Reinventing the wheel: the race towards sustainable tyre production
Nokian Tyres is building the world’s first zero-carbon tyre factory, with Michelin, Continental, Bridgestone, and Pirelli leading the charge with recycled materials, bio-based components, and innovative sustainable production methods.
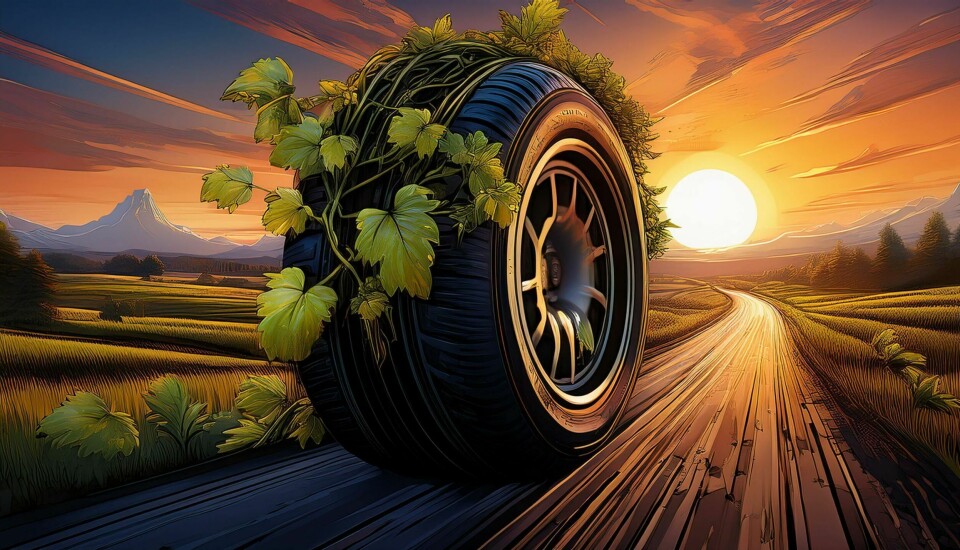
Tyre facilities released over 3.5 million metric tons of carbon dioxide in the US alone - back in 2017
US Tyre Manufacturers Association
Automotive production is increasingly finding novel ways to boost its sustainability footprint. But a lot of this focus has been on what we may term ‘internal components’; an oversight which is costing automotive sustainability efforts far more than first meets the eye. An example of this primary focus can be found in the move towards bio-materials in the production of everything from steering wheels, to door trims, and even electric vehicle (EV) batteries. Impressive and far-reaching projects, no doubt.
In this particular approach, Renault, for example, is using kenaf, a fast-growing plant, for dashboard components, while BMW is tapping into flax for their cooling systems and interiors. Bio-based composites made from flax and wood pulp by tier-suppliers, Bcomp and UPM, are finding applications across car frames and dashboards.
These circular efforts are making more than a mere dent in the carbon output that comes from automotive manufacturing activities, and taken as a whole, are setting the tone for the entire industry in terms of sustainable and circular manufacturing processes.
”Nokian Tyres is working to replace fossil-based tyre materials with sustainable ones”
Teemu Soini, VP, Innovations & Development at Nokian Tyres
But beyond the production of these internal components, tyre production is a key, carbon-intensive - yet often-overlooked process. In 2017, tyre facilities released over 3.5 million metric tons of carbon dioxide in the US alone, according to the US Tyre Manufacturers Association; a footprint roughly equivalent to that of the Congo, a nation of nearly 87 million people that same year. But of course, tyre production has only increased since then - as has the global population.
And although the primary environmental impact of tyre production is generated during their use phase - accounting for roughly 80% of their total carbon footprint according to The British Tyre Manufacturers Association - their total global carbon footprint is monumental, with 3 billion new tyres being produced each year, and about 800 million becoming annual waste, according to the journal, Science of The Total Environment.
In other words, even though emissions ‘per tyre’ may be relatively low in relation to the whole, their total environmental impact is huge.
Nokian Tyres on track to construct the world’s first net-zero tyre factory
Now, fully focused on this mountainous challenge, Finnish manufacturer, Nokian Tyres, has set out to construct the world’s first zero-carbon tyre factory.

The facility, to be constructed in Romania, and bolstered by a €150 million loan ($165.5m) from the European Investment Bank (EIB) earlier this year, is going all-in on a trailblazing sustainability project of immense proportions.
Leena Kaipainen, VP, Group Treasurer said: “Our Romania factory is a testament to our dedication to sustainability. It will set a new industry standard by utilising solely CO2-free energy sources and incorporating highly automated, energy-efficient processes.”
