Powering the future: Top 5 EV battery chemistries and formats across the world
With batteries underpinning the electrification journey, we take a look at the battery chemistries and architectures driving the change.
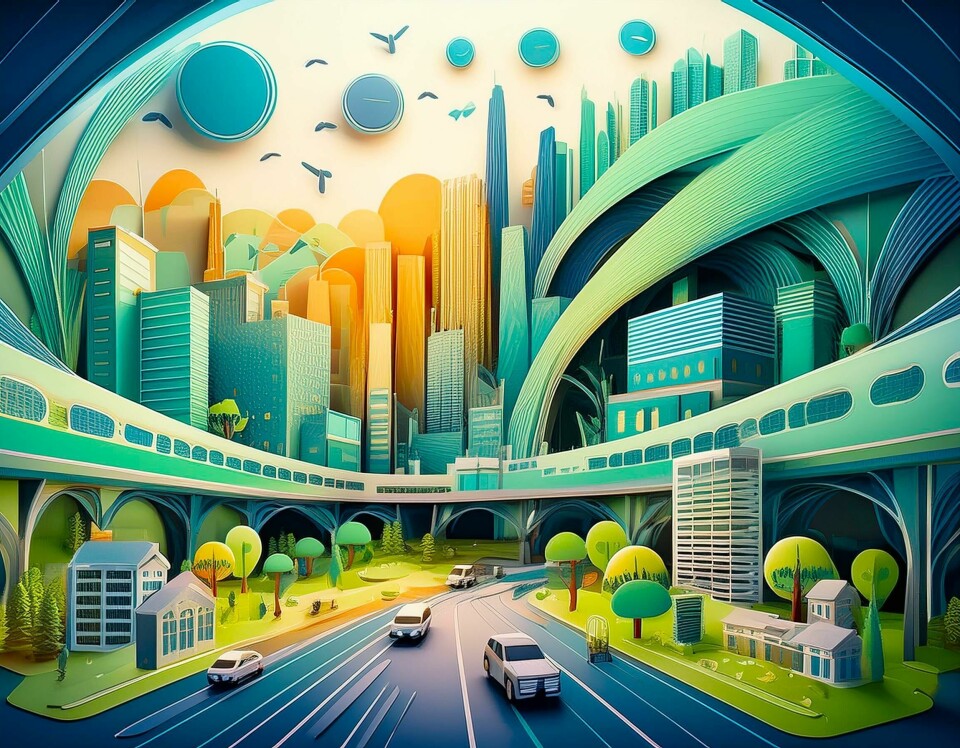
Electric vehicles (EVs) rely heavily on advanced battery technologies, each offering distinct benefits and challenges. Lithium-ion batteries, including Lithium Iron Phosphate (LFP) and Lithium Nickel Manganese Cobalt Oxide (NMC), are currently the most widely used due to their high energy density, long lifespan, and light weight. Emerging technologies such as solid-state and lithium-sulfur batteries hold the promise of even greater advancements in safety and energy storage.
Meanwhile, sodium-ion batteries provide a cost-effective alternative with abundant raw materials. Understanding these battery chemistries and formats—cylindrical, prismatic, and pouch cells—is crucial for grasping their impact on performance and design. As industry leaders like Tesla, Volkswagen, and BYD continue to innovate, the future of EV battery technology looks promising and dynamic.
Battery Chemistries
Lithium-ion (Li-ion) Batteries
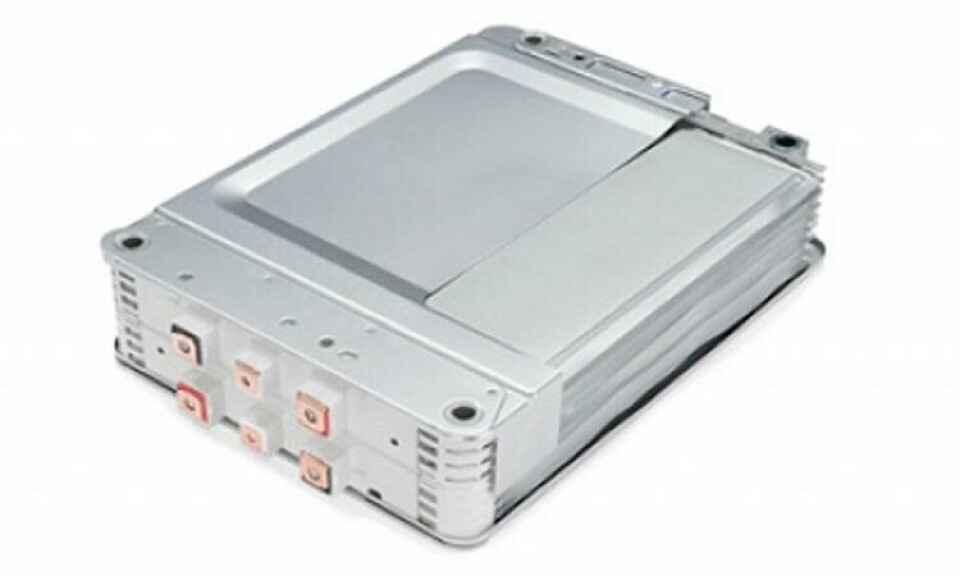
Overview and significance in the EV market:
Lithium-ion batteries are the predominant power source for EVs due to their impressive energy density, long lifespan, and relatively lightweight characteristics.
These advanced batteries have revolutionised the EV market by offering a practical and efficient means of storing electrical energy, enabling longer driving ranges and faster charging times. Their application extends beyond electric cars and buses to include portable electronics, such as smartphones and laptops, underscoring their versatility and critical importance in modern technology.
As the demand for sustainable energy solutions continues to grow, lithium-ion batteries are expected to play an even more significant role in the transition toward electrification, further solidifying their status as a cornerstone of the energy landscape.
Common types:
Lithium Iron Phosphate (LFP): Known for its safety, long cycle life, and thermal stability, LFP batteries are widely used in electric buses and lower-cost EVs. Companies like BYD and Tesla have adopted LFP batteries for their lower-end models.
