BMW’s San Luis Potosí plant in Mexico is driving global sustainability with solar power, water reuse, and AI-driven carbon reduction
BMW’s San Luis Potosí facility in Mexico exemplifies sustainability in action. From solar energy to water recycling and AI-driven efficiency, the plant demonstrates how local, effective green innovation can reshape automotive production on a global scale. Following a site visit, AMS delves into the facility’s world-leading sustainability intiatives. Ilkhan Ozsevim reports.
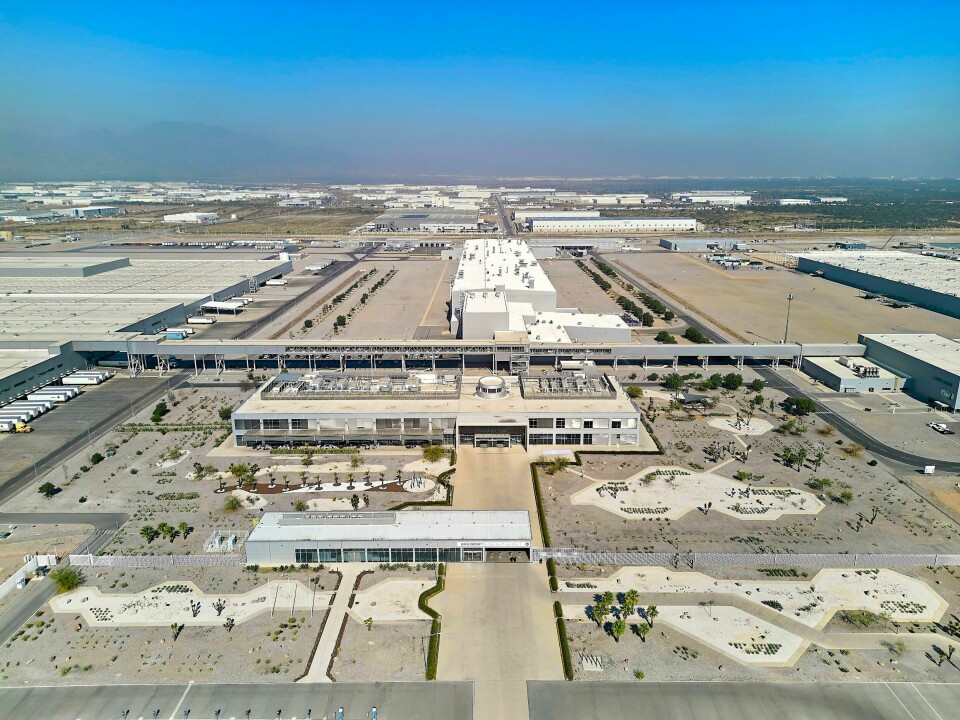
According to the locals, San Luis Potosí is where the sun is born. The central Mexican state is drenched in an average of 2,872 hours of sunshine per year, a rate significantly higher than the global average of around just 2,000 hours. Beyond notions of provincial inadequacies, the Mexican plant exemplifies BMW’s commitment to sustainability through its ambitious energy initiatives, one of the central being solar.
Solar Fields: Harnessing clean energy for production
Located in a region accustomed to such abundant sunlight, one hundred per cent of the electricity used at San Luis Potosí is provided by solar power, with the facility’s integrated photovoltaic system (one of the largest such systems in all of Mexico) covering 71,000 sq. m and currently generating 13% of the plant’s total electricity needs.
