ASEAN: Chinese OEMs increase investment through EV production
The Association of Southeast Asian Nations (ASEAN) is now seeing increasing investment in electric vehicle production with Chinese OEMs leading the way.
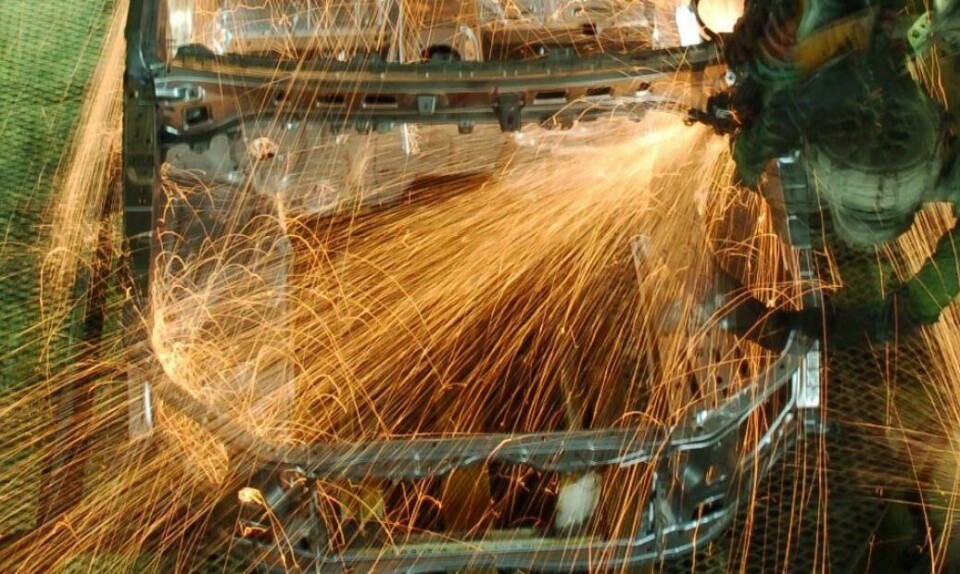
Across the ASEAN region there are full automotive manufacturing centres in Indonesia, Thailand, Malaysia, Philippines and Vietnam, along with a small Hyundai operation in Singapore making c2,500 Ioniqs a year, and a Toyota assembly partner in Cambodia making just a few hundred Camrys a year, from imported kits. Most of the full production facilities in the five main locations are run by the Japanese and increasingly the Chinese; there are also some low volume assembly plants run by German brands, notably BMW and Mercedes, in Thailand primarily. European brands are however generally minor players in the region, and only Ford remains of the American contingent, with a pick-up plant in Thailand, GM having closed its factory there some years ago and more recently sold the mothballed unit to Great Wall of China.
The two key trends across the region are the rise in EV investment and production, allied to the increasing role played by the Chinese collectively. In Thailand especially, where the Japanese vehicle makers (VMs) have dominated with globally focused pick-up factories, a major change in the industry’s supply side is taking place. Chinese factories in ASEAN will mainly supply within the region, with some exports to Australia and smaller non-ASEAN markets.
Light vehicle production across ASEAN fell from over 4m pa to under 2.9m in 2020 because of Covid but is now back over 4.2m a year and should climb to nearly 6m by the mid-2030s. This will largely be on the back of a recovery at most of the Japanese plants and new investment and expansion by the Chinese, especially in Indonesia and Thailand. Thailand has the biggest vehicle production volume, c1.8m in 2023 and is on track to reach over 2.2m by the mid-2030s; Toyota is the biggest VM in Thailand with around a one-third production market share, mostly pick-ups; Ford, Mitsubishi and Isuzu are also significant pick-up producers in the country. The Chinese, notably BYD, Chery, Changan, Great Wall and SAIC are now leading the Chinese charge in Thailand, as discussed below.
