Stellantis transfers supply chain and logistics oversight from purchasing to production with strategic leadership shake-up
The carmaker is reorganising its supply chain, separating the purchasing department to report directly to the manufacturing chief to boost collaboration and flexibility.
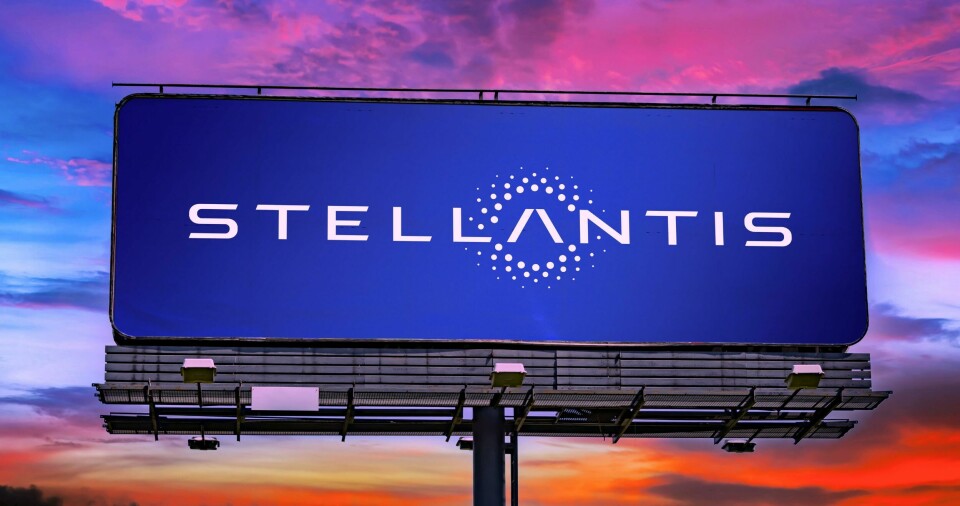
Stellantis has announced a major decision to shift its global supply chain and logistics operations away from purchasing to manufacturing, reflecting a critical structural realignment in the carmaker’s approach to production.
The move is part of a broader leadership reshuffle aimed at “driving simplification” and “enhancing organisational performance,” with the company citing the “turbulent global environment” as a key motivator. In a significant departure from previous arrangements, supply chain operations—including inbound logistics, vehicle logistics, and supply chain planning—will now report to chief manufacturing officer Arnaud Deboeuf, reinforcing the alignment between production and logistics
The change follows a growing recognition within Stellantis, and the automotive industry at large, that closer integration between manufacturing and logistics is necessary to improve flexibility and optimise the use of shared technologies. By breaking down silos and consolidating these key operational areas, Stellantis aims to “drive commercial performance” and reduce complexity across its global operations.
Maxime Picat, who had previously overseen both purchasing and supply chain functions, will now focus exclusively on purchasing. According to Stellantis, this will enable Picat and his team to “dedicate even greater focus and expertise to the performance improvements to be achieved with our supplier partners.”
“We have a big ambition for manufacturing to reduce our transformation costs globally by 40%, which includes an objective to reduce manufacturing costs by 30%, as well as to achieve carbon neutrality by 2038”
Arnaud Deboeuf, Chief Manufacturing Officer, Stellantis
Stellantis has faced a challenging market environment, with declining sales and profitability adding pressure on CEO Carlos Tavares, who will retire in 2026. The company’s restructuring is designed to address these challenges head-on by improving operational efficiency, particularly in production and logistics, areas that have become increasingly interconnected.