The solar array has a capacity of 28.3 MWp (megawatt-peaks) - enough to power around 14,000 homes. The remaining 87% of the site’s needs are sourced from a certified external photovoltaic facility, ensuring the plant operates entirely on renewable energy. But works are already underway for expansion…
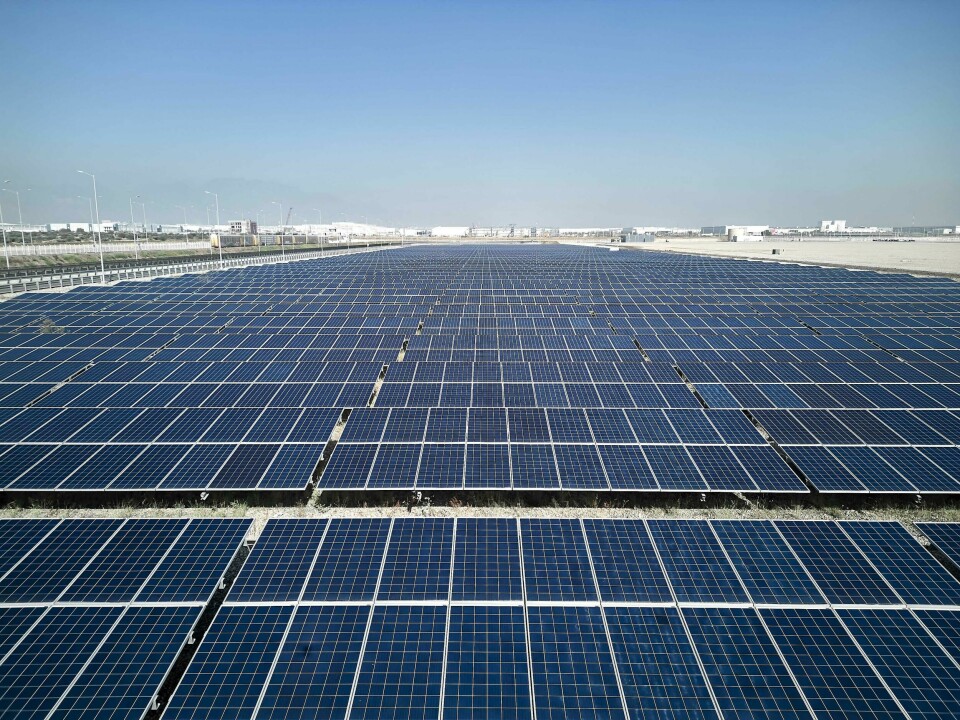
Pilar Álvarez, the plant’s Environmental Manager, highlighted San Luis Potosí’s forward-thinking approach: “By 2025, we plan to double our on-site solar panel coverage to 140,000 sq. m, boosting our on-site solar capacity to 10 megawatts.”
The goal is to generate more than 20% of the plant’s electricity requirements directly on San Luis Potosí’s premises.
“This will significantly enhance our energy self-sufficiency and further reduce our carbon footprint,” says Álvarez. This photovoltaic expansion underlines BMW’s strategic commitment to clean energy solutions, demonstrating how both local automotive manufacturing can, and must, align with global sustainability goals.
Supporting electrification: San Luis Potosí’s expansion for High Voltage Battery Production Centre
Building on this already vibrant renewable energy foundation, the site is presently driving a transformative expansion to include a High Voltage Battery Production Centre. The initiative involves a €800 million investment ($820.4m), with €500 million ($512.7m) dedicated to establishing Mexico’s first lithium battery production facility for electric vehicles.