The second largest vehicle production country is Indonesia (currently c1.3m pa and expected to rise towards 2m by the mid-2030s, with details below); in third place is Malaysia, currently producing c750,000 pa, and is expected to rise to nearly 900,000 pa. Production in Malaysia is led by Toyota and Proton which account for c75% of production there. There has been no major change in the manufacturing and investment line-up in Malaysia in recent years, although GAC of China is currently during feasibility studies regarding CKD assembly in the country. By contrast there is a great deal taking place at present in Vietnam which has quickly become the fourth largest production country, currently making c250,000 pa, a level which is expected to rise to more than 500,000 pa in the mid-2030s. Finally, in fifth place, the Philippines where Mitsubishi (c35-40,000 pa) and Toyota (60-70,000 pa) account for most of the production there, currently running at a little over 100,000 pa, potentially rising to 125,000 by the mid-2030s. The total could be much higher depending on the scale and success of Chinese investment.
Indonesia sees growing Chinese VM investment
Production in Indonesia is currently running at 1.3-1.4m per year and is expected to rise towards 2m by the mid-2030s on the back of growth at both incumbent Japanese VMs and expansion of the Chinese especially; Toyota and Daihatsu have long been the biggest manufacturers in the country, but recent problems at Daihatsu may limit Toyota’s ability to sustain its position in the face of rising Chinese competition. Together Toyota and Daihatsu have around 50% production share, producing c780,000 pa, with the total expected to rise towards 1m pa by the mid-2030s. By contrast, in a distant second place is Mitsubishi with a current production rate of c160,000 pa, which is expected to rise towards 260,000. By contrast Honda and Suzuki each produce only c120-125,000 pa, with each company expected to rise towards 190-200,000 pa. Hyundai should soon be making c120,000 pa, rising toward 200,000 pa; Hyundai plans to grow its currently low of EV production, having made nearly 7,500 Ioniq 5 EVs in 2023, although no firm details have yet been released on its plans here. VinFast of Vietnam also plans an assembly facility in Indonesia, but the timing and scale of this factory are shrouded in uncertainty.
While the Japanese seek to recover post pandemic, the Chinese have begun to make inroads in Indonesia. Chery announced in February that it would make Indonesia into a regional manufacturing hub, with plans to export from Indonesia to Thailand, Vietnam and the Philippines. Currently Chery assembles the Tiggo and Omoda 5 using a contract assembler PT Handal in Bekasi, east of Jakarta. Assembly of the Omoda 5E electric model began in December and while this is still essentially a kit operation using Chinese-sourced parts, the aim is to reach 40% local content within two years; at this level vehicles are classified as locally produced.
BYD will open a plant in Indonesia in 2026, following launching an import sales operation in January 2023. BYD will invest around US$1.3bn in a full manufacturing facility with annual capacity of c150,000 per year. This will make hybrids and EVs, specifically the Atto 3, Dolphin and Seal models at the plant in a new industrial zone in west Java, to the east of Jakarta. Production is expected to begin in January 2026. This will be BYD’s fifth plant outside China, following existing and planned factories in Thailand, Uzbekistan, Hungary and Brazil.
GAC Aion, part of the state-owned Guangzhou group, will produce in Indonesia through a local Indonesian company, Indomobil. This partnership will produce four models in 2025 and will be the company’s second plant in the region, alongside a new factory in Thailand. Two small Chinese companies are also present in the country: Seres, which is part of Chongqing Sokon (a largely CV producer) is using Sokonindo Automobile to assemble its E1 small car in Indonesia, with others including the Seres 3 compact crossover under consideration for local assembly too. Meanwhile, Neta Auto signed an agreement with Handal Motor (Chery’s local partner) to assembles EVs from late 2024.
SAIC is also present in Indonesia, through its JV with GM, Wuling, a three-way joint venture (with the Liuzhou city government). This began with entry level commercial vehicles, and later moved into cars. Its key model in Indonesia where SAIC has invested US$700m since 2015 is the Air.
And while the Chinese move into Indonesia, some legacy brands are moving out: Peugeot, Ford, Chevrolet and Renault have also left the country, and although Citroen remains, it sold less than 150 cars there in 2023, all Indian imports; Citroen, however, does plan to add Indonesian assembly, via a partner, of BEVs by the end of 2024, so – along with a few thousand Mercedes and BMWs and even lower numbers of Volkswagens assembled from kits by local companies – a small European presence will remain.
