Steel solutions for e-mobility
PARTNER CONTENT
This content was paid for by ArcelorMittal and produced in partnership with Automotive Manufacturing Solutions
ArcelorMittal is engaged in the development of the future mobility through the Steel E-Motive project lead by WorldAutoSteel and creating new solutions to simplify the car manufacturing operations
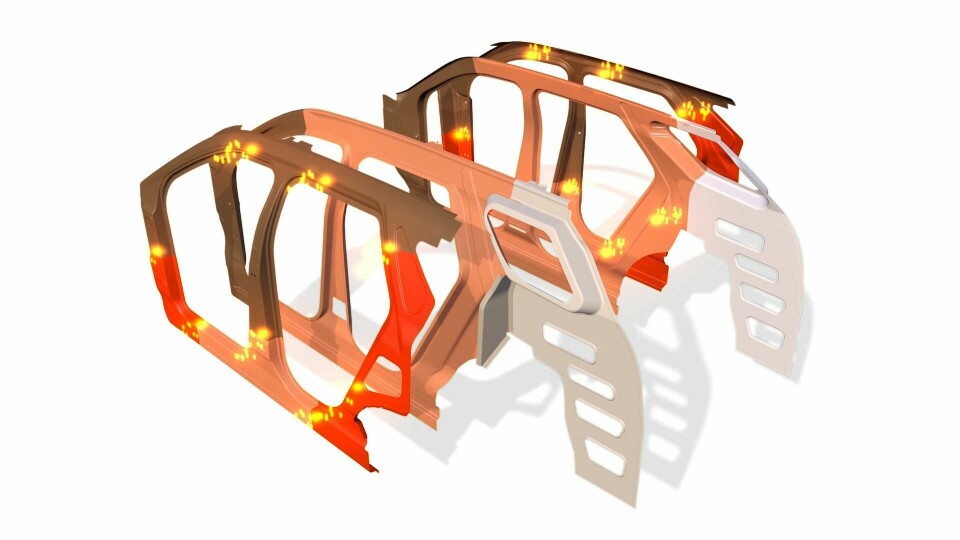
The automotive industry is currently facing a major transformation towards sustainability, firstly by deploying affordable Battery Electric Vehicles (BEV), and now by decarbonising car production and associated operations. ArcelorMittal is developing steel solutions to support the car manufacturers towards this journey by unlocking new values all along the process chain.
The transformation of the automotive industry is continuing and in the next decade we expect to see the deployment of autonomous mobility as a service (MaaS). This fascinating technology is becoming a reality thanks to huge progress in IT development and the increasing affordability of the electronic components. It is now time to make this concept concrete.
Creating a mass optimised MaaS concept
ArcelorMittal is proud to be part of the WorldAutoSteel consortium, which developed the Steel E-Motive concept with the engineering office at Ricardo. This autonomous MaaS concept was designed from scratch and its structure was optimised to meet all global high-speed crash requirements. After two years of intensive collaboration with the consortium and Ricardo, ArcelorMittal and WorldAutoSteel are today proud to propose a mass efficient design that maximises the space available for occupants and their travel experience, offered by a MaaS concept. The Steel E-Motive may be the first design fulfilling all the high-speed crash requirements with a highly engineered passive safety structure.