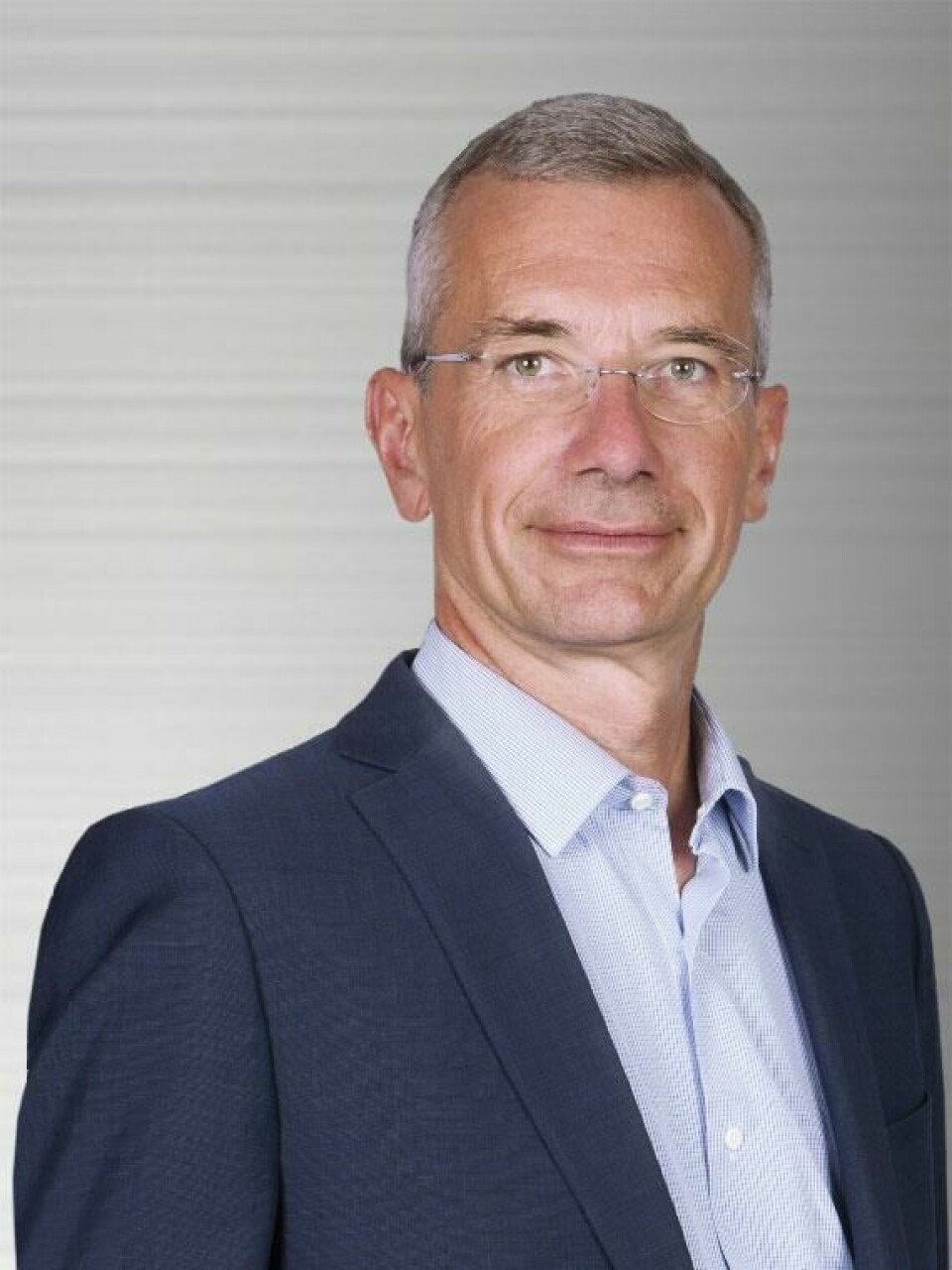
Arnaud Deboeuf has been emphasis on scaling AI and digitalisation across production and supply chain
Is Stellantis shifting further towards digitalisation and automation technologies?
The carmaker has already made strides in insourcing key logistics functions, including investing in supply chain control towers to manage disruptions and taking a majority stake in 2L Logistics, a French transport and logistics company. These moves highlight the company’s strategy to exert greater control over its logistics operations and reduce reliance on external providers.
The closer integration of supply chain with manufacturing, signals a potential shift toward deeper use of digitalisation and automation technologies across Stellantis’ production processes.
Arnaud Deboeuf, in a press roundtable with Automotive Logistics in September, outlined several innovations aimed at enhancing logistics and manufacturing synergies. For instance, he discussed a “low-cost tool to retrofit existing plant equipment for autonomous logistics” and the use of “cloud-based tools to better synchronise planning from engineering through to manufacturing.”
Deboeuf further emphasised that digitalisation and artificial intelligence will play a critical role in helping Stellantis meet its long-term cost-reduction targets. “We have a big ambition for manufacturing to reduce our transformation costs globally by 40%, which includes an objective to reduce manufacturing costs by 30%, as well as to achieve carbon neutrality by 2038,” he said.
“What we’ve got at Stellantis today is an excellent collaboration between engineering and purchasing, where we’ve got a cross-functional group with the two teams working and asking themselves the question of what the relevant supply in the future is”
Maxime Picat, Head of Purchasing Division, Stellantis
The newly-announced realignment is consistent with a broader trend among automakers to integrate supply chain and production functions, especially in response to the operational and market pressures stemming from disruptions such as semiconductor shortages and fluctuating logistics capacity.
Production-logistics coordination becoming a global direction for OEMs
As with other OEMs, including BMW, Mercedes-Benz, and Volkswagen Group, Stellantis recognises that close coordination between logistics and production can yield substantial benefits in terms of cost control and operational flexibility. The company’s shift towards a more vertically integrated production model, where it manages more logistics operations in-house, mirrors strategies employed by its competitors as they seek to mitigate supply chain volatility.