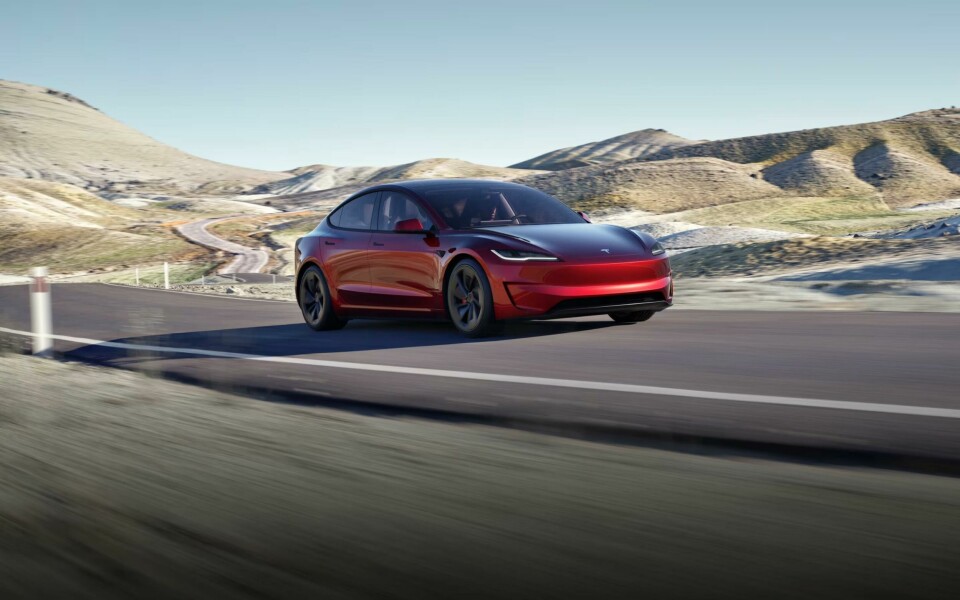
Securing nickel supply and developing battery production
On the supply chain side, Indonesia is a key source of nickel, reportedly having supplied 48% of global supply in 2022, with the Indonesian government believing it could attain a 75% global share; that said, the government has banned the export of raw nickel ore, ensuring that some of the key value-adding nickel processing work takes place in the country, boosting the economy even if full battery production is some way off.
Tesla got in early and secured long-term nickel sourcing arrangements because of its preference for NMC (nickel manganese cobalt) chemistry in its cells, although Tesla has moved away from NMC chemistry in recent times, adapting cheaper LFP (lithium iron phosphate chemistry), despite having agreed to source US$5 billion of nickel from Indonesia on a very long-term contract in 2022. Now, with nickel supplies assured, Elon Musk has started talking about the possibility of a full battery plant in Indonesia. In this area, Tesla will be beaten by a new battery plant run by a joint venture between Hyundai, LG and the Indonesia Battery Corporation. This will be south-east Asia’s first battery cell factory and will have capacity to make enough cells for 150,000 EVs.
Battery and especially cell production in Indonesia is attractive because of good local supplies of raw materials, notably nickel. Korean supplier EcoPro is taking a 9% stake in an Indonesian nickel smelting factory, Green Eco Nickel, based on Sulawesi island. This is majority owned by Chinese company, Green Eco-Manufacture and can produced 20,000 tonnes of nickel per year. EcoPro already has a stake in another nickel facility on Sulawesi, owned by GEM, with a capacity of 50,000 tonnes a year. The nickel from these sources will be supplied to an affiliate company EcoPro BM, which plans to make 200,000 tonnes of battery precursor material a year by 2027, for worldwide supply.