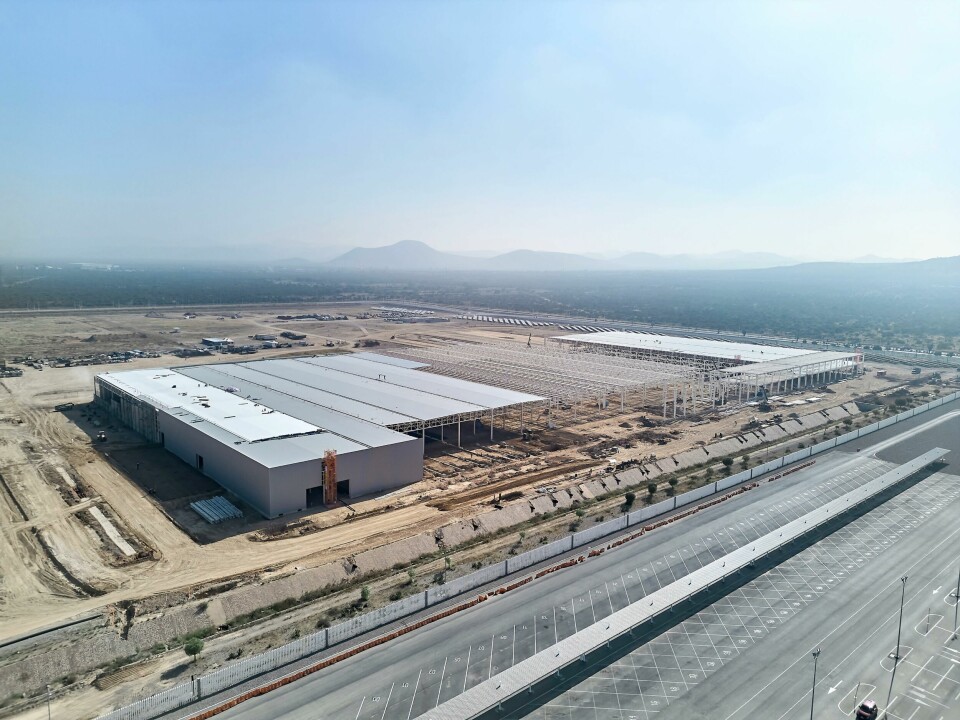
Spanning an additional 80,000 sq. m, the expanded facility is set to begin pre-series production by the end of 2025, supporting the rollout of BMW’s Neue Klasse electric vehicles by 2027.
The project also includes expanding the plant’s body shop, assembly line, and logistics areas to ensure seamless integration of the new production capabilities. These upgrades will also create approximately 1,000 new jobs, reinforcing San Luis Potosí’s status as a critical hub in BMW’s global electrification strategy.
In alignment with BMW Group’s 2030 CO₂ reduction objectives, the San Luis Potosí plant aims to reduce production-related emissions by 80% per vehicle.
Water reuse for the paintshop and production: Closing the loop
In this semi-arid region of Mexico, water conservation is both an environmental necessity, and a strategic imperative. The plant’s state-of-the-art water management system is another testament to the carmaker’s globalised dedication to sustainable practices, and its innovative approaches to energy usage in production.
”The bioreactor, which utilises millions of bacteria to break down organic pollutants, represents a groundbreaking advancement within BMW’s global operations”
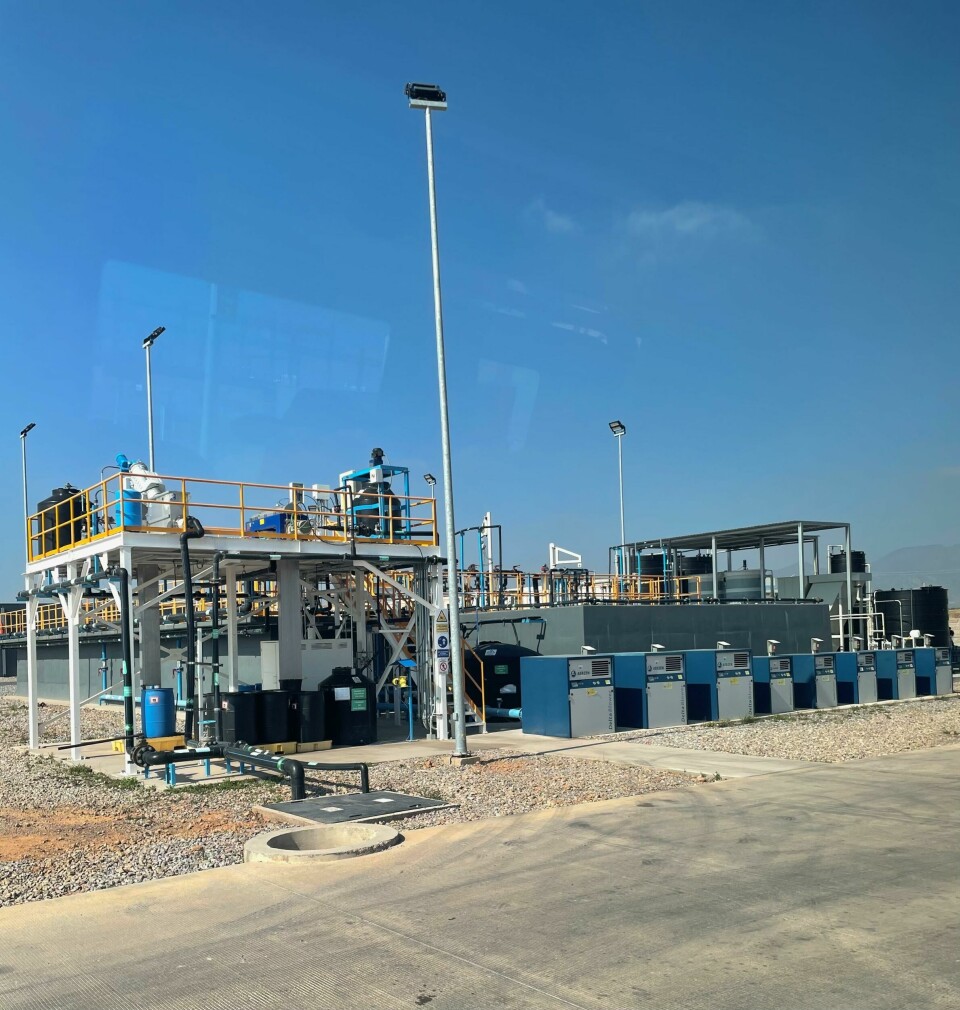
Automotive Manufacturing Solutions
With an annual investment exceeding €3 million ($3.1 million) the facility has established a comprehensive water treatment and reuse programme, particularly within its paint shop, which is the most water-intensive stage of the entire production footprint.
José Julián Ledezma Sánchez, Paintshop Process and Materials Manager, elaborated on the innovative processes employed: “We are the first BMW plant to implement a bioreactor specifically for industrial wastewater, unlike others that treat sanitary wastewater only.
