Revolutionising Automotive Manufacturing: Flexibility, Efficiency, and Sustainability with Siemens
PARTNER CONTENT
This content was produced by Automotive Manufacturing Solutions in partnership with Siemens
Discover how Siemens’ innovative solutions empower automakers to meet the challenges of EVs, sustainability, and smart manufacturing. Download the whitepaper to explore actionable insights.
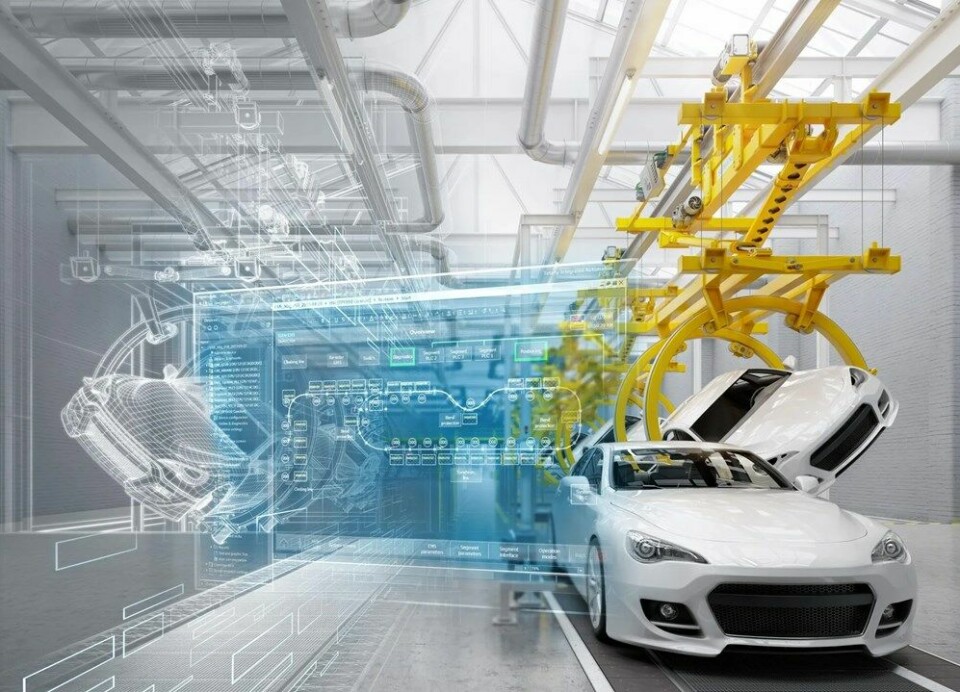
Please complete the form below and upon submission your browser will redirect you to the whitepaper.
The automotive industry continues to change at a rapid pace and vehicle makers and suppliers must be able to react in a timely and agile manner to changes in market demands, supply chain issues and legislative requirements. So, developing and operating highly flexible, efficient and sustainable production operations is a high priority.
Alongside its advanced digital platforms and services, developed to support efficient production operations, Siemens has created a trove of supporting technical literature, including whitepapers, case studies and articles, all providing a range of insights and shared experiences from the company’s experts and manufacturing clients.
In this article we look at some of the solutions offered in a very pertinent white paper produced by Siemens: How automotive manufacturing is shifting gears. This publication acts a navigation tool for the efficiency and flexibility challenges facing the industry, placing key areas of focus in the current context of manufacturing.
This whitepaper covers the trends in the industry influencing manufacturing and offers guidance on the strategic pathways to help navigate challenges these trends present. Key topics covered here include flexibility in manufacturing, sustainability, data-driven quality and maintenance, and workforce transformation.
Flexibility in production
The paper highlights the importance of manufacturers making their production lines more adaptable, flexible, and scalable to manage a very dynamic automotive market. Siemens notes that key to boosting efficiency and ensuring the flexibility required to keep pace with rapid market changes, is the adoption and integration of next-level automation. Marco Langbein, Director of Industrial Manufacturing Solutions at Siemens offers more detail how the company’s digital tools support the development of next-level automation:
“This would be a combination of automation solutions from Siemens Digital Industries Factory Automation, Siemens Digital Industries Customer Services and Siemens Digital Industries Software. This will deliver a solution where automation (OT layer) will seamlessly integrate into IT (software layer). The aim is to gain full transparency of all data and leveraging tools supported by IA to make best use of the data and support better decision making.”
This envisages embracing disruptive technologies such as digital twins, software-defined control, AI and auto code generation for standardisation. In addition, this approach should include a focus on standardising processes, scalability, and reusability to support meeting customer demands. Siemens highlights that key to enabling this is the seamless integration of data across diverse platforms.
Sustainable production practices
The automotive industry faces complex energy management challenges and Siemens notes the necessity for companies to adopt a clear and effective strategy in their approach to sustainability. The company says that the lack of detailed and consistent data transparency on the energy usage of machinery, makes it challenging to benchmark and enhance efficiency across different production facilities. This whitepaper offers insights into reducing energy consumption and achieving carbon neutrality through green manufacturing practices. It includes guidance on steps to take such as implement energy measurement devices across shop floors and evaluating machine efficiency through a standardised approach that allows for a comprehensive energy analysis at both individual plant and broader company levels.
