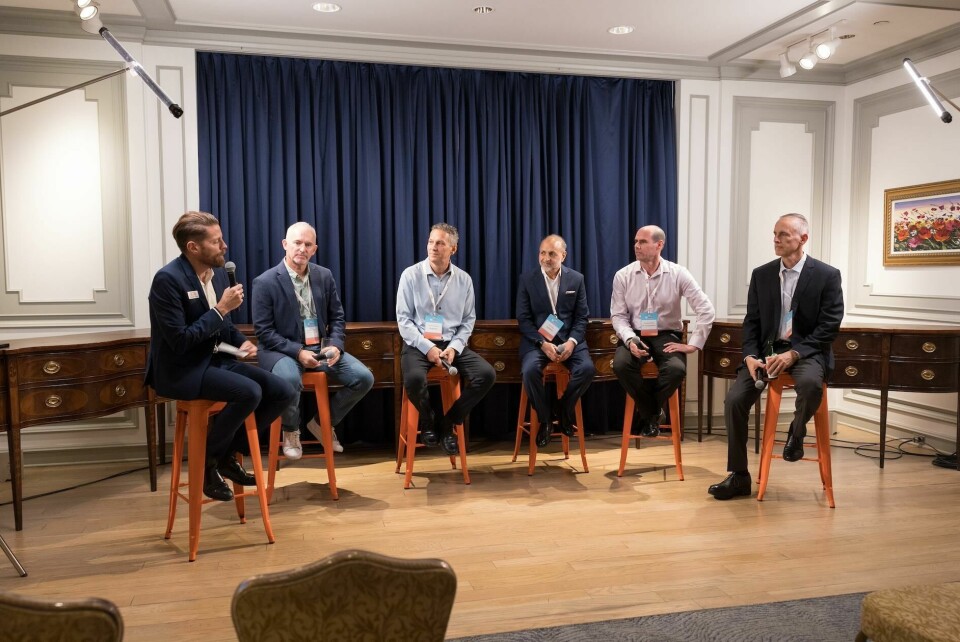
AMS Automotive Evolution: Reducing costs, fast-tracking development, embracing change
The AMS Automotive Evolution conference in Detroit brought together leading car makers and tier suppliers to discuss managing production operations as the EV transition continues. AMS Editor Nick Holt shares some takeaways from the event.
Finishing up on our latest Automotive Evolution conference in Detroit we came away with a strong sense of the change in North America’s automotive industry. Gone are the heady days of billion-dollar Capex investment in new electric vehicle (EV) and battery production (although more modest sums continue to be spent) to be replaced by a much more conservative approach towards optimising existing production assets. This reflects the gloomy outlook, as the big car makers struggle to turn a profit from their growing EV production operations. However, as we discovered, these circumstances have triggered another period of rapid development and innovation to support the manufacturing operations.

Managing investment and reducing costs
Speaking with senior executives from high-volume OEMs (VW, Toyota, GM, Stellantis and Ford) it is clear they share the same challenges. Cost is a big issue, with a focus on how to make EVs more affordable by reducing the related production costs. This is set against a backdrop of greatly increased energy, materials and labour costs, and weaker demand for EVs than forecasted, that has not helped the OEMs get closer to a profit in this segment. And the in longer term there is the looming threat of fierce competition in the form of much cheaper Chinese EVs.
Addressing the cost issue, we’re seeing a strong focus on optimising the capacity utilisation across the existing production networks and in shortening the development time scales for new products. It was recognised by all that closer collaboration across the design, engineering and production teams is vital to shortening the time to market for new products, without compromising on safety quality and performance, and that simplifying the vehicle builds is an important factor in this. Some of the OEMs have already started with the reorganisation and restructuring of these teams and although initially disruptive this approach is seeing some benefits.
The cost issue also means that the production teams will have to do more with less investment, and this sees a strong focus on optimising existing assets. This ties into our conference themes of flexible, digital and lean production and making the factories smarter and processes leaner and more efficient. Key to this will be the deployment of digital tools.
