleneck?
First of all, the bottlenecks need to be identified. We focused on the value stream management method, which is the combination of value stream analysis and value stream design. An interdisciplinary team analysed the factory processes in detail for seven weeks, inspected them and recorded data. After the bottlenecks were identified, we decided on work packages in our value stream design workshop. With the clear goal of significantly improving the performance of the factory. We shifted the focus from point kaizen to system kaizen.
Can you be more specific about what exactly you did in the paint shop?
The colleagues in the paint shop have identified ways of speeding up the paint shop processes in order to increase daily production. I’ll give you a concrete example: we had a booth in which two employees used to paint by hand. Thanks to the optimisations, we were able to reduce this to one employee per shift. Then the team realised that they could also drive through this booth during their break time if they automated it. This increased productivity. A side effect is that we also save energy costs because we don’t need any ventilation or lighting for the employees in the booth. The team carried out this continuous process improvement over a period of one and a half years, with the result that the paint shop now runs in sync with the other trades. In other words: with minimal investment, we increased output by almost 100 cars per day.
Unlike some other works, it doesn’t seem like everything is being done from scratch. It seems more like making the best of what’s been around for 30 years, would you agree?
Exactly. But it must also be said that 30 years is not old for an automobile factory. Old systems are often well run in and can be used efficiently. In the case of the paint shop, however, although it has always been excellently optimised, maintained and cared for, we are now at the point where we have to replace it in many places. This is also necessary due to the stricter legislation. That is why we are now building a new paint shop. But this will also be a hybrid solution in which parts of the current paint shop are upgraded for the future.
Let’s move on to the topic of sustainability. How does Palmela stand out here?
Sustainability is one of the six pillars of our strategy. Our plan is to reduce our factory’s CO2 emissions by 80 percent by 2030 compared to 2021. We have concrete measures to achieve the goal. The new paint shop is a big part of it, but not the only one. We also do very precise and accurate tracking to reduce our CO2 emissions. Today, we already produce 100 percent with green electricity and want to produce our own electricity in the future. Our goal is to cover the factory’s base load with our own green electricity by 2026, which we produce with photovoltaic systems on our supplier park next door.
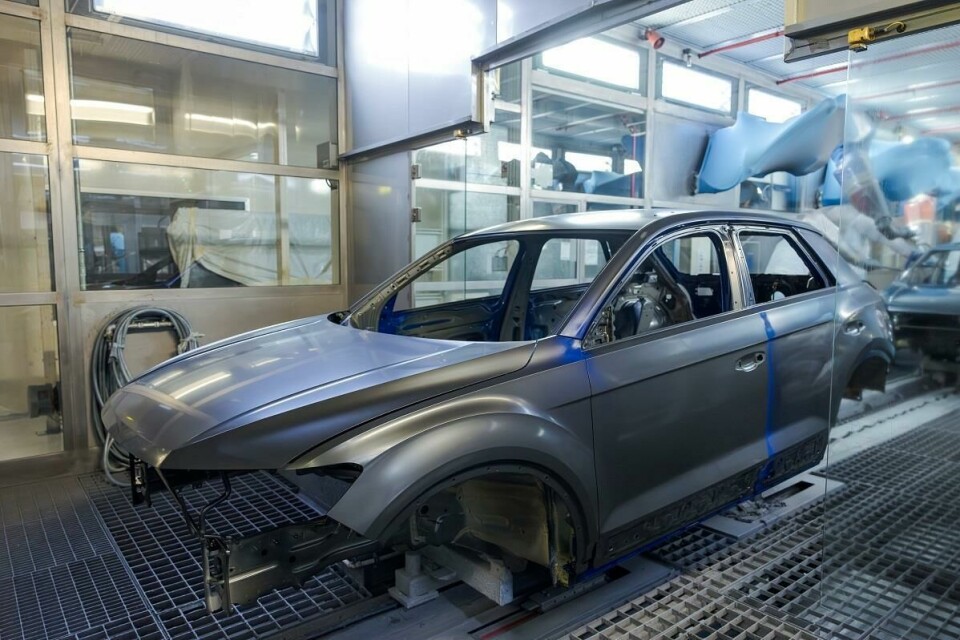
By 2030 the plant aims to reduce its CO2 emissions by 80 percent as compared to 2021
How big is your supplier base?
We currently have eleven suppliers in the supplier park and around 1,700 employees who work directly for Volkswagen Autoeuropa. The supplier park is directly adjacent to our plant. This has the advantage that we can bring JIT modules such as seats and bumpers to the line using the shortest possible routes.
Let’s be a bit more general again: How happy are you when you build a successful model like the T-Roc that sells well everywhere?
We are extremely pleased that the T-Roc is selling well. But that is also a huge responsibility. We want to serve the market and do our job within the Volkswagen brand’s production network. But to make it very clear: I am also happy when other plants perform well - there is no competitive spirit.
What about the exchange with works in other regions of the world?
Since we are based on the Iberian Peninsula, we naturally maintain a very intensive exchange with our colleagues in Spain, i.e. with Seat in Martorell and also with Volkswagen Navarra in Pamplona. But alsoWe have a lot of exchange with our colleagues in Brazil and Argentina, partly because of the language, but also because we have many employees and managers who work in these plants for a time and vice versa.
You mentioned that the number of employees was reduced as part of the lean transformation. Can you talk a little about how this helped you work more efficiently?
Over the last two years, the number of employees here at the site has fallen by more than 200, entirely due to natural attrition. Nevertheless, we have focused on building more cars with the existing workforce – and thereby reducing our factory costs
Has the automation rate increased in connection with the reduction in staff?
Automation is not an end in itself, and there is no one right automation rate. We are examining how we can become progressively more productive. Automation can also be necessary to improve quality or ergonomics. Every case must make sense, every use case must have a business case.
How important is digitalisation in your Lean journey?
A great importance. We have realised that the combination of lean production and digitalisation provides a further boost for process optimisation. There is a lot of data that we use to carry out targeted optimisations. For example, we use process mining to optimise the entire process from the paint shop to assembly.
The next year is not exactly unimportant for Volkswagen Autoeuropa: What does the launch of a new vehicle mean for the plant?
We have a big task ahead of us with the launch of the new T-Roc. We are integrating the newmodel into the existing production, which runs almost around the clock. This means that the preparation of the new model in the existing facilities can only take place during the factory holidays or on long weekends. This is all planned very precisely and we cannot afford any mistakes.
This article was origjnally written in AMS’ sister publication automobil produktion. The original article can be found in German, here.