How VW’s Palmela plant excels with lean production, in-house 3d printing, and 90% automation to produce the T-Roc while preparing for the next generation of vehicles
While the continued existence of German VW plants is being questioned, Volkswagen Autoeuropa in the middle of Portugal is operating at a good capacity. Here’s a look at the lean principles that ensure that the T-Roc plant is running so well.
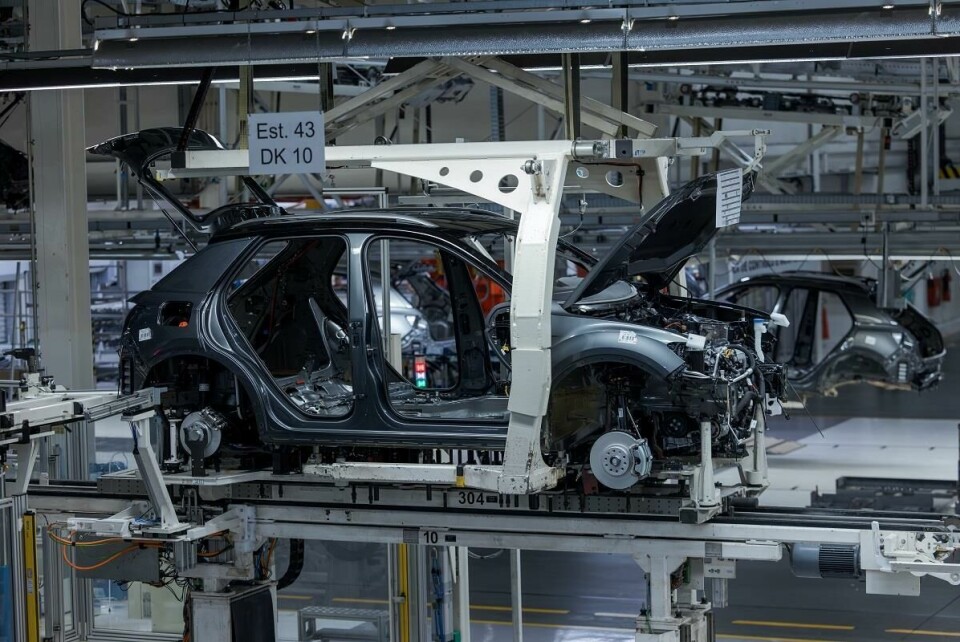
Maritime flair just around the corner, a vibrant city not far away, the 28 degrees outside temperature is easily bearable thanks to a pleasant breeze. The general conditions couldn’t be better and business is running like clockwork. Not far from the Portuguese capital, about half an hour’s drive south of Lisbon, Volkswagen is building one of its increasingly dwindling bestsellers - the T-Roc.
At the Palmela plant, it seems that all is still well with the world. Exactly one week before the VW earthquake, plant manager Thomas Hegel Gunther himself is leading a tour of the hallowed halls of Volkswagen Autoeuropa. On this sunny Tuesday, there are still around three months to go until the Automotive Lean Production Congress, which will be hosted by Hegel Gunther. Last year, his plant was awarded the prestigious Automotive Lean Production Award.
Preparations for the T-Roc successor are underway
The Autoeuropa plant in Palmela was created in 1991 from a joint venture between Volkswagen and Ford. However, Volkswagen has owned 100 percent of the shares for around 25 years now. Almost 5,000 employees work at the Portuguese plant, which has been producing the T-Roc since 2017 - around 955 units a day. With over 230,000 vehicles produced per year, mainly for export, Volkswagen Autoeuropa makes an important contribution to national exports and gross domestic product. In 2022 alone, Autoeuropa recorded sales of around €3.6 billion ($3.904 billion).
Currently, Portugal is actively preparing for the T-Roc successor, to which the OEM is devoting significant investments. The plant is involved early-on in the design-to-build phase: the vehicle has already been digitally handed over to the plant to check its assembly capability. With the help of virtual reality, experienced employees can identify potential assembly problems. Based on this, the critical parts are built in-house using 3D printing to finally verify assembly capability.
