SSAB – Sitting comfortably with Faurecia
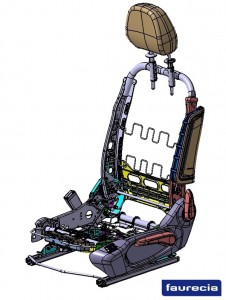
The design of automotive seating has evolved radically over the past four decades. Anna McQueen reports on the developments in materials, sustainability and weight reduction
The first focus on seat design from a safety perspective really came about in the 1970s. At that time, millions of people were dying every year in road traffic accidents all over the world and the automotive industry shifted its focus on how to best protect the vehicle’s occupants.
During the 1980s, while safety was still a key concern, the focus shifted somewhat to comfort and features, with the addition of many new options such as powered and heated seats. Now in the 21st century, as environmental concerns have become so important, the focus in terms of automotive seating manufacture has shifted to weight reduction, materials, and sustainability.
“Weight is a key issue in modern automotive design because the less weight in the vehicle, the fewer emissions, and there are ever-more stringent conditions being placed on car manufacturers in terms of how environmentally friendly their vehicles are,” explains Philippe Aumont, chief technologies officer at Faurecia’s R&D centre in Étampes, just south of Paris. He adds: “What has changed now is that in order to be able to maintain or improve safety whilst reducing weight, we have had to deep-dive into basic technology and science which weren’t previously taken into consideration when designing automotive seating”.
Considering materials
Previously, the design of a car seat was approached from a more empirical standpoint. “Nobody considered the composition of the materials such as the steel that was used. Nobody gave a second thought to the different phases of the metal – steel was steel, and if it could be bent or welded, OK, then that was fine,” notes Aumont.
“But now, with our focus on optimised weight and cost, we have had to delve into science, and with the help of suppliers, research partners and our own R&D experts, we’re on a totally different level,” says Aumont. “The business is more scientific than it ever has been and that’s the biggest change the industry has ever seen, one which is inspiring a great deal of excitement and enthusiasm”.
When creating a seat, the first thing to consider is to position the structure where the architecture of the car needs it to be. “Our customer will give us what is known as the ‘H-Point’ for the seat, which refers to where the occupant’s hips should sit, and from this reference point, we can position the various mechanisms,” explains Aumont. These are then linked together with a frame that holds the seat correctly and the occupant in a safe and comfortable position.
“Our second consideration is keeping the occupant in the right state during an emergency scenario in which the seat will need to absorb enough energy to protect the occupant from injury,” says Carey Dilliott, director Generic Frames & Advanced Frames Engineering at Faurecia R&D. The first issue to be considered is in the case of frontal impact. “Here, the seat stops the occupant from continuing forward and must prevent ‘submarining’, whereby the occupant slides forward underneath their seatbelt. This is ensured by the front part of the seat cushion,” Dilliott explains.
Most common at low speeds, rear impacts are the most difficult emergency scenario the seat design has to cope with. The seat needs to behave in an elastic way to avoid whiplash. At medium speeds, the backrest offers the main protection and a limited dynamic deflection helps to protect the people in the back. At high speed, it’s about protecting the occupant: “We spend a lot of time researching the deformation properties of the steels we use because the controlled deformation of the material is what really helps protect the occupants in these cases,” says Dilliott. For protection against lateral or side impact, the solutions included in each car depend on the manufacturer. Some choose to use the car structure, and others the seat.
“Flexible, advanced, and high-tech development in close cooperation with materials suppliers is the key to moving forward for an increasingly technical and scientific industry such as ours”
- Philippe Aumont, Faurecia
Safety regulations also play a major role in adding to the weight of the seat, but crash safety specifications would appear to be stabilising now. “Between 1980 and 2010, cars were required to be safer every year,” says Dilliott. “This pushed the weight of seat frames from an average of around 10kgs to 17kgs, in parallel with the weight of the car. But it’s hard to see how much more improvement we could have made to safety in cars using this method before they’re no longer classified as cars and are considered as tanks instead!” he adds. A complete seat module weighs between 60-70kgs, with the total weight of a modern midsize car being around 1,200kg.