Lithium Nickel Manganese Cobalt Oxide (NMC): These batteries offer higher energy density and are used in long-range EVs, such as the Tesla Model S and the Chevrolet Bolt. NMC batteries balance energy density, longevity, and cost, making them popular in passenger vehicles.
LFP Advantages: Safer due to thermal stability, longer lifespan, lower cost.
LFP Disadvantages: Lower energy density compared to NMC.
NMC Advantages: Higher energy density, better performance in cold climates.
NMC Disadvantages: Higher cost, potential supply chain issues due to cobalt.
Nickel-Metal Hydride (NiMH) Batteries
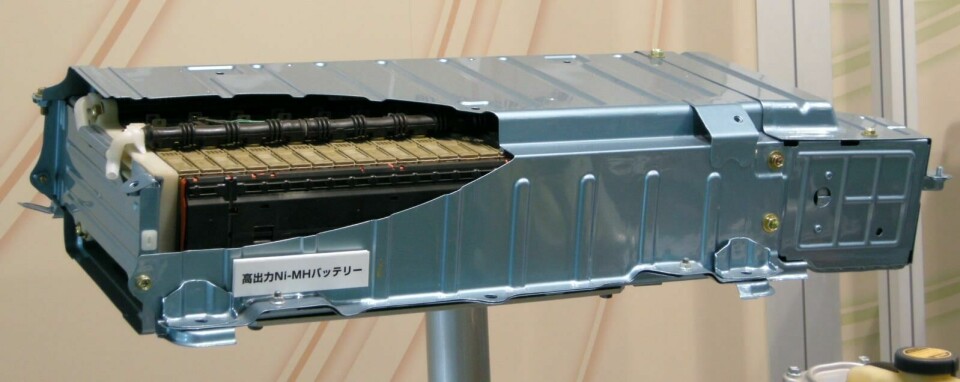
Historical significance and current usage: Nickel-Metal Hydride batteries were the mainstay of hybrid EVs (or HEVs) like the Toyota Prius before lithium-ion batteries became the standard. They are still used in some HEVs and plug-in hybrids due to their robustness and safety features.
Performance characteristics and limitations: NiMH batteries offer good performance at low temperatures and are less prone to overheating. However, they have lower energy density and higher self-discharge rates compared to lithium-ion batteries. This makes them less suitable for full EVs but still viable for hybrids where space and weight constraints are less critical.
Solid-State Batteries
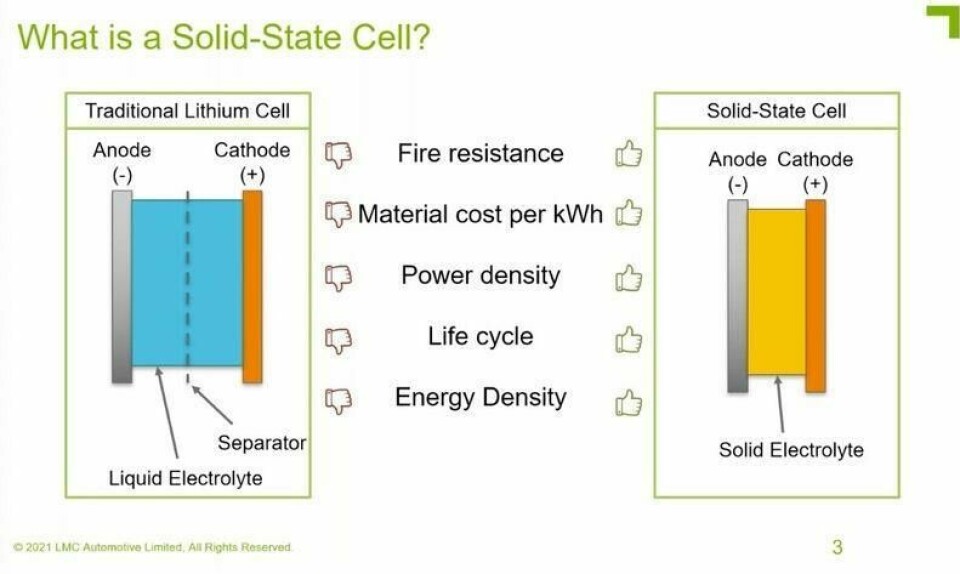
Emerging technology and potential impact: Solid-state batteries represent the next generation of battery technology, with the potential to significantly improve energy density and safety by replacing the liquid electrolyte with a solid one. Companies like Toyota and QuantumScape are pioneering this technology, which promises to revolutionise the EV market.
Current development status and future prospects: While solid-state batteries are still in the development phase, they are expected to enter the market within the next decade. These batteries could offer longer ranges, faster charging times, and improved safety, addressing many of the limitations of current lithium-ion batteries.
Lithium-Sulphur (Li-S) Batteries
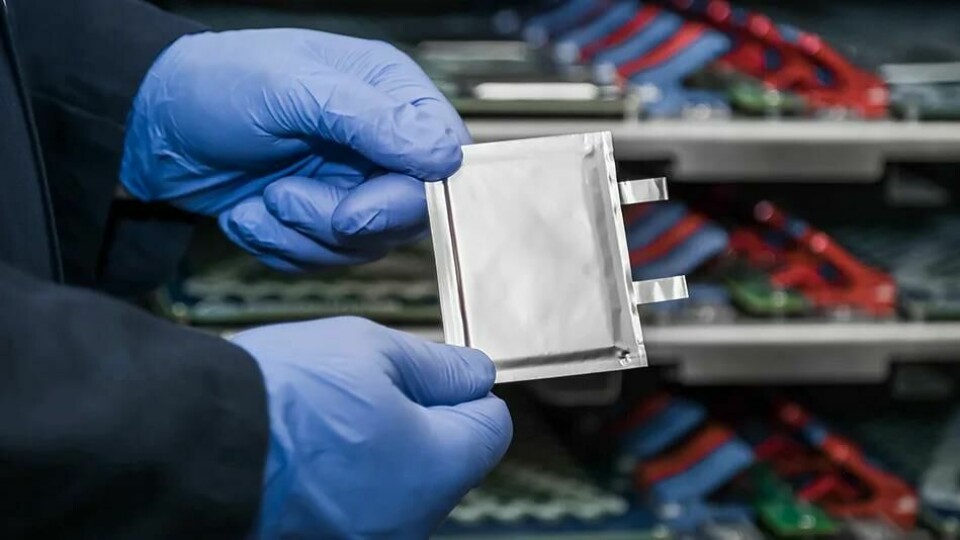
Overview of the chemistry and potential benefits: Lithium-sulphur batteries have a high theoretical energy density, potentially offering several times the energy capacity of traditional lithium-ion batteries. This makes them a promising option for future EV applications.