Beyond material traceability, material production is the crucible of sustainable tyres, and Nokian’s projects are drawing a lot of attention across the automotive world. And fortunately, they are not the only tyre production company that is involved in sustainable production.
Nokian Tyres’ materials and their alternatives
Material | % of a tyre (approximately) | Sources | Replacements and alternatives |
---|---|---|---|
Synthetic rubber | 23 | Crude Oil | - Renewable-sourced polymers - Mass-balance approach - Recycled rubber crumbs |
Natural rubber | 22 | Natural Rubber | - Guayule as an alternative for natural rubber - Recycled rubber crumbs |
Fillers | 28 | Silica, Carbon Black | - More extensive use of recycled carbon black is under investigation - Active research of different renewable fillers, for instance forest industry’s side stream-based materials |
Reinforcement materials | 15 | Steel, Textile | - Recycled steel is used in reinforcement materials - Increasing the share of recycled steel in reinforcement materials is being researched - Researching the use of renewable or recycled sources for textiles |
Chemicals | 12 | Several Sources | - Increasing renewable or recycled oil and resin content in tyres - Reduction and elimination of harmful chemicals and search of alternative options from either recycled or renewable resources |
Source: Nokian Tyres
Michelin’s mission to 100% sustainable sources: 2050
Michelin, another stalwart in the industry, is also taking strides towards sustainable tyre production. The French tyre giant aims to produce tyres from 100% sustainable sources by 2050. Today, its production process already incorporates natural rubber, vegetable oils, and recycled materials. But Michelin’s environmental commitment does not end there.
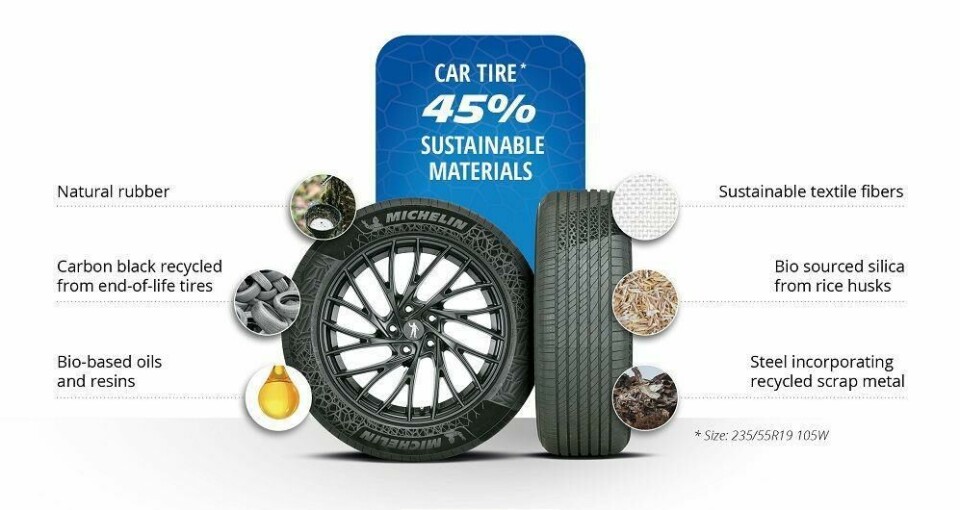
The company’s commitment to sustainability is evident in its recent production achievements. One of these is its carbon-reduced, road-approved tyre; manufactured out of 45% sustainable materials, which was awarded the AutomotiveINNOVATIONS Award 2023. The award is an inadvertent recognition of Michelin’s progress towards its ambitious goal of developing tyres made entirely from sustainable materials by 2050.
The 45% sustainable tyre, unveiled in 2022, incorporates innovative technologies that will be integrated across its standard tyre offerings by 2025. The milestone is a significant step forward in Michelin’s objective to develop new sustainable materials and promote global production using exclusively renewable or recycled resources.
“We are preparing all our plants so that they can use as much renewable energy as possible”
Dr. Bernhard Trilken, Head of Manufacturing and Logistics at Continental Tyres
Michelin has also invested in partnerships, such as with Swedish firm Enviro, to develop technologies that allow for the recycling of old tyres into new rubber, increasingly moving its production focus towards circular economic practices in its tyre production. Alongside this, and on the road to 2050, the company has committed to reducing its total CO2 emissions by 50% by 2030, and is producing tyres that are lighter and more fuel-efficient to reduce emissions during vehicle use.
