Ignacio Martin Gonzalez, Gestamp: “Steel is still a high-performance product”
For e-mobility, suppliers like Gestamp must be willing not only to produce components, but also to contribute their expertise in terms of design. Ignacio Martin explains how the supplier is preparing for an uncertain future.
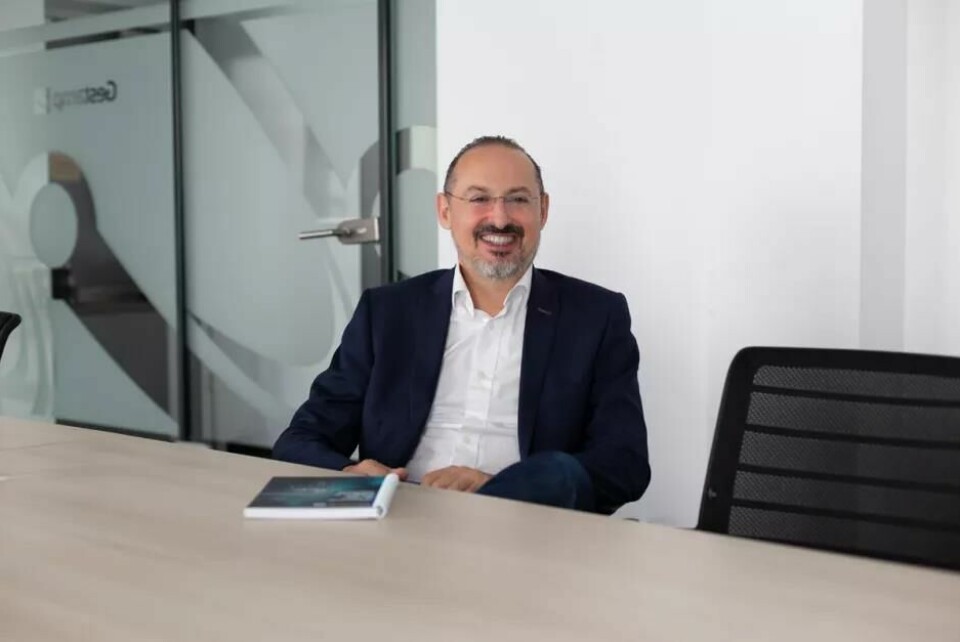
Mr. Martin, with sales of almost 12.3 billion euros, Gestamp was able to report a record in 2023, an increase of 14.4 percent over the previous year. Profit was eight percent. What recipe helped achieve this and what does the path to the future look like?
Gestamp is now a strategic partner supplier. This means that we provide our customers with solutions with a very high added value. They allow them to be at the forefront of the automotive sector. When you analyse the complexity of the automotive supplier market, this is a very decisive factor. The record figures are partly the result of our competitive position in the customer environment and partly the result of product differentiation with technical solutions that we offer worldwide.
We believe that we are good at constantly expanding this competitiveness. There is a simple formula for this: technological development coupled with innovation and competitive costs.
Many suppliers have emerged from the crises of recent years significantly weaker than most car manufacturers. How do you assess this imbalance?
Gestamp has a very strong position in the market, despite the many challenges it has faced recently. As part of this change, we have taken on more responsibility. Suppliers are now responsible for 75 percent of vehicle value creation. For many, and for us in particular, the great opportunity lies in offering cutting-edge, sophisticated and cost-effective key solutions. We do this in three key areas: body in white, chassis and batteries.
These are solutions based on reducing weight while improving sustainability. Our portfolio now includes numerous very large products that help our customers reduce assembly times. Such solutions are in great demand in the automotive industry today because they help OEMs to optimise their production.
For us as suppliers, it is important to be part of the fundamentally changing architectures of electric vehicles and to develop the key technologies required for this. In our portfolio, we are talking about structural components that we represent in a circular economy and that take CO2 avoidance into account right from the start.
Gestamp had to evolve from a company that only processed steel to become an expert in the field of aluminium and hybrid materials. How strong is the trend towards lightweight materials, especially in the area of chassis components?
