BMW’s Debrecen plant hits fossil-free milestone with gas-free, sustainable Paintshop
The Debrecen plant, set to launch pre-series production of the Neue Klasse, boasts a modern paint shop powered by renewable energy. Innovative technologies like power-to-heat, Heat Grid, and eRTO look to achieve maximum resource efficiency and sustainability.

The BMW Group’s new Debrecen plant has reached a significant milestone with the commissioning of its state-of-the-art paint shop. Marking the first technology to go live at the new Hungarian facility, this paint shop operates entirely without fossil fuels, setting a new standard in BMW’s global production network. This achievement is aligned with BMW’s iFACTORY principles, emphasising sustainability and innovation.
What sets the Debrecen plant apart in pre-series production?
At the end of the year, BMW will launch pre-series production of the Neue Klasse at the Debrecen site. The paint shop, which spans 33,000 square meters, will initially handle 30 vehicle bodies per hour, with potential for increased capacity.
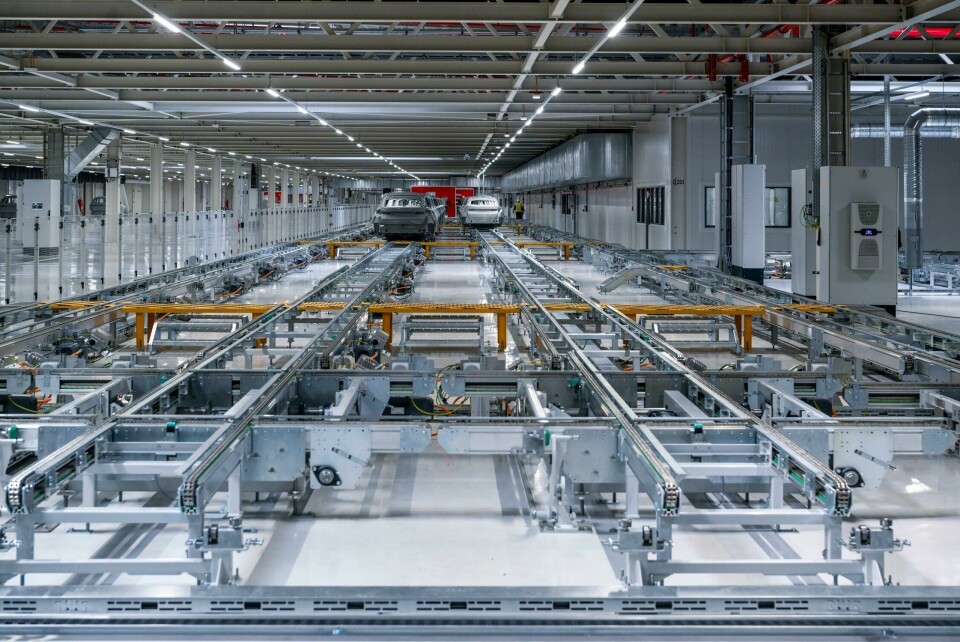
The facility represents a blueprint for future BMW plants, combining cutting-edge systems like power-to-heat, Heat Grid, and eRTO to achieve maximum resource efficiency.
How does the power-to-heat process reduce emissions?
The Debrecen paint shop’s power-to-heat technology is central to its fossil fuel-free operation.
By relying entirely on electricity, sourced from renewable energy, the facility has significantly reduced its carbon footprint. Although this approach increases electricity consumption, it eliminates the need for natural gas, making the plant one of the most environmentally friendly in BMW’s network.
What innovations drive energy efficiency at Debrecen?
BMW’s Heat Grid project exemplifies energy efficiency, integrating several measures to recover and reuse energy. A multivalent storage boiler collects waste heat from various processes, reducing overall energy consumption by up to ten percent.
Additionally, operating the system at a lower water supply temperature further enhances energy savings, showcasing the plant’s commitment to reducing environmental impact.
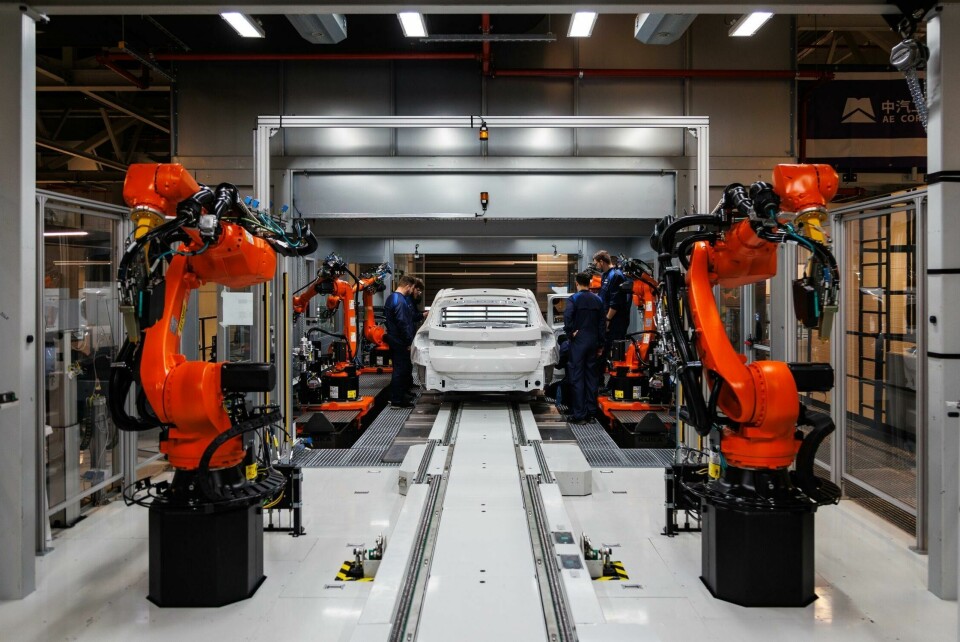
How does the eRTO process improve exhaust purification?
Debrecen’s paint shop also introduces the eRTO (electric regenerative thermal oxidation) process, which purifies exhaust air using high temperatures achieved through electricity. This method offers superior energy efficiency by retaining heat within the system, making it another innovative feature of BMW’s sustainable production strategy.
What role does digitalisation play in Debrecen’s operations?
Advanced digitalisation underpins the efficiency of Debrecen’s paint shop. Automated Guided Vehicles (AGVs) and Automated Surface Inspection (AOI) systems streamline operations, from transporting car bodies to ensuring flawless paint finishes. This comprehensive digital approach, coupled with virtual planning and training, has paved the way for a highly efficient and sustainable production environment.
With the commissioning of its innovative paint shop, BMW’s Debrecen plant is poised to set new benchmarks in sustainable automotive production, embodying the future of the BMW iFACTORY vision.