“This innovation enables us to recover and reuse wastewater across several processes such as equipment cleaning and paint application.”
The bioreactor, which utilises millions of bacteria to break down organic pollutants, represents a groundbreaking advancement within BMW’s global operations. By recycling treated water back into production, the plant achieves a key performance indicator of 1.8 cubic metres (m3) of water per vehicle, a benchmark for sustainability in automotive production. Additionally, nano-filtration technology, inspired by the food industry, ensures the further production of deionised water, which is critical for high-quality paint finishes.
”San Luis Potosí’s ongoing commitment is to treat 100 percent of the plant’s wastewater”
When asked about water usage per vehicle, Sánchez noted: “Our key performance indicator is 1.8 m3 per unit, including all domestic and industrial water usage.”
This water consumption per vehicle at 1.8 m3 stands out significantly when compared to the global average in automotive production. In 2020, for example, the BMW Group reported its global average as being 2.25 m3 per vehicle produced, while the worldwide average is typically estimated to range between 3.5 and 4.0 m3.
Read more BMW Stories
A class of its own: transforming BMW production for next-gen EVs
Smart Factory: BMW’s digital production at San Luis Potosi, Mexico
Even Tesla reported its global average as 2.48 m3 in its 2023 Impact Report. San Luis Potosí’s achievement is particularly impressive because it represents a reduction of more than 50% compared to the global average. A striking statistic.
Sánchez closes the loop: “Our bioreactor is essentially the key to this entire system. To paint you a picture, the first step in our wastewater treatment process is segregating it into different streams. We are then left with a liquid phase and a solid phase.