Bridgestone: greening tyres inside and out
Bridgestone, the world’s largest tyre manufacturer, has also laid out a comprehensive sustainability agenda, spanning both production and supply chains. Explicitly committed to sustainable production and the circular economy, the company is working towards scaling up recycled and renewable materials throughout its tyre production ecosystem. By 2030, the company aims to use 40% of these materials across the scope of its manufacturing operations.
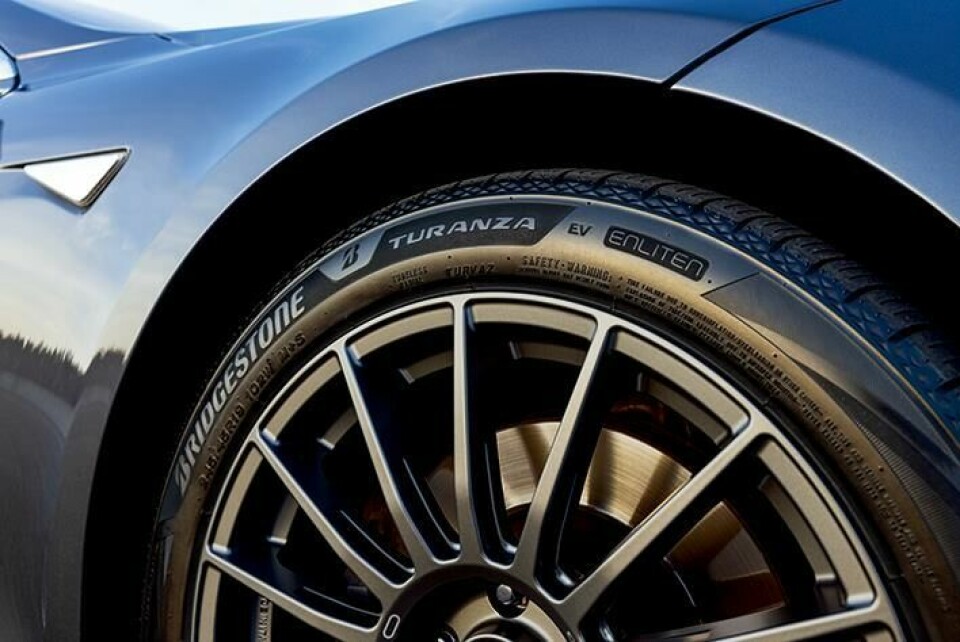
Bridgestone’s efforts are wide-ranging; from utilising natural and biomass-derived rubber to reducing fuel consumption through low-rolling-resistance tyres that make vehicles more energy efficient. The company is also actively manufacturing products to reduce carbon footprint across their use-phase, as well as boosting circularity by recycling old products. In 2023, it outperformed its 37% sustainability targets, achieving 39.6% recycled and renewable resources across its total operations.
”By achieving CO2-neutral production at the Lousado plant, Continental has set a new benchmark for the tyre industry”
In May of the same year, Bridgestone launched Turanza EV, an electric vehicle tyre that incorporates a significant amount of renewable and recycled materials. The tyre features 20% natural rubber, 18% recycled synthetic rubber, and recycled carbon black.

Source: Bridgestone
To ensure the sustainability of these materials, Bridgestone also utilises the ISCC, through the mass balance approach, allocating ISCC-certified circular butadiene rubber, styrene butadiene rubber, and carbon black.
Early this year, the Japanese producer introduced the REGNO GR-XIII in Japan. This tyre also incorporates synthetic rubber produced using the ISCC mass balance approach, further reducing its carbon production footprint and contributing to a circular economy.
Continental’s dandelion-derived tyre production
Not to be outdone, Continental has focused on alternative raw materials and circularity. Its flagship project, “Taraxagum,” is pioneering the use of dandelion rubber to replace traditional rubber trees.
Dandelions can grow in harsher climates, requiring less water and transportation, potentially mitigating the ecological burden posed by the traditional rubber industry.
The company is also making headway in tyre circularity, having developed innovative processes to extract and reuse high-quality rubber from used tyres, which is then reintroduced into the production of new ones. The producer has also taken steps to reduce energy consumption in its production facilities, focusing on renewable energy sources to reduce its carbon footprint.
Continental’s CO2-neutral tyre plant in Lousado, Portugal
Although not ‘Net-Zero’, like Nokian’s Romanian plant, Continental recently achieved a significant milestone in its sustainability journey by successfully implementing a CO2-neutral production process at its tyre plant in Lousado, Portugal.