Challenges and current research: Despite their potential, Li-S batteries face significant challenges, including limited cycle life and issues with stability. Research is ongoing to overcome these hurdles, with efforts focused on improving the cathode materials and electrolyte stability.
Sodium-Ion Batteries
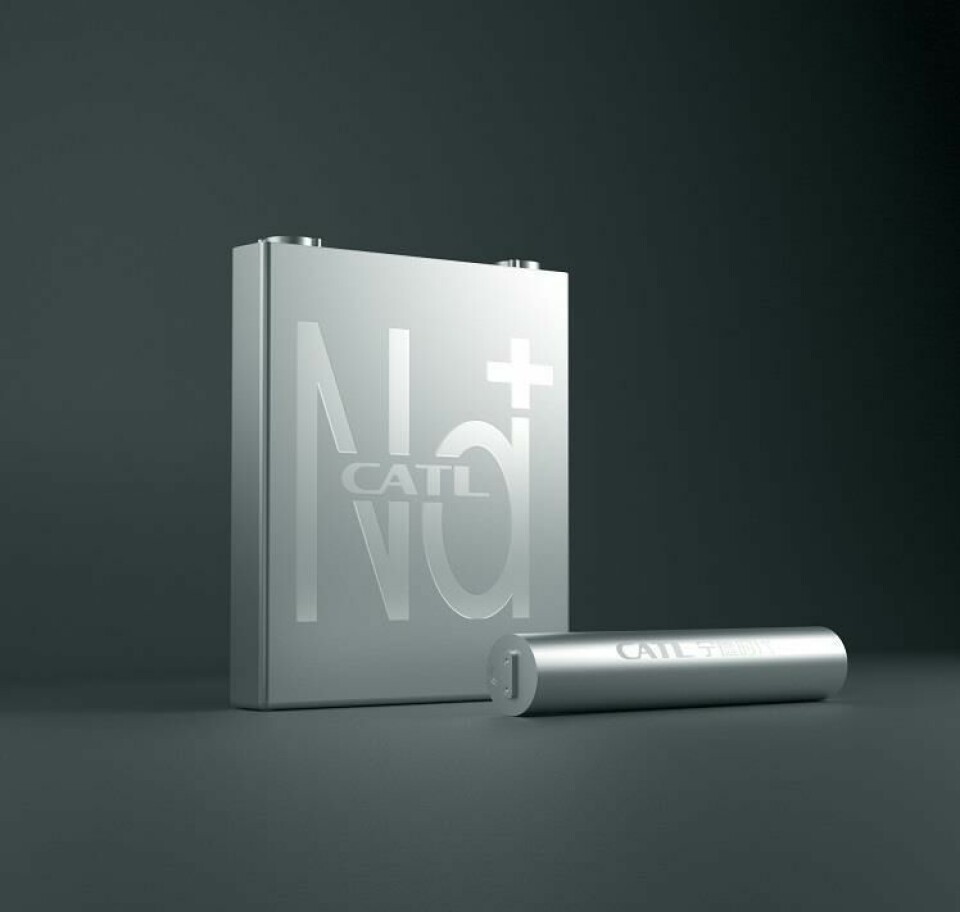
Alternative to lithium-based chemistries: Sodium-ion batteries are emerging as a cost-effective alternative to lithium-ion batteries. Sodium is more abundant and less expensive than lithium, making these batteries an attractive option for large-scale energy storage.
Advantages in terms of cost and availability of raw materials: Sodium-ion batteries benefit from the wide availability and low cost of sodium. While they currently have lower energy density compared to lithium-ion batteries, ongoing research aims to improve their performance, making them a viable option for future EVs and stationary energy storage systems.
Battery Formats
Cylindrical Cells
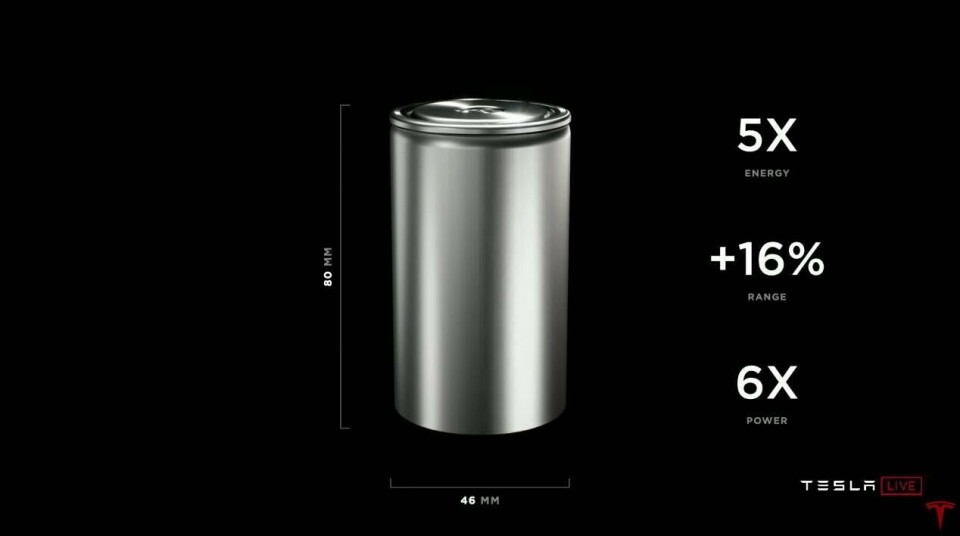
Common uses and manufacturers: Cylindrical cells are one of the most widely used battery formats in the EV industry, popularised by Tesla. These cells are often found in EVs like the Tesla Model 3 and Model S. Major manufacturers of cylindrical cells include Panasonic, LG Chem, and Samsung SDI.