“Our vehicles are produced with the lowest energy consumption, CO₂ emissions, and water consumption per vehicle”
Harald Gottsche, President and CEO, BMW, San Luis Potosí
“This solid phase contains heavy metals, oils and organics which are then removed as sludge, while the liquid phase - which at this point is clear but not clean - undergoes further treatment by being fed into the bioreactor, with any surplus water redirected back into the main facility for reuse across several other processes so that no water is wasted.”
San Luis Potosí’s ongoing commitment is to treat 100 percent of the plant’s wastewater, maximising its reuse, as well as the site’s sustainable total production footprint.
Carbon reduction efforts across San Luis Potosí’s manufacturing processes
From fire and water - to air; reducing carbon emissions is the capstone of BMW’s sustainability strategy, and San Luis Potosí is a truly impressive example of this commitment. “In 2023, our plant was the leader in resource efficiency within the global BMW network,” says Harald Gottsche, Plant President and CEO.
“Our vehicles are produced with the lowest energy consumption, CO₂ emissions, and water consumption per vehicle. This accomplishment stems from a combination of innovative practices and targeted investments.”
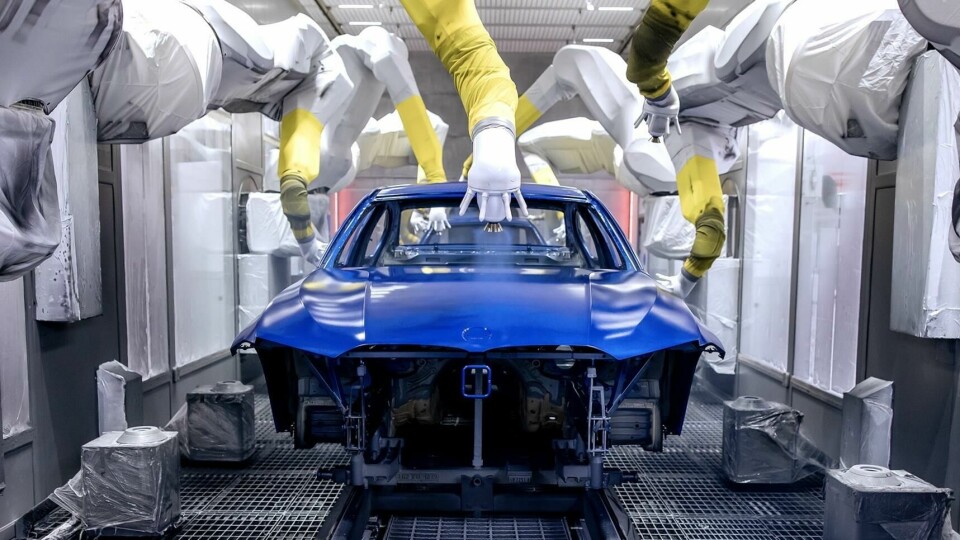
With paintshop being so energy-intensive, it makes sense for us to cycle back to this key production process, with another standout sustainability initiative being the plant’s paintshop heat recovery system. This technology captures and reuses thermal energy, which, alongside the aforementioned water-circularity solution, significantly reduces natural gas consumption across the entire site.
The system captures residual heat from oven exhaust gases and repurposes it for other processes within the facility, resulting in monthly savings of 200 m3 of natural gas.
Not resting on its laurels, San Luis Potosí is seeking further ways to ‘green’ its gases. “We are exploring further reductions in our CO₂ footprint by considering options like biomethane as a natural gas alternative,” adds Plant Environmental Manager, Álvarez.
This would represent another huge step for site sustainability. Additionally, energy consumption sensors and LED lighting is being used throughout the site to optimise overall electricity use, contributing to the facility’s energy efficiency levels.
”Water usage is meticulously monitored, ensuring that the plant adheres to its near-100-percent water recycling goal; and this level of control is critical in a region where water is a precious and limited resource”
And beyond paintshop and production, San Luis Potosí is also minimising emissions associated with material handling by employing important logistics and supply chain strategies, including the use of electric forklifts and reusable packaging. Collaborations are also underway across the value-chain with transport providers to adopt alternative gas-powered and electric trucks as part of the site’s comprehensive approach to sustainability.