Progressing digitalisation
Our speakers acknowledged that this is an important area of focus going forward as a solution to manage production costs and shorten development timescales. Digitalisation of manufacturing operations is nothing new, OEMs have well established digital networks and process tools, but the software platforms and digital tools are seeing rapid development, as is the management of the data gathered. And perhaps the biggest step in this is the application of AI. All noted that this was still in the very early stages of assessment and deployment across their respective networks, but that it offered great potential.
With several of our expert panels centred around this topic, the discussions highlighted that while the ambition for the large-scale smart factory developments remained, much of the focus is now on smaller, targeted projects within factory operations that can be more efficiently, and cost effectively progressed to a conclusion. This focus providing validated processes that can be scaled across wider operations.
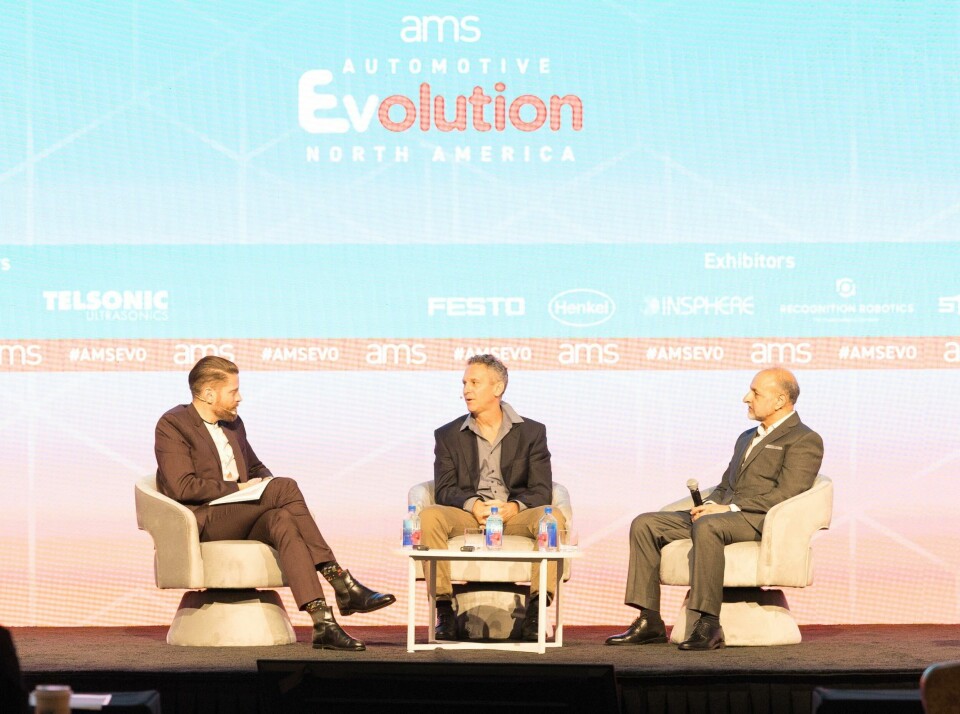
Building a culture of collaboration
However, it’s not all about the technology. The engagement of the workforce was also noted as an important factor in the wider adoption of digital systems and automation. Our speakers were keen to emphasise that this wasn’t just about gaining an agreement to these changes, but rather that full engagement and leveraging the vast experience of the factory teams is essential to the success of these projects and their outcomes. As with the above-mentioned closer collaboration of development and engineering teams, this requires a big cultural change in how they approach these new challenges.
Managing change and an uncertain future
It’s interesting to consider that modern vehicle production requires degrees of stability, consistency and repeatability, which favours the simplification and standardisation of processes. So, change and uncertainty would seem to be unwelcome, but as our speakers and delegates revealed, change is vital to the growth and development of the vehicles, the business and the industry. No matter how problematic the changes we are seeing might appear to be, they are the drivers of innovation and, as was noted by the OEM speakers, part of the everyday production cycle.
Uncertainty is less welcome. Shortly after our event concluded America went to the polls and voters sent Donald Trump back to the White House. The incoming president has strong views on trade and has promised to use tariffs as tool to protect US jobs. This presents further uncertainty for the North American auto industry and wider vehicle production in Europe and Asia.