Thailand’s EV3.5 programme boosts EV production
In Thailand, the government is putting its weight behind the EV transition and has allocated 34 billion baht (almost US$1billion) to support this switch through to 2027, under the programme title EV3.5. The programme is designed to get Thai EV production up to at least 350,000 a year by 2027, potentially as much as 525,000 pa. EV3.5 requires that for every car a VM imports tax free, it must manufacture two EVs locally by 2026, rising to one for three a year later. This rule will clearly help build production momentum as well as change the structure of the production line-up in the country, with the Thai government having targeted production of 300,000 EVs pa by 2027. At the end of 2023, it also announced a programme which gives foreign EV manufacturers as much as a 40% reduction in import duties and reduced excise duties for CBU imports in 2024 and 2025, to just 2%. to qualify, the VM concerned must start EV production in Thailand by 2027. This is an extension of a scheme launched in 2022 since when several Chinese VMs have moved to Thailand; BYD, Chery, Great Wall, SAIC and Changan are establishing a significant manufacturing network in Thailand and will slowly supplant legacy Japanese and Western brands from Europe and the US.
In total the Chinese VMs are investing over US$1.4 billion in Thailand and the government fund, worth 34 billion baht, will support some of these new production facilities and is in addition to a 7.1 billion baht fund to support consumers with EV purchases. In 2024 and 2025 EV buyers will get a 100,000-baht per vehicle subsidy (cUS$2,900), although this is actually a reduction from the 150,000-baht subsidy offered under the end of 2023. The Thai government wants at least one-third of the country’s planned 2.5m vehicles annual production by 2030 to be EVs.
In April 2024, Chery confirmed a factory in Rayong province would open by the end of 2025, initially making 50,000 electric and hybrid models, with a longer-term target of at least 80,000 pa. Meanwhile Great Wall is launching a hybrid pick-up mid-2024, producing these, initially from kits, in the former GM Thailand factory. Great Wall will also export hybrid pick-ups, notably to Australia where new, strict emissions rules to come into effect in 2025. These will make it difficult to sell traditional diesel pick-ups in the country, and the 2025 emissions limit of 199g/km will be further reduced to 81g/km in 2029. This will mean only hybrid, or fully electric pick-ups can be sold in Australia at that point, an area in which the Chinese are ahead of the Japanese. Thailand exported over 300,000 vehicles, mostly pick-ups, to Australia so these rules are a major issue for the country: hence the decision to encourage investment in EV production. Geely too is expected to produce an electric pick-up in the country in the near future.

BYD displayed its range of vehicles at the Bangkok-International-Motor-Show. The OEM will start production of EVs in Thailand by Q3 2024
Together the Chinese will provide a major shock to the established Japanese producers, who had nearly 90% of the pick-up market in Thailand in 2023, with Isuzu leading the way with 42% and Toyota 40%. Both VMs plan to launch electric pick-ups by 2025 but they will still be a year or more behind their Chinese competitors. Toyota makes a range of cars, including Yaris, Camry and Corolla, in Thailand for regional markets, including the kits shipped to Cambodia for assembly there. Ford, with the Ranger, and Mitsubishi, with the L200/Triton, also make pick-ups in Thailand, mainly for export rather than local sale it should be added. The Ford plant, AutoAlliance, also makes SUVs for Ford for the local market and a variety of small and compact Mazdas for the local market, a legacy arrangement from when the two companies had cross-shareholdings. BMW and Mercedes also have low volume assembly partners essentially producing vehicles from imported kits; BMW is understood to be considering a battery assembly plant in Thailand which suggests it is planning to boost assembly of EVs in the country.
BYD meanwhile will start production of EVs in Thailand by Q3/2024; construction of a new factory near Rayong began in March 2023 and is nearing completion, with trial assembly, of the Atto 3 model, having begun in March 2024. The factory should make around 150,000 upa but which other models it will make has not been confirmed.
SAIC has started building a 500m baht battery assembly plant near Bangkok, having had vehicles made by a local conglomerate, CP Group which has an annual capacity of c100.000pa. SAIC has actually been assembling MG4s since November last year. Another SAIC affiliate, GM-Wuling is investing heavily in the country, having committed more than US$1billion since 2015; its flagship model in Thailand is the Wuling Air EV.