Performance and production advantages and disadvantages:
Advantages:
- High mechanical stability: The cylindrical shape provides robust structural integrity, which helps in maintaining performance under various physical stresses.
- Efficient heat dissipation: The cylindrical design allows for effective thermal management, reducing the risk of overheating.
- Ease of manufacturing: Established manufacturing processes for cylindrical cells contribute to consistent quality and lower costs.
Disadvantages:
- Less efficient use of space: The cylindrical shape can lead to gaps when cells are packed together, resulting in less efficient use of space within the battery pack.
- Weight: The cylindrical format can add to the overall weight of the battery pack compared to other cell formats.
Prismatic Cells
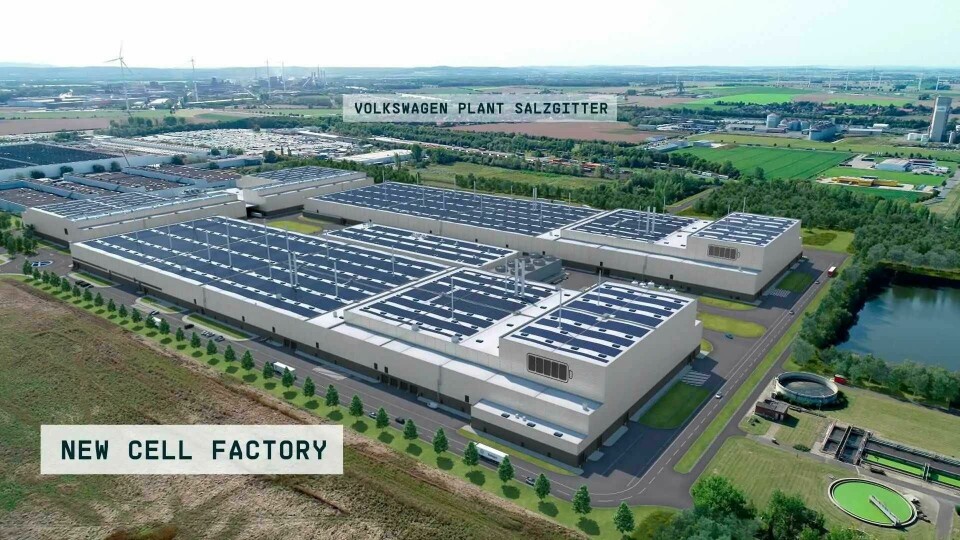
Design and application in the automotive industry:
Prismatic cells are engineered in a rectangular shape, which optimises space utilisation within the battery pack, allowing for more efficient integration into EVs. This design is particularly advantageous for automakers who seek to maximise energy density while minimising the overall size of the battery system. Leading manufacturers such as BMW and Audi have adopted prismatic cells in their EV models, capitalising on their unique configuration to enhance performance and efficiency.
Typically, prismatic cells are encased in a rigid housing, which not only contributes to the structural integrity of the battery pack but also provides additional protection against physical damage and thermal issues. This robust casing is essential for ensuring the longevity and reliability of the cells in the demanding automotive environment, where factors such as vibration, temperature fluctuations, and impact are prevalent.
Comparison with cylindrical cells:
Advantages:
- Space utilisation: Prismatic cells make more efficient use of space within the battery pack, allowing for higher energy density.
- Simplified battery management: The rectangular shape simplifies the integration and connection of cells within the pack.
Disadvantages:
- Thermal management: Prismatic cells may have less efficient thermal management compared to cylindrical cells, requiring more complex cooling systems.
- Manufacturing complexity: The rigid casing and the need for precise manufacturing increase the complexity and cost of production.
Pouch Cells
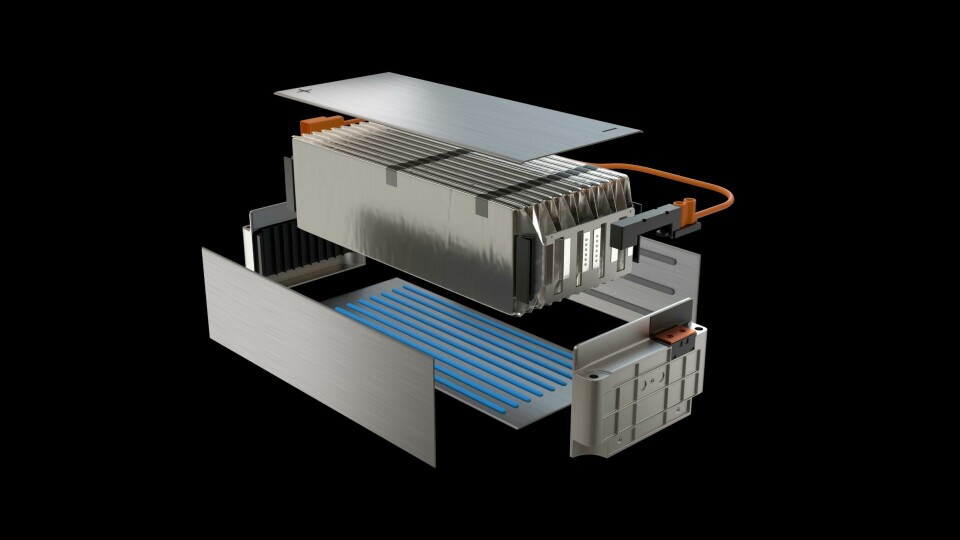
Flexibility and design advantages:
Pouch cells are characterised by their flexible and lightweight design, encased in a soft, flat bag that allows for a high degree of adaptability in various applications. This innovative format is utilised by prominent manufacturers such as General Motors and Hyundai, who leverage the unique properties of pouch cells to enhance their electric vehicle designs.
The flexibility in shape permits for a more creative approach to battery pack layouts while allowing manufacturers to optimise space utilisation within the vehicle, accommodating irregular shapes and maximising energy density.
Addtionally, the absence of a rigid casing contributes to the overall weight reduction of the battery system (lightweighting), which is crucial for improving the efficiency and performance of electric vehicles. This lightweight construction is particularly advantageous in automotive applications, where every gram counts towards enhancing range and efficiency.