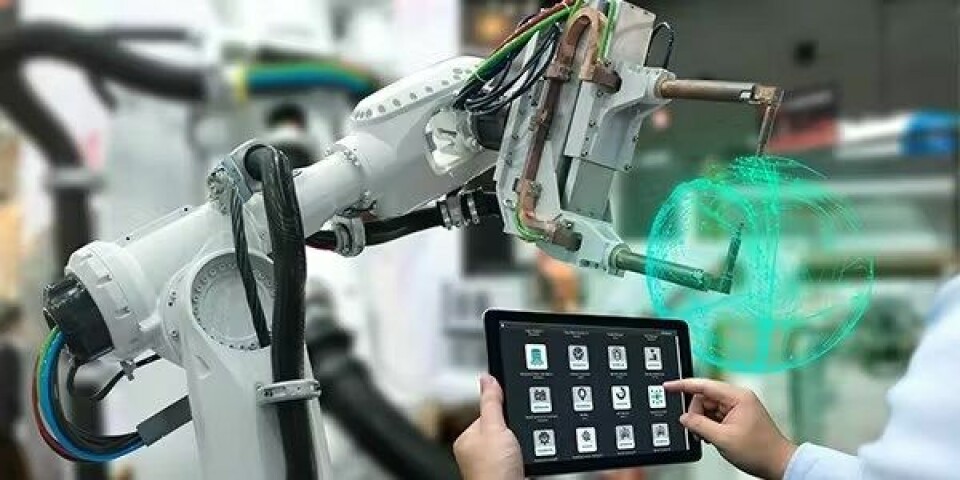
Data-driven quality and maintenance
Siemens points to the importance of data transparency in predictive maintenance, quality assurance, and operational optimisation and in this whitepaper offers use cases across several production operations including press shop, welding and conveyor systems.
According to Langbein the IT/OT connection, in conjunction with an AI supported evaluation engine, will deliver deeper insights into the current state of equipment and operating conditions. This will help the quality engineers to perform more data driven root cause analysis. Also, enabling full traceability from manufacturing execution to manufacturing planning and product design, supports a fast and efficient data collection process, preventing the need for time intensive manual searches. Another benefit of gathering real-time production data, such as process parameters, is that it also allows for analysis in real time and can be used to predict potential quality issues before they arise.
Looking at managing quality issues related to software defined vehicles (SDVs) Langbein notes there is an additional layer of complexity which impacts the quality processes:
“For example, a traditional risk analysis, using the FMEA methodology focused on hardware parts and processes, would investigate the impact on the end user customer, based on a hardware component failure. However, today there is the additional software component, which controls some of the hardware functionality.
“In addition, some manufacturers are offering over-the-air upgrades, which increases the need for traceability, to know which software version the vehicle is using, and more frequent quality checks need to be performed beyond the annual services.”
Workforce transformation
The development of smart factories and the implementation of digital tools also relies on a fully trained and engaged workforce. Siemens highlights the ongoing challenge of a shortage of operators and technicians with the required skill sets and observes the negative impact of this on operational efficiencies. Siemens says that to tackle these challenges there is an urgent need for more emphasis on comprehensive training and development programmes and in this whitepaper offers key steps to using digital tools for upskilling and reskilling to enable effective management of advanced systems.
The traditional way of creating training materials is very labour-intensive notes Langbein, and any updates would need to be manually added to the materials.
“By having the line already available in your simulation tools you are creating enablement material directly from the existing 3D simulation without waiting until the line is physically available. This will reduce the manual effort drastically. Also, any changes to the line simulation could easily be updated in the training courses,” explains Langbein.
Training in a virtual environment via VR provides the employees with a real world feeling to learn the process steps, which can be repeated as often as needed, without blocking the actual line.
All the necessary courses are tied to a qualification within the Siemens portfolio. When the employee has finished the all the courses for a particular qualification in the system, they achieve the qualification. Where courses are updated, an integrated document control function will automatically reassign the course to the necessary employee with a target date. If the course is completed in the planned time, the qualification will be maintained.
These are the main examples of how this digital enabled workforce differs from the standard training practice.
The company notes that the correct approach to training and upskilling can significantly reduce errors and improve quality, and how a more hands-on approach to training can boost understanding and the application of learnings and increase retention rates.
These are just a snapshot of the information available in this whitepaper. Download the whitepaper to delve deeper into these strategies and technologies.
Sharing knowledge and experience
Siemens has huge experience in working with vehicle makers and tier suppliers and in this whitepaper (How automotive manufacturing is shifting gears) has identified the most important challenges in automotive manufacturing and developed clear, effective tools and strategies to guide, support and enable companies to optimise production operations.
The company now shares this wealth of experience across whitepapers, articles and case studies for production teams to access and download. With these solutions automotive manufacturers can build and operate resilient, efficient and sustainable production operations.#