Great Wall took over the old GM factory in 2021 and can now produce c80,000 hybrids and EVs in a revamped factory; it makes the ORA 03 and produces batteries in-house through association with Chinese battery company, SVOLT. Changan will open a new factory in the Eastern Economic Corridor Special Zone and will be able to make 100,000 EVs and plug-in hybrids and still has room to increase production to 200,000 pa. Gotion and EVE Energy will also soon have their own battery factories in the country.
Changan is building a plant in Rayong which will export to other ASEAN markets, as well to Australia and New Zealand. This will have an initial capacity of 100,000 pa and should be producing vehicles in Q1/2025. Investment is due to reach US$285m
In addition, some CV producers are coming to Thailand, notably BYD through Thai company Rever Automotive with a licence deal which will see Rever assemble trucks and buses from Chinese kits; and Chongqing Sokon will build a CV chassis-cab plant in Thailand in association with its local distributor, Planet EV, although volumes will be low initially, not much more than 1,000 a year.
Not to be left out entirely, Hyundai is also moving into Thailand, although in a slightly different way to the Chinese. It opened an EV development centre, called Ioniq Lab, in Bangkok in December 2023. No doubt it will expand production there too because the rules of EV3.5 require this as noted earlier.
The moves by the Chinese in Thailand come on the back of exits from the country; General Motors left some years ago and now Suzuki and Subaru are pulling out of local assembly partnerships with sales in the country by each brand having fallen to less than 1,000 a year, making continued kit assembly, let alone full manufacture, uneconomic.
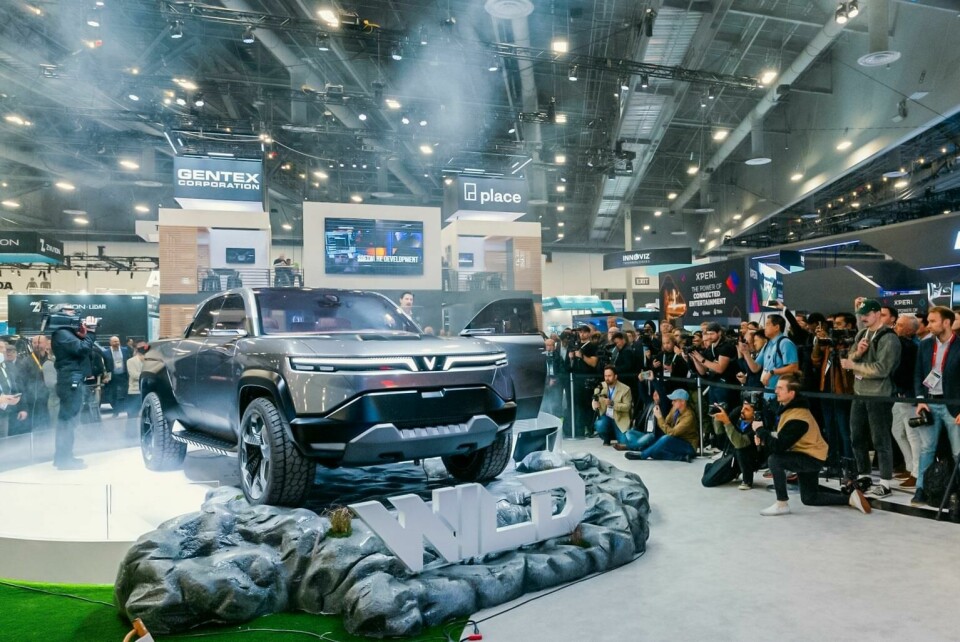
BYD eyes production in Vietnam
The third ASEAN country with major developments in automotive manufacturing is Vietnam. Much attention has focused in recent times on VinFast but just as in Indonesia and Thailand, it is the Chinese VMs who are making major moves. The other key VMs there are local assembler Thaco (which makes Kias, Mazdas and Peugeots, a combined total of c90,000pa at present), Hyundai (c70,000 pa) and Toyota (c40,000 pa), all of which are expected to more than double in the years ahead. Mercedes and BMW also have volume assembly partners.
