Taking care
OEMs are adopting a more proactive approach to employee wellbeing, including improved ergonomics
As the baby-boom generation grows older and the average age of employees rises, automotive manufacturers are responding to the need for more ergonomic workplaces. In addition, the younger generation coming through is bringing with it a different set of values. “In order to retain members of ‘Generation Y’ at the company over the long term, we will have to offer them attractive workplaces,” explains Mathias Keil, head of industrial engineering methods at Audi. Keil also cites electrification, lightweight construction, greater model diversity and a general increase in the technical complexity of cars as having a strong influence on working requirements and the content of work today, not only in the area of production.
“Other drivers of this development are Industry 4.0 and human-robot cooperation, as well as the worldwide expansion of our production network,” says Keil. “For example, the expansion of our production network in regions with other cultures means that we have to consider different body sizes and the specific conditions of those cultures in our planning procedures and standards. The focus is on the people, no matter whether in Ingolstadt, Neckarsulm, Mexico, China or India.”
Volkswagen also takes a people-first approach, providing free, comprehensive preventive medical examinations at its locations both in Germany and around the world. The company is constantly improving its programme to help maintain and improve the health, fitness and performance of its workforce.
In 2014, the manufacturer introduced a series of measures linked to preventing problems before they occur. The company’s ‘Fit the Office’ behavioural ergonomics programme addresses employees working in an office environment, while the key objective of ‘Fit in the Factory’ is to reduce physical stresses and strains on those working on the shopfloor.
The OEM staged its first Ergonomics Days last year, with activities to help improve office ergonomics, including new lighting concepts and advice for people who sit down for a large portion of their day. It also addressed ergonomics in production and logistics.
Becoming fitter in the workplace
Other preventative and holistic programmes include a weight-loss and healthy eating campaign operated by Volkswagen South Africa, as well as a company run in Munich. When there are issues regarding workplace ergonomics, Volkswagen relies on its web-based ‘Massnahmen@web’ (‘measures@web’) system.
Bentley Motors also prioritises health and fitness as a preventative measure to ensure a better working environment. Launched in 2014, the ‘BeFit at Bentley’ programme encourages employees to adopt a healthy lifestyle, focusing on the key areas of weight and nutrition; stress and depression; the corporate step challenge; and exercise and back care.
Audi also continually examines and develops its workplace ergonomics in a proactive and preventative way. In 2005, it introduced an ergonomics assessment procedure with the aim of taking appropriate measures to improve ergonomics in different production areas. This procedure was integrated into the planning process in 2008. “By assessing components in terms of ergonomics, we can identify assembly situations that require a disadvantageous posture in good time, and can optimise them so that the posture required during assembly is improved,” says Keil.
In 2011, Audi introduced a targeting process for employees with restricted capabilities. “This allows us to take into consideration the structure of our workforce and to specify exactly how many special workplaces we need (sitting, for example) for each new automobile,” says Keil. “We are reacting proactively to the challenges of the future with the Audi ergonomics strategy ‘We for us. Active into the future’. Numerous projects are currently running in six ‘action areas’ so that we can improve ergonomics at Audi even further. Our focus is on creating more attractive and more productive jobs in which our employees feel comfortable.”
The Chairless Chair
As part of this focus, Audi has introduced the high-tech, carbon fibre ‘Chairless Chair’, which allows employees to sit without having a conventional chair present, reducing the strain on the legs and helping to improve posture. “The Chairless Chair combines ergonomics and productivity,” says Keil. “The user’s bodyweight is transferred to the floor through two adjustable carbon-fibre elements. It allows the employee to sit in an ergonomically favourable position instead of standing. It improves posture and reduces the weight on the legs. Normal chairs and stools, which are used as temporary aids today on some sections of the assembly line, are no longer required.
“And optimal posture during the assembly process increases process quality. The Chairless Chair helps to reduce health-related absenteeism, to enhance our employees’ feeling of wellbeing and to integrate employees with physical limitations.”
