Smartly pressed
OEMs and suppliers are teaming up to design and construct a state-of-art press shops, duly networked for an industry 4.0 approach
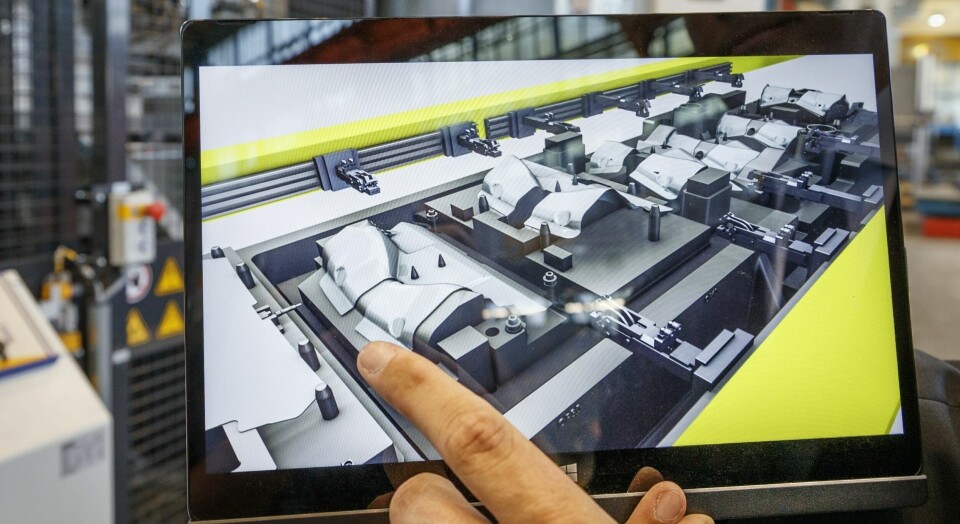
Arguably the main technological factor most commonly associated with metal pressing and forming equipment is the sheer force it can exert when in operation – multiples of tens of thousands of tonnes equivalent are commonplace. But an increasingly important factor is the extent to which such operations can be monitored and controlled automatically by a combination of intensive sensoring and appropriate software systems.
It is a concept that has come to be known as that of the ‘smart press shop’ and which is now a focus of intensive development work in the automotive industry involving whether separately or together both vehicle and component makers and technology suppliers.
Just last September, for instance, high-end German carmaker Porsche and compatriot pressing equipment supplier Schuler announced a joint agreement to go one step further and actually design and construct a state-of-art press shop to serve the former’s requirements by implementing a highly networked industry 4.0 approach. Their intention is that the new facility will pioneer technologies to enable the highly flexible production of complex car body parts with a focus on aluminum body panels and small batch production.
Porsche states that it wants to use the joint venture “to lay the foundations for the future of sports car manufacturing.” The carmaker also states that the industry 4.0 concept, or Porsche Production 4.0 as it is known internally, will play a major role. It also aims to set new standards in two respects – manufacturing performance and the digital networking and readability of data streams along the entire production process. The consistent further development of process know-how in the field of metal forming will be achieved, among other ways, by the continuous networking of production data and the use of machine learning.
The joint venture will operate as an independent company held in equal proportions by Schuler and Porsche, each of which will invest a double-digit-million euro amount in the venture with over a hundred highly skilled jobs to be created. The location of the new company has not been finally decided yet though its location is expected to minimise logistics distances for car body parts.
But what constitutes the essential underpinnings of the smart press shop concept from a technology supplier’s point-of-view? According to Robert Vollmer, technical specialist with Schuler, they involve “not just the working of and control of the line, but additional features, and for this we need a lot of data.” Moreover, he continues, “it is an essential feature that while the necessary data is collected from multiple sources, such as presses but also automation components and the furnace, that it is processed in just one system.”
Nevertheless, he also indicates that while the concept is futuristic in some ways, Schuler’s own perception is that it does build on existing capabilities. “We found out that we don’t need additional sensors for the first step,” he states. “A lot of necessary sensors are already integrated with the machines.”
Monitoring hot stampingVollmer’s own particular area of specialisation is hot stamping which he describes as “a thermo-mechanical coupled process – a heat treatment combined with forming process”. Moreover, standard practice is now that the furnace is controlled according to data gathered by temperature sensors rather than purely subjective operator-controlled criteria. But, he says, the key advance in smart forming is “that data is not just used for temperature control but also quality assurance.” So, for example, appropriately advanced ‘smart’ sensoring might involve using thermal cameras to record the temperature of parts immediately before and after forming. But the key necessary associated capability would be that of the “correlation of process data with specific manufactured parts”. As he explains, for automotive users that capability is absolutely crucial “because hot-stamped parts are safety parts in cars.”