A modern car seat is a complex system due to the number of different technologies involved in its construction. “We are dealing with companies such as SSAB in terms of steel structures, of course, but we are also working with forming and joining processes, plastics technologies, motors, foams, and any soft materials, all of which require different engineering expertise,” says Aumont. Faurecia also has to integrate electronics into its seats, and opened a new electronics lab at the Étampes site two years ago to meet the demand. “Our technological expertise is our competitive edge and we want to hold on to that position in terms of the technologies used in seating construction,” Aumont stresses.
Looking at alternatives
The materials used in automotive seating vary but they are mainly steel, with around 20 different micro-alloyed and high-strength steels used, although mild steels have now been replaced with composites. Faurecia is constantly looking at alternatives in order to always have the best weight-to-cost combination.
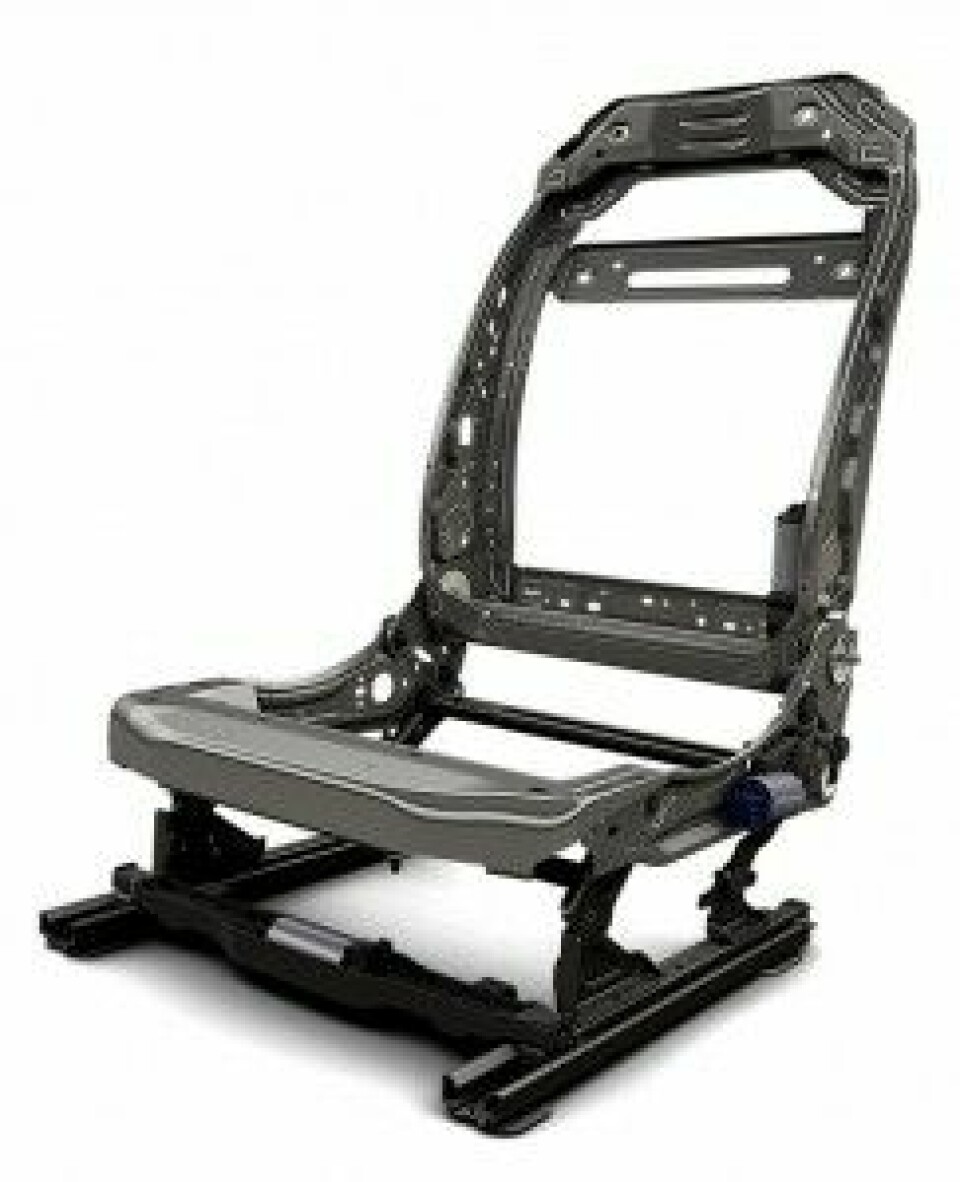
Aluminium is another material that has been considered for use in the manufacture of automotive seating due to its light weight, although to provide strength comparable to that offered by steel, it needs to be fairly thick. But the major issue for aluminium is joining technology. “Welding steel to steel is relatively easy but successful hybrid joining is expensive, which makes us tend to avoid having to join different materials,” says Joel Galmiche, stamping engineer manager at Faurecia R&D.