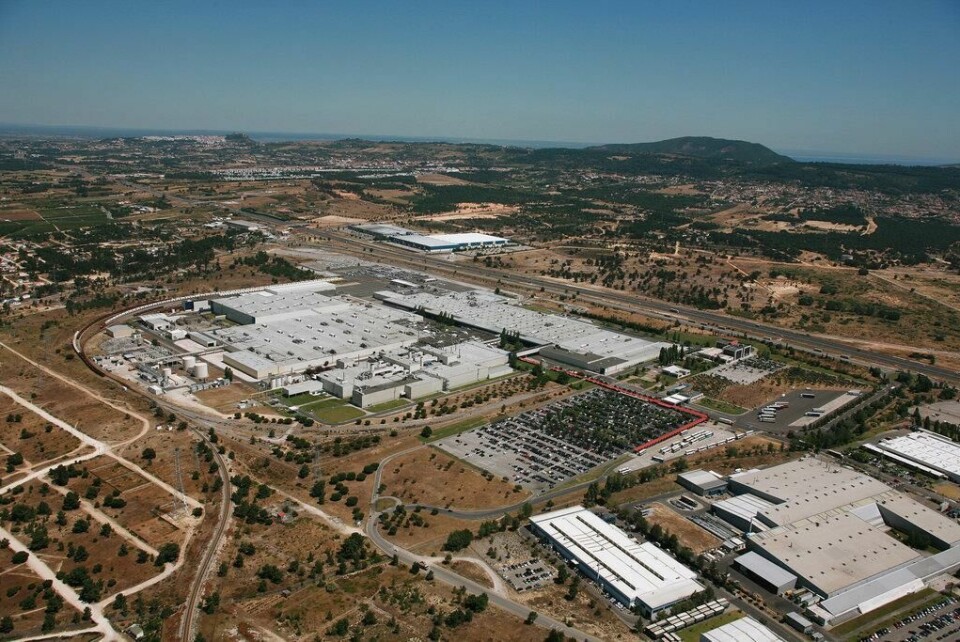
In-house 3D printing for spare parts
Before heading to the press shop, Hegel shows Gunther the factory’s own 3D printing area. It is part of the DNA in Palmela that defective individual parts should be replaced in-house wherever possible. In a press shop that is decades old, it is not uncommon for individual parts to give up the ghost. And so the employees here are tinkering with spare parts from the 3D printer, which not only bring cost advantages but also massive weight reductions.
Pressing as hard as you can
Although Palmela “only” produces one model with the T-Roc, it is also an important part of the component production network, as the press shop produces 80 percent of its parts for other plants and brands of the Volkswagen Group. “We supply a total of 31 customers with parts for 36 different models. We are currently investing in a new press, which will be put into operation next year and will enable us to be even more productive,” says Hegel Gunther.
Three cutting lines and six presses process around 600 tons of steel every day. The largest press, which works in tandem, has six press stations. Some parts, such as doors, are produced in several variants at the same time. In addition, Volkswagen Autoeuropa has a tool shop in which pressing tools are manufactured for various vehicles of the Volkswagen Group.
At the same time, the Autoeuropa plant has become a pioneer in the Volkswagen Group in terms of lean production with the aim of increasing its own productivity. Driven by the aim of being the leanest and most productive factory in the VW Group, the plant is following the Drive The Future strategy, which focuses primarily on competitiveness and preparing for the future of battery-electric vehicles. Digitalisation also plays a central role in this transformation.
The automation rate is 90 percent
At the end of each line, the car is measured for all functional dimensions that are needed for a good end result in the final assembly. “This allows us to react before major problems arise. And we measure 100 percent of the vehicles,” says Hegel Gunther.
The screens in the factory show the data of the current work online so that the operators can see the dimensions and details and make any necessary corrections directly. In the final line, the vehicle is checked again to ensure that everything complies with the specifications.
The level of automation of the 940 robots is 90 percent at the time of the tour. “We decided to carry out systematic optimisation in order to make the entire production process more efficient. The paint shop used to be our bottleneck. By looking at the production processes holistically and by better synchronising the processes, we were able to significantly improve the flow in the factory,” says Hegel Gunther.
The Value Stream Monitor sees everything
Through a series of measures, the site’s output has increased by around ten percent over the last two years, despite a reduction in the number of employees. The Value Stream methodology was particularly important as a strategic design element, which was initiated by the plant management and was able to initiate further strategic projects. The Digital Value Stream Monitor makes it possible to monitor the entire value stream - at any time and in different granularities. What exactly this means becomes clear when Hegel Gunther switches on two large flat screens in a meeting room.
A green, yellow and red flashing graphic is created, which is absolutely indecipherable for the layperson and visualises every process in the plant, no matter how small. The respective trade managers can thus switch down to every level in order to identify possible potential for increasing efficiency.