The main drivers for the change from a pure steel producer to a hybrid and aluminium provider are the technological changes resulting from the batteries in vehicles. The batteries add a significant amount of weight to the vehicles, which inevitably has an impact on crash safety, driving dynamics and ultimately also on CO2 emissions. Lightweight construction solutions are therefore indispensable.
Two aspects stand out here: firstly, the integration of the battery into the body and secondly, the integration of the motors into the chassis. We offer a wide range of solutions for both challenges, in which technology and new materials are crucial.
In addition to these trends, there is also a trend among original equipment manufacturers towards hybrid components. What proportion of these components and those made of steel and aluminium are used at Gestamp?
The body area accounts for over 70 percent of our product portfolio. Hybrid solutions account for a high proportion of chassis and battery components. The chassis components include the front and rear chassis as well as various types of control arms such as wishbones and camber arms. Hybrid systems are much more common in higher segments. And there are also geographical differences: all-aluminium chassis, for example, are often developed by new electric players from Asia. Nevertheless, we believe that in most cases we can develop the same performance with even lower CO2 emissions using our high-strength steel alternatives and our in-house technologies.
So one can make a distinction between materials in geographical terms?
Correct. At the same time, we are seeing a general “back to steel” trend. In our opinion, steel is still a high-performance product.
Which components are most commonly produced at Gestamp?
Steel is our biggest source of revenue. Due to the new lightweight platform architectures, the trend is towards high-strength, yet lighter assemblies. In hot forming, for which we operate more than 100 systems, the need for ever larger steel products is increasing. We call them “extreme-size parts”, such as the door ring or an entire floor assembly. Development is progressing unabated in these extremely strong hot-formed parts. In the battery sector, there are signs of an increased use of multi-material and aluminium. Development will continue until battery boxes are ultimately integrated into the body as so-called “cell-to-body”. This makes steel much more interesting again.
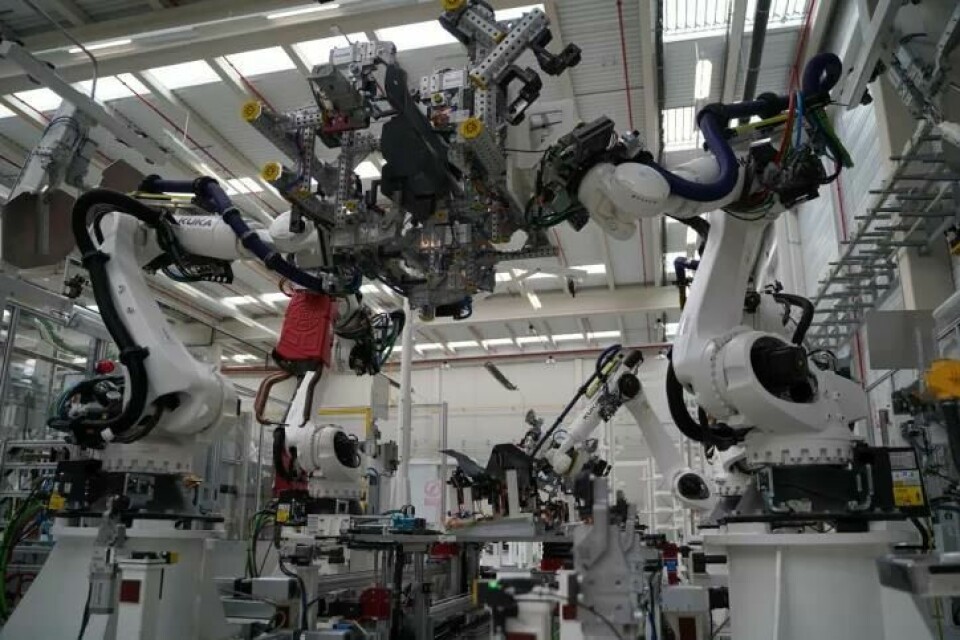
What challenges do hybrid components pose, especially with regard to connection technology?