Schuler presented its own combination of hot stamping and process monitoring for the first time in Autumn 2018. Key capabilities, says Vollmer, include “a cockpit that collects all the data in one place and provides an overview that can check if a part is within mechanical specification.” But a track-and-trace capability is still in development. “It will soon be necessary to tell customers, for safety parts especially, the conditions under which they have been made,” he states. “We are also still working on the ability to use data for predictive maintenance.”
Otherwise, Vollmer adds that already intensive use of sensors, such as those for measuring both the temperature and atmospheric composition in the furnace, the latter to guard against the danger of hydrogen embrittlement, will grow even more pervasive. In fact, he says, the further development of the concept presents opportunity to use new types of sensor – for instance, those for sound and vibration. Other parameters that will need to be monitored and recorded include “time in furnace, time of transport between furnace and press, and press kinematics, such as forming time and maximum force.”
"It will soon be necessary to tell customers, for safety parts especially, the conditions under which they have been made. We are also still working on the ability to use data for predictive maintenance" - Robert Vollmer, Schuler
An unavoidable fact of life, though, is that hot stamping involves ‘big data’ - as Vollmer points out, a typical hot-stamping line would have more than 1,000 sensors. That data can be processed at a user site, but further, more detailed processing after feature extraction can be carried out remotely, if necessary by a specialist, which is a key element of the industry 4.0 approach, is likely to be a crucial enabling technology.
Schuler is, in fact, already implementing the concept of smart press shop operations on its own account for real customers in a project that allows Vollmer to provide some figures to quantify just how data-intensive such operations can be. He confirms that a large-scale field test is currently in progress at the company’s own site in Göppingen, in southern Germany, involving a 1,600-ton hydraulic die hardening press, which is being used to produce parts for lightweight automotive construction from sheet metal heated to 930°C for real automotive customers. He says the amount of data generated by that facility, which involves just one hot-stamping machine, amounts to eight terabytes every two months.
Vollmer comments that the facility became fully networked with the application of Schuler’s own process monitoring software about a year ago. In consequence, he says, “we can now find out problems very fast,” so issues that previously took days to resolve can now be dealt with “in just a few minutes”. It is a capability that is, he confirms, now starting to be applied to real projects at customer sites.
Audi advancesHowever sophisticated the manufacturing process, appropriately precise inspection procedures for finished formed parts remain a basic requirement for effective quality control. Nevertheless, as the manufacturing technology itself advances in capability so do associated inspection technologies. Perhaps the most advanced current instance for formed metal parts in the automotive industry is to be found at Audi’s main manufacturing plant in Ingolstadt, Bavaria, in southern Germany.
The company has revealed that it has developed a system utilising artificial intelligence (AI) and machine learning (ML) to enhance existing automated inspection techniques for pressed parts in order to identify even the finest of cracks in finished components. It says the project has resulted in a production-ready solution, developed almost entirely in-house, which Audi will use exclusively and which it is confident is genuinely unique.
According to Dr Klemens Niehues, automation technology engineer with Audi, the press shop at Ingolstadt has until now employed a mix of visual inspection by employees and conventional image-recognition software fed with data captured by several small cameras installed directly in the presses. But, as he confirms, the company has deemed this set-up inadequate for satisfying today’s increasingly stringent requirements and the work that would be required to modify it unfeasible.
“The effort to adapt the current system to work with less or even without any mistakes would be very high,” he explains. “The value limits of the current system have to be adapted manually for each production batch because lighting conditions and the material surface can change.”
Audi has therefore opted to replace this process with an ML procedure that will employ a software system based on a complex artificial neural network operating in the background of what it regards as a highly innovative procedure. As Dr Niehues explains, it is needed to help the company deal with several issues, including changing both component configurations and increasingly compressed manufacturing schedules. “In general, the parts are getting a more complex geometry and there are more ambitious requirements in design terms so the process windows for their production are getting smaller and in consequence it is becoming more difficult to produce these parts,” he states. “That is why we have found ourselves focusing on this topic.”
The solution developed by the company is described as based on ‘deep learning’, a specific form of machine learning that can operate with extremely unstructured and high-dimensional amounts of data, such as those created by images. The team involved spent several months training the artificial neural network with several million test images – a task that involved not just the creation of a sufficiently large database but also the necessary ‘labelling’ of the images. The latter procedure involved recording cracks in the sample images with what is described as ‘pixel precision’. This has enabled the neural network to become capable of learning from the examples, so it can detect cracks in new, previously unseen images. The database comprises several terabytes of test images from seven presses at the Ingolstadt plant as well as from several Volkswagen plants.