Performance and safety considerations:
Advantages:
- Flexibility: The pouch format allows for a more customisable and efficient use of space within the battery pack.
- High energy density: Pouch cells can offer higher energy densities compared to cylindrical and prismatic cells.
Disadvantages:
- Swelling: Pouch cells are prone to swelling over time, which can affect the performance and safety of the battery pack.
- Protection: The soft casing provides less protection compared to rigid casings, requiring additional measures to ensure the cells are not punctured or damaged.
Overview of the main regions producing EV batteries
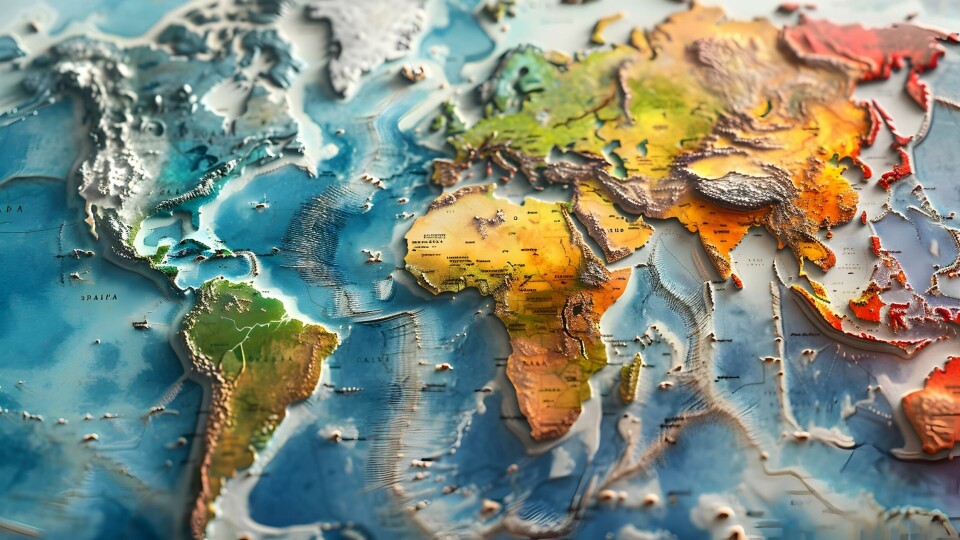
The global production of EV batteries is concentrated in several key regions, each playing a pivotal role in meeting the growing demand for EVs. The major regions include China, Europe, the USA, South Korea, and Japan.
But the battery market is rapidly consolidating in a few key regions, each vying for supremacy as global demand climbs. China dominates, producing nearly 80% of lithium-ion batteries, thanks to its control over the supply chain. Meanwhile, the United States and Europe are racing to bolster their own manufacturing capabilities, with Europe investing heavily to reduce reliance on Asian imports. South Korea also emerges as a significant player, benefiting from robust federal support:
China: China is the world’s largest producer of EV batteries, with companies like CATL and BYD leading the market. The country’s dominance is supported by extensive government incentives and a robust supply chain for raw materials.
Europe: Europe has been rapidly expanding its battery production capacity, driven by strong policy support and significant investments in gigafactories. Countries like Germany, Poland, and Hungary are becoming key players in the battery manufacturing sector.
USA: The United States is ramping up its battery production, spurred by initiatives like the Inflation Reduction Act (IRA). Tesla, with its Gigafactory in Nevada, is a major contributor to the US battery output.
South Korea: South Korea is home to some of the world’s leading battery manufacturers, including LG Chem, SK On, and Samsung SDI. These companies are known for their advanced technology and significant production capacities.
Japan: With companies like Panasonic, Japan has a long history in battery technology and continues to be a significant player in the global EV battery market.
Key Manufacturers and their contributions
CATL (China): Contemporary Amperex Technology Co. Limited (CATL) is the largest EV battery manufacturer globally, known for its high production volumes and technological innovations.
BYD (China): BYD is not only a leading EV manufacturer but also a major producer of EV batteries, supplying both its own vehicles and other automakers.
Tesla (USA): Tesla’s partnership with Panasonic at its Gigafactory in Nevada has made it a significant producer of cylindrical cells used in its vehicles.
LG Chem (South Korea): LG Chem supplies batteries to major automakers like General Motors, Hyundai, and Volkswagen, contributing significantly to the global battery supply.
Panasonic (Japan): Panasonic, in partnership with Tesla, has been a pioneer in producing high-quality cylindrical cells for EVs.
Insights into supply chain and raw material sourcing
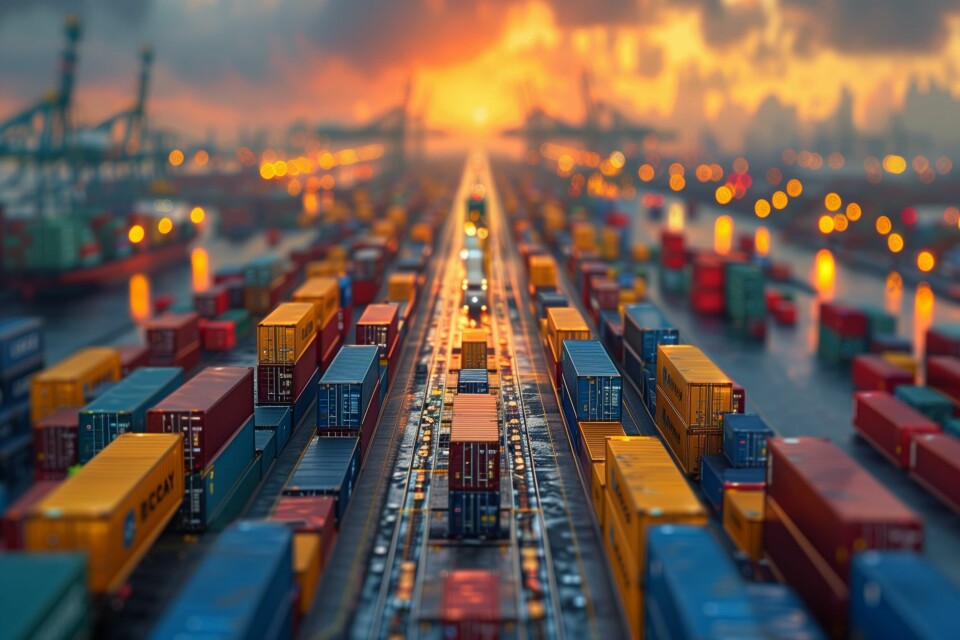
The EV battery supply chain is intricate and heavily dependent on the procurement of essential raw materials, including lithium, cobalt, nickel, and manganese. These materials are critical for the production of lithium-ion batteries, which are the standard in the EV industry due to their high energy density and efficiency.
