How Opel Eisenach’s New Grandland EV Production Blends Lean Principles, Flexibility, and Automation for Competitive Advantage in a Changing Industry
The Opel plant in Eisenach exclusively produces the new Grandland – the brand’s flagship. Plant manager Jörg Escher explains in an interview what impact the switch to the new model will have on the site.
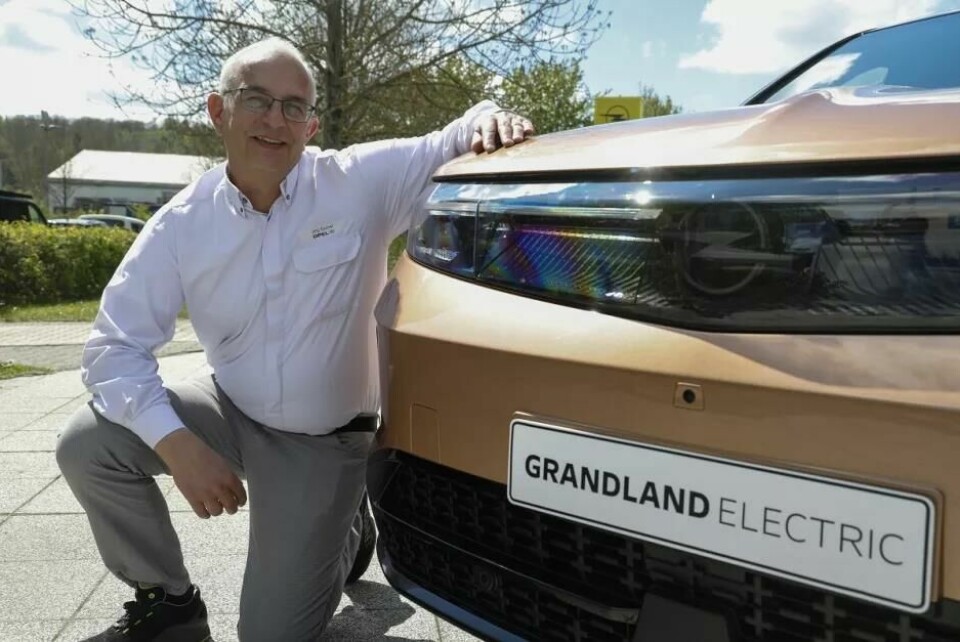
Mr. Escher, the plant in Eisenach is in the final stages of the conversion to the new Opel Grandland. What is the status quo?
We are right on schedule. We will be producing the new Grandland in all variants at our plant in the future – with fully electric drive, as a hybrid with 48-volt technology
and as a plug-in hybrid - all with the multi-energy platform on one production line. The biggest challenge is to get the entire system, including the quality system, running stably.
The transformations in the industry are enormous, especially here at the site. How have employees reacted to these changes? Do you sense any particular nervousness?
We are a pure vehicle plant. That is why our basic task remains unchanged: we built cars before the transformation and we continue to do so. That alone is a positive signal. Nevertheless, there are challenges. Many of our employees have “petrol in their blood”. The change to e-mobility is not just a technical change for these people, but also a mental one. The political discussion surrounding electromobility also plays a role. The topic must establish itself positively in people’s minds and they must experience it.
One example of how we supported this was a family celebration that we organised a few weeks ago. We offered test drives in the electric Grandland so that colleagues could experience the product first-hand. Many employees had never driven an electric car before.
The event was a valuable opportunity to get a feel for the technology. Such offers are essential to create acceptance. I think this is also a social issue - the transition to new technologies takes time and experience.
”When the plant was built in 1992, it was already one of the most modern plants in Europe and a real training ground for talent”
Jörg Escher, Eisenach Plant Manager, Opel
Nevertheless, the question again: How are the employees prepared for this?
We are building a real top-of-the-line model here in Eisenach for the first time. We are very proud of that. We have consciously encouraged this attitude by communicating intensively internally - not only about the production processes, but also about the highlights of the vehicle itself.
We create a weekly briefing card that goes to the teams. In it, we provide information about production changes or the key features of the new model, among other things.
This is important because many employees - especially in the bodyshop, the paint shop or logistics - rarely see the finished car. Another example: We presented the vehicle in the audit area and invited the entire workforce to take a look at it. Experts were on site to answer questions and explain the functions. This was very well received.
Eisenach has already undergone many restructurings. Of the approximately 1,900 employees in 2003, only 1,100 remain in 2024. How would you describe the development of the plant since its founding until today?
When the plant was built in 1992, it was already one of the most modern plants in Europe and a real training ground for talent. It was a showcase plant, especially for the implementation of the highest lean efficiency principles. We had international teams here who implemented a production system that attracted worldwide attention. Today, Eisenach is a very efficient plant that implements the principles of lean production and is known for the high quality of its products.
We are a relatively small plant and a highly productive team. We are constantly working on our competitiveness, which presents particular challenges in a country where manufacturing and energy costs are high.
