Comau’s Innovations and Solutions in Battery Manufacturing
PARTNER CONTENT
This content was produced by Automotive Manufacturing Solutions in partnership with Comau
Comau offers complete battery manufacturing solutions, from assembly and testing of battery packs to integration into vehicles.
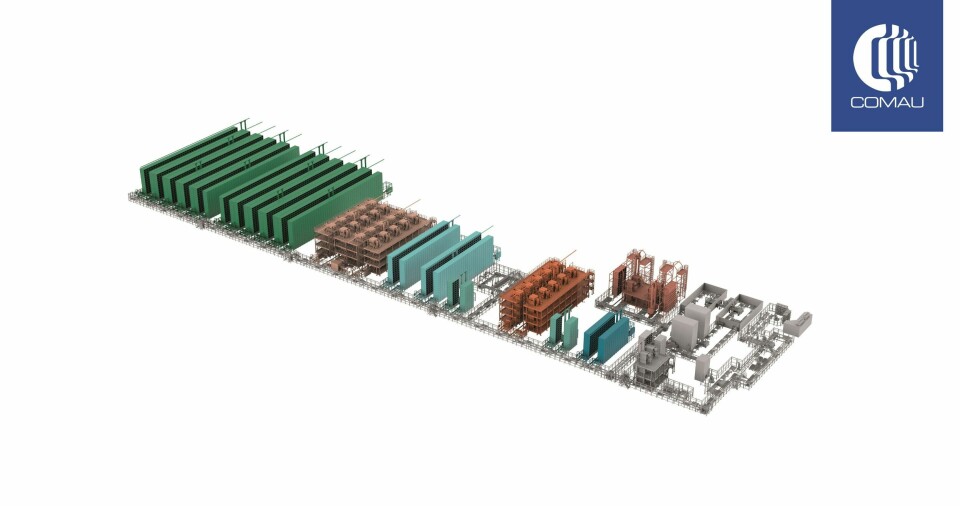
Comau provides comprehensive solutions for battery manufacturing, covering the entire process chain. The company began with battery packs, focusing on the assembly and testing of the final battery before it is integrated into the vehicle. It also produces high-speed automation lines for module assembly, handling various configurations and cell types, including cylindrical, pouch, and prismatic.
“Significant investments have been made in developing proprietary solutions for battery cell formation and ageing,” says Andrew Lloyd, Head of Engineering, Comau. “While most applications today are in prototyping stages, the long-term plan includes a stronger presence in gigafactory-scale production. At the same time, we already have customers in the Gigafactory business”.
Comau also offers production systems for battery trays, covering multiple architectures, cast products, and fabricated assembly through extrusion and welding processes.
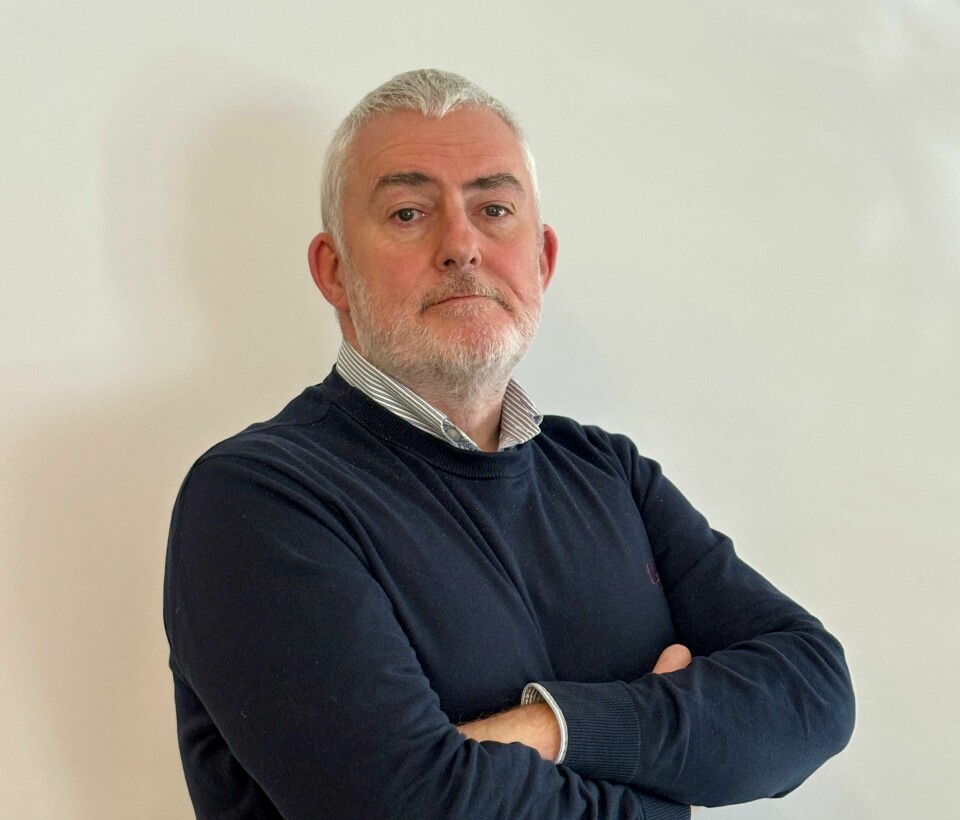
“We are also active in battery repurposing and recycling,” says Lloyd, “developing solutions for end-of-life batteries in the automotive industry.