The digital energy control room powers sustainability at San Luis Potosí
Weaving all of these sustainability efforts together is the site’s digital control room. Acting as the brain of the facility, the control room leverages cutting-edge technologies to monitor, manage, and minimise the plant’s total environmental impact. With real-time data insights, predictive analytics, and an unwavering focus on resource efficiency, the control room epitomises how digital intelligence can drive meaningful sustainability outcomes in automotive manufacturing.
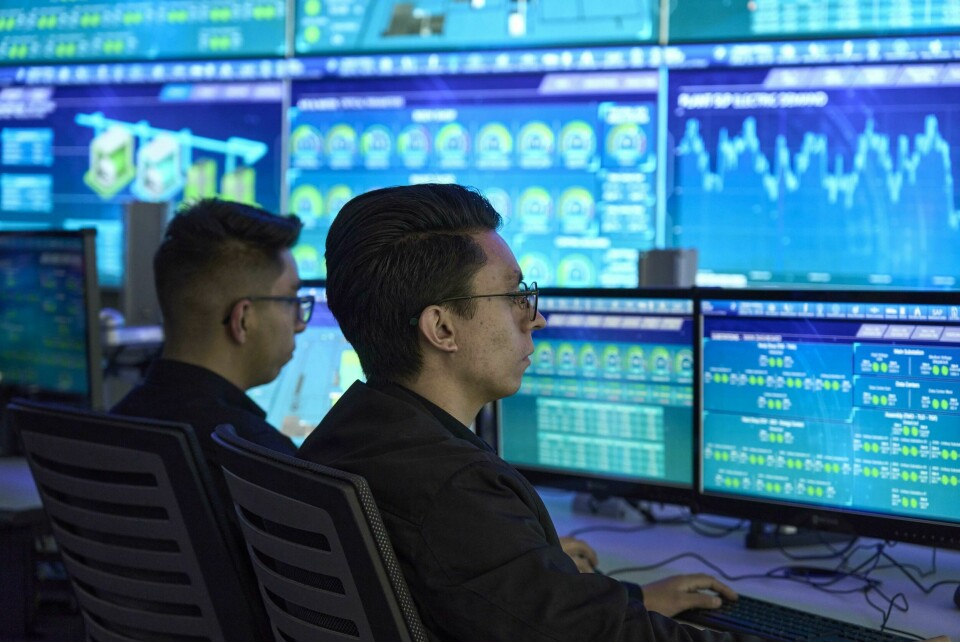
But how does it work? The plant’s digital control room is a centralised hub that aggregates vast amounts of data from across several facility processes.
This data provides instant feedback on energy consumption, water usage, and carbon emissions, giving operators the ability to monitor and optimise the plant’s environmental footprint in real-time.
For example, energy consumption is tracked continuously, enabling swift adjustments when demand increases or inefficiencies arise. Similarly, water usage is meticulously monitored, ensuring that the plant adheres to its near-100-percent water recycling goal; and this level of control is critical in a region where water is a precious and limited resource. The control room also tracks emissions at every stage of production, ensuring that the local facility aligns with BMW’s global carbon neutrality targets.
San Luis Potosí’s real-time monitoring capability transforms sustainability from a static compliance exercise into an active, dynamic component of daily production operations.
”Advanced sensors and analytics track water usage throughout the facility, ensuring efficient recycling and reuse, including almost all water employed in production processes”
Artificial Intelligence, machine learning, predictive maintenance and analytics for proactive resource management
While real-time monitoring provides immediate insights, the digital control room’s predictive capabilities take sustainability to the next level. By leveraging artificial intelligence and machine learning, the system is able to anticipate impending inefficiencies, such as equipment requiring maintenance, or processes likely to generate excessive energy consumption.