The Lousado facility has an annual production capacity of 18 million tyres, and so its CO2-neutral production footprint marks a major step towards the company’s broader goal of achieving complete CO2-neutral production across all its tyre plants by 2040. Lousado’s CO2-neutral status is made possible by an innovative electric boiler that generates steam from green electricity instead of gas.
By utilising a combination of self-generated solar power and renewable electricity from the grid, Continental has been able to replace natural gas, a primary energy source for steam generation in tyre plants. Steam is crucial in the vulcanisation process, transforming raw rubber into the flexible and elastic material used in tyres.
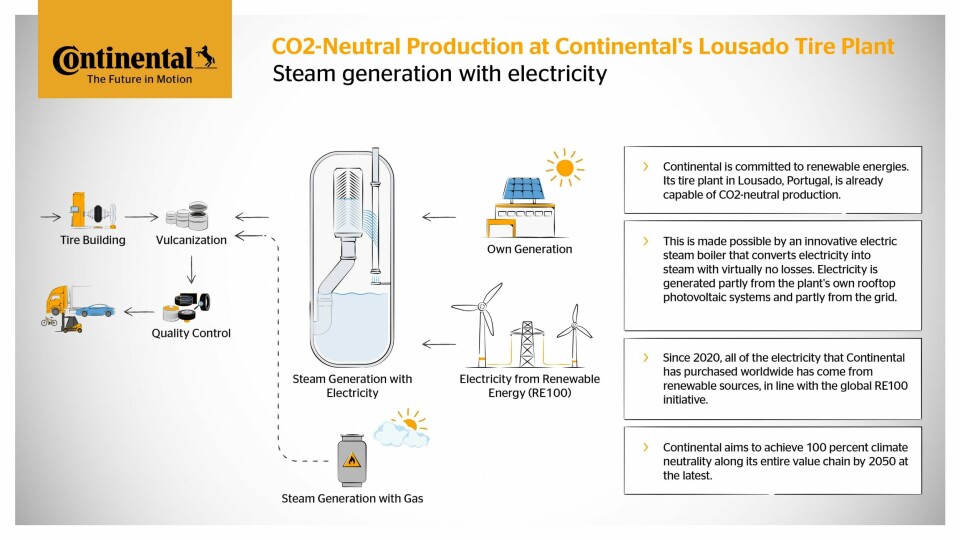
Source: Continental
The Lousado plant’s success in achieving CO2-neutral production demonstrates that even large-scale tyre manufacturing facilities can adopt sustainable practices.
Dr. Bernhard Trilken, Head of Manufacturing and Logistics at Continental Tyres said: “We are preparing all our plants so that they can use as much renewable energy as possible. The commissioning of our electric steam boiler in Lousado is the start of an exciting learning curve.”
The electric steam boiler at Lousado operates by converting solar and other green electricity into steam with minimal energy loss. The technology involves pumping water through the boiler and spraying it onto electrodes, where electric current creates heat to evaporate the water into steam. To ensure stable and reliable operations, the Lousado plant maintains a conventional gas boiler as a backup. This flexibility allows Continental to adjust production based on fluctuations in renewable energy availability and other environmental factors.
In addition to its CO2-neutral production, the Lousado plant has achieved industry-leading energy efficiency. Continental’s tyre division reduced its annual energy requirements by around 150 gigawatt hours in 2023 alone, equivalent to the average annual electricity supply of 12,500 single-family homes. This reduction was achieved through various energy-saving measures, such as thermal insulation.
Continental’s commitment to sustainability extends beyond its production processes. The company has also been actively working to reduce its carbon footprint throughout the entire product lifecycle.
The UltraContact NXT, a series tyre produced at Lousado, is one example of Continental’s efforts to create more sustainable products. By achieving CO2-neutral production at the Lousado plant, Continental has set a new benchmark for the tyre industry.
Carbon neutrality and net-zero are quite similar but net-zero refers to a broader definition of gases. Both definitions allow for ‘carbon-offsetting’ Carbon neutralityCarbon neutrality means that the carbon dioxide emitted into the atmosphere must be equivalent to the carbon dioxide being removed from the atmosphere. i.e. only referring to carbon dioxide (CO2). ‘Carbon offsetting’ can be used to achieve this goal. Net-zeroNet-zero means that a wider range of greenhouse causing gases (carbon, methane, nitrous oxide etc.) emitted into the atmosphere must be equivalent to the greenhouse gases being removed from the atmosphere. This also means that ‘carbon offsetting’ can be used to help achieve this goal.