Regardless of whether we are looking at the body or the chassis area, hybrid solutions make it possible to put the right material in the right place. In addition, there are high demands on the connections themselves, not forgetting the issues of corrosion and tolerances.
From a technical point of view, we have developed all connection solutions ourselves and often combined them with our own patented manufacturing processes, with adhesive, welding and laser connections. These hybrid solutions are of course not always the most cost-effective.
However, if the requirements for the product are very high, as is the case with battery boxes, the corresponding technologies are actually unavoidable. Today they are mostly used in the battery area, where the balance between safety, performance, weight, sustainability and costs must be found.
If battery boxes come as cell-to-body in the future, they will be simpler, but then the corresponding connection technologies will also have to be further developed.
At Gestamp, manufacturing-oriented design is a key aspect, and with it the question of functionality while at the same time being economical to produce – keyword: Design for Manufacturing. What is your strategy in this regard?
Manufacturing-oriented design has been part of our DNA for years. Strategically, we go a step further and call it “Design to Cost”, which already includes Design for Manufacturing. To do this, we have combined all research in a single organisation.
This spans a network of 13 centres worldwide and a team of 1,500 engineers who develop products, technologies and innovations in parallel. One of the most important differentiating features is our so-called co-development programs, which enable us to develop technologies and solutions years in advance and to analyse, calculate and validate them together with customers even years before the SOP.
These programs reduce the time to market. The basis for co-developments with customers are our digital vehicles developed at Gestamp, the so-called G-Labs. Put simply, technologies are pre-validated there. This allows us to offer development, testing, validation and the corresponding manufacturing conditions for the plants from a single source. However, we not only master the entire value chain, because we are also toolmakers and plant manufacturers. Using hot forming as an example, we develop and build our tools and presses ourselves.
So, from the beginning of the project, product designers and production engineers are on board together?
That’s right. Product development, validation, cost calculation and production are all carried out from a single source. An important aspect here is that the functional integration is also secured with a holistic, complete simulation. The entire chain is simulated, starting with material development, material data cards, production forming simulations, production simulations, and up to the full crash simulation of the vehicle.
This complete representation, in which simulation data is transferred from the product to production - i.e. to the systems - allows us to reduce the time to market and provide greater security for robust system planning. At the same time, this requires a strong digitisation of all processes and relationships.
You manufacture safety-relevant products for vehicles that have enormous quality requirements. How do you ensure this, especially in production? One key term here is ’unitary traceability’.
We have our own Industry 4.0 teams and our own plant development department, which works with us right from the start of product development. Quality requirements: we can control the system and data and trace the products back to delivery. We also keep an eye on the entire CO2 chain.
The new battery boxes mentioned above also represent a whole new level of production because they require complex processes and product requirements that have not existed before, for example with regard to tightness and extremely tight tolerances. As a result, we cannot avoid reliable data traceability.
A good keyword. Machines and products generate valuable data that is particularly important for research and development as well as for production itself. How do you process, store and use this data?
We have set up two technology groups specifically for this topic. One is the aforementioned Industry 4.0 and the other is the so-called Flex Manufacturing Factory Team. Both teams work on the development of new systems, the standardisation of data and the machine evaluation of this data. The large amounts of data that our systems generate range from process control to product assurance, so that we can proactively increase process reliability.
How do you filter “good” and relevant data from less important data?
Data is analysed by our teams in the Industry 4.0 group. Product data and data obtained in product development are evaluated centrally and form the basis for new developments in our digital vehicles. This means that all the data we receive on the material side enables us to validate an optimal new innovation in the digital vehicles.
For your productsYou buy raw materials from large steel and aluminium manufacturers. What are your biggest sources and what quantities are involved?
Steel and aluminium are our two most important raw materials. In Scope 3, they are of course also the biggest CO2 emitters. We rely on circular solutions, especially in the steel sector, our main application. This means that we try to return scrap to steel production. To this end, we work with practically all steel manufacturers and want to further deepen partnerships, particularly with regard to raw steel and fossil-free steel.