Lithium serves as the cornerstone of these batteries, enabling effective energy storage, while cobalt enhances stability and performance. Nickel contributes to higher energy density, and manganese plays a vital role in reducing costs and improving battery efficiency.
The sourcing of these materials presents challenges, as their availability is often concentrated in specific geographic regions, leading to concerns about supply security and potential shortages as demand for EVs continues to rise. Ensuring a sustainable and resilient supply chain for these critical raw materials is essential for the future of electric mobility and the broader clean energy transition.
Lithium: Lithium is primarily sourced from countries like Australia, Chile, and China. The extraction and processing of lithium are crucial for the production of lithium-ion batteries.
Cobalt: Cobalt is mainly mined in the Democratic Republic of Congo (DRC), with significant refining capacities in China. Ethical sourcing and reducing dependence on cobalt are ongoing industry challenges.
Nickel and Manganese: These materials are sourced globally, with significant production in countries like Indonesia, the Philippines, and South Africa.
To ensure a stable supply of these raw materials, battery manufacturers and automakers are investing in mining operations and establishing long-term supply agreements. Additionally, recycling of used batteries is becoming increasingly important to reclaim valuable materials and reduce the environmental impact of mining.
Production Volumes
Current Production Volumes of Top Manufacturers
The global production volume of EV batteries has experienced remarkable growth in recent years, reflecting the increasing demand for electric vehicles and the broader shift towards sustainable transportation solutions.
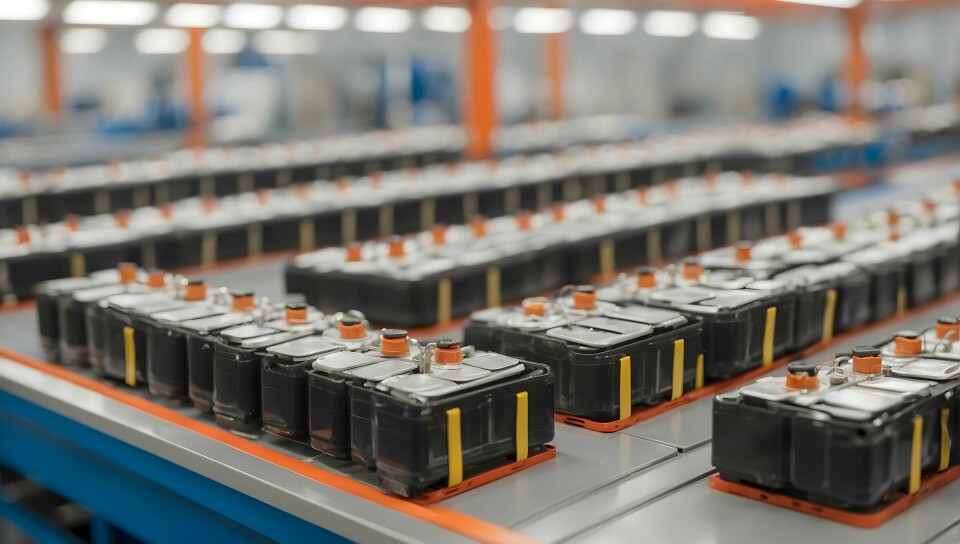
As of 2023, this upward trajectory culminated in a total global production volume that reached approximately 750 gigawatt-hours (GWh); a figure that highlights the significant expansion of electrification and the increasing investments being made in advanced battery technology and manufacturing capabilities across key global regions. The substantial growth trend reflects a concerted effort by governments, automakers and technology companies to enhance production efficiency, innovate in battery design and secure the necessary raw materials, all of which are critical to meeting the surging demand for electric vehicles and supporting the transition to a more sustainable energy future.
The top manufacturers contributing to this volume include:
CATL (China): CATL remains the largest producer with around 243.3 GWh, supplying batteries to major automakers like Tesla, BMW, and Volkswagen.
BYD (China): BYD produced approximately 117 GWh, not only powering its own vehicles but also supplying to other manufacturers.
LG Chem (South Korea): With a production volume of 106.8 GWh, LG Chem serves clients such as General Motors, Hyundai, and Volkswagen.
Panasonic (Japan): Panasonic produced about 55.8 GWh, primarily supplying batteries for Tesla’s EVs.
- SK On (South Korea): SK On contributed 40.8 GWh to the global production, supplying various automakers.
Trends and projections for the next 5-10 years
The demand for EV batteries is expected to continue its rapid growth, driven by increasing EV adoption and advancements in battery technology. Key trends and projections include:
Continued Growth: The global EV battery production volume is projected to grow at a compound annual growth rate (CAGR) of 25-30%, potentially reaching over 2,000 GWh by 2030.
Expansion of Production Facilities: Numerous gigafactories are being planned and constructed worldwide. Europe, in particular, is seeing significant investments with countries like Germany and Hungary emerging as key production hubs.
Technological Advancements: Innovations such as solid-state batteries and improved lithium-ion chemistries are expected to enhance energy density, safety, and reduce costs, further driving production volumes.
Impact of Government Policies and Incentives on Production Volumes
Government policies and incentives play a crucial role in shaping the EV battery production landscape. Key impacts include:
Subsidies and Grants: Governments are providing substantial financial support to encourage the establishment of battery manufacturing facilities. For example, the European Union has allocated funds for the development of gigafactories to reduce dependency on imports.
