Perfecting paint transfer by focusing on improving efficiency in vehicle exterior paint application
The paintshop is an area of the production process where throughput, quality and sustainability need to be carefully balanced. Paint application specialist, Sames, looks at key areas where efficiencies can be made.
PARTNER CONTENT
This content was produced by Automotive Manufacturing Solutions in partnership with SAMES
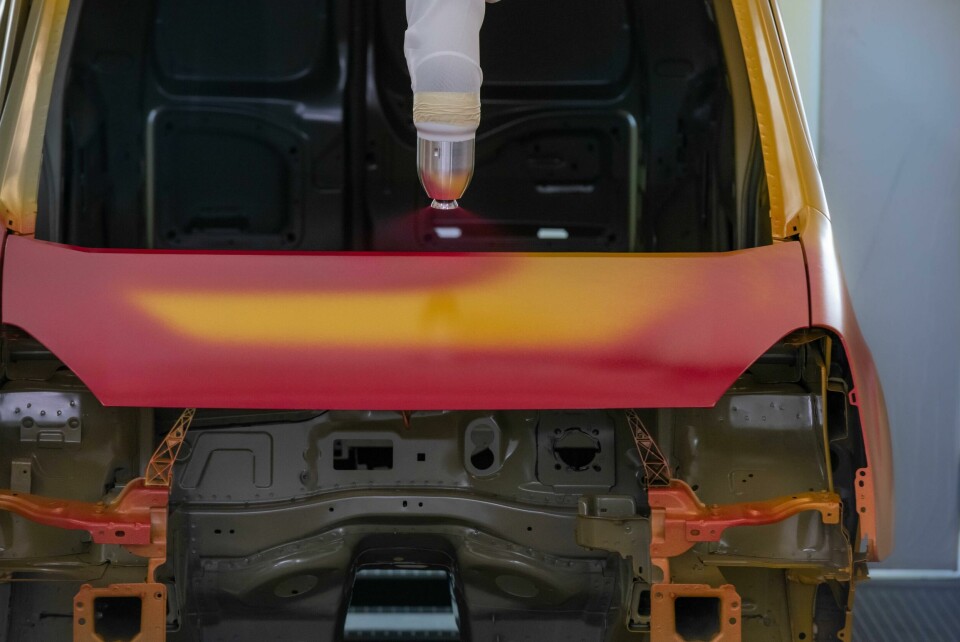
Sames has focused on vehicle exterior paint application as an area where there is the opportunity to improve the transfer efficiency. Paintshop development over the last decade has seen robot speed increase up to and above 1 meter per second as OEMs have sought to increase throughput and reduce the number of robots in the booth. However, this requires an increase in the paint flow rate, the bell cup rotation speed and the air control flow, resulting in lower paint transfer efficiency.
“For the exterior painting robots, we think the transfer efficiency can be improved by ten points, which means halving the overspray”
Sebastien Salze, Business Development Specialist – Automotive at Sames explains where improvements can be made. “For the exterior painting robots, we think the transfer efficiency can be improved by ten points, which means halving the overspray. Today we are between 70-80% of transfer efficiency for exterior body painting, but we could reach up to 90%. And there is also the materials and energy costs to consider. Reducing overspray saves on materials and the cost related to the energy to catch this overspray with the air downdraft.
“We are working on providing upgraded sprayers, to a enable a low energy and more efficient way of painting.”
Best case scenario for transfer efficiency
Through its work with global paintshop integrator partners, Sames has identified paint transfer efficiency as an operation with a lot of potential to improve. As a starting point the company targeted the best possible case for increasing transfer efficiency by reducing the paint flow rate, the bell cup rotation speed, the air control flow. This also required reducing the distance of spray nozzle to the car body and the robot speed.
Sames has also worked with a paint supplier to ‘tune’ the paint conductivity to achieve the best electrostatic effect and efficiency. Salze notes that while the paint transfer results were impressive, the adapted process couldn’t be applied to volume production, since reducing the operation speed of the robot would require more robots and have a knock-on effect on the paint booth footprint.
“We saw how far we could go but then we developed the process and applicator technology based on standard robot speeds and the number of robots in existing paintshop configurations. This makes it easier for OEMs to retrofit existing paintshops to improve their efficiency.
“With our spray systems the only two parts to change are the bell cup itself and the air shroud, these are adapted with the air control to hold the pattern. We are staying with the same robot speed, and we validated our system at 500mm per second. The nozzle distance to the car body is also reduced by 50%, from 200mm to 100mm.”