There are actually no limits here. The trend towards aluminium will increase in the meantime. We mainly use aluminium for the outer skin of vehicles in higher segments and for battery boxes. We mainly purchase the material as a flat product. One exception is that we operate extrusions ourselves in a joint venture. Secondary material in aluminium processing is constantly increasing. However, this is still very low in relation to steel.
When it comes to sustainability and recycling, Gestamp has numerous partnerships with other companies, such as SSAB. What is behind such collaborations?
Our long-term strategy includes neutrality through the decarbonisation of materials. To achieve this, we need to enter into various partnerships in order to be able to validate and bring the relevant materials to market more quickly. The cooperation with SSAB that you mentioned is about fossil-free steels, mainly in the body and chassis areas. There are other cooperations with French and Indian companies, for example, and more are coming. It can be seen that in the future the demand for green steel will be higher than the need.
A good 90 million vehicles were produced worldwide in 2023. What does this mean for Gestamp’s product portfolio?
In the long term, the electromobility market will grow. However, 2023 was marked by a great deal of uncertainty. In the next few years, however, we see further growth in the field of electromobility and thus in our body-in-white area with extreme size parts, i.e. with large gigastamping products, as well as in the chassis area with motor integration solutions such as hydroforming of high-strength tubes.
For the battery area, we see various stamping technologies and lightweight construction on the rise. 20 percent of our automotive component sales are already based on components for electromobility.
In 2023, parts for electric vehicles will account for the 20 percent of your auto components sales that you mentioned, which corresponds to growth of six percent. What prospects do you see for this area?
We expect this to account for 50 percent of our sales by 2027. It should be noted that the new product families for electric vehicles bring with them greater added value due to greater complexity. Therefore, this market is to be viewed very positively, even if it is growing more slowly at the moment.
What are the Gigastamping products you mentioned and how is it different from Gigacasting?
For many years we have been manufacturing products using the Gigastamping process, such as an entire side wall with A-pillar, B-pillar, C-pillar, partially hardened, or a one-piece floor assembly in hot forming, completely from one part.
In contrast to Gigacasting body parts, Gigastamping still requires the integration of some additional welded components. But here too, the result is a single product, an extreme-size product. This allows the customer to reduce production times in their line. Gigacasting is very common in China and in Asia in general. In Europe, however, Gigacasting is not yet as advanced because the corresponding integration must sometimes be carried out by the OEM. Due to the sheer size of the products, delivery by an external supplier is not always possible.
We are looking into the topic of Gigacasting, but think that it will not progress as much in Europe as in China. In Asia, on the other hand, there are already entire ecosystems that extend into secondary material processing.
What innovation do you see in the area of electric vehicle components with regard to noise-vibration-harshness (NVH)?
Even if electric vehicles seem to be simpler in terms of assembly technology than vehicles with combustion engines, they still have different and very high requirements when it comes to NVH. This is due to the fundamentally changed structure caused by the battery, the high mass, the centre of gravity and the integration of the engines into the chassis.
The engine frequencies are absolutely not comparable and we are dealing with a completely different NVH curve. For us, however, this is a very big opportunity, a new challenge to implement new products. And here the credo mentioned at the beginning applies: We want to guarantee complete integration, including simulation technology, from product development to production. For example in the form of
Front and rear chassis with engine integration that correctly covers all requirements from crash to NVH.
With regard to the four important issues of safety, performance, weight and cost that are important for OEMs: which of these requirements do you see as the greatest challenge?
In our opinion, the formula must be four plus one: safety, performance, weight, costs plus sustainability - in other words, CO2 reduction. We must analyse these different factors for specific vehicle types. In our opinion, the weighting must be regional and with a view to the vehicle segments. It is therefore important to find technologies that cover all requirements simultaneously.
One of these is hot forming in gigastamping, for example for the door ring, thanks to which we increase safety for side crashes and improve performance for small overlaps. We can achieve all of this with low weight, at a low price and with reduced CO2 emissions. This means we can offer a solution for most regions and applications in electric vehicles.
This article was originally written by Götz Fuchslocher, for AMS’ sister publication, Automobil Produktion. You can view the original here.