Regulations and Mandates: Policies mandating the reduction of carbon emissions and the phasing out of internal combustion engine vehicles are accelerating the shift towards EVs, thereby increasing the demand for EV batteries.
Tax Incentives: Tax breaks and incentives for EV manufacturers and battery producers are helping to lower production costs and stimulate investment in battery technology.
Research and Development Support: Governments are funding R&D initiatives aimed at improving battery technology, such as the development of solid-state batteries and more efficient lithium-ion variants.
These policies not only boost production volumes but also foster innovation and ensure a stable supply chain for critical raw materials, thereby supporting the overall growth of the EV industry.
Cost of manufacturing
Breakdown of Cost Components in Battery Manufacturing
The cost of manufacturing EV batteries involves several key components, each contributing to the overall expense.
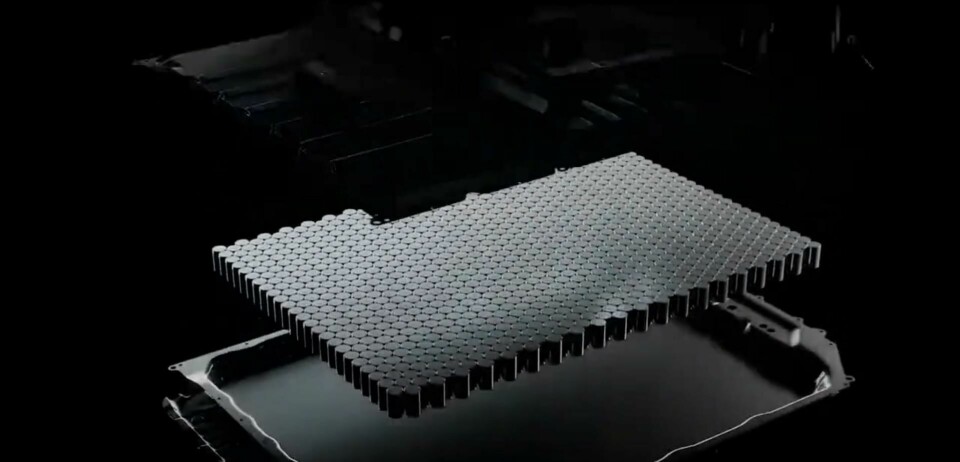
These components include:
Raw Materials: The most significant cost driver, accounting for about 50-60% of the total battery cost. Key raw materials include lithium, cobalt, nickel, manganese, and graphite. The prices of these materials fluctuate based on market demand and supply conditions.
Manufacturing Processes: This includes the costs associated with the production processes such as electrode preparation, cell assembly, formation, and ageing. Advanced manufacturing techniques and automation help in reducing these costs.
Labour Costs: Depending on the region, labour costs can vary significantly. Automation and improved manufacturing efficiencies are reducing the reliance on labour, thus lowering costs.
Capital Expenditures: Investments in facilities, machinery, and equipment contribute to the initial setup costs. Gigafactories require substantial upfront investments but benefit from economies of scale.
Research and Development (R&D): Ongoing R&D is crucial for improving battery technology, increasing energy density, and reducing costs. This includes expenses related to developing new materials and battery chemistries.
Factors Influencing Cost Reductions Over Time
Several factors contribute to the reduction in battery manufacturing costs over time:
Economies of Scale: As production volumes increase, the cost per unit decreases. Large-scale manufacturing facilities, such as gigafactories, significantly reduce costs through bulk purchasing of materials and improved production efficiencies.
Technological Advancements: Innovations in battery chemistries and manufacturing processes enhance energy density and efficiency, leading to cost reductions. For instance, advancements in solid-state batteries are expected to lower costs by eliminating the need for expensive liquid electrolytes.
Supply Chain Optimisation: Streamlining the supply chain and securing long-term contracts for raw materials help stabilise prices and reduce costs. Companies are also investing in recycling technologies to recover valuable materials from used batteries.
Government Incentives: Subsidies, tax breaks, and grants provided by governments encourage investment in battery manufacturing, reducing overall costs for manufacturers.
Cost comparison across different battery chemistries and formats
The costs of battery chemistries and formats vary based on their material composition and manufacturing complexities:
Lithium-Ion (Li-ion) Batteries: Generally, NMC batteries are more expensive than LFP batteries due to the higher cost of cobalt and nickel. However, NMC batteries offer higher energy density, making them more suitable for long-range applications.
Solid-State Batteries: Currently, solid-state batteries are more expensive than traditional lithium-ion batteries due to the nascent stage of technology and higher production costs. As the technology matures, costs are expected to decrease significantly.
Sodium-Ion Batteries: These batteries are projected to be cheaper than lithium-ion batteries due to the abundance and lower cost of sodium. However, their lower energy density makes them less attractive for high-performance applications at this stage.
Battery Formats: Cylindrical cells are typically cheaper to produce than prismatic and pouch cells due to established manufacturing processes. However, prismatic and pouch cells offer better space utilisation and higher energy density, which can justify their higher costs in specific applications.
Pros and Cons of performance – Charging and range
Charging Speed
Differences in Charging Speeds Across Chemistries: Different battery chemistries have varying charging capabilities, significantly impacting the overall performance and convenience of EVs.
Lithium Iron Phosphate (LFP): LFP batteries generally charge slower compared to other lithium-ion chemistries due to their lower energy density. However, they are more tolerant to high charging currents, which can partially offset this disadvantage.
Lithium Nickel Manganese Cobalt Oxide (NMC): NMC batteries typically offer faster charging speeds, making them ideal for long-range EVs. Their higher energy density allows for quicker accumulation of charge.
Solid-State Batteries: While still under development, solid-state batteries promise even faster charging times due to their high ionic conductivity and stability.
Impact of charging infrastructure on performance: The availability and quality of charging infrastructure are crucial for maximising the benefits of different battery chemistries. Fast-charging stations can significantly reduce downtime, particularly for chemistries like NMC that support rapid charging. However, the infrastructure must be robust enough to handle high power outputs without degrading battery health.