Local company VinFast has global ambitions, with plants planned for the US and India as well as at home in Vietnam. This is despite not having really secured its position in its home market, with less than 40,000 vehicles made there in 2023. It wants to be a much bigger player but has arguably spread its resources too thinly ahead of building a long-term presence at home. The company plans a 150,000 upa plant for India, with an initial investment of US$500m, but it has delayed its US$4 billion plant in the US as it refocuses on south-east Asia. VinFast had planned to open a plant in South Carolina in July 2024, later delayed until 2025, but now delayed even longer.
And once its operations in Thailand and Indonesia are fully operational, we can expect BYD to open a plant in Vietnam; the company already makes tablets in Vietnam and given its expansion elsewhere in the region, a car plant in Vietnam would be a logical move. The timing of this project has reportedly been put back by the general slowdown in EV sales but a BYD plant in Vietnam in the long term seems almost inevitable. One possibility for BYD which has been suggested by some Vietnamese press outlets is that it could partner with VinFast, a move which could benefit both parties, minimising investment commitments at this stage and avoiding over-exposure to the uncertain trajectory of EV growth at the present time.
Chery is investing in a US$800m joint venture to make vehicles through its Omoda & Jaecoo unit. Its local partner, Geleximco, is a diverse property, financial and industrial group. The factory will make 200,000 EVs a year in the coastal province of Thai Binh, with production due to start in early 2026.
Malaysia continues to drive forward with its National Automotive Policy
In Malaysia, production is dominated by local brands Perodua (part owned by Daihatsu) and Proton (now 49.9% owned by Geely of China), plus Toyota, partly in association with local company UMW (which is the largest shareholder in Perodua). As in Indonesia, local assemblers produce some BMWs, Minis, Mercedes, Peugeots, Volkswagens and even a few hundred Porsches a year from European supplied kits. Honda has a 100,000 upa capacity factory while Tan Chong, a local Malaysian company, produces c15,000 vehicles a year, mostly Nissans and a small number of Subarus.
Geely’s stake in Proton aside, investment by the Chinese in Malaysia is much lower than in Thailand and Indonesia especially. However, GAC is currently in negotiations with local company WTCA to assemble at least two models locally; these would likely be the EMKOO, for the right-hand-drive Malaysian market and the EMZOOM for export to (left-hand-drive) Vietnam. Whether the move by GAC into Malaysia is the harbinger of greater investment by the Chinese in Malaysia will be worth watching in the years to come.
Another EV programme with Chinese involvement is a small facility being established in Melaka; local company EP Manufacturing Berhad (EPMB), which supplies a variety of components and assemblies to Proton, Perodua, Honda, Mazda, Toyota, and Kia, will invest a modest 100m Malaysian ringgit (cUS$21m) in a new assembly plant which will have a long-installed capacity of 30,000 vehicles pa. EPMB has signed agreement to produce SUVs from BAIC and Great Wall, both ICE and electrically powered vehicles.
Malaysia is also notable for having an industrial policy for automotive, having launched its latest National Automotive Policy (NAP) in February 2020. This was designed as an enhancement of Malaysia’s previous policy, NAP 2014, with the addition of three new key objectives: Next Generation Vehicles (NxGV), Mobility as a Service (MaaS), and Industrial Revolution (IR 4.0) The government expects NAP 2020 to contribute 104 billion ringgit (US$24 billion) to the economy by 2030.
To bring these aims to reality, significant investment will be required, and not just from entirely new Chinese entrants. Domestic player, Proton, which has had the backing of Chinese giant Geely for some years, is expected to play a major role. Proton, together with original owned DRB-Hicom and Geely, is leading the development of Automotive High-Tech Valley project in Tanjung Malem in Perak state. Key to this will be the launch of several new EVs by Proton, with details still to emerge on these programmes.
Malaysia has trailed both Indonesia and Thailand in terms of automotive manufacturing volumes for some time and the government clearly wants it to be a more significant player in the region but despite two national plans for the sector it has yet to seriously challenge the two leaders in the region, let alone play a wider international role. Whether it can do either of both these in the years ahead will surely be proof of the national plan’s ultimate justification or validity.