“During a transition period, both the old and the new Grandland could be produced here. The substructure area, on the other hand, required a completely new production line. However, these expansions required additional space, as did battery production”
Jörg Escher, Opel
That sounds like a lot of pressure. Have there been any particular challenges in the recent past that the plant has had to overcome?
One of the biggest challenges in recent years was the Corona crisis, during which production at the plant was completely halted for three months. This was a purely economic decision. The Grandland was also manufactured in Sochaux, France, at the time. Since it made no sense to run two plants with low capacity due to the pandemic, all production was relocated to Sochaux for a short time.
This led to uncertainty among employees. Unfortunately, the situation was fueled by false information in the public debate. This increased the pressure on the workforce.
You mentioned Sochaux: The model is currently produced exclusively in Eisenach, right?
Exactly, the new Grandland is produced exclusively in Eisenach. The fact that the old Grandland was also initially manufactured in Sochaux was a pragmatic decision to save time when switching to the new model. In Eisenach, extensive modifications had to be made to the production facilities. After the model year change, the entire production of the old Grandland was then brought to Eisenach.
The new Opel Grandland is based on the STLA Medium group platform, which is also used for vehicles from other group brands. But the “Opel Grandland” product is built exclusively here in Eisenach.
”We work closely with other Stellantis plants that use similar platforms. This exchange helps us to benefit from each other’s experiences and create synergies within the Group”
Jörg Escher, Opel
You said that a small factory like yours is under particular pressure, especially in difficult economic times. It was emphasised several times on the Factory Tour that the motto here is: “Help yourself instead of waiting for support.” Can you give concrete examples that illustrate this spirit?
In order to make use of our positional advantages, we formed working groups at the start of the new project, for example, which were to do as much planning in advance as possible. One of the biggest challenges was to integrate a completely new platform architecture into the plant. In the shell construction, the entire main line continues to run with the original equipment from the previous Grandland, which was converted accordingly.
During a transition period, both the old and the new Grandland could be produced here. The substructure area, on the other hand, required a completely new production line. However, these expansions required additional space, as did battery production, which also had to be integrated into the factory halls without creating additional space. We have therefore developed solutions to make optimal use of existing capacities and space. For example, the production of struts - a complex system - was relocated by our own team during the factory holidays.
We have also made some progress in the area of logistics: We are using high-bay warehouses that were no longer needed at our sister plant in Kaiserslautern. Our logistics team dismantled the shelves there, transported them and reassembled them here. Such advanced work shows that we can work flexibly and independently - an advantage that large plants often do not have in this form.
Would there even be room for another model?
This of course depends on demand and other factors. If there is additional need, we could create additional capacity by introducing a third layer. Another model would therefore be conceivable, provided it is based on the same architecture. A different platform, on the other hand, would require very high costs and modifications, which would seriously affect profitability.
How does the exchange with other plants in the Stellantis Group work?
We work closely with other Stellantis plants that use similar platforms. This exchange helps us to benefit from each other’s experiences and create synergies within the Group.
”We check where quality deficiencies occur in the production process that require rework. This data is entered into our system and is currently analysed manually”
Jörg Escher, Opel
Let’s get to the main topic: Can a small plant like yours, where investments always have to be carefully considered, implement AI in many use cases? Have you already implemented AI and what importance does the topic have here at the location?
AI is certainly not the most important topic for daily operations, but it already plays a significant role, especially in quality assurance. For example, we already use it in bodyshop, where we analyse welding patterns and bolt placements. We also have specialised applications that check whether bolts or other elements are correctly placed. A larger application is in the paint shop.
There, an AI analyses the vehicle surfaces and detects whether there are dust particles, small dents or other deviations. This application is called “Eagle Eye”. It must first be trained to distinguish what is acceptable and what is not. Once this is complete, it gives the employee specific instructions, such as: “Look at the top of the fender, there is a dust particle.” We also have several AI-based applications in final assembly. For example, there is the so-called outside conformity test.
Here, the AI checks features of the vehicle, such as whether the color is correct, the type plates are present or whether something is missing. It becomes particularly complex in the substructure area, where numerous screws have to be attached - for example for heat shields or NVH components. The challenge here is to avoid errors that could later lead to costly rework. We have integrated stations that use AI to check whether all screws are present and correctly seated. This helps us to reduce errors and increase our efficiency.
Read More Stellantis Stories
- How Stellantis is managing multi-brand complexity
- Stellantis marks 60 years of vehicle production at Ellesmere Port
- Stellantis turns to AI tools and fast deployment to cut production costs and launch times
- Chinese vehicle makers look to international markets for growth
How much does AI help, especially when it comes to automation?
We have started to collect data from the end-of-line area.
We check where quality deficiencies occur in the production process that require rework. This data is entered into our system and is currently analysed manually. Our idea is to automate these processes with AI. The AI could then prioritise which control points in the line should pay more attention to certain quality features.
The results could be passed on directly to employees via a tablet, with instructions such as: “For this car, please check exactly here, here and here.” We are already in talks with an exciting start-up about this.
Another special feature that was highlighted on the tour is the closeness between the employees who work on the assembly line and you as the plant manager. What does that look like on a daily basis?