Less waste thanks to glove machines
The change in focus to the bottom-up initiative according to the Kaizen system also contributed significantly to employee productivity. Based on the macro value stream, projects to eliminate bottlenecks and increase overall equipment effectiveness (OEE ) were identified and prioritised. The hands-on mentality in Palmela is clearly evident in the glove vending machine: right next to standard drinks and snack vending machines in the factory halls, there are almost identical-looking machines that dispense new safety gloves.
Each employee has a daily quota. Previously, the gloves were often sorted out too quickly. In addition to the device, scanning a QR code tells each employee directly how much money has been saved annually through optimisation. This direct form of feedback can be found everywhere in the factory.
In addition, the resilience of the value stream was improved: Among other things, by anchoring VUCA in the future strategy as well as changing the control of the buffers between the trades and reducing the mix restrictions.
Employee ideas at every corner
From the press shop to assembly, numerous smart solutions have been implemented that are designed to achieve high levels of effectiveness with low investment. Examples of this include reducing set-up times, optimising robot processes, introducing automated material feeds, and many smart Karakuri solutions , particularly in assembly. Here, workers were able to save even more seconds by attaching a self-made platform under a lifting platform.
This no longer has to go all the way to the ground. For just a few thousand euros, efficiency was increased again. “We have also developed ergonomic solutions, such as a seat for employees that allows them to comfortably carry out overhead work while moving along the vehicle. This idea came directly from the employees,” says Hegel Gunther proudly.
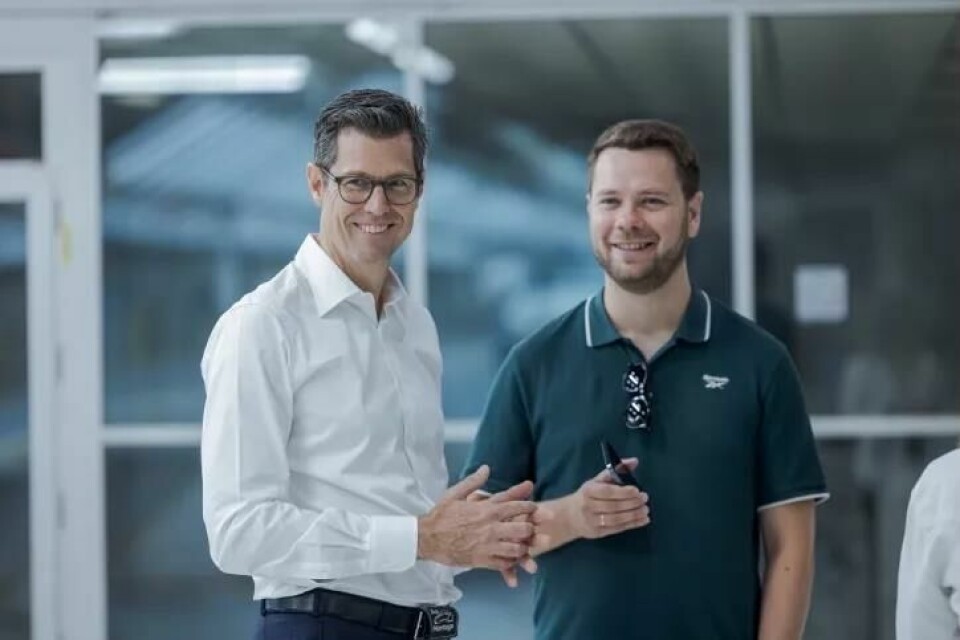
Conglomerate of Lean methods increases value stream
The use of data analysis for problem solving is firmly anchored in the organisation and supports the identification of potential for improvement. For example, it enabled the optimisation of the buffers between body shell and paint, as well as paint and assembly, the monitoring and detection of waste in the automated warehouse, and the optimisation of loading times for AGVs in logistics.
In addition, a large number of camera systems have been introduced in recent years as an intensive poka-yoke method to prevent errors. Other digitalisation topics include, for example, inventory with a drone, a real-time location system for controlling traffic in the factory, digital shop floor management, and the maintenance app.
The so-called Road Test Predictor decides, based on data collected from production, which vehicles will be driven on a longer or shorter test track. The T-Roc is built in Palmela with various engines, from a 1.0-liter entry-level model to the top model, the T-Roc R with 300 hp and all-wheel drive.
The new model is to be added in parallel to the current model from the second half of 2025. Hegel Gunther and his colleagues are not yet revealing what exactly the new T-Roc will look like, but there are really no good reasons to change much. And so the sun-drenched Palmela will continue to bring happy faces to the VW production network.
This article was originally published in AMS’ sister publication Automobil Produktion. The original article can be found in the German here.