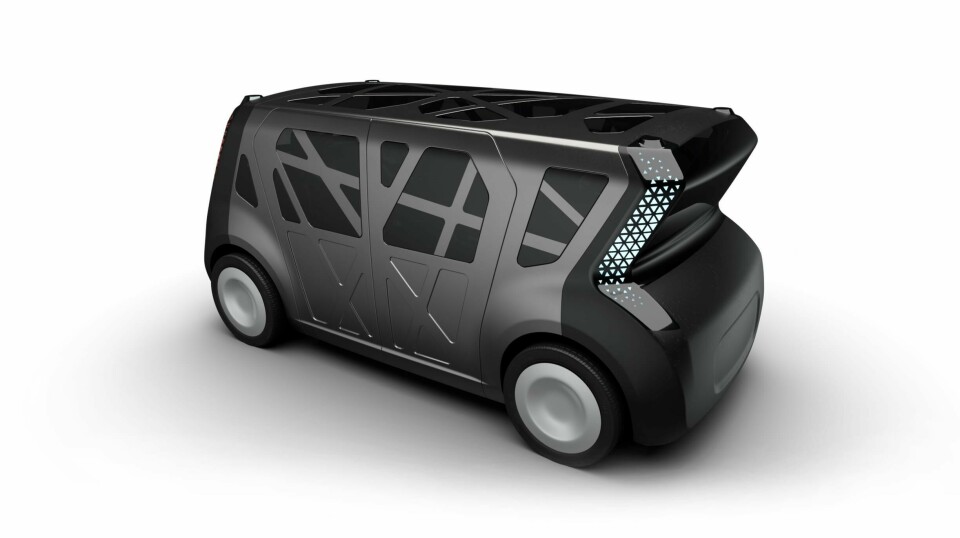
ArcelorMittal participated with the consortium providing technical guidance and support in the implementations of some key materials, such as the second generation of Press Hardening Steels or the third generation of Cold Stamping grades. Additionally, Ricardo intensively introduced Advanced High Strength Steels into the design to meet an ambitious mass target of 33% of Press Hardening Steels, 11% of third generation Cold Stamping grades and 16% of Martensitic grades. The mechanical properties of PHS 2000MPa grades, such as Usibor 2000 were key to managing the challenging front crash requirements by maximising the ratio between the passenger cell dimensions and the car footprint. The front rail dimensions were reduced to the minimum possible thanks to these best-in-class PHS grades for anti-intrusion. Another key application proposed is the Laser Welded Blanks Door Ring, mixing PHS 1500 (Usibor 1500), PHS 1000 (Ductibor 1000) and PHS 2000 (Usibor 2000), which effectively supports the crash management by ensuring the structural integrity and the ability to open the doors after a crash. The Steel e-Motive design was validated in terms of crash performance, and manufacturability.
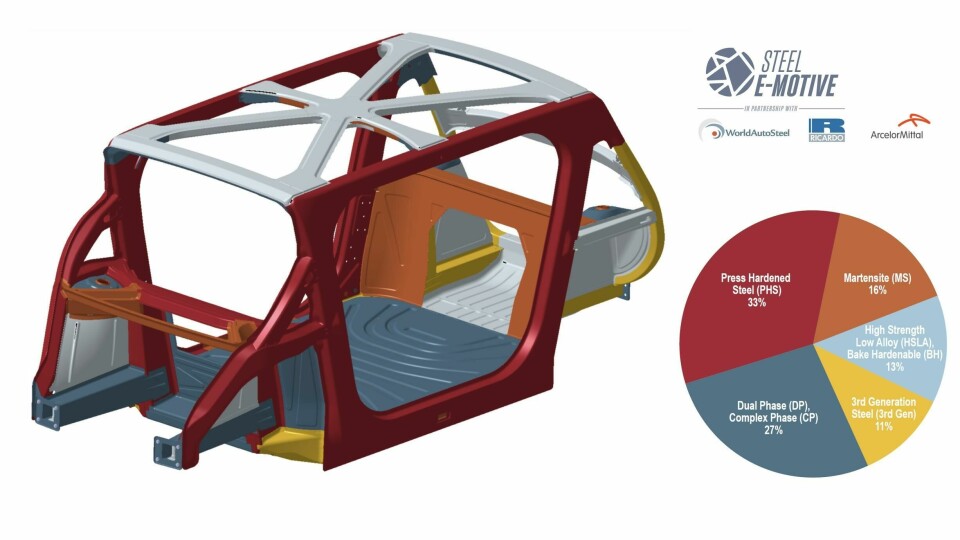
The Steel e-Motive project is currently being presented at conferences and events to demonstrate the performance of the design, and how steel addresses all the technical challenges and positions itself as the material for future sustainable mobility. Next events are C.A.R. Management Briefing Seminars in the US in August and the EuroCarBody conference in Europe in October.
Simplifying the BIW with a Multi Part Integration approach
As with the Door Ring for the Steel E-Motive projects, ArcelorMittal believes in Multi Part Integration (MPI) concepts, which can feature in large Laser Welded Blanks. These solutions offer tailored properties and thicknesses along the part to ensure a finely mastered crash scenario with an optimised mass distribution. Beside crash performance, these MPI concepts offer some key advantages in production thanks to the part integration approach and the simplification of operations.
ArcelorMittal Global R&D teams identified six applications that were integrated into one Body in White (BIW) model, and the crash performance was validated. A deeper technical analysis with partners with expertise in automotive processes and operations confirmed that the integration of these six MPI concepts in the BIW lead to a part count reduction of 46 parts, a reduction of 567 spot welds, the need for 51 fewer robots and a reduction of 30% in the hours needed per vehicle in the assembly shop. A reduction of the CAPEX for an assembly plant, in the case for a Greenfield approach, was also confirmed.
These concepts are already being studied in partnership with several OEMs, and the ArcelorMittal Global R&D team continues to develop new MPI solutions to simplify the manufacturing operations and maintain a best-in-class technical performance for the BIW.