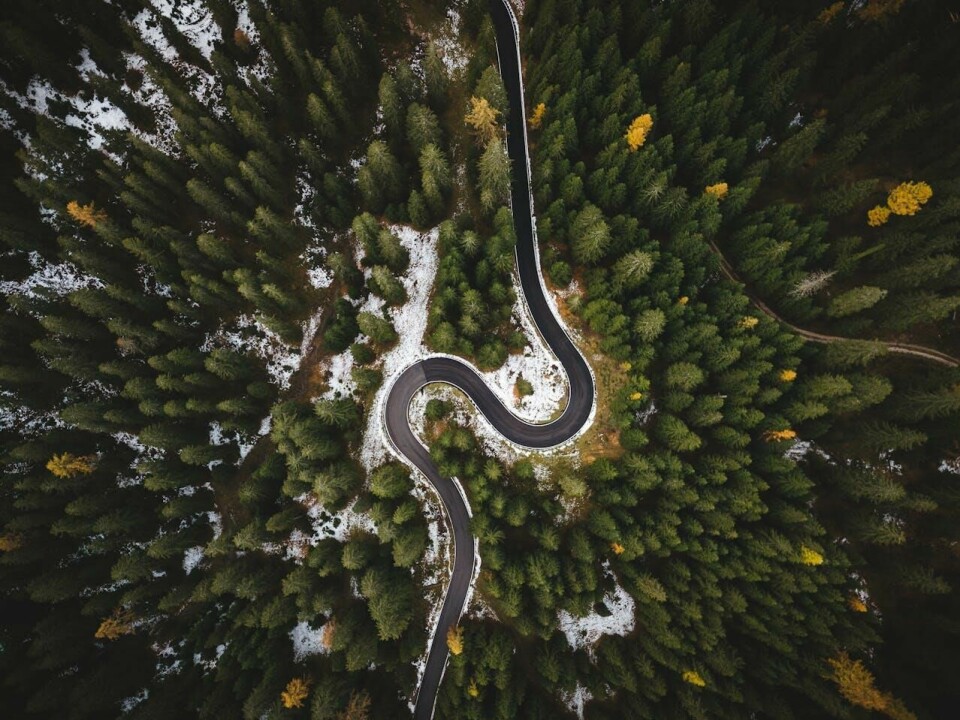
Energy Density and Range:
How Different Chemistries Impact Vehicle Range:
The energy density of a battery has a direct impact on the range of an EV. Higher energy density indicates that more energy can be stored per unit of weight, which is crucial for maximising the distance an EV can travel on a single charge.
This increased storage capacity allows manufacturers to design lighter battery packs without sacrificing performance, ultimately leading to longer driving ranges and enhanced efficiency for electric vehicles. As a result, advancements in battery technology that improve energy density are essential for the widespread adoption of EVs and the reduction of range anxiety among consumers.
- LFP Batteries: While safer and longer-lasting, LFP batteries have lower energy density compared to NMC batteries, resulting in shorter ranges.
NMC Batteries: These batteries offer higher energy density, providing longer ranges suitable for long-distance travel. For instance, vehicles like the Tesla Model 3 and Chevrolet Bolt use NMC batteries to achieve ranges exceeding 300 miles on a single charge.
Real-World Performance vs. Laboratory Results:
Real-world driving conditions often result in lower ranges than those achieved in laboratory settings. Factors such as driving speed, temperature, and terrain can significantly impact battery performance. For example, extreme cold can reduce the efficiency of NMC batteries, while LFP batteries perform more consistently across different temperatures.
Durability and Lifespan
Cycle Life and Degradation Rates: The longevity of a battery is measured by its cycle life – the number of complete charge and discharge cycles it can undergo before its capacity drops significantly.
LFP Batteries: Known for their long cycle life, LFP batteries can withstand thousands of cycles with minimal degradation, making them ideal for applications requiring frequent charging.
NMC Batteries: While offering higher energy density, NMC batteries typically have a shorter cycle life compared to LFP. However, advancements in battery management systems are improving their longevity.
Practical Implications for EV Owners: For EV owners, the choice of battery chemistry affects maintenance costs and the overall lifespan of the vehicle. LFP batteries, with their longer cycle life, may result in lower long-term costs and less frequent battery replacements. Conversely, NMC batteries provide better performance and range but may require more careful management to maintain their lifespan.
Safety and Thermal Stability:
Safety Features and Concerns for Each Chemistry: Safety is a paramount concern in battery design, with different chemistries offering varying levels of thermal stability.
LFP Batteries: Highly stable and less prone to thermal runaway, LFP batteries are considered safer, making them suitable for applications where safety is a priority.
NMC Batteries: These batteries have higher energy densities but are more susceptible to thermal runaway, necessitating advanced thermal management systems to ensure safety.
Recent Advancements in Improving Safety: Recent advancements aim to enhance the safety of all battery chemistries. For instance, solid-state batteries eliminate the flammable liquid electrolyte, significantly reducing the risk of fires. Additionally, innovations in battery management systems and cooling technologies are improving the safety profiles of NMC and other high-energy-density batteries.
Conclusion
In summary, the landscape of EV battery technology is evolving rapidly, driven by advancements in battery chemistries and formats. Lithium-ion batteries, particularly the NMC and LFP variants, dominate the market due to their balanced performance and safety features. Emerging technologies like solid-state and lithium-sulphur batteries promise significant improvements in energy density and safety, while sodium-ion batteries offer a cost-effective alternative for future applications.
Battery formats, including cylindrical, prismatic, and pouch cells, each have unique advantages and challenges. The choice of format impacts the overall design, performance, and manufacturing efficiency of EV batteries. Key regions like China, Europe, the USA, South Korea, and Japan continue to lead in battery production, with major manufacturers like CATL, BYD, Tesla, LG Chem, and Panasonic driving innovation and capacity expansion.
Looking ahead, the global production volume of EV batteries is projected to grow substantially, supported by government policies, subsidies, and incentives. Continuous cost reductions, driven by economies of scale, technological advancements, and optimised supply chains, are making EVs more accessible and affordable.
The future of EV battery technology hinges on ongoing research and development efforts to enhance performance, extend battery life, and ensure safety. As the industry changes, collaboration between manufacturers, governments and research institutions will be key to overcoming challenges and unlocking the full potential of EVs.