Considering the technical challenges, Salze observes that changes to equipment and processes in the paintshop offer a good opportunity to review settings and operations that may have not been upgraded for some time. For Sames, he notes the main technical challenge is maintaining the same film build quality.
“With a slower bell cup rotation speed you are using less air, consuming less energy, but you still need good atomisation of the paint droplets. We worked on the design of the bell cup and the air shrouds, and tried a lot of angles, directions, size and flow.”
Balancing paint booth airflow
Another challenge is to decrease the down draft air velocity in the booth, which Sames claims offers significant energy cost savings, but it’s not as simple as just dialling down the airflow. Here, as with other parts of its low energy paint application project, Sames has worked closely with other stake holders in this sector. Airflow in the paint booth is carefully balanced and the ventilation equipment is designed to perform to the requirements and size of the booth. For the purposes of Same’s low energy approach it might be necessary to downsize the existing ventilation system.
ATEX zoning can also be an issue, especially where reducing airflow might increase solvent build up in certain paint operations. This usually means that to comply with regulations OEMs must introduce external ‘fresh’ air into the booth to reduce solvent concentrations. Overspray contributes to this concentration build up, so reducing the amount of overspray would reduce the percentage of external air (which needs to be heated) required. Sames has worked closely with paintshop ventilation system suppliers to validate the low overspray, low downdraft process and address potential ATEX zoning issues.
(Image-slide 16 Save Electricity and CO2 pdf. Can we copy this slide? Caption: Reducing overspray also reduces the concentration of explosive solvent and the downdraft velocity)
“I made the calculation and checked with two ventilation system manufacturers, working with the ATEX rules for Europe. If you have more than 40 grams per m3 of explosive solvent, it represents a risk. For zone two, you must be below 25% of the limit of explosivity, So 25% of 40 grams per m3.
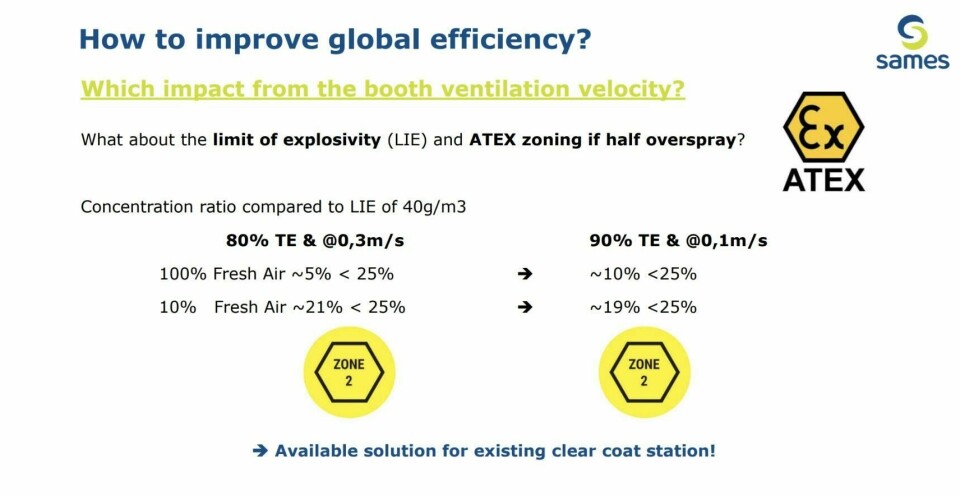
“I calculated if we increased the paint transfer efficiency by ten points to 90%, we could reduce by a third the air velocity of the downdraft, and still reduce the concentration of solvent in the booth. We could even decrease the concentration of solvent in the booth to 19% of 40 grams per m3,” explains Salze.
Solutions for different materials
Paint application systems also need manage the requirements of different substrates, something Salze notes the company is addressing as part of its development process.
“The first stage has focussed on clear coat for the bodies. After this we will work on primer where the quality of the film build is not so important, it’s more the thickness. For the base coat it becomes difficult because with the metallic paints there are particles, and the colour matching depends a lot on the spraying conditions. If you have particles, you need a lot of air to align these correctly.
“For non-metallic base coats we think we have a good solution for existing two-tone paint booths. OEMs usually build an additional base coat and clear coat station at the end of the line for the roof, which are usually black or white, and non-metallic. So, this technology for high transfer efficiency could be used for the base coat and the clear coat station. Also, as it is a separate paint booth, you could also easily decrease the air down draft since it’s easier in two smaller booths rather than on the older single painting lines, which are supplied by a big air ventilation system. And we will test this process with plastic maker as well this summer.”