”This includes making the battery safe by discharging, dismantling, and determining the fate of the dismantled parts, whether for repurposing, reuse, or salvaging materials.”
From an R&D perspective, Comau focuses on battery cell assembly technologies, collaborating with startups to improve efficiency and throughput for current technologies, and studying next-generation changes towards semi-solid or solid-state batteries. The Company’s broad ranging competence and versatile skills set allow Comau to respond to evolving market scenarios.
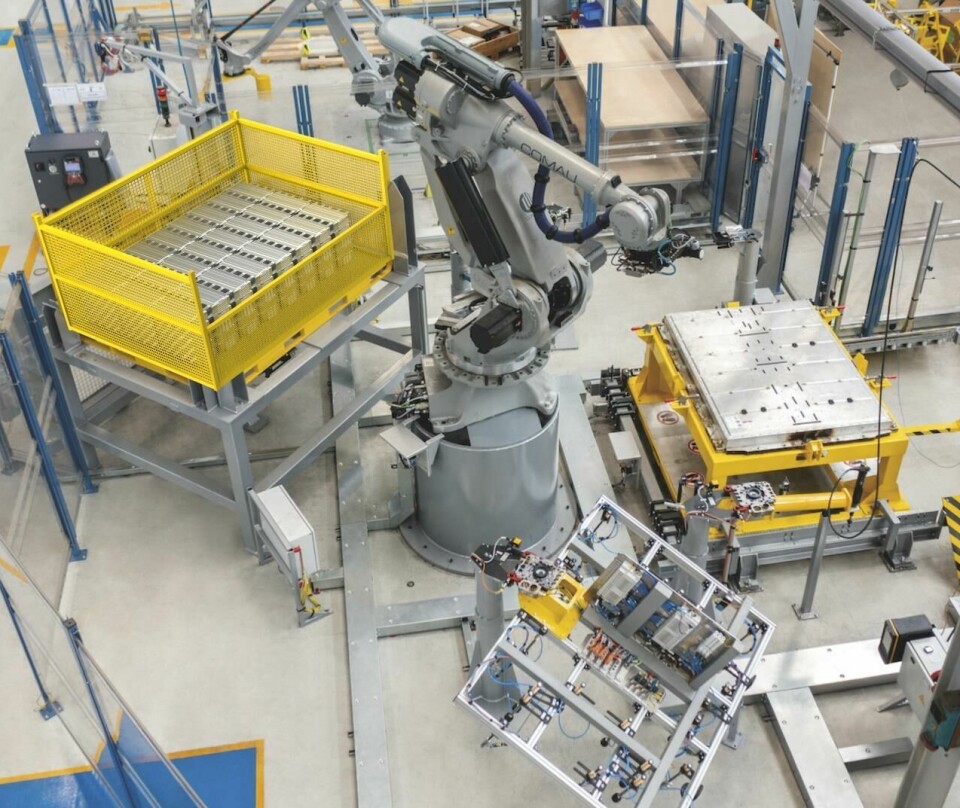
Innovation Drivers
Lloyd says Comau’s innovation drivers include two main dimensions. “Firstly, end-user efficiency. Deploying battery production in our customers’ operations involves significant investment, particularly at gigafactory scale. We aim to optimise asset utilisation, reduce floor space with high-density automation solutions, and ensure sustainability through careful material selection and energy-efficient plant operations. Cost efficiency is also crucial, as being cost-effective is a key buying criterion for our customers.