Another key issue for Faurecia to consider when choosing materials is global provisioning; the company needs to be sure that it can produce identical parts across the globe to serve its wide-reaching customer networks. “We need to be able to use the same material all over the world,” explains Galmiche. “If, say, Ford is making the same car in 15 different locations around the world, then we have to supply the same product to them wherever they are, without the need for any additional validation. That can be challenging in terms of sourcing certain materials, particularly in the US,” he explains.
Environmental impact
Sustainability is another important consideration for Faurecia. “That ‘new-car smell’ that you can detect when you entered in a new vehicle came from the chemicals used in the car’s production, such as plastic covers in a seat,” says Aumont. “In the past, those odours and thus those chemical residues were ignored, but now we are looking at new kinds of foams and plastics with fewer volatile emissions, as part of a more sustainable approach to our business, with the aim of better protecting our employees and those in our environment, as well as our customers and end users,” he adds.
The amount of freedom Faurecia has in terms of seat design varies from constructor to constructor. “In some cases, we are completely free with the design, and in others, we build to print using drawings supplied by the customer,” says Aumont. “But one thing is for sure – we are always the manufacturing arm of the car manufacturer, and in many cases, we’re the engineering arm, too. We have to be flexible and adapt our business model to that of the car manufacturers,” he adds.
To remain at the forefront of technological progress, Faurecia has a policy of working in close cooperation with materials manufacturers, and the collaboration goes both ways. “Sometimes, a steel manufacturer like SSAB might come to us with a concept for a new material, or we might have a project in mind that we’d like to develop using their steel,” Aumont explains.
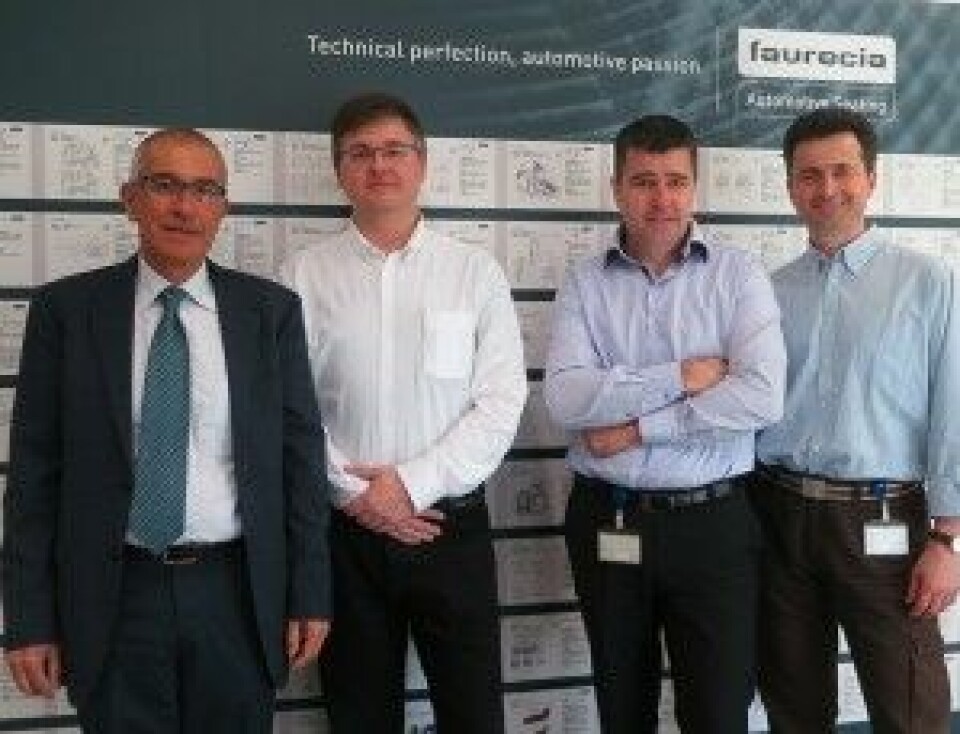
Faurecia is also very keen to participate in consortium projects, working on collaborative programmes that bring together industry players with researchers and local authorities. “Our primary concern is moving the technology to the next level, and it’s often through programmes such as these that advances are made. It gives us the opportunity to experiment with materials that aren’t yet at the mass production stage but that we might be using in the future,” explains Tudor Balan, who works part-time as a senior expert at Faurecia, and part-time as associate professor at the ENSAM French higher education establishment in the eastern city of Metz. “We are currently involved in two European projects looking at prototype steels, as ever seeking more strength for less thickness,” he adds.