That is actually one of our greatest strengths. We have a very flat hierarchy. This is also evident in our office structure: I am not sitting in a separate, closed office, but in the middle of the action. An acquaintance who often works with other car manufacturers was very surprised by this, as in other plants the plant manager is often isolated. But our philosophy from the beginning was that the plant manager is in the middle of things to encourage communication.
Our flat hierarchy is also reflected in our organisation. For example, we do not have a production manager. The department managers report directly to me. This promotes short decision-making processes and close cooperation at all levels. This structure is a great advantage, especially for a plant of our size.
”Our bodyshop […] is completely automated. Our paint shop and our new battery production […] are also technically up to date with a high level of automation”
Jörg Escher, Opel
What does a typical working day look like for you?
My workday starts at 7:30 am when I look at the results of the previous day.
I then discuss the most important key figures in a meeting with my boss at 8 a.m. My team, i.e. the department heads, meet at 9:30 a.m. We exchange ideas on topics such as safety, health and production figures. I use the opportunity to pass on information from my morning meeting. A standard appointment is the audit at 11:45 a.m., at which the quality results are discussed in detail.
Around twelve vehicles are checked in detail each day. The quality engineers or team spokespersons present the results and we clarify whether measures are necessary - such as feedback to suppliers. In the afternoon, there are problem-solving sessions directly on the line or regular meetings. Our meetings are structured in a cascade: details are discussed at department level, which are then escalated to my level if necessary.
During the assembly, it was mentioned that the level of automation in Eisenach is comparatively low. Would you say that this can even be an advantage for the location? Are you consciously going against the industry trend here?
I would like to put that into perspective. Our bodyshop, for example, is completely automated. Our paint shop and our new battery production, for example, are also technically up to date with a high level of automation.
There are some manual tasks such as filling, but here too we are already testing automation solutions. For example, we use robots that can take on such work. The level of automation in the Eisenach plant is not significantly different from other plants.
”The automotive industry is undergoing profound change, and we are experiencing increasing competition and cost pressure”
Jörg Escher, Opel
And what does it look like in assembly?
At high utilisation, automation can make sense. At the same time, flexibility is lost, and new models can have high start-up losses. Not every automation is automatically the best solution. One example is the fully automatic installation of headlights. In plants that use this, high scrap rates often arise when new models are introduced because the systems have to be finely adjusted. Every line downtime, even for a few seconds, causes enormous costs because hundreds of employees are directly affected. For a plant of our size, this is often not worthwhile.
Are there still areas where you would like to automate more?
We see great potential in logistics. So far, we have only used a few driverless transport systems or similar technologies here. There are many possible applications, especially for the small driverless transport systems, the LGVs. As soon as we have completed the current transformation, we will tackle this. Last year, we completely restructured our warehouse areas, creating additional space outside the factory to store materials. The phase-out of the old model is now complete and we are starting to remove old equipment and structures that are no longer needed.
As soon as the warehouse areas have been finally optimised, we can integrate automation solutions. In summary: Our level of automation depends on the respective requirements. There are no major differences to other plants. We use automation where it is economical and makes sense. Flexibility and efficiency are always the focus.
”In general, we in Germany have structural cost disadvantages compared to other countries in Europe and increasingly also compared to China”
Jörg Escher, Opel
Finally: Why does the Eisenach plant have a long-term future?
The Eisenach site has a lot of potential. Not only because it has grown historically, but because we are actively working to continue to position ourselves for the future. The automotive industry is undergoing profound change, and we are experiencing increasing competition and cost pressure. Stellantis has taken steps in recent years that other manufacturers may still have to take.
There are a few key factors that are crucial for the future of a plant like Eisenach. First and foremost, quality. We have to ensure that our cars are of the highest quality. Without quality, there is no basis for new models or investments. Eisenach has consistently delivered very good results in this regard and is one of the best plants in the group. That is our door opener.
”Good ideas and the continuous improvement process that we have integrated very strongly into the work processes help us to…”
Jörg Escher, Opel
What other factors are crucial?
Cost efficiency is also a focus. Flexibility is a key factor here. Good cooperation with the social partner also plays a central role here. This cooperation is often easier in a small plant than at large locations. I have direct contact with our works council chairman every day, which significantly speeds up decision-making and the implementation of measures. Here in Eisenach, this works very well.
In general, we in Germany have structural cost disadvantages compared to other countries in Europe and increasingly also compared to China. This competitive situation forces us to look every day for ways to work more efficiently. Good ideas and the continuous improvement process that we have integrated very strongly into the work processes help us to do this - from the teams on the line to the team spokespersons.
However, the last few years have been marked by many challenges. Due to Corona or the semiconductor crisis, the necessary consistency in production was lacking. This instability was a major burden for us. I am now all the more optimistic about the future because we have a very good product that is receiving positive feedback in the press and on the market. I have also received consistently positive feedback from my personal circle of acquaintances. Our new vehicle offers good value for money and I am optimistic that we will now regain the necessary stability to remain successful in the long term.