While the immediate implications of the restucturing are still unfolding, Stellantis’ focus on manufacturing as a driver of supply chain efficiency is likely to result in greater use of shared technology platforms and more seamless coordination between logistics and factory operations. The carmaker’s ongoing efforts to digitalise its manufacturing processes, as part of its Dare Forward 2030 plan, will be essential in achieving its ambitious efficiency and sustainability goals. “Digitalisation and AI are key to helping us realise significant cost savings in production,” Deboeuf noted, emphasising that these technologies would be integral to reducing the complexity of manufacturing operations across the board.
Read more Stellantis stories here:
- Dürr builds an energy-efficient paintshop for Stellantis’ Kenitra plant
- Stellantis, Ford, GM, fight EV slowdown, tariffs, IRA & China
- Stellantis turns to AI tools and fast deployment to cut production costs and launch times
- Stellantis invests $406M in three Michigan plants for EV strategy
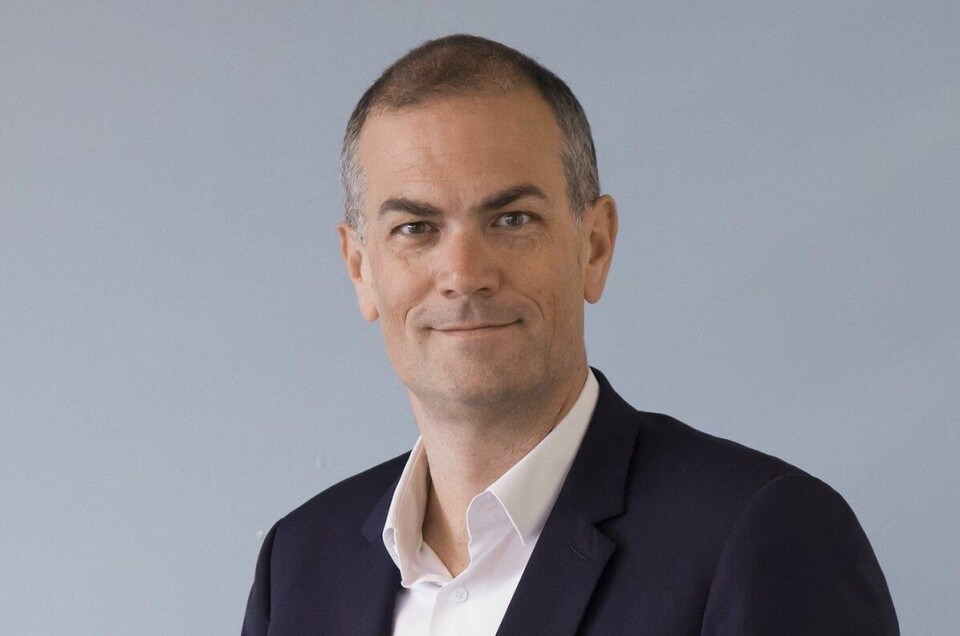
As head of the Purchasing division, Picat will concentrate on strengthening supplier relationships and driving performance improvements with Stellantis partners
At the same time, Stellantis is unlikely to abandon cross-functional collaboration with other departments, such as procurement. Picat has previously underscored the importance of teamwork across divisions.
“What we’ve got at Stellantis today is an excellent collaboration between engineering and purchasing, where we’ve got a cross-functional group with the two teams working and asking themselves the question of what the relevant supply in the future is, and they consider supplier-based and technical solutions to ensure competition and resilience,” he said in an interview with Automotive Logistics.
Flexibility and responsiveness seen as keys to automotive successes
This kind of cross-functional integration is essential to ensuring the flexibility and responsiveness required to navigate ongoing supply chain challenges, particularly in the transition to electric vehicles. Furthermore, the inclusion of procurement and engineering teams in early-stage collaboration has become a standard practice within Stellantis, aimed at improving logistics outcomes.
“It’s important that some suppliers can support several platforms, as then there is more flexibility to react for changes”
Mercedes Figueroa, Vice-President, North America transportation operations, Stellantis
Mercedes Figueroa, vice-president of North America transportation operations at Stellantis, highlighted this approach at the Automotive Logistics & Supply Chain Global conference in Dearborn, Michigan. “Procurement is also essential from the beginning, and on solutions like how the supplier base is going to be located,” she said. “It’s important that some suppliers can support several platforms, as then there is more flexibility to react for changes.”
Ultimately, Stellantis’ repositioning of its supply chain under manufacturing represents a calculated response to the increasingly unpredictable landscape of automotive production.
By following the path taken by other global manufacturers, such as JLR, which combined production, purchasing, and supply chain into a single organisation, Stellantis is aiming to streamline decision-making and boost operational performance. With the automotive sector undergoing such rapid transformations, particularly in relation to electric vehicle production, the realignment positions Stellantis to better manage the complexities of modern manufacturing while pursuing its ambitious goals of cost reduction and carbon neutrality by 2038.