“Increased strength has taken priority over formability for a long time, and we are now very close to the limit of what we can work with, which is why we are examining these new kinds of steels,” says Galmiche. “We are also looking at heat-assisted forming solutions, where currently all forming is done at room temperature. Operating at a higher temperature would aid formability but as ever, the main issue is one of cost,” he explains.
Virtual future
“I believe that in the future, we will use many more different materials to improve the construction of automotive seating,” says Aumont. “The challenge is joining them together, and I see strong development of new adhesive bonding technology.
Moreover, as engine technology improves and emissions are reduced, this will offer better performance so the pressure on weight reduction will decline,” he adds, before concluding, “But in terms of R&D, the future will be in virtual development. We are aiming to be able to develop everything without a prototype or at least to be able to sell the first prototype, as the first product, as the aviation industry does. Flexible, advanced, and high-tech development in close cooperation with materials suppliers is the key to moving forward for an increasingly technical and scientific industry such as ours.”
At SSAB, Svante Fält is the key account manager for Faurecia. “In general, companies within automotive manufacturing have a high level of technical knowledge and understanding regarding material properties. This makes for a good fit for joint projects with materials suppliers such as SSAB,” he explains.
“At SSAB, we strive to keep our customers’ business in focus and, with them, aim to find the best fit in terms of low weight, high safety and cost-efficient production. Technical customer support has always been a core issue for us and an important part of our success in the market. To keep our position as a world-leading manufacturer of advanced high-strength steel, we are continuously developing new steel grades and are running multiple trials where customers are looking to upgrade to higher strengths. Our Docol-branded top products can compete with any lightweight material and when it comes to overall economy, few can beat us, and our technical customer support is second to none,” he concludes.
Faurecia was founded in 1997 from a merger between Bertrand Faure, a specialist in seat frames and systems for the automotive industry, and ECIA, a Peugeot subsidiary and manufacturer of seats, front ends, and vehicle interiors – and one of Europe’s leading names in exhaust systems.
Today, Faurecia has over 100,000 employees working at 320 sites, including 30 R&D centres, in 34 countries around the world, and is a global leader in its four different business areas: automotive seating, interior systems, automotive exteriors and emission control technologies.
Faurecia is the world’s number one supplier of seat frames and mechanisms, emissions control technologies and vehicle interiors. The group is also the world’s third-largest supplier of complete seat systems and is Europe’s leading name in automotive exteriors.