The complexity of the task involved is confirmed by Dr Niehues’ colleague, machine learning engineer Johannes Schniertshauer. “When building our models we not only used current state-of-the-art deep-learning architectures, but also included recent research findings for training and optimising our models,” he reports. “As the whole field of deep learning is constantly evolving – from both a software and an algorithmic point of view – we are constantly updating our software chain. To catch up with all these developments is always challenging.”
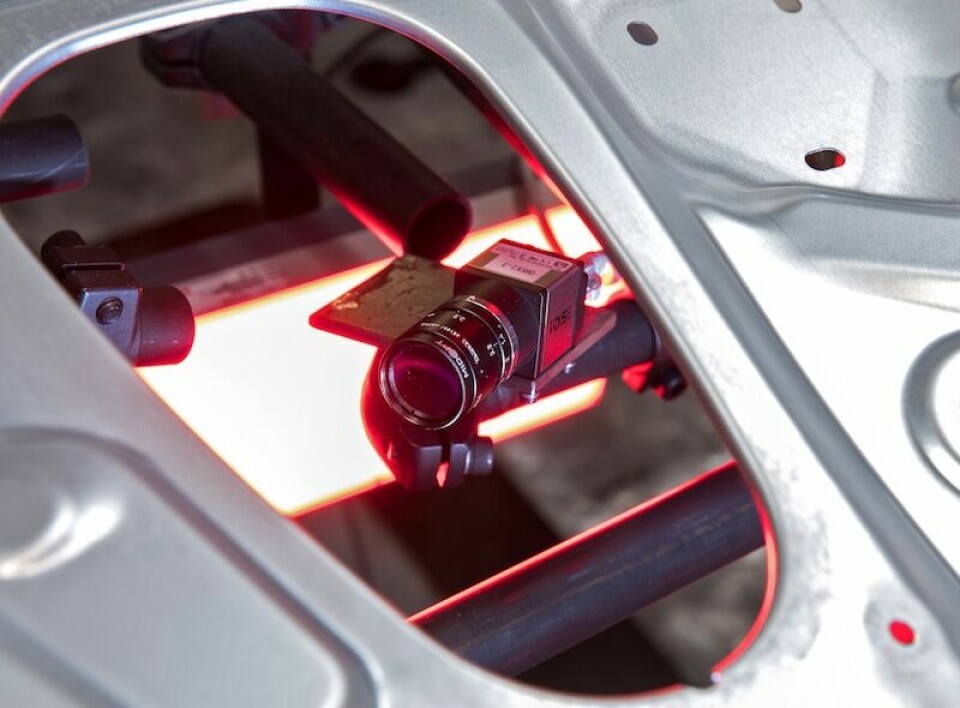
Meanwhile, flexibility of use is highlighted by Dr Niehues as one of the major benefits the new technology will bring. “The main advantage is to have an algorithm that tells you if there is a crack on the picture or not, just like a human would do, independently of the metal part and the changing conditions of material, light and so on. In consequence you do not, for instance, have to pre-define a box or set a value limit, something is usually necessary for computer vision applications.”
But a crucial technical distinction between the way inspection is carried out at Ingolstadt at present and the intended future procedure involves the very front-end camera technology. Surprisingly, perhaps, the more sophisticated approach the company is planning will actually enable less expensive, though more capable, vision capture hardware to be used.“For the current system we use smart cameras, where the evaluation takes place in the camera itself,” explains Dr Niehues. “But for the new system the cameras are only needed for the data acquisition because the image evaluation is carried out on a desktop computer. This means we can use even cheaper cameras with more resolution without special requirements and can take photos of a larger section of the part.”
That requirement for something less than highly intensive processing power to operate the system is confirmed by Johannes Schniertshauer, though he does concede that more specialised resource is nevertheless used to create the basic system capability. “To train and run our machine learning models, we use graphical processing units (GPUs),” he explains. “But although the training of those learning models requires sophisticated servers, actually running them on a detection system only requires modest hardware.”
He also confirms that one of the basic building blocks of the industry 4.0 approach is crucial to the new system’s capability. “We use MQTT (Message Queuing Telemetry Transport) for the communications between the software modules, sensors and cameras,” he states.
Further work will be required, though, to bring that capability up to the level where it can implemented as a day-to-day manufacturing support tool. “Right now we are in serial development,” states Dr Niehues. “We will work through to the end of 2019 to finalise this phase and then the prototype for a longer time period in our press shop at Ingolstadt.”