“Secondly,” he says, “we are highly customer-focused, operating in a B2B environment where customer centricity is vital. We strive to deeply understand our customers’ pain points and develop solutions that address their specific needs, whether it’s floor space, throughput, yield, flexibility, or time to market.”
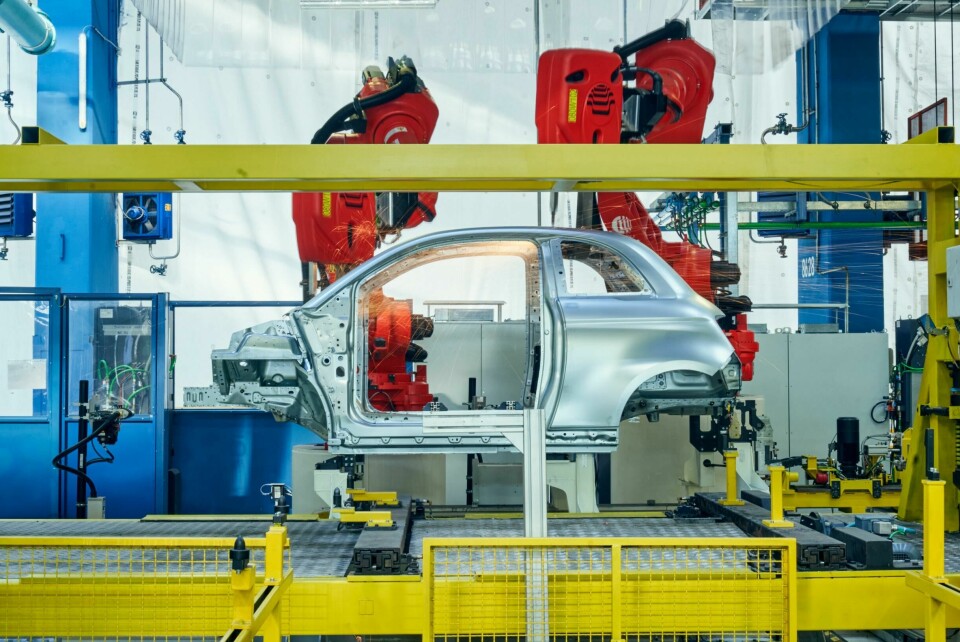
Approach to addressing resource challenges
Comau started this journey ten years ago, “at a time when we detected a shift in potential technologies in the transportation market,” says Lloyd. “We have undertaken multiple efforts to prepare for this change.”
One significant step was the company’s upskilling and reskilling of its current workforce with training programs about e-Mobility over the past five years involving around 1,200 to 1,300 people. “This process includes continuous updates to our training syllabus based on R&D learnings,” he says.
“We also took a discipline-tailored approach , hiring people with specific battery design experience and competencies in laboratories and chemistry.
“We collaborate with universities and polytechnics, engaging PhD students to explore emerging technologies. We also hire graduates and fresh high school students, leveraging our internal expertise to educate them.”
Managing five generations within the company, ensures a sustainable cycle of retirement and replenishment, particularly in the electrification field, allowing the company to maintain a strong internal competence base.
Competitive Advantage in the Battery Production Systems Market
Lloyd says, “simply put, we offer unique solutions backed by 50 years of experience in pioneering automation technology in the automotive sector. Our customers receive dedicated attention and focus from us. We solve technological problems effectively and have a strong customer-centric approach, with culturally and geographically aligned organisations and a distributed R&D group.”
Lloyd adds that Comau provides excellent value for money, ensuring its systems perform as designed, with an impeccable safety record. In electrification, where safety requirements are stringent, Comau has demonstrated its ability to deploy and run plants to a high level of safety protocols.