As part of its strategy to involve employees in the process of improving workplace ergonomics, Audi has been collecting comments from employees on the Chairless Chair. “The feedback was very positive during the pilot phase at our plant in Neckarsulm [Germany],” says Keil. “And we have already received many important suggestions on how we can further improve the Chairless Chair. The feedback from our employees is a key criterion. It isn’t technology that influences the improvement of ergonomics at the company, but the good ideas of our employees.”
The work is not yet complete on the Chairless Chair, as Audi is working with Swiss start-up Noone, the manufacturer, to further develop it into a series-compatible product and then to deploy it in workplaces where it will be beneficial.
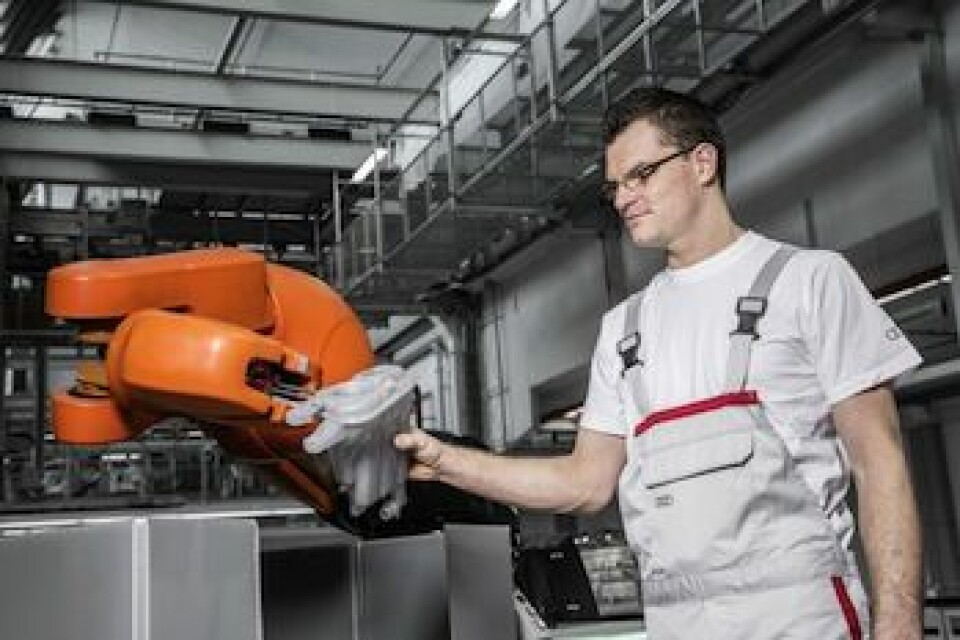
Another part of Audi’s strategy for improving ergonomics in the workplace can be found at its plant in Ingolstadt, also Germany, where the company has deployed fenceless robots that work directly with employees without a safety barrier.
Previously, workers had to bend down to take out coolant expansion tanks from material boxes, but now robots will take over the lifting and pass the components to employees. This removes the strain from workers of reaching across long distances to pick things up, as well as bending down. The robot has a soft protective skin as well as integrated safety sensors, meaning it can work side-by-side with assembly line workers without any concerns about causing injuries.
This is not Audi’s only use of robots, as the company deployed the same type of machine in its A4 bodyshop at Ingolstadt in 2013. The robots support the employees by applying adhesive to bonded seams, leaving the human operatives simply to put the body parts in place and start the automatic procedure.
Audi has also been working with other brands in the VW Group to promote a more ergonomic working environment. Along with VW and Porsche, the company has been involved in a research project entitled ‘Ageing Healthily and Appropriately in the Automotive Industry: Career-Long Participation and Inclusion’. The programme is funded by Germany’s Federal Ministry of Labour and develops tools and initiatives to maintain employees’ health and capacity throughout their working lives.
Furthermore, Audi and VW have produced a handbook that presents a standardised approach to ergonomics in automotive product development. The manual is being rolled out to other brands in the group during 2015.