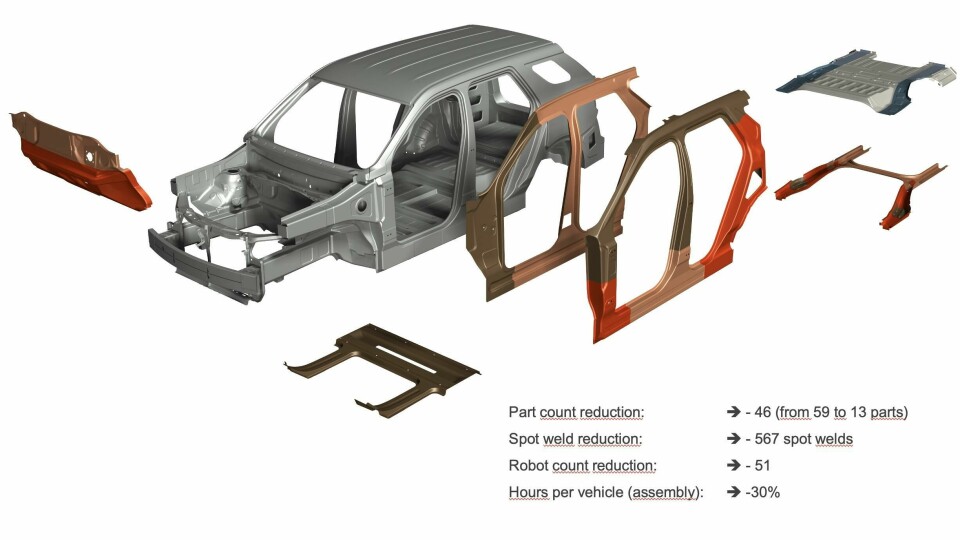
High Pressure Die Casting (HPDC) of aluminium is an alternative solution for reducing part integration, especially with the Megacasting concept. However, while this process may offer a higher potential for reducing part integration than the steel based MPI concept, if we draw a full comparison, we note that a flat steel-based design offers a higher lightweighting potential compared to Megacastings. A benchmarking analysis of similar cars having both aluminium HPDC based design and steel-based design revealed that the steel sheet-based design was 13% lighter than the aluminium HPDC-based design for the front module, and 9% lighter for the rear module at a function level. A fixed minimum wall thickness for the casting process of large parts seems to constrain the part design.
Materials choices for sustainable production
Cost pressures continue to slow the wider market acceptance for BEVs, as there is still a substantial cost gap between BEVs and ICE vehicles. According to our analysis, which was confirmed by external sources, the cost of a fully assembled module with flat steel remains less expensive than just the raw material cost needed for aluminium HPDC Megacasting.
It is also important to keep sustainability in mind as the pressure to decarbonise the BIW will become more important, as the use phase emissions for BEVs strongly decrease. Today, on average, a steel module is 70% less CO2eq intensive than an equivalent design based on aluminium Megacasting in Europe (cut off approach). This calculation was done by considering both solutions at the same net weight, which is conservative for steel, and considering the remelting of aluminium casting process scrap.
The evaluation of CO2eq emissions linked to the manufacturing processes is based on the German energy supply mix of electricity and natural gas. If we consider that a low carbon aluminium reaching 4TCO2eq/T is used, combined with a green electricity mix for the process, the steel module emits still 38% less CO2eq. If we now consider a decarbonised scenario for a car currently being designed, the relative difference between a short-term low carbon aluminium HPDC module and a short-term low carbon steel-based module remains high, the steel module being 63% less CO2 intensive (cut off approach). For this scenario we have considered aluminium at 4.0TCO2eq/T and for steel, a mix between XCarb recycled and renewably produced, and XCarb steels using a DRI-EAF route (gas powered). Aluminium may progress in recycling, but according to our calculation, a minimum of 80% of secondary aluminium would be needed to challenge steel, which is today technically questioned and highly reliant on scrap availability.
As circularity becomes a hot topic, we can also recall that steel used in the BIW is already fully and easily recycled at a very competitive cost. Steel is indeed the most recyclable material, reaching 99.3 % efficiency in mass. ‘Circular steel’, maximising the use of scrap material, is one driver of decarbonisation that we do consider, but we are limited by scrap availability and metallurgies, and this is why ArcelorMittal is promoting technologies such as Innovative DRI, Smart Carbon or Direct electrolysis to significantly reduce the carbon emissions.
Click here for more information on Steel E-Motive and ArcelorMittal