These forecasts enable teams to take preemptive action, avoiding resource waste before it ever occurs. This predictive maintenance ensures that equipment operates at peak efficiencies, reducing unnecessary energy usage and having a direct future-focused impact on site sustainability.
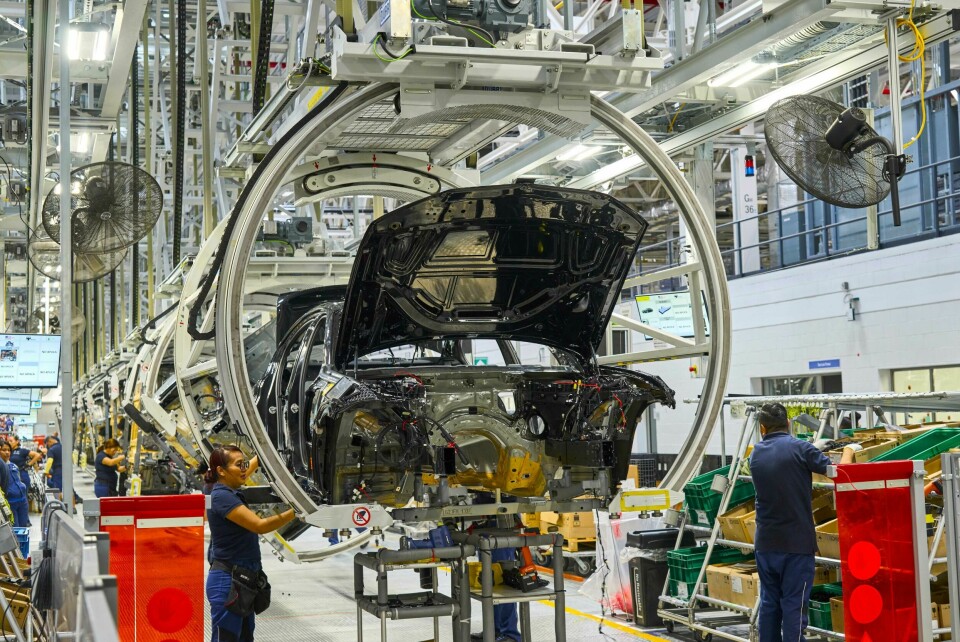
Production workflows are thereby further optimised to prevent bottlenecks that could result in wasted materials or additional emissions. The proactive approach reduces the plant’s environmental impact while ensuring that its sustainability objectives align seamlessly with operational efficiency.
Water usage data also flows into this control room, and in water-scarce San Luis Potosí, this digital nervous system plays a vital role in the plant’s water conservation strategy.
Advanced sensors and analytics track water usage throughout the facility, ensuring efficient recycling and reuse, including almost all water employed in production processes that are treated and returned for further use.
”The control room demonstrates that advanced technology, when paired with a commitment to environmental responsibility, can transform how automotive manufacturing addresses global challenges”
The plant’s innovative zero-liquid-discharge system further ensures that no untreated wastewater ever leaves the site. All of these measures are tightly managed and adjusted via insights generated by the digital control room, boosting San Luis Potosí’s holistic sustainable production ecosystem.
Driving sustainability through Data
The digital control room’s impact extends beyond environmental metrics at San Luis Potosí—it fosters a culture of sustainability across the plant. Operators are empowered with intuitive interfaces and visual dashboards that make complex data both accessible and actionable. With these tools, the site’s workforce becomes an integral part of BMW’s sustainability strategy, allowing them to make informed decisions that enhance operational efficiencies and environmental performance.
By centralising sustainability efforts and embedding them into daily operations, the digital control room enables BMW’s San Luis Potosí plant to achieve tangible - and measurable - sustainability results.
The control room demonstrates that advanced technology, when paired with a commitment to environmental responsibility, can transform how automotive manufacturing addresses global challenges, and although located out in the semi-arid - semi-desert - San Luis Potosí is leading the way on a global scale.